Capítulo 4 - MÉTODO
DE INSPEÇÃO POR CORRENTES PARASITAS
traduzido do livro: AIR
FORCE TO 33B-1-1 / ARMY TM 1-1500-335-23 / NAVY (NAVAIR) 01-1A-16-1 -
Manual Técnico - Métodos de Inspeção Não Destrutiva, Teoria Básica
- APARELHO DE EC
- Componentes do Sistema de Inspeção por
Correntes Parasitas
- Oscilador
- Bobina de Ensaio (Sonda)
- Circuito em Ponte
- Circuito de Processamento do Sinal
- Mostrador/Tela de Resposta
- Subsistemas do Ensaio de Correntes Parasitas
- Sondas (Montagem da Bobina)
- Blindagem/Isolamento da Sonda
- Tipos e Classificação das Sondas
- Modo de Operação
- Método de Aplicação da Sonda
- Considerações e Limitações do Projeto
da Sonda
- Usos e Limitações das Sondas Internas
e Externas
- Funções do Instrumento de Correntes
Parasitas
- Requisitos Gerais
- Requisitos Específicos da Instda
Instrumentação
- Componentes da Instrumentação
- Osciladores de Frequência Variável
- Circuito em Ponte
- Circuitos de Amplificação
- Forma de Apresentação de Sinais e
Telas
- Medidores (analógicos)
- Mostradores Digitais
- Mostradores Lineares com Base no
Tempo (varredura)
- Aparelho de Correntes Parasitas
com Plano de Impedância
- Aparelho Digital
- Gravadores
- Dispositivos de Varredura Mecânica
- Posicionadores e Guias
- Processos Especiais
- Detecção por Amplitude
- Ensaio Multifrequência
- Técnica de Corrente Parasita Pulsada
- Medidas da Espessura do Metal
- Corrente Parasita de Baixa Frequência
- Ensaio com Dupla Frequência
- Técnicas Eletromagnéticas Fortemente
Relacionadas com Corrente Parasita
- Ensaio de Ruído Barkhausen em
Materiais Ferromagnéticos
- Imagem Ótico-magnética ("MOI")
- Aplicações de Técnicas Avançadas
4 APARELHO DE CP.
A
maioria dos instrumentos de ensaio não destrutivos por correntes
parasitas para uso em campo são unidades portáteis alimentadas por CA
ou bateria. Geralmente são leves, com menos de 3 kg, com baterias que
fornecem até 12 horas de operação. Podem ter um tipo de mostrador/tela
digital, como os de cristal líquido (LCD) ou os
eletroluminescente (EL). Algumas unidades operam em dupla frequência
com recursos telas (planos de impedância) alternadas ou
intercambiáveis. As unidades mais novas possuem circuitos de última
geração com microprocessadores avançados. Faixas de frequência de
aproximadamente 100 Hz a 6 MHz para detecção de descontinuidades. Essas
unidades podem ser usadas para inspecionar trincas na primeira ou
segunda camadas (chapas superpostas), revestimentos, espessuras de
galvanoplastia e medição de condutividade.
-
4.1 Componentes de um Sistema de Correntes parasitas.
Em sua forma mais simples, um sistema de inspeção por correntes parasitas consiste nos seguintes componentes:
- Um oscilador
- Um conjunto de bobinas
- Um circuito em ponte
- Circuitos de processamento de sinal
- Um mostrador de saída (leitura/tela)
Um
diagrama de blocos de um sistema de inspeção é mostrado na Figura 4.1
com a bobina aplicada a uma peça ensaiada. Os sistemas podem ser
construídos para múltiplos propósitos ou para funções muito
especializadas. Em geral, instrumentos projetados para tarefas
específicas, como medir espessura de revestimento ou condutividade
elétrica, são mais fáceis de calibrar/ajustar e operar do que
instrumentos de uso geral, mas também são limitados à sua aplicação
projetada
.
4.1.1 Oscilador.
O
oscilador fornece uma corrente alternada de uma ou mais frequências
para a bobina de ensaio. A frequência usada é determinada pela objetivo
da inspeção e pelo material que está sendo inspecionado. As frequências
usadas para ET variam de menos de 100 Hz a mais de 6 MHz.
4.1.2 Conjunto de bobinas (sonda).
O
conjunto de bobinas induz correntes parasitas na peça que está sendo
inspecionada e detecta mudanças no fluxo de correntes parasitas. Para
algumas aplicações, uma única bobina é usada para ambas as funções.
Mais comumente, múltiplas bobinas são empregadas em um conjunto. Uma
configuração comum possui uma bobina induzindo o fluxo de correntes
parasitas (excitadora) e bobinas separadas usadas como detectores.
Outra configuração usa uma bobina como indutor e detector na peça
ensaiada.
4.1.3 Circuito em Ponte.
O
circuito em ponte converte mudanças na intensidade e
distribuição das
correntes parasitas em sinais que são, por fim, processados e
exibidos. Um modo comum de operação é ter a
saída da ponte igual a zero
para uma condição boa ou sem defeito (NT: Ponto de
trabalho ou de Operação). A presença de um defeito
ou de
uma condição diferente de boa resulta em um
desequilíbrio da ponte,
produzindo assim um sinal relativamente pequeno. Este sinal se torna a
entrada para circuitos subsequentes.
