IAEA - Correntes Parasitas - Capítulo 5 - APLICAÇÕES
traduzido do livro: https://www.iaea.org/publications/8414/eddy-current-testing-at-level-2-manual-for-the-syllabi-contained-in-iaea-tecdoc-628rev-2-training-guidelines-for-non-destructive-testing-techniques
- Ensaio Superficial
- Ensaio Tubular
- Ensaio Multifrequência
- Exercícios do Capítulo 5
5. APLICAÇÕES
5.1.
Ensaio Superficial
5.1.1 Introdução
O ensaio superficial por correntes parasitas refere-se ao ensaio da
superfícies de componentes de várias formas quanto a falhas de
superfície ou subsuperfície, ou propriedades do material.
NT: Aqui no Brasil usa-se a designação Ensaio Superficial quando é
realizada com sondas, classificadas quanto a forma, como superficiais
5.1.2 Sondas e sua sensibilidade
A seguir estão descritos os tipos de sondas comumente usados em
ensaios superficiais, sua sensibilidade a várias condições e exemplos
de onde cada tipo de sonda é usado. Mais
informações sobre os tipos de sondas usadas para aplicações específicas
e sondas para aplicações especiais são fornecidas nas notas sobre essas
aplicações.
A sensibilidade das sondas de ensaio superficial padrão
As sondas superficiais padrão consistem em uma bobina
enrolada em um núcleo de plástico, ferrite ou outro material e são
usadas com o eixo da bobina normal à superfície de ensaio. A FIG 5.1 mostra uma sonda absoluta típica e o campo de correntes parasitas que ela induz. Sondas
diferenciais, com duas bobinas, uma em cada um dos dois braços
adjacentes do circuito da ponte, e sondas de reflexão, que contêm uma
bobina ou conjunto de bobinas que gera o campo de corrente parasita e uma segunda bobina ou conjunto de
bobinas que detectam a resposta do material ensaiado, também são usados algumas vezes. As bobinas de captação nas sondas de reflexão podem ser absolutas ou diferenciais. As
sondas de reflexão operam numa faixa de frequência mais ampla e uma
relação sinal-ruído mais alta do que outros tipos de sonda.
NT: As sondas reflexivas são também chamadas de duplas
Todas essas bobinas têm o fluxo magnético essencialmente normal à
superfície de ensaio e, portanto, produzem correntes parasitas em
caminhos circulares essencialmente paralelos aos enrolamentos da bobina
e à superfície ensaiada.
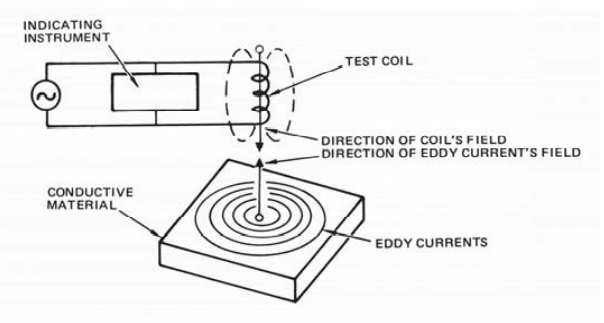
FIG. 5.1. Diagrama
esquemático mostrando uma bobina de ensaio de corrente parasita padrão e
o campo de corrente parasita induzido na peça de teste. O núcleo da bobina não é mostrado.
A
intensidade da corrente parasita é máxima, no material,
imediatamente abaixo do
enrolamento da bobina, que está próximo da
superfície da peça, e diminui linearmente até zero
no centro da
bobina. Além
disso, exceto para sondas blindadas (discutidas abaixo), o campo de
correntes parasitas se estende lateralmente por alguma distância da
bobina, a distância aumentando à medida que o diâmetro da bobina
aumenta, bem como também aumenta com o diâmetro, a profundidade de penetração. Portanto,
bobinas de grande diâmetro e baixa frequência, que apresentam a maior
profundidade de penetração, também apresentam o maior campo de
correntes parasitas laterais.
As falhas só podem ser detectadas se distorcerem o fluxo de correntes parasitas. Isso
significa que fissuras e falhas semelhantes normais à superfície de
ensaio em qualquer direção podem ser detectadas, mas falhas paralelas à
superfície de ensaio, como laminações, não podem ser detectadas.
No entanto, se uma falha for menor que o diâmetro da bobina, existe a
possibilidade de não ser detectada porque, dependendo de sua
localização e orientação em relação à bobina, pode não distorcer
significativamente as correntes parasitas (FIG. 5.2). Ou
seja, as falhas podem ser detectadas de forma confiável apenas se seu
comprimento for aproximadamente igual ou maior que o diâmetro da
bobina. Por isso, as
sondas para a detecção de pequenas falhas superficiais geralmente têm
bobinas de pequeno diâmetro (aproximadamente l mm a 2 mm de diâmetro),
embora se apenas falhas mais longas forem procuradas, bobinas de maior
diâmetro podem ser usadas.
Embora falhas com o mesmo comprimento que o diâmetro da sonda ou
maiores possam ser detectadas com segurança, desde que o avanço de
varreduras (a distância entre varreduras sucessivas) seja pequeno o
suficiente, a amplitude do sinal de trinca aumenta com o aumento do
comprimento da trinca até um máximo obtido quando a trinca é longa o
suficiente para distorcer todo o campo de correntes parasitas da
superfície.
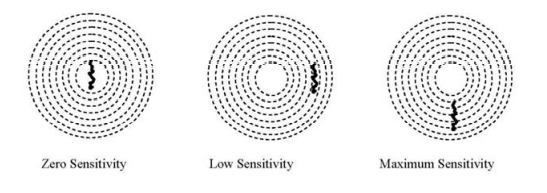
FIG. 5.2 Propriedade direcional de uma sonda superficial para um dato tamanho de trinca.
A profundidade das falhas a partir da superfície (a distância que a falha se
estende abaixo da superfície) também afeta a amplitude do sinal -
quanto maior a profundidade, maior a amplitude do sinal. A profundidade das falhas da superfície também afeta a fase do sinal. À medida que a profundidade da falha aumenta, ela distorce as correntes parasitas mais abaixo da superfície. À
medida que a profundidade das correntes parasitas abaixo da superfície
aumenta, elas mostram um atraso de fase (defasagem) cada vez maior em relação às
correntes parasitas da superfície, o sinal de falha mostra uma rotação
de fase correspondente no sentido horário (ver FIG. 5.3). Isso é verdade mesmo se a falha se estender além da profundidade efetiva de penetração. Neste
caso, uma vez que as correntes parasitas não podem fluir em seus
caminhos normais, elas fluem abaixo da falha e mostram um atraso de
fase crescente.
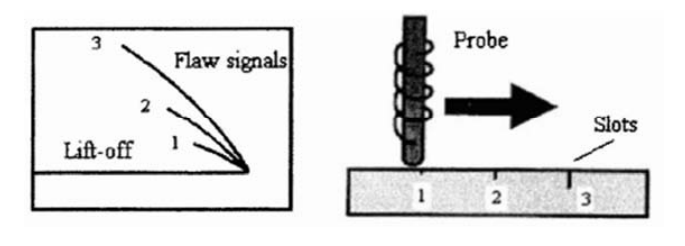
FIG.
5.3. Mostra de sinais obtidos de descontinuidades superficiais com
várias profundidades. Quando a profunidade da descontinuidade aumenta,
o a amplitude do sinal aumenta e a fase do sinal aumenta no sentido dos
ponteiros do relógio.
O
aumento da distância sonda-peça (desacoplamento da sonda, representado
pelo efeito de lift-off) sempre reduz a amplitude do sinal
correspondente a profundidade da descontinuidade, embora não
tenha efeito sobre a profundidade de penetração ou a fase das correntes
parasitas. Por esta
razão, as sondas devem ser mantidas de forma que o eixo da bobina seja
normal à superfície de ensaio (principalmente nas sondas com ponta
"rombuda"). No
entanto, apesar da sensibilidade reduzida, é prática comum aplicar um
pequeno pedaço de fita adesiva de Teflon nas pontas das sondas de
pequeno diâmetro para evitar o desgaste da sonda.
Tipos padrões de sondas para o ensaio de superfícies
(a) Sonda lápis ("Pencil probes")
As
sondas lápis são simplesmente sondas de pequeno diâmetro, com bobinas
de pequeno diâmetro e são a sonda normalmente utilizadas para a
detecção de falhas superficiais devido à sua sensibilidade a pequenas
fissuras (ver FIG.
5.4). As
sondas lápis são geralmente sondas de alta frequência para a
detecção de falhas superficiais, mas as sondas lápis de
baixa frequência também estão disponíveis e são usadas para a detecção
de falhas sub superficiais.
As
sondas lápis tipo Lang são sondas de lápis
padrão onde a
bobina está localizada alguns milímetros acima da ponta
da sonda (que entra em contato com a superfície a ser
inspecionada), mas
um núcleo de ferrite alongado canaliza o campo magnético
da bobina para
a superfície de ensaio, reduzindo assim os efeitos de
acoplamento (lift-off) (consulte a FIG. 5.5 uma). Esta construção implica em não haver um desgaste possível com o uso da bobina.
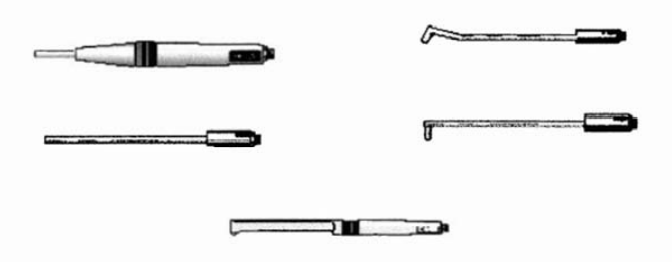
FIG. 5.4. Vários tipos de sonda lápis e uma sonda tipo faca ("knife",mais baixa). A sonda faca é equivalente a uma sonda lápis com uma curva em ângulo reto (inferior direito).
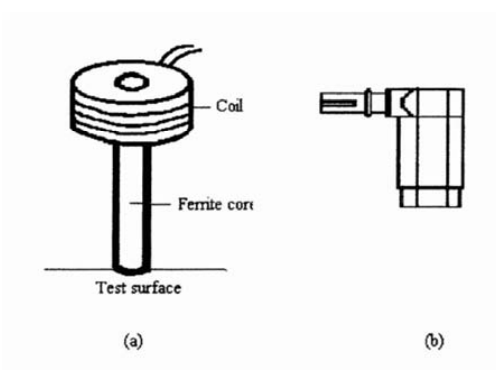
FIG. 5.5. (a) O núcleo e a bobina de uma sonda tipo lápis tipo Lang. (b) Uma sonda pontual.
b) Sondas pontuais ("Spot probes")
Sondas pontuais são sondas com uma face plana relativamente grande para ensaiar
superfícies planas quanto a falhas ou propriedades do material
(condutividade ou espessura) (ver FIG. 5.5b). O
diâmetro da bobina pode ser pequeno ou grande - o tamanho da sonda não
fornece necessariamente uma boa indicação do tamanho da bobina.
As sondas pontuais também podem ter entalhes em "V" ou faces curvas para
o posicionamento em superfícies curvas de forma a obter sinais estáveis.
NT: Embora no inglês sejam conhecidas como sondas pontuais, a melhor
denominação em português seria sondas superficiais amplas. Sondas
pontuais se aplicaria melhor as sondas tipo lápis ("pencil").
(c) Sondas acionadas por molas
As sondas pontuais são frequentemente acionadas por mola, como mostrado na FIG. 5.6, para garantir que a distância sonda-peça seja minimizada. Eles
são frequentemente usados para medição de
condutividade ou espessura de revestimentos não condutores. As
sondas de lápis raramente são carregadas com mola, mas os suportes de
sonda com mola estão disponíveis para sondas lápis de alguns
fabricantes.
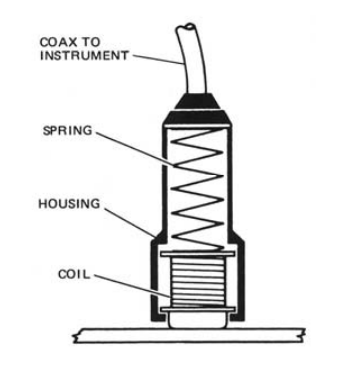
FIG. 5.6. Sonda acionada por mola.
(d) Sondas blindadas (isoladas) e com núcleos de ferrita
A
blindagem (isolamento ou concentração do campo magnético) é
frequentemente aplicada a sondas tipo lápis e, às vezes, a sondas
pontuaiss. O campo de correntes parasitas das sondas comuns não blindadas estende-se a uma certa distância lateral da bobina. A
extensão lateral do campo pode ser encontrada experimentalmente
posicionando uma sonda em uma superfície e movendo-a em direção a uma
borda da peça. A alguma
distância da borda, uma indicação (um sinal de borda, na realidade uma
modificação do sinal, mais ou menos constante existente quando afastada
da borda) será obtida. Os
sinais de borda estão localizados no primeiro quadrante no sentido
horário do sinal de lift-off, geralmente em um ângulo maior do sinal
de lift-off do que para sinais de trincas na superfície. Se a sonda for varrida perto de uma borda ou de um furo, o campo de correntes parasitas laterais dará um sinal de borda. Embora
seja geralmente evidente por seu ângulo que é um sinal de borda, um
sinal de trinca que pode estar presente simultaneamente pode não ser
detectado. Isso é particularmente um problema ao inspecionar entre dois furos ou um furo e uma borda. Pequenas
variações na distância da ponta de prova até a borda produzem uma
grande mudança no sinal da borda, produzindo um sinal ruidoso, e a
possibilidade de um sinal de falha não ser observado. Sempre
que possível o uso de um guia de sonda não metálico (para manter a
distância da borda constante durante a varredura) deve ser usado para
reduzir os sinais de borda sem afetar o sinal de trinca.
A varredura perto de um furo com a presença do pino fixador ("fastner") ou perto de uma mudança
brusca na geometria (espessura) pode causar problemas semelhantes ao do sinal de borda.
Sondas
blindadas, que geralmente contêm uma bobina enrolada em um
núcleo de ferrita e cercada por um cilindro vazado de ferrita, aço
inoxidável, ou cobre (ver FIG. 5.7), superam esses problemas
restringindo
a extensão lateral do campo de correntes parasitas. O
uso de sondas blindadas permite realizar varreduras próximo a qualquer
um desses inconvenientes ao ensaio citados sem interferir nos sinais. Sondas blindadas também podem ser usadas para medir o comprimento de uma fissura na superfície. A
sonda deve ser escaneada ao longo da trinca, monitorando o sinal e
verificando se a sonda permanece bem em cima da abertura da fissura movendo-a levemente
lateralmente para manter o sinal no máximo. À
medida que o final da fissura se aproxima, o sinal diminuirá em
amplitude e, eventualmente, retornará à posição de equilíbrio. Quando a sonda é retornada ao local onde o sinal de trinca aparece, a extremidade da fissura corresponde à localização da blindagem. A outra extremidade da trinca pode ser encontrada de forma semelhante.
NT: O procedimento indicado acima pode ser usado com
qualquer sonda superficial para determinar as extremidades das trincas,
mas evidentemente que as sondas blindadas apresentam uma maior precisão
nesse método.
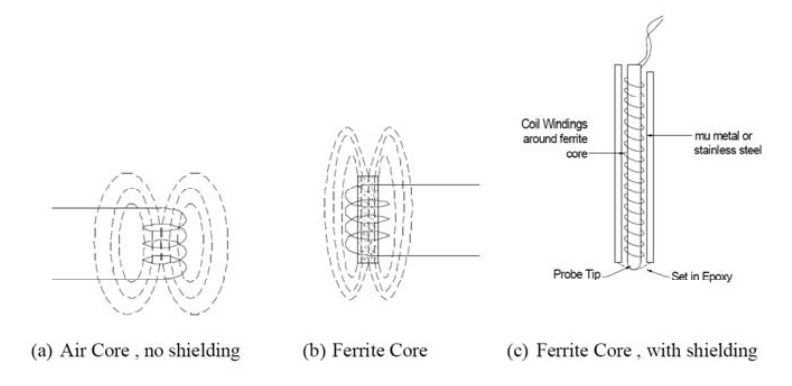
FIG. 5.7. Efeitos dos entreferros e das blindagens externas ("shields") na extensão do campo.
Outros tipos de sondas superficiais
(a) Sondas tangenciais
Em uma sonda tangencial, o eixo da bobina de ensaio é paralelo à
superfície inspecionada, com um lado da bobina próximo à superfície de ensaio (ver FIG 5.8). Imediatamente
abaixo da bobina, onde as correntes parasitas na peça de teste são mais
fortes, o campo magnético é essencialmente paralelo à superfície de
ensaio e na direção do eixo da bobina, e as correntes parasitas fluem
paralelamente à superfície em ângulos retos para o campo, na direção
dos enrolamentos da bobina. Os caminhos de retorno das correntes parasitas estão mais ao lado da bobina e abaixo da superfície.
Isso significa que a sensibilidade a trincas e falhas semelhantes
depende da direção da falha em relação à bobina, diferentemente das
sondas de superfície normais. Para as sondas tangenciais absolutas, a sensibilidade máxima a falhas
superficiais ocorre se a falha for paralela ao eixo da bobina e, à
medida que o ângulo entre a falha e o eixo da bobina aumenta, a
sensibilidade diminui, chegando a zero quando a falha está a 900º do
eixo da bobina (ou seja, paralelo as espiras da bobina). As
sondas tangenciais devem, portanto, ser usadas apenas quando forem
procuradas falhas em apenas uma direção devido a sua maior
direcionalidade. Uma
de suas aplicações comuns é a detecção de trincas de fadiga no raio de
curvatura das rodas de aeronaves, que sempre ocorrem na direção
circunferencial.
As sondas tangenciais permitem que toda a área de assentamento da sonda
seja ensaiada em uma única varredura, ao contrário das sondas de superfície
normais, que exigem várias varreduras porque uma bobina de pequeno
diâmetro precisa ser usada para detectar trincas curtas de maneira
confiável. Quando
uma sonda tangencial é usada, uma pequena fissura no raio de curvatura
das rodas de aeronaves sempre distorcerá as correntes parasitas,
embora, como a
distorção ocorre apenas em um local no caminho da corrente parasita, o
efeito relativo nas correntes parasitas é menor do que para uma sonda
superficial comum, onde, se a bobina estiver imediatamente acima da
trinca, a maior parte do campo de correntes parasitas é
interrompida. Isso
significa que o sinal da trinca não será tão forte quanto o de uma
pequena sonda tipo lápis, no entanto, a técnica mostra sensibilidade
adequada e é usada por várias grandes companhias aéreas com uma
conseqüente economia nos custos de operação.
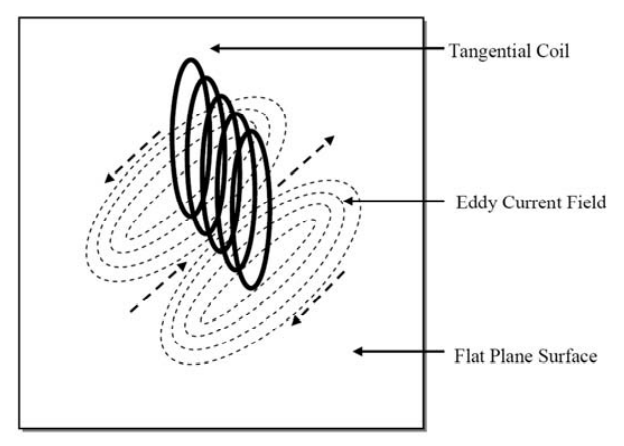
FIG. 5.8. A tangential probe showing the direction of the eddy currents at the test surface.
(b) Sonda com abertura ou ferradura ("Gap or horseshoe probes")
As
sondas com abertura ou ferradura usam um núcleo
ferromagnético em forma de "U" para conformar o campo
magnético da bobina de modo que fique essencialmente paralelo
à superfície de ensaio, conforme mostrado na FIG. 5.9. Isso produz laços de correntes parasitas em planos normais à superfície de ensaio. Na
superfície, as correntes parasitas fluem
perpendicularmente à linha que une as duas extremidades do
núcleo e que indicariam a direção do campo magnético introduzido na peça inspecionada. Conseqüentemente,
a máxima sensibilidade às falhas superficiais ocorre se a
falha for paralela a esta linha e, à medida que o ângulo
entre a falha e a linha que une as extremidades do núcleo
aumenta, a sensibilidade diminui, chegando a zero quando a falha
está formando um ângulo de 900 com está linha. Este
tipo de sonda é usado para a detecção de
delaminações em chapas, em vez de trincas ou outras
falhas normais à superfície de ensaio.
