IAEA - Correntes Parasitas - Capítulo 4 - PROCEDIMENTOS DE
ENSAIO
traduzido do livro: https://www.iaea.org/publications/8414/eddy-current-testing-at-level-2-manual-for-the-syllabi-contained-in-iaea-tecdoc-628rev-2-training-guidelines-for-non-destructive-testing-techniques
- Influência
da Posição do Defeito e de sua
Orientação
- Influência da Temperatura do Material
- Influência da Estrutura e Geometria da Peça
Ensaiada (ruído)
- Influência do Acoplamento
- Influência da Velocidade Relativa Sonda/Peça
- Padrões de Referência Usados no Ensaio de
Correntes Parasitas
- Método de Inspeção
- Preparação da Instrução Técnica para o
Auxiliar Nível 1
- Exercícios do Capítulo 4
4.
PROCEDIMENTOS DE ENSAIO
4.1. Influência da posição e orientação da
descontinuidade
As
correntes parasitas induzidas por um campo magnético variável se
concentram perto da superfície adjacente à bobina de excitação. A
profundidade de penetração diminui com a frequência do teste e é uma
função da condutividade elétrica e da permeabilidade magnética da
amostra. Esse
fenômeno é conhecido como efeito de pele e é análogo à situação na
condução de calor terrestre, onde as flutuações diárias da temperatura
da superfície não são apreciáveis abaixo da superfície da Terra. O
efeito de pele surge da seguinte forma: as correntes parasitas que
fluem no objeto de teste em qualquer profundidade produzem campos
magnéticos que se opõem ao campo primário, reduzindo assim o fluxo
magnético líquido e causando uma diminuição na corrente conforme
aumenta a profundidade. Alternativamente, correntes
parasitas perto da superfície podem ser vistas como uma blindagem do campo
magnético da bobina enfraquecendo assim o campo magnético em maiores
profundidades e reduzindo correntes induzidas.
4.1.1
Caminho das correntes parasitas
As correntes parasitas formam circuitos fechados ("loops") da corrente induzida circulando em planos perpendiculares ao fluxo magnético. Elas normalmente trafegam paralelas ao enrolamento da bobina e paralelos à superfície da peça inspecionada. O fluxo de corrente parasita é limitado à área de presença do campo magnético indutor. A frequência do ensaio determina a profundidade de penetração na amostra; à
medida que a frequência aumenta, a penetração diminui e a distribuição
de correntes parasitas torna-se mais densa perto da superfície do
espécime. A frequência de ensaio também afeta a sensibilidade a mudanças nas propriedades e defeitos do material.a FIG. 4.1
mostra a relação da distribuição das correntes parasitas com a
profundidade de penetração na amostra e o aumento do atraso de fase (defasagem) com a
profundidade. Tanto as correntes parasitas quanto o fluxo magnético ficam mais fracos com a profundidade por causa do 'efeito de pele'. Além
dessa atenuação, as correntes parasitas tem a sua fase relacionada com
a profundidade. A defasagem elétrica das correntes parasitas é um
parâmetro importantíssimo para a aplicabilidade do método de correntes
parasitas.
4.1.2 Profundidade de penetração e atraso de fase (defasagem)
A densidade das correntes parasitas diminui exponencialmente com a profundidade. A
profundidade na qual a densidade de correntes parasitas diminuiu para
1/e (inverso da base do logarítimo Neperiano) ou 36,8% da densidade da superfície é chamada de profundidade
padrão de penetração. A palavra 'padrão' denota excitação de campo eletromagnético de onda plana dentro da amostra ensaiada. A profundidade padrão de penetração é dada por:

ou

onde:
f = frequência (Hz)
σ = condutividade elétrica (IACS%)
μr =
permeabilidade relativa
ρ = resistividade (μΩ-cm)
A
equação da profundidade da pele é estritamente verdadeira apenas para
materiais infinitamente espessos e campos magnéticos planares. Usando a profundidade padrão δ , calculada a partir da equação acima, torna-se um parâmetro de material ensaiado em vez de uma medida real de penetração.