4.1.4 Circuitos de Processamento de Sinais
O
processamento do sinal do circuito em ponte depende do tipo de
informação a ser exibida. Dispositivos simples de correntes parasitas
podem ser construídos para detectar e amplificar o sinal ou convertê-lo
em formato digital (por exemplo, um valor de condutividade). Sistemas
mais sofisticados podem processar o sinal eletromagnético complexo em
amplitude e fase, e fornecer filtragem para suprimir sinais
indesejados. Os detalhes dos processos são discutidos mais
detalhadamente nas seções posteriores.
4.1.5 Dispositivo de Exibição de Saída.
Os
dados do ensaio de correntes parasitas podem ser apresentados em
formato
analógico ou digital. Alguns dispositivos de saída comuns são a leitura
num medidor analógico (galvanômetro), uma gráfico cartesiana, um
registrador gráfico XY ou um
mostrador digital. Os medidores são adequados para realizar tipos
específicos de ensaio que exigem apenas a medição da amplitude do
sinal. Registradores gráficos XY permitem que a amplitude do sinal seja
exibida e correlacionada com
algum outro parâmetro, como tempo ou posição. Instrumentos de correntes
parasitas com um mostrador gráfico bidimensional são usados onde
tanto a amplitude quanto a fase do sinal de correntes parasitas devem
ser medidas. Esses são os instrumentos mais comuns disponíveis e
fornecem ao inspetor a maior capacidade de interpretar os resultados.
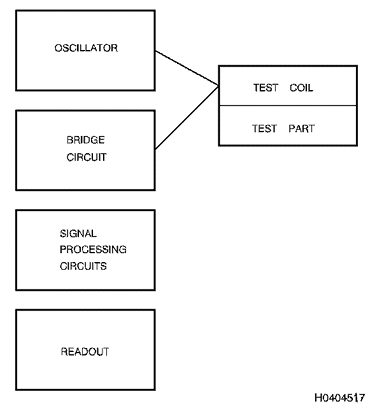
Figura 4.1. Diagrama de blocos do sistema de CP
4.2. Subsistemas de correntes parasitas
Os sistemas de correntes parasitas geralmente consitem em três
subsistemas. Um é o subsistema da sonda. O segundo é o
instrumento de correntes parasitas. O terceiro é o subsistema de
acessórios. Dispositivos de varredura da sonda na peça
("scanners") e registradores gráficos estão
incluídos em alguns subsistemas e são considerados
acessórios.
4.2.1 Sondas (Conjuntos de Bobinas).
Sondas
de correntes parasitas consistem em uma ou mais bobinas projetadas para
induzir correntes parasitas em uma peça a ser inspecionada e detectar
alterações no campo de correntes parasitas. Uma consideração
fundamental na seleção de uma sonda de correntes parasitas é o seu uso
pretendido. Uma sonda de pequeno diâmetro ou uma bobina envolvente
estreita proporcionarão maior resolução de pequenos defeitos. Uma sonda
maior ou uma bobina envolvente mais larga proporcionarão melhor média
das propriedades do material, com perda de sensibilidade a pequenos
defeitos. Além disso, a sonda ou bobina deve corresponder à faixa de
impedância elétricado instrumento de correntes parasitas com o qual será
utilizada.
4.2.1.1 Blindagem/Isolamento da Sonda.
A
blindagem da sonda é usada para prevenir ou reduzir a interação do
campo magnético da sonda com características não relevantes nas
proximidades da sonda. A blindagem pode ser usada para reduzir os
efeitos de borda ao ensaiar perto de transições dimensionais na peça inspecionada, como um
degrau ou uma borda. A blindagem também pode ser usada para reduzir os
efeitos de fixadores condutores ou magnéticos na região do ensaio.
Sondas de correntes parasitas são mais frequentemente blindadas usando
blindagem magnética ou blindagem de correntes parasitas.
4.2.1.1.1
Sondas blindadas magneticamente têm sua bobina envolvida por um anel de
ferrita ou outro material com alta permeabilidade e baixa
condutividade. A ferrita cria uma área de baixa relutância magnética e
o campo magnético da sonda é concentrado nessa área em vez de se
espalhar para além da blindagem. Isso concentra o campo magnético em
uma área mais estreita ao redor da bobina.
4.2.1.1.2
A blindagem por correntes parasitas usa um anel de material altamente
condutor, mas não magnético, geralmente cobre, para envolver a bobina.
A porção do campo magnético da bobina que atravessa a blindagem gerará
correntes parasitas no material de blindagem em vez de nas
características não relevantes fora da área blindada. Quanto maior a
frequência da corrente usada para acionar a sonda, mais eficaz será a
blindagem devido ao efeito pelicular no material de blindagem.
4.2.1.2 Tipos e Classificação das Sondas.
Sondas
e bobinas de correntes parasitas podem ser classificadas por modo de
operação, aplicação (ou forma) e projeto.
4.2.1.2.1 Modo de Operação.
Existem
três modos gerais de operação para conjuntos de bobinas de correntes
parasitas: absoluto, diferencial ou emissor/receptor (também chamado
de reflexão).
- O
tipo mais comum de sonda de correntes parasitas utilizada em aplicações
de campo é a sonda absoluta. Sondas absolutas consistem em uma única
bobina colocada em contato com a peça a ser inspecionada, ou adjacente
a ela. Como quaisquer alterações na área interrogada pela bobina
produzem uma resposta, as sondas absolutas podem ser usadas para medir
propriedades específicas de materiais, como condutividade elétrica e
permeabilidade magnética. Elas podem ter outros elementos elétricos
discretos, como capacitores, incluídos no invólucro da sonda para
atender aos requisitos específicos do aparelho.