NT: Pode ser que esse tipo de sonda tenha sucesso na
detecção de falhas paralelas a superfície, o que é conhecidamente uma
limitação do ensaio de correntes parasitas. Não tenho conhecimento do
sucesso dessa aplicação, mas vi o uso desse tipo de sonda para a
medição de chapas de aço carbono com espessuras bem acima das quais o
ensaio de correntes parasitas costuma ser empregado.
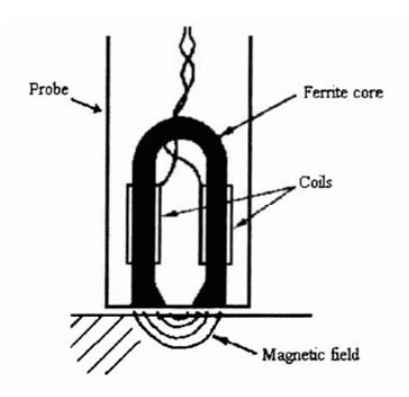
FIG. 5.9. Uma sonda com abertura (ferradura="horseshoe").
5.1.3 Ensaio de descontinuidades abertas a superfície
Introdução
O
ensaio de correntes parasitas para falhas abertas para superfície é uma das principais aplicações
do ensaio de correntes parasitas. É
amplamente utilizado para a detecção de trincas
relacionadas à fadiga e corrosão na
manutenção de aeronaves e para o ensaio em serviço
de estruturas soldadas quanto a presença de trincas. Inspeção por líquidos penetrantes e por partículas magnéticas também
são usados para detectar falhas na superfície e
têm a vantagem de que toda a superfície de peças
com formas complexas pode ser examinada em um único ensaio. O ensaio de correntes parasitas pode ser usado para ensaiar toda a
superfície de peçascom geometria simples, mas para formas
mais complexas, é apropriado apenas ensaiar uma pequena
área, geralmente um local onde é conhecida a
ocorrência de descontinuidades. A
vantagem do ensaio de correntes parasitas sobre o de líquidos penetrantes
é que ele pode detectar falhas mesmo se estiverem bloqueadas com
contaminantes, e pode detectar falhas abaixo da pintura e outros revestimentos. Para
materiais ferromagnéticos, a vantagem do ensaio de correntes
parasitas sobre o de partículas magnéticas é
que ele pode detectar fissuras abaixo de revestimentos de tinta mais
espessos do que é possível para o ensaio de
partículas magnéticas. Por esse motivo, é
preferível detectar trincas superficiais em estruturas de
aço soldadas com o ensaio de correntes parasitas. Além disso,
indicações não relevantes, um problema comum para o ensaio de
partículas magnéticas de soldas, são menos influentes negativamente no
ensaio de correntes parasitas de soldas.
O item seguinte discute as aplicações gerais do ensaio de correntes parasitas. O ensaio de soldas em estruturas de aço é considerado separadamente posteriormente.
Seleção de sondas e frequência
Quanto
mais o campo de corrente parasita é distorcido por uma falha, maior é o sinal de corrente parasita e
maior a probabilidade de a falha ser detectada. Portanto,
para detectar falhas superficiais rasas, o campo de correntes parasitas
deve ser confinado a uma camada superficial relativamente rasa (pouco profunda),
semelhante à profundidade das falhas necessárias para
serem detectadas. Para reduzir a profundidade de penetração, é necessária uma alta frequência. No
entanto, se a frequência for muito alta, a sonda se
tornará excessivamente sensível à rugosidade da
superfície e à distância sonda-peça, causando uma
relação sinal-ruído ruim e um conseqüente
declínio na confiabilidade da inspeção. Normalmente,
para ligas de alumínio, as frequências na faixa de
aproximadamente 200 kHz a 500 kHz são apropriadas, sendo
preferido aproximadamente 200 kHz. Para materiais de baixa condutividade como aço inoxidável, ligas de níquel, e
ligas de titânio, a penetração seria excessiva
nessas frequências, sendo necessárias frequências
mais altas. Normalmente, 2 MHz a 6 MHz devem ser usados.
Geralmente,
para detectar pequenas falhas, bobinas com um diâmetro pequeno,
não maior que o comprimento da falha são necessárias. Além
disso, a falha em serviço ocorre com mais frequência nos locais da peça
com uma mudança de seção, entalhe de forma ou na raiz de rosca. Portanto,
sondas tipo lápis de pequeno diâmetro dão bom
acesso a tais superfícies de ensaio e são mais comumente
usadas, embora sondas pontuais (mais amplas) com uma bobina de pequeno diâmetro
possam ser usadas em superfícies planas ou onde a curvatura da
superfície de ensaio é constante e não muito
grande (menores diâmetros de peças). Se forem
procuradas apenas falhas relativamente grandes, podem ser utilizadas
sondas de maior diâmetro, com a conseqüente
redução do número de passadas necessárias
para escanear uma determinada área de ensaio.
Sondas
absolutas são quase sempre usadas para detecção de
descontinuidades superficiais, com sondas diferenciais sendo usadas
apenas para aplicações especiais, como o ensaio de furos,
discutidos posteriormente. A sonda pode ser blindada ou não. Sondas blindadas devem ser usadas para ensaiar a periferia de orifícios.
Se
o parafuso, pino ou rebite de fixação não for removido, as trincas normalmente
serão detectadas apenas elas se estenderem razoavelmente além do fixador.
Para detectar fissuras sob os fixadores, uma sonda na forma de anel ou uma sonda chamada deslizante deve ser usada. Estas sondas são discutidos posteriormente sob o título 'Detecção de falhas superficiais'. Sondas
blindadas também devem ser usadas para ensaiar perto de bordas,
em mudanças na seção, como em ranhuras, raízes de rosca e, se estiver ensaiando material não
ferromagnético, onde há um material ferromagnético
adjacente. Além
disso, como o campo de correntes parasitas de sondas blindadas é
muito mais confinado do que o de uma sonda não blindada com o
mesmo diâmetro de bobina, as sondas blindadas são capazes
de detectar trincas menores e, portanto, devem ser usadas sempre que
for necessário detectar trincas muito pequenas. Sondas
não blindadas podem ser usadas em outras situações e têm a vantagem de
que, como possuem correntes parasitas mais espalhadas lateralmente,
menor número de passes de inspeção são necessários para cobrir uma
determinada área de ensaio.
Sondas
blindadas são mais sensíveis a mudanças na
geometria e vibrações durante o manuseio da sonda, também a separação
de fase dos sinais é reduzida tornando a
interpretação mais difícil. O
uso de guias de sonda pode reduzir esse problema, assim como o uso de
sondas com projeto especial para aplicações
específicas.
A seguir apresenta-se alguns exemplos de sondas especialmente projetadas:
(a) Componentes roscados
Sondas moldadas para um contorno de rosca específico, podem ser
fabricadas para detectar trincas nas raízes da rosca. Um exemplo é mostrado na FIG. 5.10. Tanto as roscas externas quanto as internas podem ser ensaiadas dessa forma.
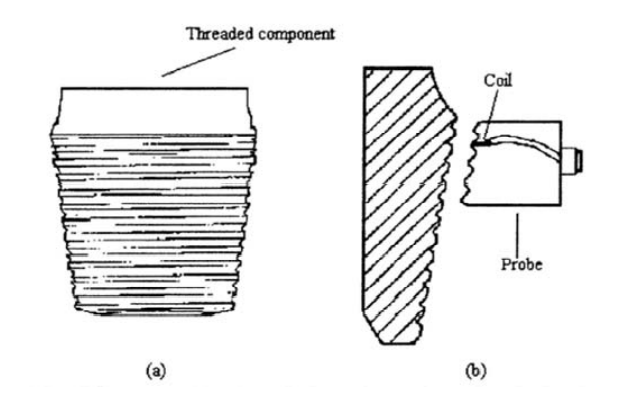
FIG. 5.10. Um componente roscado (a) e uma sonda projetada para testar trincas nas raízes da rosca (b).
(b) Furos
O
ensaio para a detecção de trincas ao longo dos furos dos parafusos ou com outra finalidade
é realizado usando sondas de furo, também chamadas de
sondas de furo de parafuso, que podem ser operadas manualmente ou
acionadas por motor. Uma
sonda de furo ainda é efetivamente uma sonda superficial, mas que foi encaixada em um suporte projetado para
esse fim. Cada sonda será construída para se ajustar a um orifício de diâmetro específico. As
sondas podem ser absolutas ou diferenciais, mas as sondas diferenciais
são mais comumente usadas porque eliminam os sinais das
extremidades, das interfaces entre as multiplas camadas de estruturas laminadas,
dos sulcos circunferenciais e das variações de acoplamento.
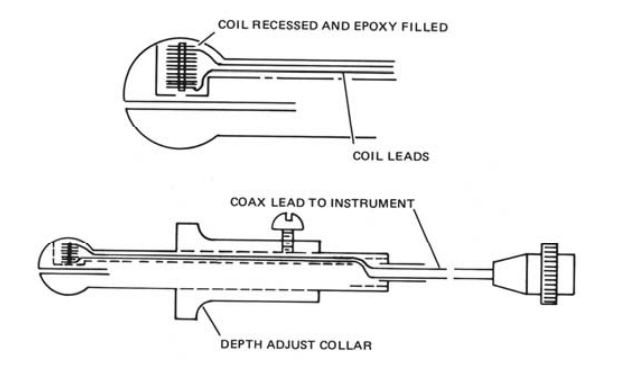
FIG. 5.11. Uma sonda de furo operada manualmente para detecção de trincas ao longo da superfície do furo.
Sondas superficiais comuns ou sondas de furos movimentadas por inspetores, geralmente consistem em um corpo de plástico
dividido, com o núcleo e o eixo da bobina em ângulo reto
com relação o eixo do suporte da sonda (ver FIG. 5.11). A
divisão permite que a sonda seja levemente comprimida para
entrar no orifício e, em seguida, expanda para pressionar as
paredes do orifício de modo a minimizar o lift-off. Para ensaiar
um orifício, a sonda é inserida até que a bobina
esteja dentro do lado mais distante do orifício furo, o batente
de profundidade é ajustado para ficar nivelado com a
superfície próxima e o parafuso de fixação do batente é
apertado. A sonda é então girada aproximadamente uma volta e um quarto, para garantir a cobertura total nessa profundidade. O
parafuso de ajuste é então afrouxado, a sonda é
retirada uma determinada quantidade, geralmente 1 mm a 2 mm, mantendo o
batente de profundidade nivelado com a superfície, então
o parafuso é reapertado. A sonda é novamente girada como antes.
Este
processo é confiável se executado com cuidado, mas
demorado e, especialmente se um grande número de furos for
testado, as sondas acionadas por motor são preferidas. Estas são invariavelmente diferenciais porque as sondas absolutas mostrariam ruído de acoplamento excessivo. Além
disso, as sondas diferenciais eliminarão os sinais da
extremidade e das interfaces (múltiplas camadas) dentro do orifício. As
sondas diferenciais são essencialmente cilindros com as duas
bobinas próximas a uma extremidade, lado a lado
circunferencialmente com seus eixos em ângulo reto com o eixo da
sonda (semelhante às sondas manuais). O
diâmetro da sonda é normalmente um pouco menor que o
diâmetro do furo (geralmente 0,2 mm) para facilitar a
rotação. Alternativamente,
sondas (bipartidas) divididas, diferenciais, semelhantes às sondas manuais,
às vezes são usadas para permitir variações
no tamanho do furo.
Se forem utilizadas sondas motorizadas, o instrumento de corrente parasita deve suportar esta facilidade. As
exibições são a exibição de ponto
vetorial normal e também uma exibição de base de
tempo (Y x t) que mostra a amplitude vertical dos sinais em
relação ao tempo, o período de tempo exibido pela
tela sendo ajustado automaticamente para corresponder a uma
rotação completa da sonda. A
posição de um sinal de falha ao longo da
exibição da base de tempo representa então a
posição angular da falha ao redor do furo em
relação a uma marca de referência na carcaça
do motor da sonda. Ao
configurar, um sinal é obtido no mostrador do tipo ponto vetorial de
uma descontinuidade em um furo em um bloco de referência, sendo o material e
o diâmetro do furo os mesmos que estão sendo ensaiados. Este sinal é girado até ficar na vertical e a amplitude definida, normalmente 80% da altura da tela inteira, o
sinal é então girado para 30o da vertical, no sentido
horário para materiais ferromagnéticos e
anti-horário para materiais não ferrosos (FIG. 5.12a). Uma fissura de fadiga estreita aparecerá então vertical como na FIG. 5.12b.
A
inspeção é realizada usando a
apresentação do tipo ponto vetorial para permitir a
interpretação da causa do sinal usando a análise
de fase. Para
localizar a posição circunferencial da falha, o mostrador
é comutado para o display de base de tempo (FIG. 5.12 c &
d).
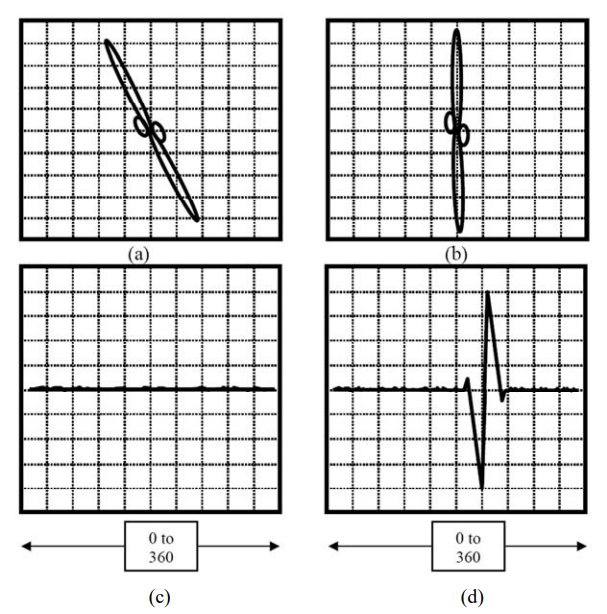
FIG. 5.12. Tela
do aparelho típica da inspeção com sonda de furo com motor mostrando a
apresentação tipo ponto vetorial (a) e (b) e apresentação tipo base de
tempo (c ) e (d) e mostrando um sinal de trinca (d). Os dois picos são produzidos porque uma sonda diferencial é usada.
(c) Rodas do trem de pouso de aeronaves
Rodas
de trem de pouso de aeronaves têm a possibilidade de desenvolver
trincas de fadiga na região de raio de assentamento das bordas do pneu
na roda com as trincas crescendo circunferencialmente ao longo do raio,
é então uma prática corriqueira ensaiar essa região, e algumas vezes
também outras regiões, pelo ensaio de correntes parasitas
Se
uma sonda superficial convencionar for usada para ensaiar essa raio de
assentamento, ela deve ter um pequeno diâmetro da bobina de formas a
detectar pequenas trincas. Entretanto, o raio é relativamente amplo,
especialmente para rodas grandes, então um grande número de passes de
varredura é necessário para ensaiar a área toda. Para garantir que toda
a área foi ensaiada, é comum na prática usar um bloco guia da sonda,
consistindo de um bloco plástico fabricado para se ajustar
perfeitamente ao raio da roda sendo ensaiada, com um quantidade de
furos de diâmetro conveniente para permitir que sondas delgadas do tipo
lápis (como o tipo mostrado na região central esquerda da FIG. 5.4)
sejam ali inseridas, e posicionadas em locais do raio com pequenos
intervalos entre eles (ver FIG. 5.13a). Para maior confiabilidade, a
sonda deve ser razoavelmente fixada com firmeza no furo, e os furos
devem ter uma pequena superposição de posição entre eles para cobrir
completamente toda região do raio. O ensaio é executado ajustando o
bloco ao raio da roda, inserindo a sonda lápis no primeiro furo até que
toque a roda, balanceando o aparelho, varrendo o perímetro mais que uma
volta (para garantir que nenhuma área ficou sem inspeção) ao redor na
região de assento do pneu. A sonda passa a ser inserida no segundo furo
e o processo todo repetido em todos os furos do bloco, até que toda
roda seja inspecionada. Uma mesa rotativa é muito útil por permitir que
a roda seja rotacionada suavemente durante a varredura, com o inspetor
simplesmente mantendo a sonda em posição.
Aparelhos automatizados que realizarão varreduras desse tipo sem guia de sonda estão disponíveis. Os mais sofisticados realizam automaticamente a calibração antes e
depois dos ensaios e fornecem uma impressão ou registro da inspeção em
computador de todo o processo.
Uma alternativa ao uso de sondas de superfície padrão é usar uma sonda tangencial, como mostrado na FIG. 5.13b. A
sonda é moldada para se ajustar ao raio da sede curvatura da
superfície que está sendo ensaiada, então a bobina
é encaixada
em uma ranhura rasa existente no corpo da sonda. Todo o raio da sede do pneu na roda é ensaiado em uma única varredura. A
sensibilidade não é tão grande quanto a de uma
pequena sonda tipo lápis, mas é adequada para o
propósito da inspeção.
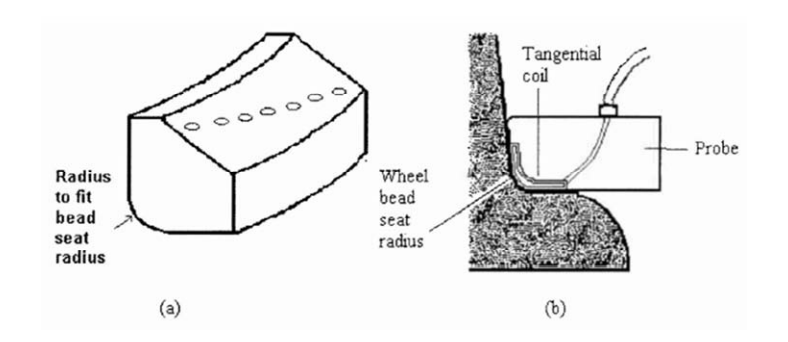
FIG.
5.13. (a) Suporte guia de sonda apropriado para o ensaio da roda na
região típica do surgimento de trincas na roda de aeronaves. (b) Uma
sonda tangential sendo usada para varrear a região do raio de curvatura
da roda necessária de inspeção.
Bloco de referência
É
essencial usar um bloco de referência contendo uma ou mais falhas
superficiais reais ou artificiais conhecidas para verificar se
o aparelho está funcionando satisfatoriamente e ajustar o
ganho para um nível adequado. Um
bloco de referência típico para falhas superficiais é um bloco de
material de condutividade
semelhante ao que está sendo ensaiado, com três ranhuras
produzidas por eletroerosão em uma face (consulte a FIG. 5.3). As
ranhuras têm 0,2 mm, 0,5 mm e 1,0 mm de profundidade,
respectivamente , Um bloco de referência de liga de
alumínio, geralmente fabricado a partir da liga de
alumínio 7075-T6, é adequado para uso ao ensaiar todas as
ligas de alumínio, latão e outros materiais de
condutividade relativamente alta, também pode ser usado para ensaiar
ligas de magnésio, mas devido à sua a
condutividade é um pouco menor, é preferível um
padrão de referência de magnésio. Blocos de referência de aço
carbono, aço inoxidável, ligas de titânio são também disponíveis
e devem ser usados quando ensaiando esses materiais específicos.
Embora
esses blocos possam ser usados para calibrar o aparelho para ensaiar
peças de qualquer formato. Para ensaiar roscas, ranhuras ou
entalhes e para ensaiar trincas em furos, onde o campo de correntes
parasitas difere daquele para uma superfície relativamente
plana, é recomendado fortemente que seja usado um bloco de
referência do material e configuração que
está sendo ensaiado, com uma ou mais falhas superficiais
reais ou artificiais conhecidas (geralmente um entalhe produzido por eletroerosão) no local em que as falhas são
esperadas. Essa
abordagem também é frequentemente usada com outras
peças de ensaio, por exemplo, o raio do assento do pneu das rodas de
aeronaves, porque ela oferece um maior grau de garantia de que
as falhas necessárias para serem detectadas podem ser
encontradas.