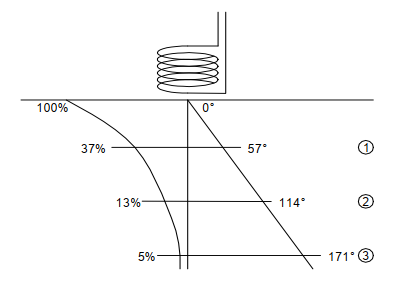
FIG. 4.1. Distribuição de correntes parasitas com profundidade em uma placa espessa e atraso de fase resultante.
A sensibilidade a defeitos depende da densidade de correntes parasitas no local do defeito. Embora as correntes parasitas penetrem mais fundo do que uma profundidade padrão de penetração, elas diminuem rapidamente com a profundidade. Em duas profundidades padrão de penetração (2 δ ), a densidade de correntes parasitas diminuiu para 1/e2 ou 13,5% da densidade da superfície. Em três profundidades (3 δ), a
densidade de correntes parasitas é reduzida a apenas 5% (1/e3) da densidade da
superfície. No entanto, deve-se manter em mente estes valores só se
aplicam a amostra espessa (espessura, t > 5δ ) e campos de excitação magnética planares. As condições planas do campo exigem grandes sondas (diâmetro > 10 t) em teste de placa ou bobinas longas (comprimento > 5t)
em ensaios de tubo. Bobinas de teste reais raramente atenderão a esses
requisitos, uma vez que fariam possuem baixa sensibilidade a defeitos.
Para amostras de chapas finas ou tubos finos, a densidade de corrente cai menos do
que a calculada a partir da Eq. (4.1).
Para cilindros sólidos, o fator de redução é uma diminuição
para zero no centro resultante de efeitos de geometria.
Deve-se
notar também que o fluxo magnético é atenuado através do amostra, mas
não completamente. Embora as correntes sejam restritas a fluxo dentro
dos limites da amostra, o campo magnético se estende até o espaço aéreo
ao redor da amostra. Isso permite a inspeção de componentes
constituidos de várias camadas de chapas separados por um espaço de ar.
A
sensibilidade a descontinuidades internas depende da densidade de corrente
parasita nessa profundidade, é portanto, é importante conhecer a
profundidade efetiva da penetração. O a profundidade efetiva de
penetração é arbitrariamente definida como a profundidade em cuja
densidade de correntes parasitas diminui para 5% da densidade da
superfície. Com o emprego de sondas grandes e amostras espessas, esta
profundidade é de cerca de três padrão profundidades de penetração.
Infelizmente, para a maioria dos componentes e práticos tamanhos de
sonda, esta profundidade será inferior a 3δ, as correntes parasitas sendo atenuadas mais do que o previsto pela equação da profundidade da pele.

onde:
β = defasagem
x = distância dentro do material, a partir da superfície
δ = profundidade padrão de penetração
4.1.3 Zona de ação da sonda
As
correntes parasitas formam circuitos fechados de corrente elétrica
induzida circulando em um
plano perpendicular à direção do fluxo magnético. Sua direção normal de
passagem é paralela ao enrolamento da bobina e paralelo à superfície.
Veja a FIG. 4.2a e a FIG. 4.2b As sondas de superfície do tipo panqueca
(do inglês "pancake", finas e com gande diâmetro, semelhantes a discos)
são portanto, insensível a porventura existência de uma falta de
aderência de revestimento metálico e falhas
paralelas a superfície da amostra ensaiada.
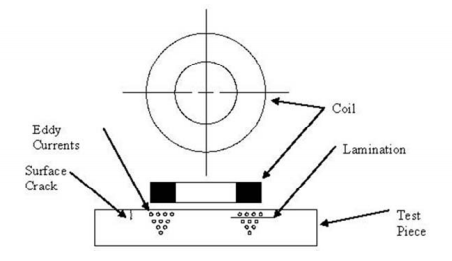
FIG. 4.2a Propriedades direcionais de uma sonda superfícial.