- Sondas
diferenciais contêm duas ou mais bobinas e são intencionalmente
projetadas para produzir uma resposta quando mudanças são detectadas
apenas pela bobina ativa (aquela única que no momento está sentindo a
mudança). Consequentemente, se a sonda diferencial
tiver duas bobinas montadas lado a lado, mudanças graduais na
condutividade elétrica ou na permeabilidade magnética seriam detectadas
por duas bobinas simultaneamente e nenhuma resposta ocorreria. Por
outro lado, se uma mudança abrupta na condutividade ocorresse,
localizada onde pudesse ser detectada por apenas uma bobina por vez,
então haveria uma resposta. Normalmente, em sondas diferenciais de
superfície e furo de parafuso, duas pequenas bobinas de detecção são
enroladas lado a lado no formato de duas letras D maiúsculos
consecutivas, sendo que a primeira em posição invertida.
Elas são conectadas em série, com uma enrolada no sentido horário e a
outra no sentido anti-horário. Isso produz uma indicação de uma trinca
que desvia primeiro para um lado e depois para o lado oposto,
enquanto produz pouca ou nenhuma indicação de condições que afetam
ambas as bobinas igualmente, como elevação ou mudança suave de
condutividade.
- Sondas
de reflexão podem ter uma ampla variedade de
configurações, mas todas
possuem uma bobina excitadora (de geração das correntes
parasitas, no inglês "driver") conectada separadamente de uma ou
mais
bobinas receptoras. Uma sonda com uma bobina receptora é chamada
de
reflexão absoluta, e uma sonda com duas bobinas receptoras
é chamada de
reflexão diferencial. Sondas de reflexão geralmente
oferecem melhores
níveis de sinal-ruído, mas são mais
difíceis de fabricar e, portanto,
mais caras.
- Um
quarto tipo de sonda, chamada de campo remoto, possui duas ou mais bobinas, com
a bobina excitadora a uma distância maior da(s) bobina(s) receptora(s). Sondas
de correntes parasitas de campo remoto são usadas para penetração
profunda em estruturas mais espessas e tipicamente em material ferromagnético.
4.2.1.2.2
Método de Aplicação da Sonda.
Sondas de correntes parasitas também
podem ser classificadas pelo método de aplicação
(Figura 4.2). A
aplicação mais comum é a sonda de contato ou
superfícial usada para
superfícies planas ou relativamente planas de uma peça.
Sondas de
correntes parasitas usadas para circundar uma peça são
chamadas de
bobinas envolventes. Sondas de correntes parasitas completamente
circundadas pela peça são chamadas de bobinas internas
internas "(bobbin"). Sondas de transparência, que utilizam uma
bobina em cada lado da peça (uma folha de alumínio, por
exemplo), são
outro método de aplicação. Todas essas
aplicações de sonda podem ser
operadas em modos absoluto ou diferencial (Figura 4.3). Sondas de
correntes parasitas também podem ser classificadas de acordo com
o
formato ou alguma outra característica proeminente da sonda.
Sondas
muito finas são chamadas de sondas tipo lápis. Sondas com
blindagem
eletromagnética especial são chamadas de sondas blindadas
ou focadas.
Sondas usadas em furos de rebites ou parafusos são chamadas de
sondas
de furos de parafusos. Certos tipos de sondas com núcleos de
ferrita
moldados podem ser chamados de sondas com núcleos na forma da
letra E, da letra U, ou na forma de copo.
4.2.1.2.3
Considerações e Limitações do Projeto da Sonda.
As sondas de correntes
parasitas têm vários requisitos conflitantes. Primeiro, elas devem
corresponder razoavelmente aos requisitos de impedância elétrica do
instrumento ao qual estão conectadas. Quanto mais próxima a
correspondência de impedância, maior a relação sinal-ruído. Além disso,
as bobinas precisam ser projetadas para que o tamanho da falha seja
detectado. Falhas menores requerem bobinas menores. A maioria dos
ensaios de correntes parasitas no campo é realizada com sondas
superficiais. A sonda superficial é usada em placas, chapas, folhas
metálicas, peças de
formato irregular e em furos. A extensão da área a ser ensaiada pela
sonda é controlada pelo diâmetro da bobina e pela presença de blindagem
da bobina. Quando a área a ser varrida é grande, bobinas superficiais
do tipo com a forma de disco ("pancake") ou sondas multibobina
sobrepostas podem ser
usadas para reduzir o tempo necessário para inspecionar a peça. Quando
pequenas falhas precisam ser detectadas, bobinas de até 1 mm de
diâmetro podem ser usadas para examinar áreas limitadas.