Procedimento de ensaio
O procedimento geral para detecção de falhas na superfície é o seguinte:
Padronização
- (a)
Conecte a sonda a ser usada ao aparelho, ligue o instrumento de ensaio,
realize uma verificação da condição da bateria e deixe o instrumento
aquecer por pelo menos 5 minutos. NT: Esse procedimento não é mais
necessários nos modernos aparelho eletrônicos digitais
- (b) Certifique-se de que a área de ensaio esteja limpa e livre de tinta solta, sujeira ou outros contaminantes.
- (c) Selecione a frequência necessária e ajuste o ganho para o meio da faixa do aparelho.
- (d) Posicione
a sonda no bloco de referência em um local distante das
descontinuidades de referência com o eixo da bobina em ângulo reto com
a superfície e balanceie o instrumento. Ajuste o ponto luminoso, se necessário, para aproximadamente o centro da tela. O
ponto pode ser localizado no quadrante inferior direito, se desejado,
para permitir mais espaço para visualizar os sinais à direita
(lift-off) e para cima (sinais de falha).
- (e)
Levante a sonda ligeiramente da superfície para obter um sinal de
lift-off e ajuste a fase de modo que o aumento do lift-off dê um sinal
horizontalmente para a esquerda, levantando e abaixando continuamente a
sonda até a superfície de ensaio para monitorar o sinal de lift-off
durante este ajuste.
- (f) Faça
uma varredura sobre a descontinuidade apropriada no bloco de referência
e então ajuste a posição da sonda para obter um sinal máximo da
descontinuidade. Defina o ganho para que o sinal máximo da descontinuidade tenha a amplitude exigida pelo procedimento de ensaio. Um
requisito comum ao usar um bloco de referência padrão é ajustar o ganho
de modo que o componente vertical do sinal do entalhe de 0,5 mm seja um
terço da altura total da tela (ATT, consulte o sinal nº 2 na FIG. 5.3). Para
alguns instrumentos, alterar o ganho pode afetar o balanço, portanto,
pode ser necessário novamente balancear o aparelho e verificar se
os sinais de lift-off e descontinuidade e ajustar conforme necessário. Se
o instrumento permitir alterar a relação de ganho X (horizontal) para Y
(vertical), o ganho Y pode ser aumentado acima do ganho X, se desejado. Isso aumenta o componente vertical dos sinais de falha, tornando-os mais facilmente detectados e reduz comparativamente a amplitude do sinal de lift-off. Observe
que se os ganhos X e Y forem diferentes, a fase dos sinais é
distorcida em comparação com sua aparência normal. A diferença excessiva entre o ganho X e Y deve ser evitada.
- (g)
Posicione a sonda na superfície de ensaio com o eixo da bobina
em ângulo reto com a superfície e balanceie o aparelho. Reajuste
a fase, se necessário, para que o sinal de lift-off fique
horizontal à esquerda, mas não ajuste o ganho.
- (h) Escaneie as áreas de ensaio conforme necessário. A varredura não deve ser realizada a menos de 3 metros de máquinas elétricas alimentadas por CA. Os incrementos de varredura não devem exceder a largura da bobina de ensaio de uma sonda absoluta. Para
bobinas blindadas, o passo entre varreduras deve ser determinado
experimentalmente para garantir que toda a área a ser ensaiada seja
coberta, mas um passo de varredura de metade do diâmetro da bobina
geralmente é satisfatório. Registre os resultados e qualquer outra informação necessária.
- (i)
Durante o teste por longos períodos de tempo, a sensibilidade deve ser
verificada novamente, e ajustes devem ser feitos, se necessário, em
intervalos de aproximadamente 30 minutos e na conclusão do ensaio
(Algumas normas requerem verificações mais frequentes). Este
procedimento de calibração deve incluir
verificações de condição da bateria e
verificações de sensibilidade. Se
um aparelho estiver fora da calibração, todas as áreas inspecionadas
desde a última verificação de calibração aprovada anterior devem ser
inspecionadas novamente. Além
disso, o instrumento deve ser recalibrado se qualquer parte do sistema
for substituída ou se quaisquer configurações de controle que possam
afetar a calibração forem alteradas.
Inspeção em serviço de soldas em materiais ferromagnéticos
As soldas completas normalmente não são ensaiadas quanto à qualidade da
soldagem pelo ensaio de corrente parasita devido à profundidade
limitada de penetração da corrente parasita. Isto é especialmente
verdade para materiais ferromagnéticos, porque a permeabilidade reduz a
penetração. No entanto, as soldas em serviço são frequentemente
ensaidas para trincas relacionadas à fadiga ou corrosão por ensaios de
correntes parasitas em vez de ensaios de partículas magnéticas devido à
sua capacidade de detectar trincas através dos revestimentos de tinta
muito mais espessos e porque é mais rápido e a interpretação dos
resultados é geralmente mais fácil. As trincas por fadiga podem ser
detectadas de forma confiável através de espessuras de tinta de até 2
mm por ensaio de correntes parasitas, enquanto que para obter
indicações de partículas magnéticas mesmo de trincas grandes, a tinta
deve ter menos de 0,5 mm de espessura.
Sondas especiais são usadas para ensaiar soldas em material
ferromagnético. As sondas de ensaio superficiais convencionais emitem
sinais muito ruidosos devido a variações na condutividade e na
permeabilidade, particularmente esta última, que resultam de diferenças
na composição e estrutura, e porque a configuração da solda causa
variações no lift-off. As sondas projetadas para ensaio de solda são
sondas diferenciais, que reduzem esse ruído a um nível aceitável. De
fato, um projeto comum para sondas de ensaio de solda é uma sonda
tangencial diferencial, com ambas as bobinas tangenciais, mas a 90o uma
da outra (ver FIG. 5.14). As duas bobinas estão no mesmo local, de modo
que os enrolamentos se cruzam, como o equador e um círculo que passa
pelos pólos norte e sul da Terra. Embora diferentes fabricantes
produzam sondas com uma variedade de formas, um dos tipos mais comuns
de sondas para ensaio de solda possui ponta semicilíndrica, e
destina-se a ser operado com o eixo do semicilindro paralelo à solda.
Dessa forma, uma bobina fica paralela à solda e o plano da outra,
transversal à solda. Como as correntes parasitas produzidas na
superfície sob bobinas tangenciais fluem ao longo da superfície na
direção dos enrolamentos, as correntes parasitas produzidas pela bobina
enrolada paralelamente à solda também são paralelas à solda e,
portanto, detectarão trincas transversais, mas não trincas
longitudinais . Da mesma forma, as correntes parasitas produzidas pela
bobina enrolada transversalmente à solda também são transversais à
solda e, portanto, detectarão trincas longitudinais, mas não trincas
transversais. Portanto, quando essas duas bobinas são conectadas
diferencialmente, elas darão um sinal para uma fissura transversal ou
longitudinal. Se uma trinca estivesse presente a 45° da solda, o que,
felizmente, é extremamente improvável, ela não seria detectada porque
as correntes parasitas de ambas as bobinas seriam distorcidas
igualmente por ela. As diferentes sensibilidades das duas bobinas
também explicam por que os sinais de trincas das sondas de varredura de
solda não têm a forma típica de sinal diferencial. Uma vez que apenas
uma bobina detecta a trinca, o ponto simplesmente desvia quando a sonda
se aproxima da trinca e retorna à posição de equilíbrio após a passagem
da sonda.
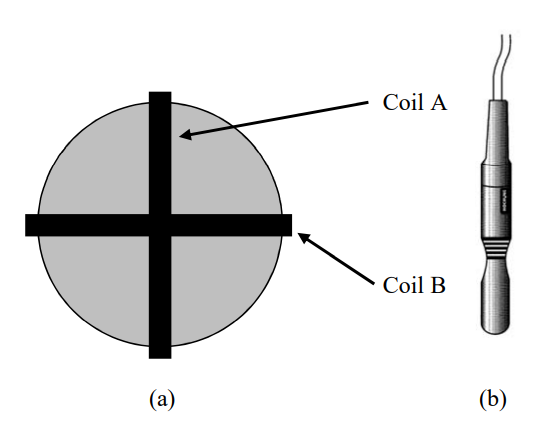
FIG.
5.14 (a) Sonda típica para inspeção de solda, arranjo das bobinas
(vista superior, planta). (b) Sonda típica para o ensaio de solda.
Frequências de ensaio de
aproximadamente 100 kHz foram consideradas satisfatórias para
ensaiar estruturas ferromagnéticas para detectar trincas superficiais,
embora frequências mais altas possam ser usadas.
O instrumento deve ser calibrado usando um bloco de referência de aço com falhas artificiais. Geralmente, são entalhes usinados por eletroerosão de 0,5 mm, 1 mm e 2 mm de profundidade. Se
as soldas forem pintadas, deve-se medir primeiro a espessura da tinta,
depois realizar a calibração com lâminas
plásticas da espessura da tinta sobre as descontinuidades
artificiais. Como as
sondas são diferenciais, não há um sinal claro de
lift-off para usar como sinal de referência para ajustar a fase,
embora os pontos de balança com a sonda no ar e a sonda em um
material ferromagnético geralmente diferem ligeiramente porque a
impedância diferente do bobinas no material ferromagnético
altera a impedância do circuito da ponte. Depois
que o instrumento é balanceado no bloco de referência, a
fase é normalmente ajustada para que os sinais de falha sejam
verticais.
Para
o ensaio, o instrumento deve ser balanceado na estrutura a ser ensaiada
em um local distante da área soldada para evitar possivelmente o
balanço infelizmente na região de uma trinca, então a área a ser
ensaiada deve ser escaneada. Durante a varredura, a sonda deve ser mantida paralela à direção mais provável de trincas. Isso
também detectará fissuras em ângulos retos a esse
ângulo, mas o ponto será desviado para baixo em vez de
para cima. Se
o ponto de
equilíbrio estiver baixo na tela, os sinais descendentes podem
não ser distinguíveis do ruído. Se o ponto de balanço estiver muito
baixo na tela, os sinais descendentes podem não ser visíveis ou
distinguíveis dos sinais de ruído. Geralmente,
a sonda deve ser mantida em ângulos aproximadamente retos em
relação à superfície de ensaio, mas para
máxima sensibilidade ao escanear ao longo da margem das soldas, a
ponta de prova deve ser inclinada de modo que a ponta da solda fique
imediatamente abaixo da ponta da sonda. As
trincas por fadiga em estruturas soldadas são mais
prováveis na direção longitudinal, e a margem da
solda é o local mais provável de trincas por fadiga,
embora as trincas também possam ocorrer em outras partes da
solda ou metal de base adjacente. Para
escanear a zona afetada pelo calor e o metal original adjacente, deve
ser empregado um escaneamento em ziguezague em ângulos retos com
a solda. Para ensaiar o
cordão de solda, pode ser usada uma varredura em ziguezague ao
longo do cordão ou várias varreduras ao longo da solda,
dependendo da condição da solda. Se
uma trinca transversal for considerada provável, a varredura
com a sonda transversal à solda pode ser necessária,
embora tais trincas emitam sinais para baixo durante a varredura para
trincas longitudinais.
Se
a tela estiver configurada conforme indicado acima, trincas
paralelas à sonda produzirão uma deflexão vertical
do ponto. A
amplitude do sinal é aproximadamente proporcional à
profundidade das fissuras, de modo que a profundidade da fissura pode
ser estimada, se necessário, por comparação do
sinal com os sinais das ranhuras nos blocos de referência, com
uma lâmina plástica de espessura igual à da tinta
revestimento no local dos entalhes no bloco.
5.1.3 Detecção de falhas subsuperficiais
Introdução
A
profundidade de penetração do campo magnético
produzido pelas bobinas de ensaio por correntes parasitas e, portanto,
das correntes parasitas produzidas por este campo é altamente
dependente do diâmetro da bobina, quanto maior o diâmetro
da bobina maior a profundidade de penetração. Este
é o efeito predominante na limitação da
penetração de correntes parasitas e explica por que a
penetração é frequentemente muito menor do que a
calculada usando a fórmula de profundidade efetiva de
penetração. Normalmente,
o campo magnético na direção axial é
relativamente forte apenas para uma distância de aproximadamente
um décimo do diâmetro da bobina e cai rapidamente para
apenas aproximadamente um décimo da intensidade do campo
próximo à bobina a uma distância de um
diâmetro da bobina. Para penetrar profundamente, portanto, são necessários grandes diâmetros de bobina. No entanto, à medida que o diâmetro da bobina aumenta, a sensibilidade a pequenas falhas, superfíciais ou subsuperfíciais, diminui. Por
esta razão, a detecção de falhas por correntes
parasitas é geralmente limitada a profundidades mais comumente
de até aproximadamente 5 mm apenas, ocasionalmente até 10
mm.
Para
materiais ou componentes com seções transversais maiores,
o ensaio de correntes parasitas é geralmente usado apenas para a
detecção de falhas na superfície e
avaliação das propriedades do material, e a radiografia
ou ensaio ultrassônicos são usados para detectar falhas
abaixo da superfície, embora o ensaio de correntes parasitas
possa ser usado para detectar falhas perto da superfície (subsuperficiais). No
entanto, uma aplicação muito comum do ensaio de correntes
parasitas é para a detecção de falhas em materiais
finos e, para estruturas multicamadas, com falhas presentes em uma camada de
subsuperfície.
Seleção de sonda e frequência
Os
requisitos essenciais para a detecção de falhas superficiais são, penetração suficiente
para possibilitar sensibilidade de detecção das falhas subsuperficiais porventura desejada e
separação de fase suficiente dos sinais para definir a
localização ou a profundidade das falhas a serem
identificadas. À
medida que a profundidade padrão de penetração
aumenta, a diferença de fase entre descontinuidades de
diferentes profundidades diminui. Portant, dificultando a interpretação da localização ou profundidade das falhas.
Examplo:
- Se
a frequência for ajustada para obter uma profundidade de
penetração padrão de 2 mm, a
separação entre descontinuidades em 0 mm e 2 mm seria de
57°.
- Se
a frequência for ajustada para obter uma profundidade de
penetração padrão de 4 mm, a
separação entre descontinuidades em 0 mm e 2 mm seria de
28,5°.
Um
compromisso aceitável que dá tanto sensibilidade adequada
para falhas superficiais e separação de fase
adequada entre os sinais de falha do lado próximo e do lado
distante é usar uma frequência para a qual a espessura (t)
= 0,8δ. Nesta
frequência, o sinal de uma falha rasa do lado distante
está próximo a 90o no sentido horário do sinal de
uma falha rasa do lado próximo, então essa
frequência é denominada f90. Substituindo
t = 0,8δ na fórmula padrão de profundidade de
penetração e alterando Hz para kHz, obtém-se a
seguinte fórmula:
f90 = 280/ (t2σ)
(5.1)
onde
f90 = frequência de operação (kHz),
t = a espessura ou profundidade do material a ser ensaidado (mm), e
σ = a condutividade do material ensaiado (% IACS).
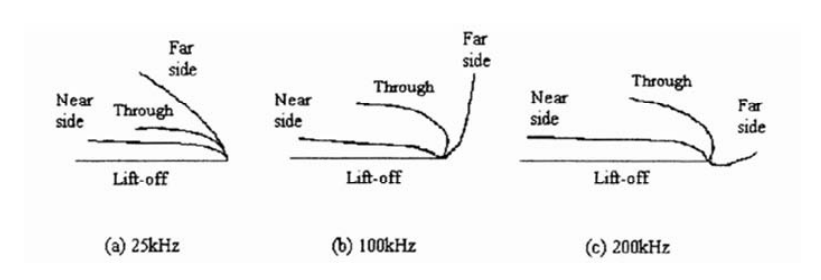
FIG. 5.15. Sinais
de corrente parasita de uma chapa fina com uma falha rasa no lado
próximo (lado da sonda), uma falha rasa no lado distante e um
orifício passante, em três frequências diferentes.
Em
25 kHz (a), a sensibilidade a falhas do lado distante é alta,
mas a diferença de fase entre os sinais do lado próximo e
do lado distante é relativamente pequena. Em 200 kHz (b), a separação de fase entre os sinais do lado próximo e do lado do jar é grande. mas a sensibilidade a falhas do lado distante é pobre. Para
esta parte do ensaio, uma frequência de ensaio de 100 kHz (b)
mostra boa sensibilidade para falhas do lado distante e boa
separação de fase entre os sinais do lado próximo
e do lado distante.
Para
obter profundidade de penetração adequada, não
só a frequência deve ser menor do que para a
detecção de falhas na superfície, mas
também o diâmetro da bobina deve ser maior. Em
superfícies planas, uma sonda pontual, absoluta ou de
reflexão, deve ser usada para obter sinais estáveis
(ver FIG. 5.16). Em superfícies curvas, deve-se usar uma sonda pontual com face côncava ou uma sonda tipo lápis. Sondas
pontuais acionadas por mola podem ser usadas para minimizar o lift-off,
e sondas pontuais blindadas estão disponíveis
para escaneamento próximo a bordas, fixadores (rebites em
chapas) e mudanças
bruscas na configuração geométrica.
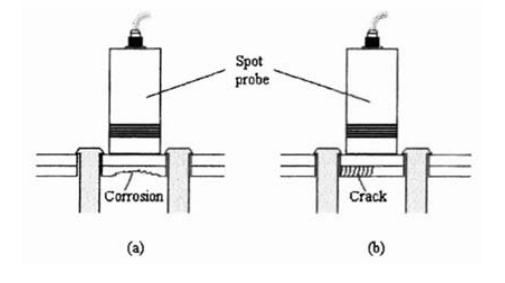
FIG. 5.16. Sondas
pontuais ensaiando uma estrutura em camadas para corrosão (a) e
trincas (b) na segunda camada de um laminado de duas camadas.
Duas sondas para aplicações especiais devem ser conhecidas:
Sonda em anel
Sondas em
anel são sondas em forma de toroide usadas para a
detecção de trincas na superfície e
subsuperfície ou outras falhas nos orifícios dos
fixadores (rebites) quando oensaio é realizado com os fixadores instalados
(ver FIG. 5.17 ). Essas
sondas são capazes de detectar trincas que não se
estendem muito longe do furo, por exemplo, aquelas que não se
estendem além da cabeça do fixador e, portanto, podem
não ser detectadas usando uma sonda localizada adjacente ao
fixador. As sondas em anel são geralmente sondas de reflexão absoluta e podem ser blindadas.
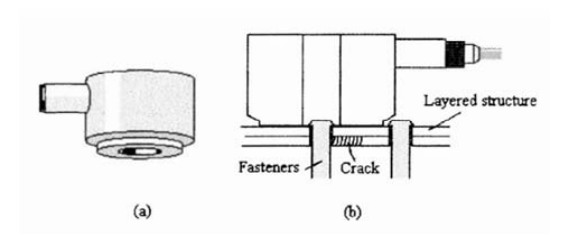
FIG. 5.17. (a). Sonda em anel. (b) Sonda de anel posicionada sobre um rebite para detecção de falha
Sondas deslizantes ("Sliding probes")
As sondas deslizantes
também são projetadas para detectar trincas na
superfície e na subsuperfície ou corrosão nos
orifícios dos rebites de fixação de chapas.
São projetadas para deslizar ao longo de uma fileira de
fixadores (consulte a FIG. 5.18). São sondas de reflexão,
geralmente com pelo menos duas bobinas de captação. Um
tipo tem uma bobina de acionamento central e quatro pequenas bobinas de
captação igualmente espaçadas em torno dela e
conectadas diferencialmente, todas alojadas em um único bloco.
Algumas sondas têm uma ranhura rebaixada ao longo do comprimento
da sonda para deslizar sobre as cabeças de fixação
salientes.
Sondas deslizantes emitem um sinal à medida que passam por um
fixador, mas se houver uma trinca ou corrosão, um sinal
caracteristicamente diferente e mais complexo é produzido. Para
estruturas multicamadas, sinais caracteristicamente diferentes
são dados para trincas que se estendem ao longo da fileira de
fixadores e para trincas que se estendem perpendicularmente à
fileira. Além disso, os sinais são diferentes para
trincas em cada camada. A interpretação é,
portanto, feita pelo reconhecimento do padrão
característico do sinal de cada condição, e
não pela análise do sinal. Uma amostra de
referência apropriada é essencial para que o operador
possa se familiarizar com os padrões de sinal. Um operador
experiente pode testar uma fileira de fixadores muito mais rapidamente
do que ao usar um anel ou outro tipo de sonda.