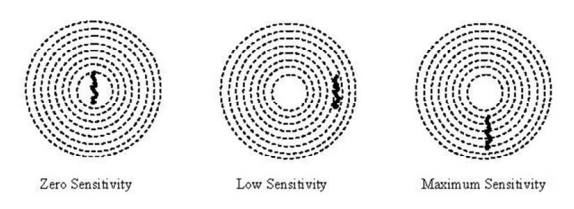
FIG. 4.2.b Propriedades direcionais de uma sonda superfícial para um determinado tamanho de trinca.
Ao
ensaiar descontinuidades do tipo fissuras, é essencial que o fluxo de
corrente esteja formando um grande ângulo (de preferência
perpendicular) a trinca para obter a máxima resposta. Se o fluxo de
corrente parasita
for paralelo ao defeito haverá pouca ou nenhuma interrupção da corrente
e, portanto, sem mudança de impedância da bobina.
Ao
ensaiar peças com descontinuidades paralelas à superfície, como laminações, uma sonda em
forma de ferradura ("yoke probe or "large gap probe")
pode ter sensibilidade razoável.
4.2. Influência da temperatura do material
Temperatura
é uma variável de teste importante, particularmente quando correntes
parasitas são usadas para estabelecer a faixa de condutividade básica para
uma liga metálica. Consideração deve ser dada a:
(1) a temperatura do material de
ensaio,
(2) a diferença de temperatura entre a amostra de ensaio e a
referência e,
(3) tipo de instrumento de corrente parasita que está
sendo utilizado.
4.2.1 Aquecimento
Um aumento da temperatura aumenta a atividade térmica dos átomos no reticulado cristalino de um metal . A atividade térmica faz com que os átomos vibrem em torno
de suas posições normais de equilíbrio. A vibração térmica dos átomos
aumenta a resistência ao fluxo de elétrons, diminuindo assim a
condutividade do metal. Abaixar a temperatura reduz a oscilação térmica
dos átomos, resultando em aumento da condutividade elétrica.
A influência da temperatura sobre a resistividade de um metal pode ser determinada a partir do seguinte equação.

onde:
Rt = resistividade elétrica do metal a temperatura de ensaio
Ro = resistividade elétrica do metal na temperatura padrão
α = coeficiente da rinfluêcia da temperatura na esistividade
T = diferença entre a temperatura padrão e a temperatura de ensaio (oC)
Da
Eq. (4.3) pode-se ver que se a temperatura for aumentada, a
resistividade aumenta e a condutividade diminui a partir de seus níveis
de temperatura ambiente. Por outro lado, se a temperatura é diminuída a
resistividade diminui e a condutividade aumenta.
Para
converter valores de resistividade, como os obtidos da Eq. (4.3) em
condutividade em termos de % IACS (normalmente empregada na área de
correntes parasitas), a fórmula é,

onde:
%IACS = condutividade em International Anneales Copper Standard
ρ =
resistividade elétrica (μΩ-cm)
4.2.2
Desvios
A condutividade de padrões geralmente é determinados a uma temperatura específica; 20°C
é mais comumente usado. Os valores típicos de condutividade são faixas
de condutividade permitidas também estabelecido a aproximadamente esta
temperatura. Se todos os instrumentos calibração e medição de
condutividade podessem ser realizadas neste temperatura, erros na
medição da condutividade relacionados à variação da temperatura não
ocorreria e/ou a compensação da temperatura não seria necessário. Em
aplicações de campo, a faixa de temperaturas concebiveis pode estar na faixa de -20 a 50 ° C.
A menos que precauções sejam tomadas na seleção de padrões de calibração
do instrumento de ensaio, erros podem ser obtidos nos valores de
condutividade medidos. Duas formas pelas quais leituras errôneas
ocorrem são :
(1) diferença na temperata entre padrões e peça de ensaio;
e/ou
(2) diferença de temperatura a que a condutividade do padrão foi
originalmente estabelecida, e a temperatura em que o ajuste da
condutividade do instrumento para as medições forem realizadas.