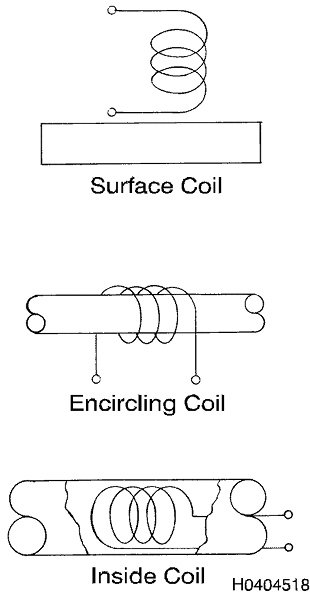
Figura 4.2. Tipos de bobina quanto a forma
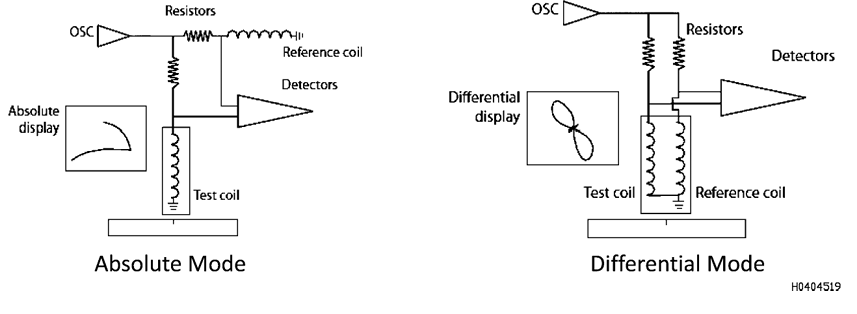
Figura 4.3. Exemplo de modo absoluto e diferencial.(Tipo de Sinal de Resposta)
4.2.1.2.4
Uso e Limitações de Bobinas de Diâmetro Interno (DI) e Envolventes.
Uma
bobina interna ("ID") pode ser usada em tubos, ou
outras peças cilíndricas onde a geometria é regular e o interior é
acessível. A bobina ID deve preencher quase toda a abertura da peça
para fornecer um alto fator de enchimento para máxima sensibilidade
do ensaio. O uso de bobinas ID pode ser restringido por curvas ou
diâmetros não uniformes. Bobinas envolventes são usadas principalmente
para inspecionar hastes, tubos, cilindros ou fios em aplicações de
fabricação. Com bobinas envolventes e internas, toda a circunferência
da amostra é avaliada de uma só vez. Consequentemente, embora a
localização axial dos defeitos (ao longo do comprimento da peça) possa
ser determinada, a localização circunferencial (ao redor da peça) não
pode ser definida.
-
4.3. Funções do Instrumento de Correntes Parasitas.
O instrumemto do ensaio de correntes parasitas desempenha três funções
básicas. Primeiro, ele gera a corrente alternada que induz o fluxo de
correntes parasitas na peça a ser inspecionada. Segundo, ele processa
as respostas ao fluxo de correntes parasitas induzido. Terceiro, ele
exibe as respostas de forma a auxiliar a interpretação.
- Geradores de Corrente. O
gerador de corrente é geralmente um oscilador de frequência variável
operado em uma única frequência para qualquer inspeção. A maioria dos
instrumentos tem a capacidade de operar em frequências de 100 Hz a 6
MHz. Instrumentos mais novos têm a capacidade de fornecer múltiplas
frequências à(s) bobina(s) de teste, sequencialmente ou simultaneamente.
- Current Generators. The current generator is usually a variable frequency oscillator operated at a single frequency for
any given inspection. Most instruments have the capability of operating at frequencies from 100Hz to 6 MHz. Newer in
struments have the ability to provide multiple frequencies to the test coil(s), either sequentially or simultaneously.
- Processamento. A
função de processamento do instrumento de correntes parasitas inclui
diversas subfunções. A maioria dos instrumentos inclui algum tipo de
circuito de balanceamento ou compensação, ajustado para fornecer uma
saída essencialmente zero para condições sem falhas. O sinal do
circuito de ponte é amplificado antes de prosseguir para o detector
e/ou circuito de análise. Os sinais podem ser analisados quanto à sua
amplitude e fase. A saída dos circuitos de análise pode ser filtrada
para auxiliar na interpretação antes da exibição. c.
- Processing. The processing function of the eddy current instrument includes a number of sub-functions. Most instru
ments include some form of a balancing or compensating circuit which is adjusted to provide essentially a zero out
put for non-flaw conditions. The signal from the bridge circuit is amplified before proceeding to the detector and/or
analysis circuitry. Signals can be analyzed for their amplitude and phase. The output from the analysis circuits may be
further filtered to assist interpretation before display.
c.
- Métodos de Exibição do Sinal Resposta. O
método de exibição principal da maioria dos dispositivos de correntes
parasitas é unidimensional, como um medidor, ou bidimensional, como uma
tela LCD. As saídas também podem ser transferidas para registradores
XY, registradores de gráficos de tiras, mídias de armazenamento
magnético ou até mesmo computadores para gerar registros de inspeção e
auxiliar na análise dos sinais de correntes parasitas.
- Display Methods. The primary display method of most eddy current devices is either one dimensional, such as a meter,
or two-dimensional, such as an LCD screen. The outputs can also be transferred to X-Y recorders, strip chart record
ers, magnetic storage media or even computers to both generate inspection records as well as aid in the analysis of
the eddy current signals
4.3.1 Requisitos Gerais.
O aparelho de correntes parasitas é o núcleo de um sistema de
correntes parasitas, seja uma simples combinação de instrumento/bobina
ou uma estação de inspeção por varredura totalmente automatizada. Para
garantir uma operação confiável, a instrumentação deve possuir os
recursos descritos abaixo:
- Sensibilidade (Detectabilidade).