O
ensaio com multifrequência pode ser usado para eliminar sinais de
fixadores, de modo que os únicos sinais exibidos sejam sinais de falha. O
uso de inspeção multifrequência para a
detecção de trincas e corrosão subsuperficiais
está se tornando mais comum atualmente. Duas
aplicações da multifrequência são separar as variáveis existentes na
várias camadas e corrosão em profundidades semelhantes no material e
inspecionar por baixo dos fixadores instalados para detecção de trincas
onde os sinais causados pela presença dos fixadores podem ser
eliminados.
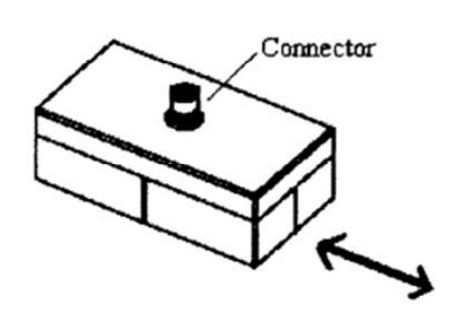
FIG. 5.18. A sliding probe intended for detecting surface and subsurface flaws by sliding it
along rows of fasteners in the direction of the arrows
Amostras de referência
As amostras de
referência devem ser, tanto quanto possível,
idênticas às peças a serem testadas. Eles devem ser
do mesmo material (ou material da mesma condutividade) e espessura das
peças a serem testadas e, se uma peça multicamada for
testada, cada camada deve ter o mesmo material (ou condutividade),
espessura e separação como as peças de teste.
Além disso, devem ter falhas reais ou artificiais simulando o
tipo procurado e nos locais e orientações em que as
falhas devem ser detectadas.
A corrosão pode ser simulada perfurando furos rasos, usando uma
broca padrão ou de fundo chato. Alternativamente, podem ser
usadas ranhuras fresadas. As trincas podem ser simuladas por entalhes
obtidos por eletroerosão ou por serras estreitas.
Procedimento de ensaio
Os procedimentos de ensaio são geralmente similares a aqueles de
detecção de trincas superficiais em outros métodos
de END.
5.1.4 Ensaio de condutividade e classificação de materiais
Introdução
O
teste de correntes parasitas pode ser usado para classificação de
materiais com base em que materiais diferentes, e até mesmo amostras do
mesmo material em diferentes condições de tratamento térmico, têm
valores diferentes de condutividade elétrica. A condutividade de um condutor pode ser medida usando um medidor de condutividade de corrente parasita dedicado. Alternativamente,
a maioria dos instrumentos modernos com mostrador ou tela de exibição
de impedância incluem um recurso de medição de condutividade digital
quando usado com uma sonda projetada para esta finalidade. Nenhum desses instrumentos fornecerá uma leitura de condutividade se um material ferromagnético for testado. Para
classificação de materiais, uma comparação da fase dos sinais de
lift-off obtidos das amostras desconhecidas com os sinais de materiais
de referência conhecidos pode ser suficiente: pode não ser necessário
determinar o valor real da condutividade. Esta abordagem pode ser usada com materiais não ferromagnéticos e ferromagnéticos. Teste
de condutividade ou classificação por comparação de condutividade
também pode ser usado para determinar a densidade de peças produzidas
por metalurgia do pó.
Condutividade e sua medição
A unidade SI de
condutividade é o Siemens/metro (S/m), mas por ser uma unidade
que representa uma condutividade muito pequena para os metais, seu
múltiplo, o megaSiemens/metro (MS/m) é mais comumente
usado. Os medidores de condutividade de corrente parasita geralmente
fornecem leituras na unidade prática de condutividade,% IACS (%
International Annealed Copper Standard), que fornece a condutividade em
relação ao cobre recozido comercialmente puro. Para
converter % IACS em MS/m, multiplique por 0,58, e para converter MS/m
em % IACS, multiplique por 1,724.
Por exemplo, a condutividade do aço inoxidável Tipo 304 é de 2,5% IACS ou 1,45MS/m.
A resistividade é o inverso da condutividade, e algumas
publicações sobre ensaios de correntes parasitas
referem-se a valores de resistividade em vez de valores de
condutividade. No entanto, a condutividade em % IACS é
universalmente usada nas indústrias de alumínio e
aeroespacial.
Fatores que afetam a condutividade
A condutividade de um metal
está relacionada à facilidade com que os elétrons
de condução presentes no metal podem se mover
através do material. Qualquer coisa que impeça o
movimento desses elétrons reduz a condutividade. Isso inclui
qualquer fator que estressa a rede cristalina. Geralmente, os fatores
que endurecem e fortalecem os metais também reduzem a
condutividade. Isso ocorre porque a maioria, embora não todos,
os mecanismos de endurecimento atingem seu endurecimento introduzindo
tensão na rede cristalina.
Os fatores que afetam a condutividade incluem o seguinte:
(a) Temperatura. - O
aumento da temperatura aumenta a amplitude de vibração
dos átomos, que por sua vez aumenta a impedância ao fluxo
de elétrons. Para leituras precisas, os padrões de
referência e a peça de ensaio devem estar na mesma
temperatura. Para maior precisão, a medição deve
ser realizada a aproximadamente 20oC, pois esta é a temperatura
para a qual os padrões de referência são
certificados e o efeito da temperatura na peça de ensaio e nos
padrões de referência podem diferir.
(b) Liga metalúrgica (composição química) -
A dissolução de qualquer elemento em um metal
sólido causa tensão na rede por causa dos diferentes
tamanhos dos átomos e, portanto, causa endurecimento e
redução da condutividade. As ligas, portanto, têm
menor condutividade do que o metal puro do qual são formadas.
Algumas impurezas em metais, mesmo em pequenas quantidades, podem
reduzir significativamente a condutividade. Por exemplo, 0,1% de
fósforo no cobre reduz sua condutividade de 100% IACS para 50%
IACS. Isso é importante, porque o fósforo às vezes
é usado para desoxidar o cobre durante seu refino e, nesse caso,
algum fósforo permanece no material. Este material, portanto,
não é adequado para aplicações de alta
condutividade.
(c) Tratamento térmico. - Muitas ligas podem ser endurecidas por
tratamento térmico, que introduz tensão na rede e reduz a
condutividade. Por outro lado, os processos de recozimento, que
geralmente consistem em aquecimento seguido de resfriamento muito
lento, aliviam as tensões na rede cristalina e, assim, reduzem a
dureza do metal ao mínimo e aumentam a condutividade ao
máximo.
(d) Trabalho a frio - A deformação plástica de
metais à temperatura ambiente introduz tensão na rede
cristalina, aumentando assim a dureza e reduzindo a condutividade. No
entanto, o efeito na condutividade é geralmente inferior a 10%
e, portanto, geralmente pode ser ignorado. Uma exceção
é o aço inoxidável austenítico, que
normalmente não é ferromagnético, pois pode se
tornar ferromagnético se trabalhado a frio. Isso tem um efeito
importante no sinal de corrente parasita e evita que uma leitura de
condutividade seja feita nos medidores de condutividade.
Fatores que afetam a leitura de condutividade
(a) Lift-off - Medidores de condutividade e instrumentos de
exibição no plano de impedância que incluem um
recurso de medição de condutividade digital normalmente
fornecem compensação de lift-off para valores de lift-off
de pelo menos 0,08 mm, de modo que a leitura não deve ser
afetada por revestimentos de tinta de até esta espessura ou por
menor rugosidade superficial. Se for considerado provável que a
leitura seja afetada por um revestimento ou rugosidade da
superfície, as leituras de condutividade devem ser feitas em uma
superfície que mostre a condição da peça de
ensaio e em uma superfície plana e lisa para determinar se uma
correção de lift-off é necessária .
(b) Espessura da peça ensaiada - A leitura de condutividade
será afetada se a espessura da peça de ensaioe for menor
que a profundidade efetiva de penetração, que, para o
diâmetro da bobina normalmente usado para o ensaio de
condutividade (aproximadamente 10 mm), pode ser considerado como 3
vezes a profundidade padrão de penetração. Se
houver dúvida se a peça ensaiada é suficientemente
espessa, ela deve ser testada, se possível, com e sem um bloco
de cobre encostado na superfície distante. Qualquer
diferença nas leituras indica que a espessura é menor que
a profundidade efetiva de penetração. A maioria dos
medidores de condutividade de correntes parasitas opera em uma
frequência fixa comum de 60 kHz. Isso é baixo o suficiente
para fornecer penetração suficiente para evitar qualquer
contaminação da superfície de ensaio com um efeito
significativo e alto o suficiente para permitir o teste de materiais
razoavelmente finos. Alguns medidores de condutividade têm uma ou
mais frequências de teste alternativas mais altas e, nesse caso,
uma frequência mais alta pode ser selecionada para evitar
penetração excessiva. No entanto, eles devem ser operados
na frequência mais baixa possível para a espessura da
peça ensaiada, a fim de evitar que qualquer
contaminação da superfície de teste tenha um
efeito significativo. A segunda frequência 'mais alta' é
comumente usada para determinar a espessura do revestimento.
Se a espessura da peça de teste for menor que a profundidade
efetiva de penetração, as peças podem ser testadas
determinando uma correção, ou para material tão
finos como folha, por empilhamento de várias espessuras de
material
(c) Efeito de borda - As sondas dedicadas ao teste de condutividade
são fabricadas de modo que não haja efeito de borda se a
área testada for igual ou maior que a área da sonda e a
sonda estiver centralizada nesta área. Ou seja, se a borda (ou
furo) estiver fora da área coberta pela sonda, não deve
haver efeito de borda. Isso deve ser verificado fazendo leituras em uma
amostra à medida que a sonda se aproxima de uma borda. Se uma
área menor for necessária para ser testada, uma sonda de
teste de condutividade menor deve ser usada, se disponível, ou
teste comparativo com um instrumento de corrente parasita padrão
e uma sonda de pequeno diâmetro ou blindada para determinar o
sinal de lift-off e compará-lo com aqueles de amostras de teste
conhecidas devem ser usadas.
(d) Curvatura - Superfícies curvas com pequenos raios de
curvatura podem dar uma leitura incorreta, o desvio aumentando com o
aumento da condutividade. Se for considerado provável que a
curvatura afete a leitura, uma correção deve ser
determinada.
Seleção da frequência
A frequência usada para medição de condutividade
geral é de 60 kHz, no entanto, onde a capacidade de detectar
mudanças muito pequenas na condutividade é
necessária, a frequência deve ser otimizada, de modo que a
mudança na impedância da bobina para uma pequena
mudança na condutividade seja a maior.
Se a compensação de lift-off for importante por causa de
uma superfície áspera ou de um revestimento não
condutor, o sinal de lift-off deve estar o mais próximo
possível de 90o do sinal de condutividade para mudança na
condutividade, porque os sinais são mais facilmente suprimidos
se forem em 90o para o sinal de interesse.
A FIG. 5.19 mostra os pontos de operação para
vários materiais em três frequências diferentes.
Pode-se observar que, à medida que a frequência aumenta, o
ponto de operação se move no sentido horário, mais
abaixo na curva de impedância. Além disso, a maior
separação dos pontos de operação para
materiais de condutividade diferente e, portanto, a maior sensibilidade
à condutividade é obtida se o ponto de
operação estiver na região central da curva de
impedância. Se possível, ensaios de condutividade e
classificação de materiais devem ser realizados com uma
frequência que traga os pontos de operação dos
materiais sendo testados para esta porção central da
curva de impedância. Além disso, se a
compensação de lift-off for importante o ponto de
operação deve estar na porção inferior
desta região, abaixo do 'joelho' da curva.
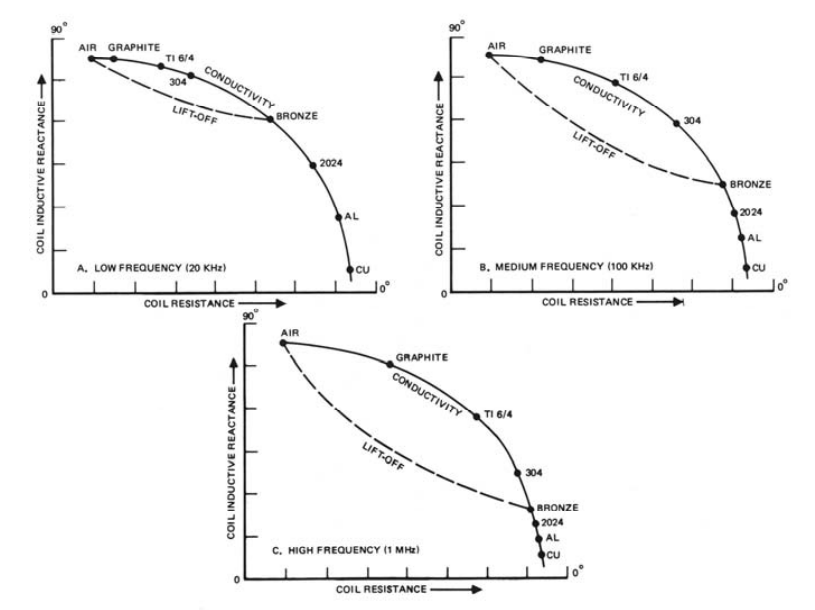
FIG. 5.19. Diagramas
de impedância e curva de condutividade em três frequências diferentes
A figura mostra que, à medida que a frequência aumenta, o ponto de operação
se move para baixo na curva de condutividade. Também
pode ser visto que o ângulo θ entre a condutividade e a curva de
lift-off é bastante pequeno para pontos de operação próximos ao topo
da curva de condutividade, mas maior nas partes intermediária e
inferior da curva. A
sensibilidade aumentada às variações de condutividade em direção ao
centro da curva de condutividade também pode ser observada.
O
Parâmetro Característico (PC) é um meio de
determinar o ponto de operação na curva de
impedância. A fórmula para PC depende das unidades utilizadas, mas o seguinte é recomendado:
PC = 4.6 × 10-3 f µr σ r2
(5.3a)
Ou
f = PC / (4.6 × 10-3
µr σ r2)
(5.3b)
onde
PC = parâmetro característico,
f = frequência (kHz),
µr
= permeabilidade relativa,
σ = condutividade (% IACS),
r = raio médio da bobina (mm)
Observe que a unidade de
frequência usada nesta fórmula, como nas outras
fórmulas de correntes parasitas 'aplicadas' (para f90 e f/fg )
é kHz, ao contrário das fórmulas teóricas
básicas para profundidade de penetração e
reatância indutiva.
Os cálculos de PC são usados em conjunto com a
FIG. 5.20, que relaciona o valor de PC com o ponto de
operação na curva de impedância para sondas de
superfície.
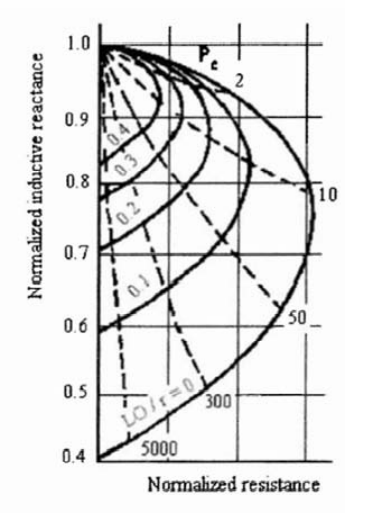
FIG. 5.20. Diagrama de impedância mostrando curvas de condutividade
para diferentes valores de lift-off em relação ao raio da bobina (LO/r)
(curvas sólidas) e curvas de diferentes lift-off (tracejadas).
Os valores de PC são indicados de zero lift-off na curva de
condutividade. Esses valores também se aplicam as localizações
correspondentes nas outras curvas de condutividade.
Exêmplo:
Calculo da ótima frequência para máxima sensibilidade na separação de
titânio comercialmente puro (condutividade aproximada de 2.5% IACS), da
liga Ti-6AI-4Va (conductivity 1% IACS), empregando uma bobina com
diâmetro 10 mm enrolada em um núcleo plástico de 6 mm.
Cálculo:
Para máxima sensibilidade a condutividade, um resposta mínima de
lift-off, o ponto de operação deve estar algo abaixo do joelho da curva
de impedância. Isso significa que PC deve estar entre 10 e 200. O
valor de PC será diferente para as duas ligas, mas, visto que PC éw
poroporcional a condutividade, os dois valores diferirão por um fator
de 2.5/1 = I (a razão entre as condutividades). Valores
disponíveis serão 30 para o titânio e 75 para o aço inoxidável, supondo
que valores similares sejam obtidos na faixa de 10 a 200 escolhida.
Isso é:
f = PC /(4.6 × 10-3
µr σ r2
)
PC = 30 (para o titânio),
r = (10 + 6)/2 = 8 mm, então r = 4 mm,
µr
= 1
σ = 1% IACS
Inserindo esses valores na equação vem:
f = 30/ (4.6 × 10 -3 × 1 × 1 X 4 2
)
= 407.6 kHz ou, empregando um valor arredondado por conveniência vem que:
= aproximadamente 400 kHz
Quando
os medidores de condutividade de correntes parasitas são usados,
essa abordagem normalmente não é possível, pois
eles operam em uma ou mais frequências fixas. Normalmente,
esses instrumentos são projetados para fornecer um ponto de
operação na região do joelho da curva na
frequência mais baixa possível, normalmente 60 kHz, e as frequências
mais altas são usadas apenas se o material for muito fino para ensaiar na frequência mais baixa.
Procedimento de teste usando um medidor de condutividade de corrente parasita
- (a) Posicionar o padrão de referência e
a peça a ensaiar na mesma área, e dar tempo para a
temperatura de ambos equalizar.
- (b) Ligar o instrumento e permitir seu aquecimento por um período de tempo de 5 minutos.
- (c)
Ajustar o instrumento de acordo com as instruções do fabricante. Se
possível, o ajuste deve ser feito ou checado empregando os padrões de
referência com valores de condutividade que difiram de pelo menos 10%
IACS, uma na faixa de 25 a 32% IACS e a outra na faixa de 38 a 50% IACS.
- (d)
Faça medidas de condutividade na peça desejada. Normalmente pelo menos
3 medidas devem ser realizadas em cada peça para estabelecer a
condutividade pela média, cada medida feita numa área diferente. A área
ensaiada deve ser plana, grande para evitar efeito de borda, e
espessura suficiente para não afetar a medida, e, se um revestimento
está presente, ele deve ser fino o suficiente para não afetar a medida.
Se qualquer dessas condições não pode ser alcançada , com o instrumento
e frequência empregados, uma frequência alternativa, sonda, ou
instrumento que alcance essas condições deve ser tentada. Se isso não
for possivel a correção da influência destes inconvenientes na medida
deve ser determinada experimentalmente para o material e condições de
teste particulares, e adicionada ou subtraida da leitura do
instrumento.
Procedimento de teste usando outros instrumentos de correntes parasitas
Se um instrumento de exibição de sinais no plano de
impedância estiver sendo usado para classificar materiais, os
sinais de lift-off devem ser obtidos de padrões de
referência adequados e os sinais de lift-off dos materiais a
serem testados devem ser comparados com estes. Por
exemplo, se for necessário classificar um material conhecido por
consistir em duas ligas diferentes conhecidas ou
condições de tratamento térmico, os sinais de
lift-off devem ser obtidos de várias amostras de cada material.
É
importante ter amostras suficientes para garantir que a faixa de
condutividade dos dois materiais não se sobreponha. O
instrumento é ajustado de modo que os sinais de lift-off de um
material estejam localizados em uma borda da tela e os sinais de
lift-off do outro material estejam localizados na outra borda da tela.
Os
detectores de falhas que possuem escalas de medição (analógicas ou digitais) podem ser usados para a
mesma finalidade, neste caso ajustando o instrumento de modo que as
leituras de um material fiquem em uma extremidade da escala e as
leituras do outro material fiquem na outra extremidade da escala.
Tratamento térmico de ligas de alumínio e sua verificação
Durante o endurecimento por envelhecimento de ligas de alumínio
ou titânio, a dureza e a condutividade do material mudam
simultaneamente, de modo que o grau de endurecimento pode ser obtido
medindo a condutividade do corpo de prova e comparando-o com um
padrão de aquele material com uma dureza conhecida. O operador deve estar ciente dos efeitos das descontinuidades e lift-off nas leituras do medidor.
Como
pode ser visto na FIG.5.21, uma condutividade típica de 35% IACS
pode ter uma dureza Rockwell B de 20 ou 85, a partir disso, podemos ver
que as medições de condutividade para danos causados
pelo calor devem ser acompanhadas de testes de dureza para confirmar
a condição verdadeira. Na
indústria de manufatura, a condutividade por si só pode
ser usada para confirmar a têmpera do material após o
tratamento térmico.