Termo que se refere à capacidade dos instrumentos de encontrar as
falhas mais difíceis de localizar; com referência ao tamanho e tipo que
precisam ser detectados.
- Baixo
Ruído. O ruído deve ser baixo o suficiente para que o sinal da menor
falha a ser encontrada (ou menor falha de calibração) seja pelo menos três
vezes o nível de ruído da instrumentação.
- Tempo
de Resposta. O tempo de resposta do circuito deve ser rápido o
suficiente para processar e exibir sinais na velocidade de varredura
necessária.
- Seletividade. A instrumentação deve ser imune a fontes externas de interferência eletromagnética.
- Estabilidade.
A tela do aparelho deve permanecer estável (sem desvios de
resposta) durante o período de ensaio necessário.
- Robustez.
A instrumentação deve ser capaz de operar no ambiente de ensaio. Isso
pode incluir uma variedade de extremos ambientais de temperatura,
umidade, poeira e vibração.
4.3.2 Specific Instrumentation Requirements.
Choice of an eddy current test instrument must take into account the
type of flaw to be detected, the permeability of the material
(nonferromagnetic or ferromagnetic), type of probe to be used, display
method (meter, digital display, recorders, etc.), test frequency, and
signal processing requirements, portability, if needed, and any
accessories to be used.
4.3.2 Requisitos Específicos de Instrumentação.
A
escolha do instrumento de ensaio por correntes parasitas deve levar em
consideração o tipo de falha a ser detectada, a permeabilidade do
material (não ferromagnético ou ferromagnético), o tipo de sonda a ser
utilizada, o método de exibição (medidor, display digital,
registradores, etc.), a frequência do ensaio e os requisitos de
processamento de sinal, a portabilidade, se necessária, e quaisquer
acessórios a serem utilizados.
4.3.3 Instrumentation Components.
In general, most eddy current instruments consist of an oscillator, a bridge circuit
or similar null balancing system, and a variety of other circuits for processing and display of the eddy current signal. Units
will vary depending upon the complexity of the instrumentation and the requirements of the test.
4.3.3 Componentes da Instrumentação.
Em
geral, a maioria dos instrumentos de correntes parasitas consiste em um
oscilador, um circuito de ponte ou sistema de balanceamento nulo
similar e uma variedade de outros circuitos para processamento e
exibição do sinal de correntes parasitas. As unidades variam dependendo
da complexidade da instrumentação e dos requisitos do teste.
4.3.4 Oscilador de Frequência Variável.
Um
instrumento básico de correntes parasitas, ao operar em uma única
frequência durante um ensaio específico, geralmente possui uma faixa de
frequência operacional ajustável para atender a uma grande variedade de
situações de inspeção. Baixas frequências aumentam a profundidade de
penetração e, consequentemente, seriam usadas para detecção de falhas
subsuperficiais em materiais de alta condutividade. Frequências mais altas
limitam a profundidade de penetração e, portanto, são usadas para
materiais de baixa condutividade, bem como para detectar falhas
menores. Alguns instrumentos também incorporam um ajuste fino de
frequência como mecanismo para suprimir o lift-off. Esses instrumentos
incorporam a bobina da sonda em paralelo com um capacitor como uma das
pernas de uma ponte. A combinação bobina/capacitor é ressonante próxima
à frequência operacional pretendida. A frequência selecionada para
operação causa uma deflexão do medidor suficientemente fora da
ressonância para que o lift-off cause uma mudança de impedância menor
do que a causada por um defeito e a mudança de impedância para aumentar
o lift-off seja oposta à de um defeito.
4.3.5 Circuito em Ponte.
Um
circuito em ponte básico é mostrado na Figura 4.4. Neste exemplo, uma
tensão é aplicada nos pontos E1 e E2 à ponte contendo as impedâncias
Z1, Z2, Z3 e Z4. Z1 e Z4 são impedâncias fixas de mesmo valor; Z3 é uma
impedância ajustável; e Z2, a impedância desconhecida ou da ponta de
prova. Inicialmente, Z3 é ajustado para que nenhuma corrente flua
através do amplificador. Isso significa que a tensão nos pontos A e B é
a mesma e a ponte é dita balanceada ou anulada. Qualquer mudança na
impedância de Z2, a impedância da ponta de prova, resultará em uma
mudança de corrente através da perna da ponte e, consequentemente, uma
mudança na tensão no ponto B. Uma corrente então fluirá através do
amplificador, uma vez que existe uma diferença de tensão ou potencial
entre os pontos A e B. A ponte é agora dita desbalanceada. A ponte pode
ser novamente balanceada pelo ajuste de Z3 e a variação na impedância
da ponta de prova, Z2, pode ser determinada medindo-se a variação em Z3
necessária para rebalancear a ponte. O circuito da ponte em um
instrumento de ensaio de correntes parasitas é denominado ponte de
impedância, pois contém elementos resistivos e reativos. A impedância
Z2 na Figura 4.4 consiste na bobina de ensaioe de correntes parasitas.
Outros elementos reativos, indutores e capacitores podem ser incluídos
na ponte de impedância, dependendo do projeto e da função específicos.
No entanto, o princípio básico é que uma variação na impedância da
bobina de ensaio resulta em um desequilíbrio do circuito da ponte. A
saída (desequilíbrio) do circuito da ponte pode ser amplificada,
processada e exibida.
4.3.6 Circuitos de Amplificação.
O
desequilíbrio no circuito em ponte é devido a uma mudança na impedância
de inspeção. Isso resulta em uma mudança na amplitude do sinal,
na fase do sinal ou em ambas. Essas mudanças no sinal devem ser
amplificadas, detectadas ou demoduladas e processadas para apresentação
no dispositivo de saída (medidor, osciloscópio [tela] ou registrador, etc.). O
sinal de falha pode ter apenas alguns microvolts de amplitude e pode
exigir uma amplificação de mil a um milhão de vezes para processamento
e exibição posteriores. O conteúdo de frequência do sinal de falha pode
variar de muito baixo (essencialmente CC) até a frequência máxima de
operação do instrumento de correntes parasitas. Isso define a resposta
de frequência livre de distorção do amplificador. O amplificador também
deve ser muito estável, com muito pouco desvio, a fim de manter a
sensibilidade e a calibração necessárias durante todo o ensaio.

Figura 4.4. Circuito em ponte básico
4.3.7 Formas de Apresentação do Sinal e Mostradores.
A
saída de um instrumento de correntes parasitas pode ser lida em
um
medidor (galvanômetro analógico ou digital), um
mostrador/tela de plano de impedância (XY) ou um
registrador,
dependendo do tipo de informação necessária para o
ensaio. Um medidor
analógico (ponteiro) é o tipo mais simples de indicador
de saída. Uma
saída composta por amplitude e fase é chamada de
mostrador de plano de
impedância e pode ser exibida em um display LCD ou EL. Os
displays
LCD/EL exibem o sinal de correntes parasitas, a barra lateral do menu,
a barra de situação do ensaio "status", outros
indicadores e texto em tela cheia.
4.3.7.1 Medidores (analógicos).
Os
detectores portáteis de defeitos metálicos e de condutividade mais
antigos utilizavam um medidor que essencialmente indicava o grau de
desequilíbrio da ponte em termos de amplitude. Dependendo do circuito
do instrumento, as diferenças de fase também podiam ser exibidas em um
medidor. Esses instrumentos de correntes parasitas contêm medidores de
saída integrados, projetados ou selecionados especificamente para uso
com o circuito específico envolvido. Se utilizados, esses medidores
DEVEM ter uma velocidade de resposta suficiente para detectar as
descontinuidades de interesse na velocidade de varredura mais alta
esperada. No entanto, o medidor deve ser suficientemente amortecido
para que as indicações de "ruído" não confundam o inspetor, mas não
amortecido a ponto de as informações de interesse serem suprimidas. A
resposta ideal do medidor é um equilíbrio entre velocidade de resposta
e amortecimento.
4.3.7.2 Mostrador/Tela Digital.
A
maioria das unidades de correntes parasitas fornece saída em forma de
onda em um mostrador bidimensional de pequenos pontos quadrados
chamados pixels. A luz é gerada em tal tela aplicando uma pequena
voltagem aos pixels individuais. Uma forma de onda é criada energizando
os pixels necessários para moldar a forma de onda apropriada. Como a
persistência de um mostrador digital é controlada por uma voltagem
aplicada, e não pelo impacto de elétrons em uma tela com um revestimento de
fósforo (antigos osciloscópios), a persistência pode ser controlada pelo inspetorr. Em geral, o
pixel aceso permanecerá aceso até que o operador o "apague", desligando
a voltagem dos pixels.
4.3.7.2.1 Exibição de Base de Tempo Linear (Varredura).
Equipamentos
do ensaio por correntes parasitas frequentemente possuem a
capacidade de
usar uma exibição de base de tempo linear. O sinal
vertical da exibição
é recebido da bobina de ensaio e o sinal horizontal (por
exemplo, tempo)
é recebido de uma tensão de temporização. A
tensão de temporização é
ajustada à frequência ou período do gerador e
fornece uma varredura
horizontal linear da tensão de entrada vertical. Uma
mudança na
reatância da bobina de teste resulta em uma mudança de
fase da tensão
em um dos braços do circuito em ponte (sinal vertical). Essa
mudança de
fase é evidenciada por um deslocamento (ao longo da linha de
base
horizontal) da forma de onda. Durante a operação, a
tensão de
temporização ou varredura é usada para ajustar a
exibição e exibir o
número desejado do número de ciclos da forma de onda
(geralmente um). Geralmente, um controle também é
incluído para controlar a posição horizontal da
forma de onda na tela.
4.3.7.2.2
Aparelho do Ensaio de Correntes Parasitas no Plano de Impedância.
O
uso de aparelhos de análise no plano de impedância aumenta
significativamente a capacidade de análise de descontinuidades no processo de
inspeção por correntes parasitas. Alguns aparelhos de correntes
parasitas utilizam a técnica de exibição de pontos vetoriais, exibindo
informações em uma tela. A fase e a amplitude do sinal são apresentadas
diretamente para análise das informações de correntes parasitas. A tela
consiste em um ponto de luz em vez de uma forma de onda. Alterações no
produto ensaiado em relação ao padrão de referência farão com que o
ponto iluminado se mova. Os movimentos do ponto de luz podem ser
analisados para determinar qual variável de ensaio (condutividade,
permeabilidade ou dimensão) causa a alteração.
- 4.4 Equipamentos Digitais.