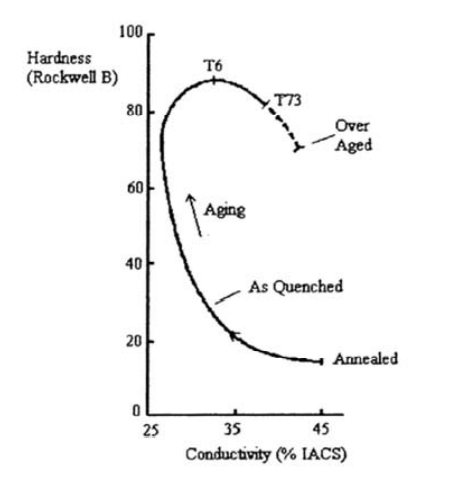
FIG. 5.21. Diagrama
mostrando a relação entre dureza e condutividade em
várias etapas do tratamento térmico, ligas de
alumínio-zinco 7075. Outras ligas de alumínio
tratáveis termicamente apresentam curvas semelhantes.
Classificando materiais por permeabilidade magnética
No
ensaio de correntes parasitas, a bobina de ensaio é
sensível a muitos parâmetros de teste, incluindo
permeabilidade magnética. Devido
ao efeito de amplificação causado pela permeabilidade
magnética, a medição de permeabilidade em
níveis elevados geralmente não é possível. No
entanto, muitas ligas paramagnéticas podem exibir propriedades
de permeabilidade e quase todas as ligas não magnéticas
podem receber inclusões magnéticas ou
contaminação durante a fabricação ou
serviço.
Em
frequências normais de ensaio de correntes parasitas, as
indicações magnéticas muitas vezes
parecerão semelhantes a descontinuidades. As
indicações magnéticas podem ser distinguidas das
descontinuidades por meio de um novo ensaio com uma frequência de
teste reduzida.
5.1.4 Medição de espessura de revestimentos não condutores
Introdução
A
espessura de revestimentos não condutores sobre bases condutoras é
medida avaliando a quantidade de lift-off que os revestimentos
produzem. A
técnica pode ser aplicada igualmente a materiais
ferromagnéticos ou não ferromagnéticos, e
também pode ser usada para medir a espessura de não
condutores como chapas plásticas, colocando-as em cima de um
condutor plano.
A
maioria dos instrumentos digitais modernos de correntes parasitas,
quando usados no modo de condutividade, fornecem uma leitura digital
tanto da condutividade quanto do lift-off (espessura do revestimento
não condutivo).
As
medições comparativas também podem ser feitas
usando o plano de impedância e são resumidas a seguir.
Seleção de sonda e frequência.
Qualquer
sonda superficial de reflexão absoluta ou
absoluta padrão pode ser usada, mas para obter sinais
estáveis e repetíveis, uma sonda com acionamento por mola deve
ser usada. Se
uma sonda do tipo lápis ("pencil probe") for usada, ela deve ser equipada com uma luva
ou sapata para que a oscilação da sonda seja eliminada
(consulte a FIG. 5.22a). Se
superfícies curvas devem ser testadas, uma sonda acionada por
mola na forma de um bloco em V, ou um bloco em V ou sapata com
contornos especiais deve ser usada pelo mesmo motivo (ver FIG. 5.22b).
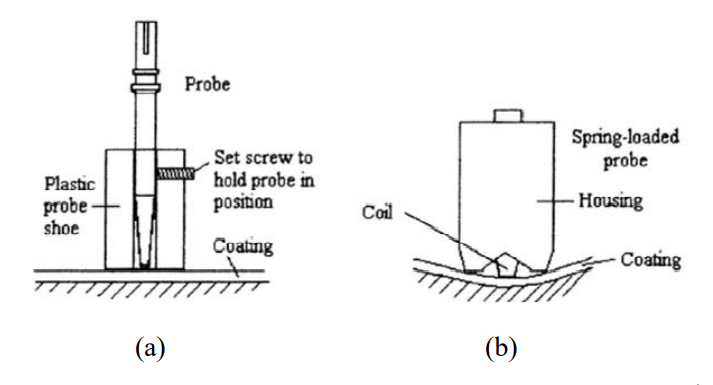
FIG. 5.22. Métodos
para obter leituras estáveis e repetíveis da espessura
do revestimento:
(a) Usando uma sonda lápis com uma sapata de
sonda. A sapata da sonda pode ser contornada para se ajustar a uma superfície curva.
(b) Usando uma sonda acionada por mola com entalhes em V em uma superfície curva. Superfícies convexas também podem ser testadas.
O
tipo preferido de sonda é uma sonda de reflexão absoluta,
de preferência com mola, e com entalhes em V se
superfícies curvas forem testadas. As
sondas de reflexão são preferidas porque mostram uma
curva de lift-off mais linear e respondem a uma faixa maior de valores
de lift-off. Observe que as sondas diferenciais não devem ser usadas porque eliminam ou reduzem o sinal de lift-off.
O
diâmetro da bobina é importante porque o tamanho do campo
magnético aumenta à medida que o diâmetro da bobina
aumenta. O
campo magnético de uma bobina a uma distância de um
diâmetro de bobina da bobina é apenas aproximadamente 10%
daquele adjacente à bobina, e uma intensidade de corrente
parasita muito baixa é produzida a essa distância. Os
campos magnéticos de bobinas de pequeno diâmetro podem
não se estender através de um revestimento espesso
até o substrato. Se
este for o caso, um sinal de lift-off não pode ser obtido e a
medição da espessura do revestimento não é
possível. Em geral, portanto, quanto mais espesso o revestimento a ser medido, maior deve ser o diâmetro da bobina. Observe que o tamanho de uma sonda não é necessariamente um bom guia para o tamanho da bobina. Algumas sondas de ponto possuem uma bobina de pequeno diâmetro em um alojamento de grande diâmetro.
A
medição da espessura do revestimento não condutor
pode ser realizada em uma ampla faixa de frequências, mas
é preferível selecionar uma frequência de ensaio que
forneça um ponto de operação na parte inferior do
diagrama de impedância. Há duas razões para isso.
- (a) O sinal para uma determinada quantidade de lift-off é maior na parte inferior da curva de impedância. A FIG. 5.20 mostra este efeito: para um valor de PC
de 300 (na parte inferior da curva), o sinal de lift-off para uma
valor de 5% do diâmetro da bobina (a curva rotulada como 0,1)
é aproximadamente 50% maior do que para um valor de PC de 10 (no joelho da curva) e aproximadamente 4 vezes maior do que para um valor de PC de 2 (no topo da curva).
- (b)
Quando operando na direção da parte inferior da curva de impedância, a
mudança do sinal para uma dada mudança da condutividade do substrato é
bem pequeno (ver FIG. 5.19), então o efeito de variações pequenas na
condutividade do substrato é reduzida. Adicionalmente, na parte baixa
da curva de impedância, ps sinais de lift-off e mudanças na
condutividade são razoáveis perto de 90o, então qualquer
mudança menor na condutividade do substrato terão pequeno efeito no
sinal de lift-off. Para a parte superior da curva de impedância,
os sinais de lift-off e mudanças na condutividade são separados por
apenas um pequeno ângulo, tornando-se dificil a distinção de ambos.
Uma
consideração adicional ao selecionar a frequência
é a profundidade de penetração das correntes
parasitas no substrato. É
preferível garantir que a profundidade efetiva de
penetração das correntes parasitas seja
significativamente menor que a espessura do substrato, de modo que as
variações na espessura do substrato não afetem o
sinal das correntes parasitas. Portanto,
para material fino, a profundidade efetiva de penetração
na frequência de teste proposta deve ser calculada e a
frequência aumentada se necessário.
Uma
frequência de operação típica para medir uma
espessura de tinta de 0,15 mm em um substrato de liga de
alumínio, condutividade de aproximadamente 30% IACS seria 300
kHz para medir a mesma espessura de tinta em uma liga de
magnésio, condutividade de aproximadamente 15% IACS, uma
frequência mais alta, até 1 MHz, seria o preferido. Isso
ocorre porque o ponto de operação depende não
apenas da frequência, mas também da condutividade (e do
diâmetro da bobina). Materiais
de baixa condutividade, portanto, requerem frequências mais altas
para trazer o ponto de operação para um local semelhante
ao dos materiais de alta condutividade. Geralmente,
à medida que a espessura a ser medida aumenta, o diâmetro
da bobina deve ser aumentado, conforme indicado acima. Isso
move o ponto de operação mais abaixo na curva de
impedância e, portanto, frequências mais baixas podem ser
usadas. Não há dificuldade nisso porque, em geral, bobinas de maior diâmetro são projetadas para operar em frequências mais baixas. De
fato, frequências mais baixas são recomendadas para
revestimentos mais espessos, a fim de evitar sensibilidade excessiva ao
lift-off e obter uma resposta mais linear. Por
exemplo, para uma espessura de 1 mm em um substrato de liga de
alumínio, deve-se usar uma frequência de aproximadamente
80 kHz.
Amostras de referência
A amostra de referência de substrato para
medição de espessura de revestimento não condutor
deve ter a mesma condutividade, contorno de superfície e
espessura do material a ser testado.
Para
amostras de referência para o revestimento, são
necessários calços de plástico rígido de
espessura apropriada. Se
a medição for do tipo passa/não passa, para
verificar se a espessura está dentro dos limites
aceitáveis, são necessárias apenas duas espessuras
de calço, uma com a espessura do limite inferior e outra com a
espessura do limite superior. No entanto, um terceiro calço, com espessura no meio da faixa, é desejável. Se,
no entanto, a espessura real do revestimento for medida, são
necessárias pelo menos três espessuras de calço. Estas
devem ter espessuras iguais às espessuras máxima e
mínima esperadas, e uma aproximadamente a meio caminho entre
elas. Se o revestimento necessário para ser medido for fino, metal nu pode ser usado para calibração. Mais espessuras de calços podem ser necessárias se a resposta for notavelmente não linear.
Procedimento de medição
- (a) Conecte a sonda ao aparelho a ser empregado, ligue o aparelho e permita que o mesmo aqueça por pelo menos 5 minutos.
- (b) Garanta que a área a ser medida esteja limpa e sem sujeira ou outro contaminante.
- (c) Seleciona a frequência requerida, e ajuste o ganho no meio da faixa.
- (d)
Aplique a sonda a amostra de referência, tanto na superfície nú, ou com
uma fina lâmina plástica sobre ela, balanceio o instrumento, e ajuste a
fase de forma que o sinal seja horizontal e se deslocando para a
esquerda.
- (e) Ajuste ponto luminoso na linha horizontal central e próximo a região direita da tela.
- (f)
Aplique a sonda a amostra de referência com a lâmina sobre a
superfície, sem rebalancear o sistema, cheque se o sinal aparece na
tela. Se visivel, o ponto deve estar a esquerda do sinal mostrado
anteriormente. Ajuste o ganho de forma que o ponto esteja localizado a
direção esquerda da tela. Se o ponto não estiver visivel, inicialmente
reduza o ganho até que apareça na tela, então reajuste o ganho para
localizar o ponto a esquerda da tela.
- (g)
Para alguns instrumentos, a mudança do ganho também muda o ponto de
balanço, devido a isso os passos (d), (e), e (f) devem ser repetidos
para garantir que o ponto esteja localizado na linha horizontal
central, na direção da extremidade direita da tela com a sonda
posicionada na menor espessura de pelicula ou no metal nu, e na direção
esquerda da tela com a sonda na pelicula mais grossa.
- (h) A posição do ponto quando a sonda está localizada na pelicula mais grossa deve ser marcada.
- (i) Posicionar a sonda nas outras espessuras de película, marcando a posição de cada ponto.
- (j)
Se medições de espessura são necessárias, construa gráfico da posição
horizontal do ponto, medida em milimetros ou número de divisões da tela
a partir da extremidade da tela, versus espessura de revestimento. Se o
gráfico é acentuadamente curvo, diferentes frequências podem ser
experimentadas para determinar se uma resposta mais linear é obtida.
Alternativamente, usar mais películas de referência de forma que uma
curva suave e precisa seja plotada. Uma vez que um gráfico satisfatório
é obtido, faça medições de espessura aplicando a sonda na peça a
insepcionar, medindo a horizontal posição do ponto a partir da
extremidade da tela, depois use o gráfico para determinar a espessura
da película.
- (k) Alternativamente, se a medição a ser realizada é para
verificar se a espessura de pelicula está entre dois limites de
espessura aceitáveis, mova o ponto verticalmente de forma na se
sobreponha (na tela) aos sinais das películas de referência, quando
aplicando a sonda na peça a medir. A espessura é aceitável se o ponto
está localizado entre as marcas dos limites inferior e superior para as
espessuras limites maior e menor.
- (l) Se um grande números de
medições são requeridas, a ajustagem do aparelho
deve ser verificada pelo menos a cada 30 minutos.
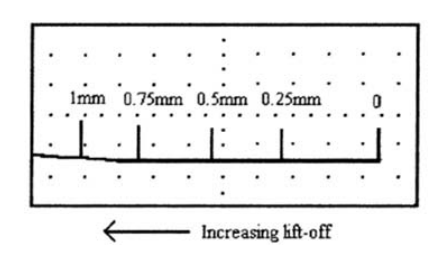
FIG. 5.23. A
exibição da tela para calibração/ajuste para medir
a espessura do revestimento não condutor na faixa de 0 mm a 1
mm. A
posição do ponto é marcada para cada padrão
de referência usando o controle de posição Y para
alterar a posição Y e, em seguida, retorná-lo
à sua posição original.
5.1.5 Medição de espessura de condutores
Introdução
A
espessura dos materiais condutores pode ser medida porque, desde que a
espessura seja menor que a profundidade efetiva de
penetração, o sinal de corrente parasita depende da
espessura (ver FIG. 5.24). O
teste ultrassônico também pode ser usado para
medição de espessura, mas a medição de
espessura por correntes parasitas é preferível para
materiais finos porque é mais fácil obter leituras
precisas. A
técnica também pode ser aplicada para medir a espessura
de um revestimento condutor em um não condutor, por exemplo,
revestimentos metálicos em plástico.
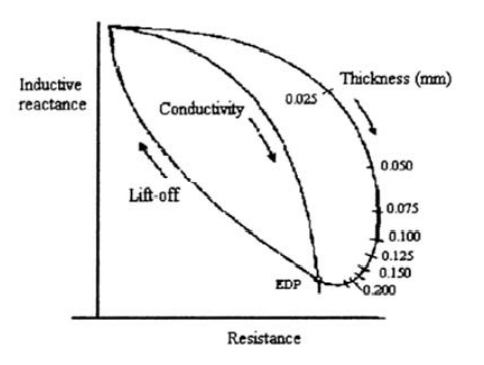
FIG. 5.24. Diagrama
de impedância mostrando a curva de condutividade e o locus dos
pontos de operação para latão vermelho fino
(condutividade de aproximadamente 40% IACS) a 120 kHz (a curva de
espessura). A curva de
espessura encontra a curva de condutividade quando a espessura é
igual à Profundidade Efetiva de Penetração (EDP=Effective Depth of Penetration).
Seleção de sonda e frequência
Os tipos de sonda mais adequados para medição de espessura de condutores
são os mesmos usados para medir espessura de revestimento
não condutor em condutores. Sondas
pontuais, absolutas simples ou de reflexão, com ou sem carga de mola,
são normalmente usadas, mas também podem ser usadas
sondas lápis com um suporte de sonda, de preferência
com mola para minimizar o lift-off. Sondas
ou suportes de sonda na forma de um bloco em V ou com uma face
contornada devem ser usados em superfícies curvas.
A
base para a seleção da frequência de ensaio é
a mesma que para a seleção da frequência para a
detecção de falhas subsuperficiais. De
fato, a detecção de corrosão e a
medição de sua profundidade é um problema de
medição de espessura. A
frequência deve ser baixa o suficiente para que a intensidade da
corrente parasita na superfície distante seja relativamente
alta, mas baixa o suficiente para fornecer um grau relativamente alto
de separação de fase entre sinais de diferentes
espessuras. Portanto, a frequência de operação deve ser f90. Normalmente, t nesta fórmula seria igual à espessura máxima a ser medida.
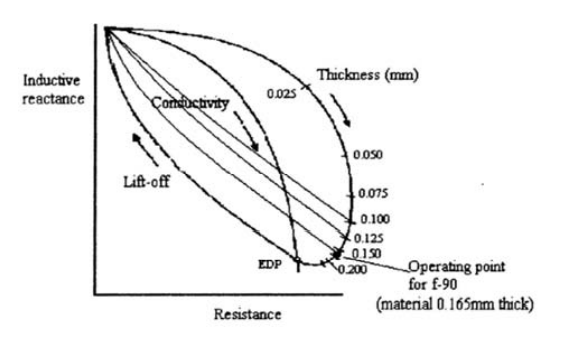
FIG. 5.25. Diagrama
de impedância mostrando a curva de condutividade e a curva de
espessura para latão a uma frequência de 120 kHz, a
frequência f90 para uma espessura de 0,165 mm. O
ponto de operação para esta espessura é mostrado,
e as curvas de levantamento para esta e várias outras espessuras
também são mostradas.
Sinais de variações de espessura
Se
a frequência de ensaio for definida para f90 para o material mais
espesso a ser ensaiado, o ponto de operação está
muito abaixo da curva de espessura e a curva de elevação
a partir deste ponto é de aproximadamente 90o em
relação à curva de espessura, conforme mostrado na
FIG. 5.25. Para este diagrama, o material mais espesso a ser testado é 0,165 mm e a frequência é 120 kHz. O
visor do instrumento de correntes parasitas é normalmente
configurado com o traço de lift-off horizontal à
esquerda. A FIG5.26 mostra parte da tela mostrada na FIG. 5.25,
girado de modo que o traço de elevação do ponto de
operação seja horizontal (para maior clareza, a curva de
condutividade não é mostrada). Pode-se
ver que, se a sonda for aplicada a um material mais fino, por exemplo,
material de 0,125 mm de espessura, o sinal será quase paralelo
ao sinal de lift-off para o material de 0,165 mm de espessura, mas
estará mais acima na tela.
Por
outro lado, se o material 0,165 estiver sendo escaneado e o material
gradualmente se tornar mais fino, o ponto se moverá para cima na
tela ao longo da curva de espessura.
O
material significativamente mais espesso do que aquele para o qual f90
foi calculado não deve ser ensaiado em espessura porque a
sensibilidade às mudanças na espessura reduz rapidamente
abaixo do ponto de operação f90, conforme mostrado na
FIG. 5.25. Esta figura também
mostra que a curva de espessura cruza a curva de condutividade à
medida que a espessura se aproxima da profundidade efetiva de
penetração.
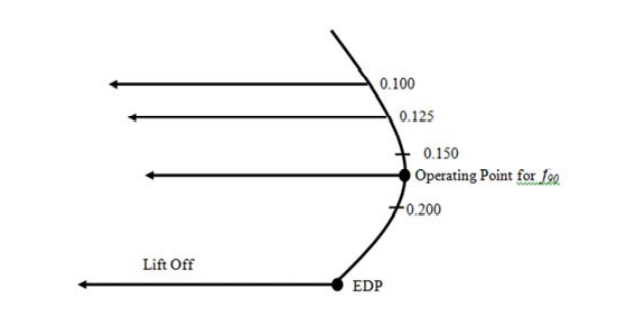
FIG. 5.26. Parte da tela mostrada na FIG. 5.25,
girado de modo que o traço de elevação do ponto de
operação seja horizontal, como apareceria em uma tela
de instrumento de corrente parasita. Os traços de decolagem são mostrados como linhas retas, mas normalmente aparecem ligeiramente curvas.
Amostras de referência
As
amostras de referência devem consistir em calços ou folhas
do material a ser testado (ou de um material da mesma condutividade)
que cobrem a faixa de espessura esperada. Quanto
à medição de espessura de revestimento não
condutor, se a medição for determinar se a espessura da
peça ensaiada está ou não dentro de uma
determinada faixa, deve-se usar uma amostra com a espessura do limite
inferior e outra com a espessura do limite superior. No entanto, um terceiro corpo de prova, com espessura no meio da faixa, é desejável. Se,
no entanto, a espessura real do material deve ser medida, são
necessárias pelo menos três espessuras de amostra. Estas
devem ter espessuras iguais às espessuras máxima e
mínima esperadas, e uma aproximadamente a meio caminho entre
elas.
Measurement procedureMeasurement procedure
- (a) Conecte a sonda a ser usada no instrumento, ligue o aparelho e permita que aqueça por pelo menos 5 minutos.
- (b) Garanta que a área ensaiada esteja limpa e livre de sujeira ou outros contaminantes.
- (c) Selecione a frequência requerida, e ajuste o ganho para o meio de sua escala.
- (d)
Aplique a sonda a amostra de referência, balanceie o instrumento, e
ajuste a fase para que o sinal de lift-off seja horizontal para direita.
- (e)
Com a sonda ainda na amostra, ajuste a posição do ponto para uma
locação na direção ao canto inferior direito da tela (ver FIG. 5.27).
- (f)
Aplique a sonda na amostra de referência de menor espessura e verifique
se o sinal aparece na tela. Não rebalanceie o instrumento. Se visível,
o ponto deve estar acima do sinal obtido previamente. Ajuste o ganho
para localizar o ponto na canto superior direito da tela, como mostrado
na FIG. 5.27.
- (g) Para alguns instrumentos, mudando o ganho
muda também o balanço, então os passos (d), (e) e (f) devem ser
repetidos para garantir que o ponto esteja localizado no canto inferior
direitoda tela com a sonda na amostra de maior espessura, e no canto superior direito com a sonda na amostra mais fina.
- (h) Posicione a sonda nas outras amostras de referência agora e anote o sinal, sem no entranto rebalancear o instrumento.
- (i) Se medições de espessura são requeridas, trace o gráfico
da posição vertical do traço, medidos em milímetros ou números das
divisões da escala a partir do topo ou de baixo da tela ao longo da linha vertical traçada
na tela, versus espessura. Se o gráfico ficar extremamente curvo, mais
amostras de referência podem ser necessárias para que uma curva suave e
precisa seja traçada. Uma vez que um gráfico satisfatório for obtido,
execute mais medidas aplicando a sonda nas peças a serem medidas,
medindo a posição vertical do traço a partir do topo ou de baixo da
tela, e empregue o gráfico para determinar a espessura.
- (j)
Alternativamente, se a medição estiver sendo executada para verificar
se a espessura se encontra entre dois limites de aceitação, marque a
posição do traço para os valores superiores e inferiores, depois
aplique a sonda a peça a ser verificada. A espessura será aceitável se
o traço estiver localizado entre as posiçoes das marcações dos limites
superior e inferior.
- (k) Se um grande número de medições é necessário, a calibração
deve ser verificada a cada 30 minutos, pelo menos. A calibração deve
ser verificada após o término da inspeção.
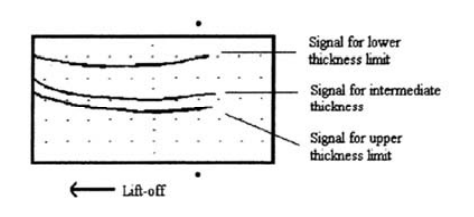
FIGO. 5.27. Tela do instrumento de correntes parasitas após a
configuração para verificar se a espessura das amostras
de teste está entre os limites aceitáveis.
5.1.6 Medição de espessura de revestimentos condutores em substratos condutores
A espessura de um condutor em um substrato condutor, por exemplo,
revestimento metálico em metais, pode ser medida por
técnicas de correntes parasitas desde que a razão da
condutividade dos metais seja maior que 1,5. A
técnica é igualmente aplicável a revestimentos de
baixa condutividade em um substrato de alta condutividade e
revestimentos de alta condutividade em um substrato de baixa
condutividade. Também
pode ser aplicado a revestimentos condutores não
ferromagnéticos em um substrato ferromagnético.
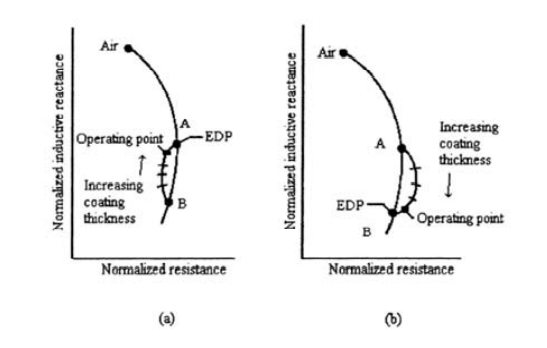
FIG. 5.28. Diagramas de impedância mostrando os "loci" para variações na espessura de um condutor sobre outro.
(a)
mostra a espessura de um metal de baixa condutividade (A) em um metal
de alta condutividade (B)
(b) mostra a espessura de um metal de alta
condutividade (B) em um metal de baixa condutividade (A).
A FIG. 5.28 mostra as curvas de impedância para os dois casos envolvendo materiais não ferromagnéticos. As
curvas de espessura do revestimento atendem à curva de
condutividade quando a espessura do revestimento é igual
à profundidade efetiva de penetração (EDP) das
correntes parasitas no revestimento. Assim
como na medição da espessura de um condutor, a
frequência de teste deve ser f90 calculada sobre a espessura do
revestimento. Isso fornece pontos de operação nos locais marcados nas curvas. Um
outro fator que precisa ser levado em consideração ao
selecionar a frequência do teste é evitar, se
possível, que as correntes parasitas penetrem no substrato, pois
a espessura do substrato afetará a leitura. Frequências superiores a f90 podem ser necessárias para esta finalidade. Para determinar se as correntes parasitas penetram no substrato, o material pode ser colocado sobre um bloco de cobre. Se um sinal não for obtido, as correntes parasitas não penetram.
Os
requisitos para amostras de referência e os procedimentos de
teste são essencialmente os mesmos para medir a espessura dos
condutores.
5.2. Teste de tubo
5.2.1 Teste de tubo usando sondas internas
O
ensaio de corrente parasita do tubo usando sondas internas é uma
das principais aplicações do ensaio de corrente parasita e
é usado para ensaiar tubos em trocadores de calor do tipo casco-tubo, por exemplo,
em condensadores em usinas de geração de energia e
grandes unidades de ar condicionado. O
ensaio é realizado para detectar corrosão e trincas nas
superfícies interna e externa, e a estimativa da profundidade de
quaisquer falhas é um aspecto importante do ensaio para que
ações possam ser tomadas antes que os tubos comecem a
vazar.
Sondas de ensaio de tubo e sua sensibilidade
A sonda interna absoluta padrão para ensaio de tubo, comumente
chamada de sonda bobina (NT: no inglês, "bobbin probe"), consiste em um cilindro curto com uma
bobina enrolada em uma ranhura ao redor de sua circunferência
(ver FIG. 5.29a). As sondas de bobina diferencial possuem duas bobinas enroladas lado a lado (FIG. 5.29b). Os
tubos normalmente ensaiados por este método geralmente têm
um diâmetro externo na faixa de aproximadamente 12 mm a 30 mm,
com espessuras de parede na faixa de aproximadamente 0,7 mm a 3 mm. O
diâmetro da sonda é compatível com o diâmetro
interno do tubo que está sendo ensaiado, com uma folga de
aproximadamente 0,8 mm a 1,5 mm de diâmetro, sendo a folga maior
para tubos de grande diâmetro ou danificados.
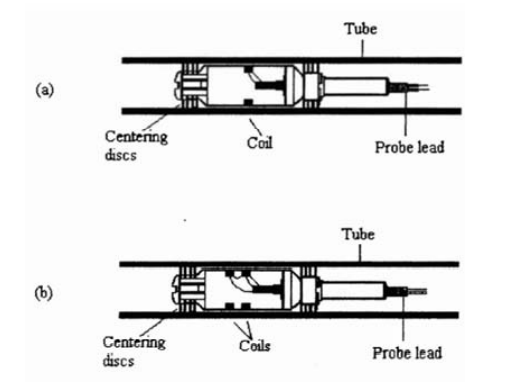
FIG. 5.29. Seções
através de uma sonda de bobina padrão absoluta (a) e uma
sonda de bobina diferencial padrão (b). Discos de centralização nem sempre estão presentes.
A(s)
bobina(s) em sondas circunferenciais produzem campos magnéticos
semelhantes aos produzidos por sondas de ensaio superficial,
mas como a bobina é concêntrica com o material do tubo, as
correntes parasitas fluem circunferencialmente ao redor da parede do
tubo. Como
as falhas só podem ser detectadas se distorcem o fluxo de
correntes parasitas, isso significa que uma laminação ou
outra separação do material paralela à
superfície do tubo não pode ser detectada. Felizmente,
esta não é uma falha comum em tubos, e geralmente
não é muito prejudicial ao serviço do tubo. No
entanto, isso também significa que falhas circunferenciais ou
transversais estreitas não podem ser detectadas, como mostrado
na FIG. 5.30. Tais falhas incluem trincas por fadiga e trincas por corrosão sob tensão. As
trincas de corrosão sob tensão são frequentemente
ramificadas em vez de uma única separação de
material e, nesse caso, podem ser detectadas. Fissuras de fadiga, no entanto, não são ramificadas, portanto, a probabilidade de detecção é muito baixa. Falhas
que progridem ao longo do tubo, como costuras, e falhas que são
relativamente largas, como ranhuras de desgaste e sulcos de
corrosão, podem ser facilmente detectadas se forem de tamanho
significativo.
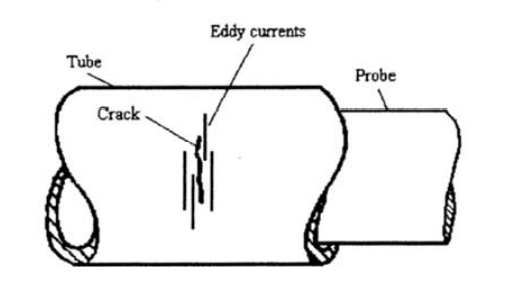
FIG. 5.30. Esboço
de um tubo sendo ensaiado com uma sonda de bobina mostrando que uma
trinca transversal não distorce as correntes parasitas e,
portanto, não é detectada.
Outros
projetos de sondas estão disponíveis e são capazes
de detectar fissuras transversais estreitas, bem como outras falhas. Estes
incluem sondas em ziguezague e sondas diferenciais com as duas bobinas
montadas com seu eixo normal ao eixo do tubo e em ângulo reto
entre si (FIG. 5.31). Um
desses tipos de sonda deve ser usado quando a trinca por fadiga ou
corrosão sob tensão for um problema conhecido ou
suspeito.
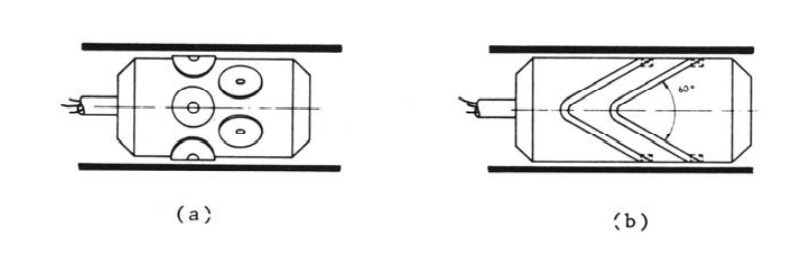
FIG. 5.31. (a) sonda estilo panqueca multi-coil e (b) sonda estilo ziguezague.
Para
obter sensibilidade adequada a falhas na superfície externa do
tubo, a profundidade de penetração das correntes
parasitas deve ser adequada para obter uma intensidade de correntes
parasitas relativamente forte na superfície externa. A
profundidade de penetração pode ser aumentada reduzindo a
frequência de teste, mas, assim como no teste superficial, as dimensões da bobina têm um efeito
importante no tamanho do campo magnético da bobina e,
consequentemente, na profundidade de penetração das
correntes parasitas. Para
o ensaio superficial, o diâmetro da bobina pode ser
aumentado para aumentar a penetração, mas com o ensaio de
tubos, o diâmetro da bobina é controlado pelo
diâmetro interno do tubo, e é a profundidade e
particularmente o comprimento axial dos enrolamentos da bobina que
são aumentados para aumentar a penetração. No entanto, aumentar a profundidade ou o comprimento da bobina reduz a sensibilidade a pequenas descontinuidades. Para
o melhor compromisso entre penetração e sensibilidade, o
comprimento e a espessura da bobina (profundidade dos enrolamentos)
devem ser aproximadamente iguais à espessura da parede do tubo. Observe
que, como as sondas com bobinas largas são projetadas para
penetração, elas também são projetadas para
operar em baixas frequências. As sondas absolutas possuem apenas
uma bobina detectando o material ensaiado. A carga de equilíbrio pode estar dentro da sonda ou em qualquer outro lugar do circuito elétrico. As
sondas diferenciais possuem duas bobinas que detectam partes do
material ensaiado, com as bobinas conectadas em braços adjacentes do
circuito da ponte. Por
causa disso, as sondas diferenciais emitem um sinal somente quando as
duas bobinas detectam condições diferentes. Portanto, condições idênticas e condições gradualmente variáveis, como o afinamento gradual da parede, não pode ser detectado por sondas diferenciais. Falhas longas, como uma costura em um tubo, darão um sinal apenas no início e no fim. Além
disso, como eles fornecem sinais mais complexos (discutidos
posteriormente), a interpretação dos sinais pode ser
muito mais difícil. Apesar dessas desvantagens, eles são mais comumente usados do que as sondas absolutas. Isso
ocorre em grande parte porque o ruído de oscilação
da sonda é muito menor e o desvio de temperatura e o
deslocamento do ponto devido a mudanças na condutividade do tubo
estão quase ausentes. eles são mais comumente usados do que sondas absolutas. Isso
ocorre em grande parte porque o ruído de oscilação
da sonda é muito menor e o desvio de temperatura e o
deslocamento do ponto devido a mudanças na condutividade do tubo
estão quase ausentes. eles são mais comumente usados do que sondas absolutas. Isso
ocorre em grande parte porque o ruído de oscilação
da sonda é muito menor e o desvio de temperatura e o
deslocamento do ponto devido a mudanças na condutividade do tubo
estão quase ausentes.
Assim como para o ensaio superficial, a sensibilidade do ensaio também depende do grau de acoplamento magnético. Ao
testar com bobinas internas, o acoplamento magnético é
medido como o fator de enchimento, dado o símbolo η (a
letra grega 'neta'), e definido como a razão entre a área
média da bobina e a área interna do tubo.
O fator de enchimento também pode ser expresso como a%. Para
máxima sensibilidade, o fator de preenchimento deve ser o mais
alto possível compatível com o fácil movimento da
sonda no tubo. Observe que o fator de preenchimento nunca pode exceder 1 (100%).
Seleção de frequência de ensaio
O
diagrama de impedância para tubos ensaio com sondas internas
tem a mesma forma geral que o diagrama de impedância para teste
superfiaial de materiais. Como
a detecção de falhas nas superfícies interna e
externa é necessária, a frequência do teste
é escolhida de modo que a espessura da parede do tubo seja menor
que a profundidade efetiva de penetração. Ou
seja, o ponto de operação está localizado em uma
curva de espessura e não na curva de condutividade. A
localização onde cada uma das curvas de espessura
encontra a curva de condutividade ocorre quando a espessura da parede
do tubo é igual à profundidade efetiva de
penetração. A
localização deste ponto na curva de condutividade depende
da frequência do ensaio, da condutividade da curva e do
diâmetro do tubo - à medida que qualquer um deles aumenta,
esse ponto se move mais para baixo na curva de condutividade. Observe
que isso é semelhante ao ensaio superficial, exceto que,
para tubos, o diâmetro do tubo é o parâmetro
relevante, não o diâmetro da bobina como para o ensaio superficial. A
razão para isso é que na verdade é o
diâmetro das correntes parasitas que é o parâmetro
significativo. Para
testes superficiais com sondas padrão, as correntes
parasitas mais fortes fluem imediatamente abaixo da bobina, de modo que
o diâmetro das correntes parasitas é essencialmente o
mesmo que o diâmetro da bobina. Para tubos, as correntes parasitas fluem no tubo e, portanto, seu diâmetro é essencialmente o do tubo. as
correntes parasitas mais fortes fluem imediatamente abaixo da bobina,
de modo que o diâmetro das correntes parasitas é
essencialmente o mesmo que o diâmetro da bobina.
A
base para a seleção da frequência de ensaio é
a mesma que para a seleção da frequência para ensaio
superficiais para falhas de subsuperfície ou
medição de espessura. A
frequência deve ser baixa o suficiente para que a intensidade da
corrente parasita na superfície externa seja relativamente alta,
mas baixa o suficiente para fornecer um grau relativamente alto de
separação de fase entre sinais de diferentes espessuras. Portanto,
a frequência de operação normal deve ser a
frequência que fornece uma separação f90 entre os
sinais de uma falha superficial interna e uma falha superficial
externa. No entanto,
devido à diferença de configuração entre o
teste superficial e o ensaio do tubo, essa frequência
é aquela na qual a espessura da parede do tubo é igual a
aproximadamente 1,1 profundidades padrão de
penetração.
f90 =530 / (t2σ)
(5.4)
onde
f90 = frequência de operação (kHz),
t = espessura de parede do tubo (mm) , e
σ = condutividade do material (% IACS)
Um
diagrama de impedância mostrando os sinais de uma falha
superficial interna rasa e uma falha superficial externa rasa é
mostrado na FIG. 5.32. Pode-se
observar que, à medida que a frequência aumenta, a
separação de fases entre o defeito da superfície
interna e o defeito da superfície externa aumenta, mas a
amplitude do defeito da superfície externa diminui em
relação ao defeito da superfície interna.
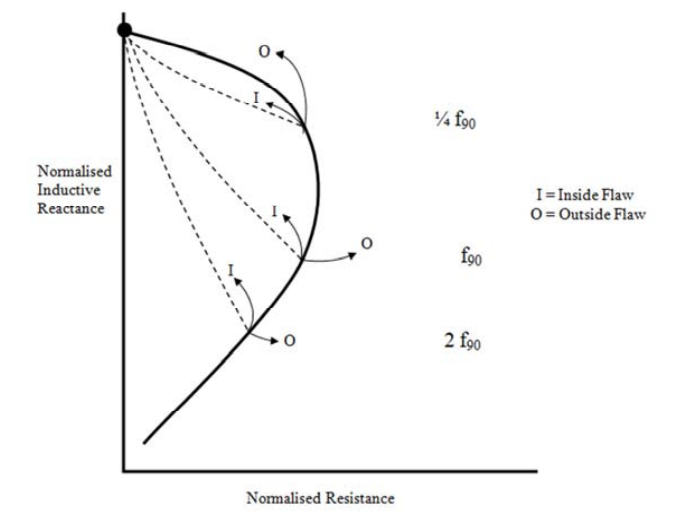
FIG. 5.32. Diagrama
de impedância mostrando os sinais de uma falha superficial
interna rasa e uma falha superficial externa rasa em três
frequências diferentes. Pode-se
observar o aumento da separação de fases e a
diminuição da amplitude do defeito superficial externo em
relação ao defeito superficial interno.
Sinais de falha de sondas absolutas
Em f90, os sinais obtidos usando uma sonda absoluta de um tubo com uma falha
superficial interna rasa, uma falha superficial externa rasa e um furo
passante aparecem como mostrado na FIG. 5.33
quando o mostrador é girado de modo que a orientação
seja semelhante àquela obtida nas mesmas condições
durante o ensaio superficial. Observe que um sinal de fator de enchimento decrescente normalmente não é obtido. Em
vez disso, para ensaio de tubo, o controle de fase é ajustado
para que o sinal de uma falha superficial interna rasa seja
aproximadamente horizontal. Observe que a ilustração dos sinais absolutos da sonda no código ASME é girada 180o e está, portanto, de cabeça para baixo em relação à FIG. 5.33. No
entanto, o Código afirma que os sinais podem ser girados para os
quadrantes superiores conforme a conveniência do operador. Uma
vez que é prática padrão internacionalmente ao
realizar ensaios com sondas superficiais ajustar a fase para fornecer a
orientação do sinal mostrada na FIG. 5.33,
é altamente recomendável que a mesma
orientação seja usada durante o teste do tubo para evitar
possíveis confusões.
Em f90,
todos os sinais de falha aparecem no quadrante entre os sinais para uma
falha superficial interna e aqueles para uma falha superficial externa.
Sinais de
falha que aparecem entre aqueles para uma falha superficial interna
rasa e um furo passante indicam uma falha na superfície interna,
e sinais de falha que aparecem entre aqueles para uma falha superficial
externa rasa e um furo passante indicam uma falha na superfície
externa.