- O
uso de equipamentos de teste digitais, juntamente com computadores
digitais para processar e analisar dados, proporcionou uma redução
significativa nos níveis de ruído. Isso aumentou efetivamente a
sensibilidade do processo de detecção de falhas.
- Os
registradores são usados principalmente em
inspeções onde a bobina de
ensaio ou as peças se movem uma em relação
à outra. Muitas
aplicações mais recentes que utilizam um dispositivo de
ensaio e um
movimentador ("scanner") mecânico para mover uma sonda de
correntes parasitas por uma
área específica de uma peça podem usar um
registrador para mapear as
indicações de falhas. Um registrador para
aplicações de correntes
parasitas pode ser de vários tipos. No entanto, o registrador de
gráfico com amplitudes em função do
tempo/posição é provavelmente o mais comum. Os
instrumentos de
correntes parasitas mais recentes fornecem meios de armazenar
informações em mídia digital. Isso é
particularmente útil onde o tempo
de inatividade é importante, uma vez que o ensaio pode ser
realizado o
mais rápido possível e as informações
armazenadas em mídia digital para análise
posterior. Ao selecionar um registrador para uso com um determinado
instrumento de correntes parasitas, vários fatores devem ser
considerados:
- Correspondência de impedância entre gravador e instrumento
- Resposta de frequência do gravador
- Sensibilidade do gravador (faixa de tensão)
- Tempo de resposta
- 4.6 Dispositivos de Varredura ("Scanners") Mecânicos.
- O
uso crescente de "scanners" mecânicos para controlar o movimento da sonda
melhorou a capacidade de detecção de muitos métodos de ensaio. A
repetibilidade dos ensaios também é aprimorada pela varredura mecânica.
Um "scanner" mecânico pode fornecer ensaios em áreas de difícil acesso das
peças. Câmeras de vídeo remotas também podem ser incorporadas a um
"scanner" mecânico para fornecer cobertura visual durante o teste de
áreas inacessíveis.
- 4.7 Dispositivos de Fixação e Guias.
- O
requisito mais importante para detectar uma pequena trinca é que a
bobina passe sobre a trinca. Sondas, dispositivos de fixação e guias
com formatos especiais podem ajudar a garantir que isso aconteça. Guias
de sonda aumentam a detectabilidade da inspeção por correntes parasitas
e devem ser usadas sempre que necessário. A guia de varredura por
correntes parasitas mais simples é uma seção de plástico fino e
flexível cortada para se adaptar à área de inspeção, com margem para o
posicionamento da sonda. Tal guia pode ser facilmente preparada a
partir de filme de raio-X usado. A flexibilidade permite o encaixe da
guia em curvaturas compostas. É necessário que a borda usada para guiar
a sonda seja lisa para permitir um movimento constante a uma distância
constante da borda da abertura. A guia pode ser mantida no lugar ou
fixada com fita adesiva na posição necessária. Outro tipo de guia de
sonda que pode ser usado para pequenas aberturas, incluindo furos com
buchas, consiste em uma inserção circular que se encaixa no furo e tem
um diâmetro maior em uma extremidade para fornecer a distância de
deslocamento necessária da borda do furo. As guias de sonda DEVEM ser
construídas para fornecer o deslocamento necessário da borda para um
tipo específico de sonda e NÃO DEVEM interferir no movimento da sonda.
- Uma
ampla variedade de técnicas eletrônicas foi desenvolvida para problemas
específicos de inspeção em ensaios de correntes parasitas. Os circuitos
usados dependem do tipo de saída, do tipo de falha a ser detectada ou
de quando uma variável de teste específica (como lift-off) deve ser
suprimida para detectar outras condições.
4.8.1 Detecção de Amplitude.
O
tipo mais comum de medidor de detecção em instrumentos de correntes
parasitas é aquele que precisa detectar mudanças na amplitude do sinal
sem o uso de informações de fase. Nesse caso, a detecção de amplitude
pode ser utilizada com um detector simples do tipo diodo. O diodo
retifica a saída da ponte para produzir um sinal de corrente contínua
de amplitude variável.
4.8.2 Correntes parasitas multifrequenciais.
As
correntes parasitas multifrequenciais podem ser utilizadas quando
diversas propriedades do material mudam simultaneamente, como quando é
necessário diferenciar uma trinca de alterações geométricas em uma peça
complexa. Para ser eficaz, cada condição a ser suprimida deve produzir
alterações significativas na impedância para uma frequência e
alterações menos significativas para as outras frequências utilizadas
na inspeção. Um exemplo seria o uso de uma inspeção de dupla frequência
para corrosão subsuperficial, compensando o lift-off. Uma frequência
baixa seria selecionada, permitindo penetração suficiente para detectar
a corrosão. Respostas de lift-off também estariam presentes a partir
dessa frequência. O uso de uma frequência mais alta responderia ao
lift-off, mas não teria penetração suficiente para responder à
corrosão. A análise desses sinais pode se tornar extremamente complexa.
Atualmente, a maioria dos ensaios multifrequenciais se limita a testes
de dupla frequência.
4.8.3 Técnicas de Correntes parasitas Pulsadas.
A
técnica de correntes parasitas pulsadas é uma técnica de ensaio de onda
não contínua e também possui características multifrequenciais. A
largura do pulso estabelece o limite inferior de frequência, enquanto a
nitidez dos cantos do pulso estabelece o limite superior de frequência.