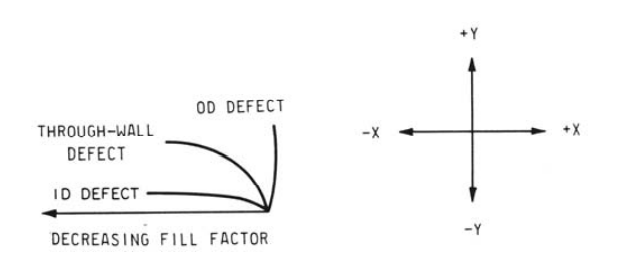
FIG. 5.33. A tela do instrumento usa uma sonda absoluta para falhas superficiais internas e externas e um furo passante em f90. O sinal do fator de enchimento normalmente não é obtido, então é mostrado tracejada.
Sinais de sonda absoluta oriundos de outras condições
Durante
a inspeção de tubos em serviço, são exibidos na tela sinais
de várias condições, além de falhas. Alguns desses sinais podem aparecer em ângulos de fase semelhantes aos das falhas. Portanto, é importante estar familiarizado com esses sinais e como distingui-los dos sinais de falha. Essas condições incluem o seguinte.
(a) Vibração da sonda
A
oscilação da sonda aparece como uma variação no fator de enchimento
e, portanto, fornece um sinal aproximadamente horizontal em ambos os
lados do ponto de operação para todas as frequências de ensaio, conforme
mostrado na FIG. 5.34. Este
sinal é facilmente distinguível dos sinais de falha, mas
pode adicionar ruído a outros sinais e, portanto, é
indesejável. Altas
frequências aumentam a intensidade relativa das correntes parasitas da
superfície interna e, assim, causam maiores sinais de oscilação da
sonda. Os sinais podem, portanto, ser reduzidos diminuindo a frequência de ensaio. Isso
pode não ser aceitável devido à diminuição da sensibilidade às
condições da superfície externa, portanto, se o ruído de oscilação da
sonda for um problema, uma sonda de diâmetro ligeiramente maior deve
ser usada. Alternativamente,
a sonda que está sendo usada pode ser embrulhada com fita
adesiva para reduzir a oscilação.
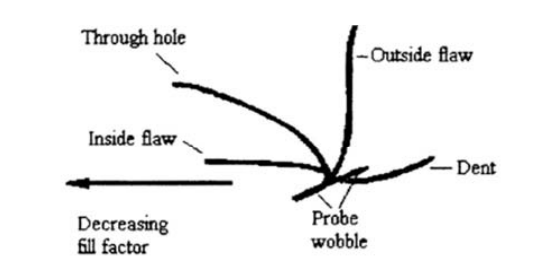
FIG. 5.34. A tela do instrumento usando uma sonda absoluta para várias falhas, oscilação da sonda e um amassado em f90.
(b) Amassamentos
Amassamentos
podem estar presentes em tubos em trocadores de calor devido ao
acúmulo de produtos de corrosão entre o tubo e uma placa defletora ou de suporte do tubo, e por outras causas. As tensões associadas a eles podem levar a trincas por corrosão sob tensão ou trincas por fadiga. Um
amassado causa uma redução nos diâmetros interno e externo sem qualquer
afinamento significativo da parede do tubo e, portanto, aparece como um
aumento no fator de preenchimento em todas as frequências de teste,
conforme mostrado na FIG. 5.34. Este sinal é facilmente distinguível dos sinais de falha.
(c) Condições ferromagnéticas na superfície interna
Uma
inclusão ferromagnética na superfície interna de um tubo não ferroso ou
próximo a ela ou um acúmulo de produto de corrosão de óxido de ferro
dão um sinal semelhante. Em ambos os casos o material ferromagnético
aumenta a quantidade de fluxo que por sua vez aumenta a reatância
indutiva da bobina. O sinal produzido é, portanto, no sentido
ascendente no diagrama de impedância, qualquer que seja a frequência de
ensaio. No entanto, embora a direção no diagrama de impedância varie
pouco com a frequência, a direção relativa à direção do fator de
preenchimento ou a direção dos sinais de falha varia consideravelmente.
Isso pode ser visto na FIG. 5.35. Em f90 (e em frequências mais altas)
o sinal aparece entre os sinais de falha superficial interna
superficial e falha superficial externa rasa e, portanto, pode ser
confundido com um sinal de falha (veja os dois pontos operacionais
inferiores na FIG. 5.34).
Um sinal de uma condição
ferromagnética na superfície interna pode ser distinguido de um sinal
de falha ensaiado novamente em uma frequência mais baixa, por exemplo,
1/4 f90 ou inferior. À medida que a frequência é reduzida, o ângulo
entre a falha superficial da superfície interna e os sinais da falha
superficial superficial externa diminui, como mostrado no ponto de
operação superior na FIG. 5.34. Ou seja, o sinal de falha da superfície
externa gira no sentido anti-horário em direção ao sinal de falha da
superfície interna. No entanto, um sinal de uma condição ferromagnética
na superfície interna irá girar ligeiramente no sentido horário.
(d) Condições ferromagnéticas na superfície externa
Uma
condição ferromagnética na superfície externa dá o mesmo sinal que uma
condição ferromagnética na superfície interna, exceto que, porque as
correntes parasitas que são afetadas por ela têm um atraso de fase em
relação às correntes parasitas da superfície interna, o sinal mostra
uma mudança de fase . Além
disso, as correntes parasitas na superfície externa têm uma intensidade
menor do que as da superfície interna, de modo que a amplitude do sinal
é menor para uma condição ferromagnética na superfície externa. Ou
seja, a diferença é a mesma que a diferença entre
os sinais de falhas nas superfícies externas e internas. Em
uma frequência de teste de f90, os sinais da superfície externa são
girados 90o no sentido horário em relação aos sinais internos. Em
frequências mais baixas, a rotação de fase é menor, mas a amplitude do
sinal é maior, enquanto em frequências mais altas, a rotação de fase é
maior, mas a amplitude do sinal é menor.
A FIG. 5.36 mostra o sinal de uma condição ferromagnética na superfície externa. Pode
ser confundido com um sinal de um amassado, mas os dois podem ser
facilmente distinguidos, se necessário, retestando em uma frequência de ensaio diferente. O
sinal de uma condição ferromagnética na superfície externa mostrará
rotação de fase em relação ao sinal de uma falha de superfície interna,
como indicado acima, enquanto um sinal de dente permanecerá
aproximadamente 1800 do sinal de falha de superfície interna.
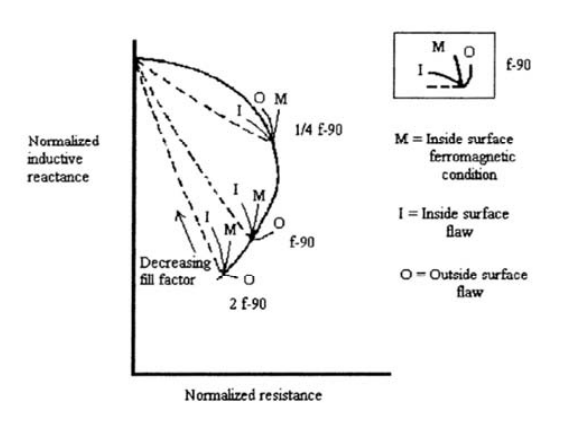
FIG. 5.35. Diagrama
de impedância mostrando sinais de falha e um sinal de uma condição
ferromagnética de superfície interna em três frequências diferentes. A
inserção mostra os sinais em 190 girados para sua
orientação aproximada em uma tela de instrumento de
corrente parasita.
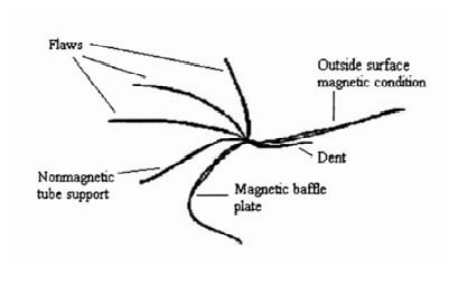
FIG. 5.36. Sinais de uma sonda absoluta típica para detecção de falhas.
Aparecem uma
condição ferromagnética da superfície externa, um amassado, uma placa
defletora ferromagnética e um suporte não ferromagnético ensaiado em f90.
(e) Suporte não ferromagnético ou placas defletoras e depósitos condutores na superfície externa
Um
suporte de tubo não ferromagnético de placa defletora dá o efeito
combinado de um aumento na espessura do tubo e, se o suporte tiver uma
condutividade diferente daquela do tubo, uma mudança de condutividade,
girada no sentido horário devido à mudança de fase. Em f90 o ponto de operação é relativamente baixo na curva de espessura, semelhante ao mostrado na FIG. 5.25 para ensaio de medição de espessura. O
grande aumento de espessura (maior que a profundidade efetiva de
penetração) causado por uma placa de suporte move o ponto para a
localização EDP na curva de condutividade e, portanto, fornece um sinal
no quadrante inferior esquerdo, conforme mostrado na FIG. 5.36. Este sinal será modificado por qualquer diferença de condutividade entre o suporte e o tubo. Uma
mudança de condutividade dará um sinal aproximadamente
paralelo à curva de condutividade, que é aproximadamente
vertical. Uma
diminuição na condutividade moverá o ponto geralmente para cima,
enquanto um aumento na condutividade moverá o ponto geralmente para
baixo. No entanto, a mudança de condutividade ocorre na parte externa do tubo e, portanto, é defasada. Em
f90, esse deslocamento de fase é de 90° no sentido horário, portanto,
se a condutividade do suporte for menor que a do tubo, o ponto se
moverá geralmente para a direita. Considerando que, se a condutividade do suporte for maior que a do tubo, o ponto se moverá geralmente para a esquerda. Consequentemente,
o efeito de uma diferença de condutividade entre o suporte e o tubo é
girar o sinal de aumento de espessura no sentido anti-horário se o
suporte tiver uma condutividade menor e no sentido horário se o suporte
tiver uma condutividade maior. enquanto um aumento na condutividade moverá o ponto geralmente para baixo. No entanto, a mudança de condutividade ocorre na parte externa do tubo e, portanto, é defasada. Em
f90, esse deslocamento de fase é de 90° no sentido horário, portanto,
se a condutividade do suporte for menor que a do tubo, o ponto se
moverá geralmente para a direita. Considerando que, se a condutividade do suporte for maior que a do tubo, o ponto se moverá geralmente para a esquerda. Consequentemente,
o efeito de uma diferença de condutividade entre o suporte e o tubo é
girar o sinal de aumento de espessura no sentido anti-horário se o
suporte tiver uma condutividade menor e no sentido horário se o suporte
tiver uma condutividade maior.
Isso
leva à possibilidade de o sinal de suporte ser girado suficientemente
no sentido horário para aparecer acima da horizontal, em um ângulo
semelhante ao de uma falha de superfície interna. Uma
condição quando isso é possível é a
deposição de cobre na superfície externa de um
tubo. O
cobre pode ser lixiviado das ligas de cobre e redepositado nas
superfícies dos tubos, particularmente adjacentes aos suportes dos
tubos. Mesmo depósitos de cobre muito finos dão um sinal forte devido à alta condutividade do cobre. Se
houver suspeita desta condição, deve ser realizado um
novo teste em uma frequência mais baixa, por exemplo, 1/2 f90. Isso
reduzirá a mudança de fase do sinal para que ele apareça no quadrante
inferior esquerdo, facilmente distinguível das falhas da superfície
interna.
(f) Suporte ferromagnético ou placas defletoras
O sinal do suporte ferromagnético ou das placas defletoras é complexo
porque combina um aumento de espessura, uma mudança de condutividade
com deslocamento de fase e um aumento de permeabilidade com
deslocamento de fase. Os
dois primeiros efeitos dão um sinal semelhante ao de uma placa
defletora não ferromagnética e movem o ponto para baixo e para a
esquerda. De
fato, o sinal de uma placa defletora ferromagnética começa da mesma
maneira, porque há pouca resposta magnética ao campo magnético muito
fraco produzido inicialmente na placa defletora. No
entanto, à medida que a sonda se aproxima da placa defletora, o efeito
magnético aumenta e o ponto se move lateralmente para a direita, como
foi o caso de uma condição ferromagnética na superfície externa. O sinal, portanto, geralmente tem uma curva distinta, com aparência de gancho ou sinal curvo (ver FIG. 5.36).
Os
sinais absolutos da sonda obtidos nas placas defletoras (chicanas)
ferromagnéticas estão abaixo da horizontal e, portanto, não são
facilmente confundidos com sinais de falha. No
entanto, a corrosão é comum nos locais das placas defletoras e, se
ocorrer uma falha nesse local, o sinal será uma combinação das duas
condições e pode ser difícil de interpretar. Os
sinais da placa defletora devem, portanto, ser examinados
cuidadosamente, e qualquer diferença do sinal usual para a instalação
específica precisa ser analisada para determinar se ele incorpora um
sinal de falha. Felizmente,
isso geralmente é possível porque os sinais de correntes
parasitas são geralmente aditivos vetorialmente. Isso
significa, por exemplo, que se uma condição faz com que o ponto se mova
para cima e outra condição simultânea faça com que o ponto se mova para
a esquerda, então o ponto se moverá obliquamente, para cima e para a
esquerda. A FIG. 5.36
mostra a adição vetorial de um sinal de defletor e o sinal de um sulco
de abrasão (causado pela vibração entre o tubo e o defletor). A
análise vetorial de sinais de placa de suporte não ferromagnéticos
geralmente não é possível porque o sinal de placa de suporte predomina
e não mostra a curva característica na forma de gancho, cuja variação
ou distorção é mais facilmente reconhecida.
O
melhor método para obter uma detecção confiável de falhas no local dos
defletores de fluxo é usar o ensaio com multifrequência, descrito mais
adiante neste manual.
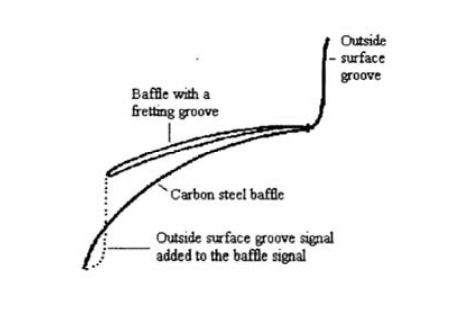
FIG. 5.37. . Os
sinais de um defletor de aço carbono, uma ranhura de superfície externa
e as duas condições ocorrendo simultaneamente mostrando que o sinal
combinado é produzido pela adição vetorial dos sinais de dois
componentes.
Sinais de sondas superficiais
Os sinais produzidos por uma sonda diferencial têm uma aparência característica como mostrado na FIG. 5.38. Isso ocorre porque apenas diferenças nas condições detectadas pelas duas bobinas são detectadas. À
medida que a sonda é puxada ao longo do tubo, a primeira bobina detecta
a condição específica e, assim, é produzido um sinal muito semelhante
ao produzido por uma sonda absoluta. No
entanto, à medida que a sonda é puxada mais adiante, a
segunda bobina começa a detectar a condição. A
diferença entre as duas bobinas é reduzida, e assim a amplitude do
sinal diminui até que, quando a condição é detectada igualmente pelas
duas bobinas, o ponto retorna ao ponto de operação. À
medida que a sonda é puxada mais adiante, a condição é detectada mais
pela segunda bobina do que pela primeira bobina, de modo que a ponte
fica desequilibrada na direção oposta,
Deve-se notar que os sinais absolutos da sonda, que estão próximos a 180o
de diferença, para uma falha superficial na superfície interna e um
depósito magnético na superfície externa, fornecerão sinais de sonda
diferencial muito semelhantes. Eles
podem ser distinguidos apenas observando a direção
inicial do movimento do ponto, que é a mesma
direção do sinal absoluto. Deve-se
notar também que se a sonda de ensaio for empurrada em vez de puxada,
não há mudança nos sinais absolutos, mas os sinais diferenciais são
registrados em sentido inverso. Ou
seja, a direção inicial do movimento do ponto é o oposto de quando a
sonda é puxada e oposta à direção do sinal absoluto da sonda
correspondente. Uma
outra propriedade dos sinais de sonda diferencial é que quando uma
condição persiste por algum comprimento ao longo do tubo, como uma
costura, a
primeira metade do sinal é produzida quando detecta o início da
condição, e a segunda metade do sinal é produzida quando detecta o fim
da condição. No meio, quando ambas as bobinas estão detectando a condição, não há sinal.
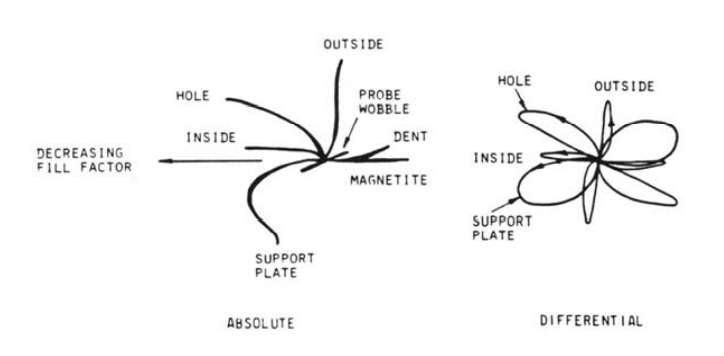
FIG. 5.38. Sinais absolutos e diferenciais.
Os sinais absolutos são mais complexos e podem ser mais difíceis de interpretar. Para
uma correta interpretação, deve-se observar a
direção inicial do movimento do ponto, indicada pelas
setas.
Correlação da profundidade da falha e o ângulo de fase do sinal
Normalmente,
a avaliação da profundidade do defeito é realizada medindo-se o ângulo
de fase do sinal do defeito e comparando-o com os obtidos a partir de
um padrão de referência adequado. Isso
normalmente é feito usando um padrão de referência do tipo indicado na
Seção V Artigo 8 do ASME Boiler and Pressure Vessel Code, para preparar
um gráfico correlacionando a profundidade da falha e o ângulo de fase
do sinal. O
padrão de referência ASME contém furos de fundo plano de 20%, 40%, 60%
e 80% da espessura da parede do tubo da superfície externa e um furo
passante. Se
essas falhas artificiais no padrão de referência representarem as
falhas que estão sendo analisadas, podem ser obtidos resultados
razoavelmente precisos. No
entanto, deve-se perceber que algumas falhas, por exemplo, falhas
circunferenciais estreitas como as de sulcos estreitos de abrasão sob
suportes e as ranhuras no tubo de referência britânico comum, não
mostrarão correlação do ângulo de fase e a profundidade da falha pelo
tubo de referência ASME.
Uma curva típica correlacionando a profundidade da falha e o ângulo de fase é mostrada na FIG. 5.39. Ou
seja, a frequência mais alta fornece maior
separação de fase do que as outras frequências
mostradas. A
análise mostra que a precisão da estimativa da profundidade da falha
correlacionando a profundidade da falha e o ângulo de fase aumenta com
o aumento da frequência. A
frequência ideal para avaliar a profundidade da falha
relacionando-a com o ângulo de fase do sinal foi de
aproximadamente 2f90 , e esta frequência é recomendada para avaliação de defeitos. (A frequência de avaliação ótima, baseada em uma separação de 90o entre o furo passante e uma falha a 50% da espessura da parede na superfície externa, é 2,2f90).
Frequências mais altas que 2.2f90 pode
dar maior precisão, mas o sinal de uma falha superficial na
superfície externa se aproximará da horizontal (180o ) e, portanto, pode ser confundido com uma indicação de amassamento ou sinais de oscilação da sonda. Além disso, frequências mais altas reduzem a força dos sinais de falhas na superfície externa. Deve-se notar que operando em 2f90 gira
os sinais da condução de depósitos não
ferromagnéticos na superfície externa para mais de 360o isto é, para a região ocupada por falhas na superfície interna. Deve-se
ter cuidado, portanto, para identificar corretamente os sinais de tais
depósitos na frequência usada para detecção de sinais (f90) antes de mudar para a frequência de avaliação. A precisão da estimativa da profundidade da falha aumenta com o aumento da profundidade da falha. Isso é vantajoso porque as maiores profundidades de falha são, obviamente, mais críticas.
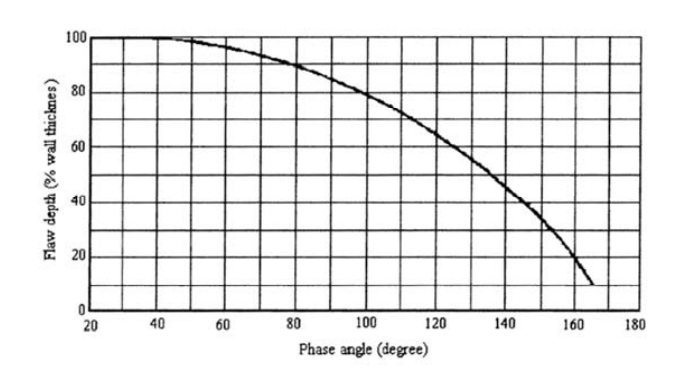
FIG. 5.39. Gráfico
mostrando a correlação entre a amplitude do sinal e a profundidade da
falha para falhas circunferenciais estreitas, como ranhuras produzidas
na abrasão sob suportes.
Correlação entre a profundidade da falha e a amplitude do sinal
Como
mencionado anteriormente, algumas falhas não mostram a correlação do
tipo de ângulo de fase e profundidade da falha mostrada pelo tubo de
referência ASME. Este
pode ser o caso de falhas estreitas, como desgaste por atrito nas
placas de suporte do tubo e barras antivibração. Se
for conhecido que o tipo provável de falha mostra correlação entre a
amplitude do sinal e a profundidade da falha, a amplitude do sinal pode
ser usada para estimar a profundidade da falha. Um
padrão de referência adequado contendo falhas artificiais simulando o
tipo de falha esperado deve ser preparado e um gráfico correlacionando
a amplitude do sinal com a profundidade da falha, como mostrado na FIG. 5.40, deve ser preparado.
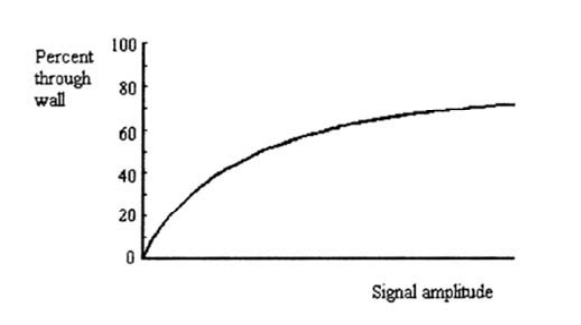
FIG.
5.40. Gráfico mostrando a correlação entre a amplitude do sinal e a
profundidade de descontinuidades circunferenciais estreitas tal como
sulcos ou frestas.
5.2.2 Ensaios de barras e tubos empregando bobinas envolventes
Barras
e tubos são frequentemente ensaiados por correntes parasitas durante a
fabricação para detectar falhas ou variações de condutividade e para
medir seu diâmetro. Ambos são testados usando bobinas envolventes, que podem ser absolutas ou diferenciais. Uma configuração comum é usar bobinas diferenciais com uma referência externa. Uma
barra de referência, conhecida por ter as propriedades exigidas, é
inserida em uma bobina, e as barras a serem ensaiadas são passadas pela
bobina de equilíbrio. Qualquer
diferença entre as duas barras fornece um sinal, que pode ser
analisado conforme necessário para determinar sua causa. O
ensaio de barra de correntes parasitas geralmente é altamente
automatizado, com sinais registrados para análise ou marcação
automática do produto em locais que mostram sinais de condições
inaceitáveis.
O
item seguinte descreve o ensaio de barra usando bobinas envolventes,
mas é uma aplicação especializada, e mais informações devem ser
buscadas pelos responsáveis pela configuração ou modificação de tais
sistemas de ensaio. a
A abordagem para ensaiar barras com bobinas envolventes é semelhante,
mas complicada por diferenças na razão entre o diâmetro interno e o
diâmetro externo e, portanto, não será considerada mais aqui.
A sensibilidade das bobinas envolventes
As
correntes parasitas produzidas numa barra pelas bobinas envolventes
fluem em torno da barra paralelamente aos enrolamentos da bobina, de
forma semelhante às correntes parasitas produzidas no tubo pelas
bobinas internas. Isso
significa que descontinuidades planares paralelas à superfície da barra
e descontinuidades planares transversais não serão detectadas.
A
profundidade de penetração das correntes parasitas abaixo da superfície
da barra aumenta à medida que a frequência, condutividade e
permeabilidade são reduzidas, mas a penetração é ainda mais limitada
devido à configuração, que resulta na densidade de correntes parasitas
caindo para zero no centro da barra. A FIG. 5.41 mostra a densidade de correntes parasitas em várias frequências. Pode-se
ver que a condição limite é uma diminuição linear na densidade de
correntes parasitas de um máximo na superfície para zero no centro da
barra. Isso
significa que, por mais baixa que seja a frequência, as falhas não
podem ser detectadas no centro de uma barra no ensaio de correntes
parasitas, e o ensaio ultrassônico deve ser usado.
Como
em todos os ensaios de correntes parasitas, a sensibilidade do ensaio
também depende do grau de acoplamento magnético. Ao
ensaiar com bobinas envolventes, o acoplamento magnético é medido como
o fator de enchimento (η), como no ensaio de tubo com bobinas de
bobina, e é definido como a razão entre a área da seção transversal da
barra ou tubo e a área média da bobina .
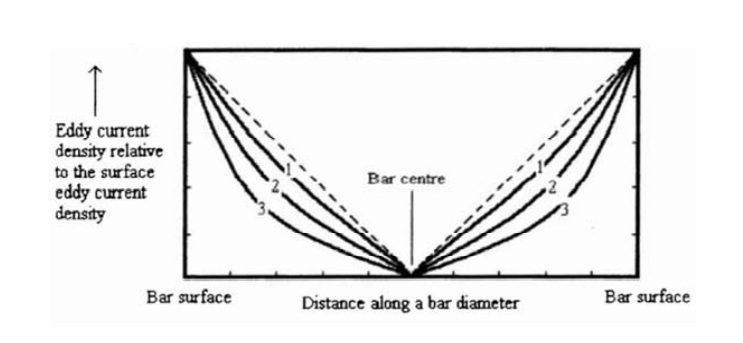
FIG. 5.41. A intensidade da corrente parasita ao longo do diâmetro de uma barra.
As curvas 1, 2, 3 mostram frequências progressivamente crescentes. A
condição limite é uma diminuição linear na densidade de correntes
parasitas de um máximo na superfície para zero no centro da barra,
mostrado pela linha tracejada.
O fator de enchimento também pode ser expresso em % e não pode exceder 1 (100%). Para
máxima sensibilidade, o fator de enchimento deve ser o mais alto
possível compatível com o fácil movimento da barra ou tubo através da
bobina. A
folga necessária para permitir o movimento livre depende do
diâmetro da barra ou tubo, mas geralmente é de 2-3 mm no
diâmetro.
Seleção da frequência
Para
ensaiar barras com bobinas envolventes, a frequência geralmente é
selecionada para fornecer um ponto de operação em um local específico
na curva de impedância. Para ensaios com sondas superficiais, o conceito de Parâmetro Característico (PC) foi desenvolvido para este fim. Forster,
que desenvolveu a teoria do ensaio de barras e tubos usando bobinas
envolventes, usou uma abordagem diferente e propôs o conceito de
frequência limite (fg). A fórmula original de Forster era:
fg = 5066 / ( µr σ d2)
(5.5)
onde
fg = frequência limite (Hz),
µr = permeabilidade relativa,
σ = condutividade (m/Ωmm2
), e
d = diâmetro da barra (cm).
A
frequência limite não é a frequência de ensaio, nem em si tem qualquer
significado prático para ensaios de correntes parasitas. Sua importância está na razão da frequência de ensaio (f) para fg , que permite determinar a posição do ponto de operação na curva de impedância. Esta relação, f/fg,
é, portanto, equivalente ao Parâmetro Característico (PC), e é usada da
mesma forma referindo-se a uma curva de impedância mostrando valores de
f/fg (FIG. 5.42). Deve-se notar, no entanto, que o valor de f/fg em
um determinado ponto da curva de impedância não é igual ao valor do PC
no local correspondente (comparar a FIG. 5.42 com a FIG. 5.20).
O valor de f/f g pode
ser calculado para materiais não ferromagnéticos usando a seguinte
fórmula, que é derivada de Forster, mas com unidades mais práticas.
f/fg= (f d
σ)/873
(5.8)
onde:
f = frequência de operação (kHz),
d = diâmetro da barra (mm), e
σ = condutividade (% IACS).
Associada ao conceito f/fg está a lei da similaridade. Pode-se afirmar que, se duas barras ensaiadas forem testadas na mesma razão f/fg, a distribuição geométrica e a densidade de correntes parasitas são as mesmas. Assim,
por exemplo, se duas barras, que podem diferir em diâmetro,
condutividade e permeabilidade, ambas têm falhas de mesma profundidade
e largura medidas como porcentagem do diâmetro da barra, os sinais de
correntes parasitas serão idênticos. Esta
lei pode ser útil para que a experiência com barras de um material ou
diâmetro possa auxiliar na configuração para ensaiar e interpretar
sinais de barras de um material ou diâmetro diferente. A
lei da similaridade também se aplica ao ensaios com sondas
superficiais, usando o Parâmetro Característico, mas é mais comumente
usado para ensaiar barras e tubos durante a fabricação.
O
ponto de operação ideal depende da aplicação do ensaio, sendo o
princípio geral selecionar uma frequência de ensaio que otimize o sinal
da propriedade de interesse. O teste geralmente não é realizado próximo ao topo da curva de impedância (f/fg
menor que 4), porque o ângulo entre os sinais de variações de diâmetro
e variações de condutividade é bastante pequeno, dificultando sua
separação. Além
disso, o ângulo entre os sinais de falhas em diferentes profundidades é
pequeno, dificultando a determinação da profundidade. Ocasionalmente,
uma baixa frequência e um conseqüente alto ponto de operação podem ser
usados para melhorar a penetração em um material de alta
condutividade como o cobre. As
aplicações comuns incluem medição de
diâmetro, medição de condutividade e
detecção de falhas. Estes aplicados a barras não ferromagnéticas são discutidos nos parágrafos seguintes. O teste de barras ferromagnéticas mostra algumas diferenças e é discutido mais adiante neste manual.
Aplicação de ensaio específica para barras não ferromagnética
- (a) Medição do diâmetro - O efeito principal das
variações no diâmetro é modificar o fator de enchimento, mas um segundo
efeito significativo é a mudança na relação f/fg. Uma diminuição no
diâmetro diminui tanto o fator de enchimento como a razão f/fg, dessa
forma o ponto de trabalho/operação segue um "locus" ligeiramente acima
do locus do fator de enchimento, mostrado como linha tracejada na FIG.
5.41a. Para medição precisa do diâmetro, f/fg deve ser maior que 4, de
forma que o ângulo entre o sinal de variações no diâmetro e
variações na condutividade seja relativamente grande, permitindo que
ambos estejam bem separados. Se apenas a medição do diâmetro da barra é
o propósito da inspeção, uma frequência bem mais alta, dando um ponto
de trabalho bem abaixo na curva de impedância é preferida. Nessas
condições, sinais do diâmetro e da condutividade estarão bem separados,
a penetração é rasa, dando sensibilidade aumentada na superfície da
barra com o fill-factor, também conseguindo reduzir variações na
condutividade do material abaixo da superfície da barra. Adicionalemte,
em pontos de operação na parte baixa da curva de impedância, a
sensibilidade a variações na condutividade é bastante baixa (vdr
FIG. 5.42).
- (b) Condutividade - Se o interesse é medir a
conduitividade ou comparar a condutividade de amostras de barras
desconhecidas com a condutividade de barras conhecidas, o ponto de
opreação deve ser ajustado na vizinhança do "joelho" da curva. (Por
exemplo, para verificar a uniformidade do tratamento térmico de barras
em liga de alumínio, ou classificar grupos de materiais diferentes
misturados). Isso é,
o ponto de operação deve ser similar a aquele requerido para medição da
condutividade empregando sondas superficiais. Isso significa que f/fg
deve estar próximo de 6, mas qualquer valor na faixa de 4 a 20 pode ser
empregado.
- (c) Detecção de falhas - Indicações de falhas superficiais ocrrem
com um pequeno angulo de fase com relação ao do sinal do fator de
enchimento, assim como no ensaio com sonda superficial, a indicação de
de descontinuidades superficiais ocorrem com um pequeno ângulo de fase
relativo ao sinal de lift-off. Então, passos devem ser tomado no ensaio
automatizado para garantir que variações no diâmetro da varra não sejam
consideradas descontinuidades. A maneira mais simples de garantir isso
é monitar a componente do sinal na direção perpendicular a aquela das
variações de diâmetro. Isto é, se variações no sinal do diâmetro da
barra é ajustado na horizontal, a componente vertical de qualquer sinal
é monitorada para detecção de descontinuidades,
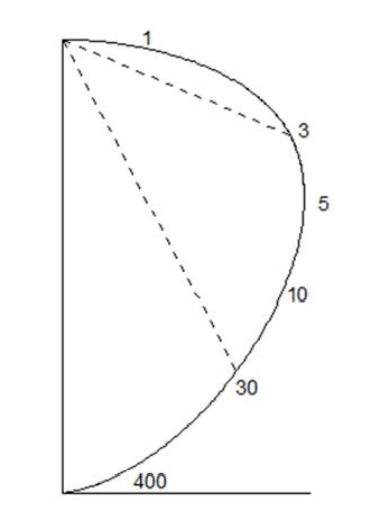
FIG. 5.42. Diagrama de impedância mostrando valores de f/fg. Curvas de fator de enchimento para f/fg = 3 e f/fg =
30(curvas sólidas).
A
experiência mostrou que, usando esta abordagem, a frequência ideal para
a detecção de falhas de quebra de superfície é aquela que fornece uma
relação f/fg na faixa de 10 a 50, os valores mais baixos fornecem maior sensibilidade para falhas mais profundas.
Se
for necessário detectar falhas subsuperficiais, deve-se notar que,
devido à diminuição relativamente rápida na densidade de correntes
parasitas abaixo da superfície da barra, é improvável que falhas
situadas mais profundamente do que aproximadamente 10% do diâmetro da
barra abaixo da superfície sejam detectados, a menos que sejam
relativamente grandes. Frequências
mais baixas e, portanto, pontos de operação mais altos na
curva de impedância maximizarão a penetração. Testes
mostraram que, se o componente dos sinais em uma direção em ângulo reto
com as variações do diâmetro da barra for monitorado, uma relação f/fg
de 5 fornece sensibilidade aproximadamente igual a um determinado
tamanho de falha, independentemente de sua localização de profundidade
(acima até aproximadamente uma profundidade de 10% do diâmetro da
barra). Além disso, relações f/fg na faixa de 5 a 15 fornecem sensibilidade adequada para falhas até esta profundidade,
mas valores maiores da relação f/fg fornecem uma rápida redução da
sensibilidade para descontinuidades mais profundas que essa faixa.
Ensaio de barras em material ferromagnético
As
curvas de impedância para barras ferromagnéticas são idênticas em forma
às barras não ferromagnéticas, mas são aumentadas em magnitude por um
fator igual à permeabilidade da barra. À
medida que a permeabilidade da barra aumenta, a quantidade de fluxo
magnético na barra aumenta e, portanto, a reatância indutiva aumenta
proporcionalmente. Além
disso, o aumento do fluxo causa um aumento na intensidade das correntes
parasitas e, portanto, as perdas resistivas das correntes parasitas e a
resistência efetiva da bobina também aumentam proporcionalmente. Portanto, o ponto de operação se move para baixo na curva (FIG. 5.42). Se
o diâmetro da barra aumenta, a quantidade de material ferromagnético no
qual o campo magnético pode ser induzido também aumenta, então a
quantidade de fluxo magnético na barra aumenta.
Variações
de permeabilidade em materiais ferromagnéticos são bastante comuns por
causa de pequenas variações na composição, tratamento térmico,
quantidade de trabalho a frio e tensão residual, por exemplo, do
endireitamento da barra e, se o material foi magnetizado, por causa de
diferentes graus de magnetização. Isso leva a um sinal ruidoso.
Essas
duas limitações, a incapacidade de medir o diâmetro da barra e os
sinais ruidosos, e uma terceira limitação, a profundidade de penetração
muito restrita devido à alta permeabilidade, podem ser superadas pela
magnetização do material até a saturação ou próximo dela. Nesta
condição, o material tem uma permeabilidade incremental de, ou próximo
a, um e, portanto, mostra o mesmo comportamento para o ensaio de
correntes parasitas que o material não ferromagnético. Neste caso, aplica-se a análise utilizada para barras não ferromagnéticas. Barras
e tubos ferromagnéticos são, portanto, frequentemente testados com duas
bobinas grandes transportando uma grande corrente contínua, uma de cada
lado da(s) bobina(s) de corrente parasita. A
corrente necessária é geralmente grande o suficiente para causar
problemas de aquecimento nas bobinas de magnetização, e a pulsação da
corrente e o uso de camisas refrigeradas a água são frequentemente
empregados para superar esses problemas.
O
material ferromagnético pode ser ensaiado quanto a falhas sem
magnetizá-lo, mas para detectar falhas subsuperficiais, frequências até
100 vezes menores do que as usadas para barras não ferromagnéticas de
mesmo diâmetro precisam ser usadas. Se
apenas as falhas superficiais precisarem ser detectadas, frequências de
ensaio mais altas podem ser usadas e melhorarão a sensibilidade a essas
falhas. Sinais
de falha em barras ferromagnéticas mostram diferença angular suficiente
do locus de permeabilidade/diâmetro da barra para permitir uma
interpretação confiável.
Na
parte inferior do diagrama de impedância as direções de variação da
condutividade e da permeabilidade ou variação do diâmetro da barra são
quase as mesmas. Se
for necessário distinguir entre eles, deve-se escolher um ponto de
operação no alto da curva de impedância, onde o ângulo entre esses dois
sinais seja próximo a 90°.
5.3. Ensaio Multi-frequência
5.3.1 Princípios
No
ensaio com multi-frequência, dois ou mais sinais senoidais de
diferentes frequências são alimentados simultaneamente a uma única
sonda de corrente parasita. O ganho e a fase do sinal de saída de cada frequência podem ser controlados separadamente.
O teste multi-frequência permite que os sinais de variáveis indesejáveis sejam eliminados. Normalmente,
duas frequências são misturadas (comumente chamado mixados) para
suprimir uma variável a fim de monitorar uma segunda variável. A
aplicação mais comum é eliminar sinais indesejados, para que os sinais
de interesse forneçam indicações claras e fáceis de interpretar.
Tendo
obtido sinais da condição a ser eliminada nas frequências de ensaio, a
amplitude e o ângulo de fase do sinal são ajustados e girados para
serem quase iguais nas frequências de ensaio selecionadas. Esses
sinais são então subtraídos vetorialmente pelo instrumento, resultando
em uma saída 'misturada' que é insensível a essa condição. A
frequência primária usada em ensaios multi-frequência é geralmente f90
e, como regra geral, a segunda frequência não deve ser maior que a
metade da frequência primária para variáveis externas e não menos que
duas vezes a frequência primária para variáveis internas a eliminar.
5.3.2 Aparelhos
A
maioria dos sistemas modernos de correntes parasitas pode ser operado
em duas frequências, no entanto, aplicações especializadas, como o
ensaio de tubo, podem usar até dezesseis (16) canais operando em até
quatro (4) frequências. Sondas
especializadas não são necessárias, pois dois ou mais sinais senoidais
de diferentes frequências são alimentados simultaneamente a uma única
sonda.
5.3.3 Aplicativos
É
usado com mais frequência no ensaio de tubos, mas alguns
aplicativos de ensaio com sondas superficiais também existem. Por
exemplo, os aplicativos na inspeção de tubos permitem separar os sinais
das descontinuidades dos sinais perturbadores que são sinais das placas
defletoras, sinais da oscilação da sonda e sinais de fator de
eenchimento. O
mesmo ocorre na inspeção com sonda de superfície de chapas de fuselagem
de aeronaves, nesse caso, os sinais perturbadores incluem os dos
fixadores, distorção/separação das camadas e sinais de geometria. No
teste de tubo, uma terceira frequência às vezes é
usada para eliminar ruídos de oscilação da sonda
ou sinais de amassamentos. Em
geral, frequências de operação mais altas são usadas para a supressão
de variáveis internas, como oscilação ou amassados da sonda,
enquanto frequências baixas e intermediárias são usadas para a
supressão de variáveis externas, como defletores.
|