Sistemas multifrequenciais convencionais geralmente utilizam duas ou
três frequências. Frequências adicionais requerem sistemas de mistura
multiplex muito complexos para analisar as informações do ensaio.
Diversas técnicas experimentais têm utilizado as características
multifrequenciais de um pulso elétrico curto para obter o mesmo tipo de
resultados que a técnica de teste multifrequencial. Em princípio, essa
técnica é vantajosa, pois requer componentes eletrônicos mais simples
para processar os dados. Ela pode potencialmente gerar frequências mais
altas do que os sistemas de frequência fixa. Isso permitiria o ensaio de
materiais mais finos e materiais com condutividade elétrica muito baixa
(alta resistividade). O pulso de corrente parasita também pode ser um
pulso muito curto e de alta tensão, que pode ser usado para produzir
momentaneamente saturação magnética em uma peça ferromagnética. Isso
permitirá a detecção de falhas internas em materiais
ferromagnéticos.
4.8.4 Medições de Espessura de Metais.
Uma ampla faixa de espessuras pode ser medida com equipamentos de ensaio de correntes parasitas de baixa frequência.
4.8.5 Correntes parasitas de baixa frequência
Correntes parasitas de baixa frequência significam que a inspeção
requer frequências abaixo de 50 kHz. Equipamentos e técnicas de
processamento de dados aprimorados agora permitem o uso de frequências
de ensaio tão baixas quanto 55 Hz. Juntamente com equipamentos de plano
de impedância para medir a fase do sinal, isso proporcionou um meio
para testar materiais multicamadas espessos. É possível detectar
trincas profundas no subsolo, trincas em camadas intermediárias do
material e corrosão na parte posterior do material.
4.8.6 Teste de Dupla Frequência.
Esta
é uma versão básica do teste multifrequencial que pode ser usada para
filtrar uma condição indesejada. Se apenas duas frequências forem
usadas, um canal de frequência pode operar no modo de sonda diferencial
e o outro canal de frequência pode operar no modo absoluto. Com esta
configuração, o modo diferencial pode ser usado para detectar
indicações discretas, como pequenas trincas e furos. O modo absoluto
pode ser usado simultaneamente para registrar a espessura da parede ou
outras alterações dimensionais na peça ensaiada.
- 4.9 Técnicas Eletromagnéticas
- Intimamente relacionadas à corrente parasita. Embora não façam parte do método de
CP conforme definido atualmente, as seguintes técnicas estão mais
intimamente relacionadas à CP do que a qualquer outro método básico de
END.
4.9.1 Ensaios de Ruído de Barkhausen em Materiais Ferromagnéticos.
Tensões
anormais induzidas por jateamento, outros processos de trabalho a frio
e queimas locais por retificação afetam as propriedades estruturais de um
material e podem levar ao crescimento de descontinuidades e à falha de peças. Em
materiais ferromagnéticos, esses processos afetam a facilidade com que
os domínios magnéticos na superfície do material podem ser movidos. Em
materiais ferromagnéticos não magnetizados, os domínios magnéticos são
orientados aleatoriamente. Se o material for submetido a um campo
magnético, os domínios magnéticos tendem a se alinhar na direção do
campo magnético. Quando os domínios se movem para se alinhar, pulsos
elétricos são gerados durante o movimento do domínio, o que é chamado
de ruído de Barkhausen. Esse ruído elétrico pode ser detectado e medido
por sensores de efeito Hall. Se o material estiver livre de tensões
anormais, os domínios são relativamente livres para se mover e pouco
ruído de Barkhausen é gerado. Áreas de tensão de tração paralelas ao
campo magnético aplicado causam um aumento no ruído de Barkhausen.
Exemplos de aplicações deste método de ensaio são componentes de motores
ferromagnéticos e trens de pouso. Medições de ruído de Barkhausen
também são usadas para detectar a qualidade da perfuração e alargamento
de furos em materiais ferromagnéticos.
4.9.2 Imagem Magneto-Óptica ("MOI").
A
imagem magneto-óptica depende da capacidade de certos materiais de
rotacionar o plano de polarização da luz na presença de um campo
magnético. Este Efeito Faraday é usado para detectar perturbações no
campo magnético produzidas pela passagem de uma corrente alternada em
uma fina lâmina plana de ferro dopada de ítrio. Quando a
lâmina é colocada próxima à superfície de um objeto metálico ensaiado,
correntes parasitas são produzidas, as quais modificam o campo
magnético na lâmina. Quando defeitos ou outras descontinuidades
materiais, como rebites ou furos, desviam o fluxo uniforme de corrente
elétrica próximo à superfície do corpo de prova, campos magnéticos
perpendiculares à superfície do corpo de prova são produzidos, os quais
podem ser visualizados em tempo real por um sistema óptico
adequadamente projetado. Como o sistema fornece informações ópticas, os
resultados podem ser gravados em vídeo para análise e documentação
permanente.
- 4.10 Aplicação de Técnicas Avançadas.
- Várias
das técnicas e processos avançados discutidos acima não possuem
procedimentos de ensaio, controles de processo e procedimentos de
qualificação totalmente desenvolvidos e reconhecidos. A aplicação
específica de TODOS esses processos e técnicas DEVE estar de acordo com
os procedimentos aprovados e a aprovação de engenharia.
|