Para
evitar erros de diferenças de temperatura entre o padrão e a
peça de ensaio, o instrumento e os padrões devem ser permitidos
equilibrar à temperatura juntamente com a peça de ensaio antes da
calibração e da
condutividade as medições serem realizadas. Em nenhum caso devem ser
feitas medições se as temperaturas da peça dos padrões diferirem mais de 5 °C.
Embora os padrões e a peça de teste estejam na mesma temperatura, erro em
a determinação do valor da condutividade ocorre quando a temperatura de
medição difere da temperatura a que a condutividade das normas foi
originalmente estabelecida. A magnitude do erro torna-se maior à medida
que essa diferença de temperatura aumenta.
Dois
outros fatores também contribuem para erros causados pela diferença nas temperaturas:
(1) aumento da diferença de condutividade entre os
padrões de referência superiores e inferiores; e
(2) diferenças na
temperatura da resistividade elétrica obtida em tabelas de referência
e a da peça ensaiada.
Essas duas fontes de erro podem ser reduzidas
diminuindo o intervalo entre as condutividades dos padrões utilizados e
a utilização de ´padrões de referência com resisitividade elétrica
obtida nas mesmas ou aproximadamente a mesma de
temperatura da amostra de ensaio. Porque
todas as ligas de alumínio têm aproximadamente a mesma taxa de variação
da resistividade elétrica com mudança de temperatura, os padrões de
condutividade de alumínio são preferidos para ligas de alumínio.
As medições de condutividade não devem ser realizadas em condições onde a umidade relativa do ar excede 85%.
4.2.3. Compensação
A
condutividade da peça à corrente parasita deve ser corrigida usando Equações
(4.3) e (4.4). Em ligas de alumínio, por exemplo, uma mudança de
aproximadamente 12% IACS pode ser obtida para uma mudança de temperatura de 55°C, usando resistividade elétrica de 2,828 microohm.cm e um coeficiente de temperatura de 0,0039 a 20°C. Se a condutividade de alumínio comercialmente puro é 62% IACS a 20°C, então seria de se esperar uma condutividade de 55% IACS a 48°C e uma condutividade de 69% de IACS a –10 °C.
4.3. Influência da estrutura e geometria das peças testadas (ruído)
Os
resultados mais precisos serão obtidos usando um relação sinal-ruído
alta no ensaio. Uma alta relação sinal-ruído permitirá a fácil
identificação de um descontinuidade relevante com baixo ruído de fundo
eletrônico.
O
ruído de fundo pode ser produzido por variáveis indesejadas no ensaio.
Fontes prováveis de ruído incluem, mudanças microestruturais ao longo
da varredura, rugosidade da
superfície, variações na distância sonda-peça durante a varredura,
mudanças pontuais de permeabilidade e condutividade na amostra.
Mudanças
abruptas na curvatura da superfície resultam em mudanças na corrente
parasita sinais à medida que as sondas as varrem. Isso causa
mudanças no acoplamento e a produção de um grande sinal de lift-off (falta de acoplamento) e a
curvatura também muda a distribuição de fluxo de corrente
parasita criando
uma mudança de resistência efetiva, produzindo uma sinal com ângulo de
fase semelhante ao do lift-off. O aparecimento deste o tipo de sinal
não mudará significativamente quando reescaneado com frequências de
ensaio maiores ou menores.
Tais
sinais podem ser difíceis de analisar porque dependem de como bem, a
sonda segue curvaturas de superfície complicadas. Basicamente o a
direção da mudança de impedância obedece às seguintes regras ao usar
sondas de superfície:
- a)
Raio decrescente de curvatura em uma superfície externa, por exemplo,
ressalto, produzirá mudança na direcção do aumento da resistividade,
- b)
Raio decrescente de curvatura em uma superfície interna, por exemplo,
sulco, produzirá uma mudança na direção da diminuição da resistividade.
O
parâmetro mais problemático no ensaio de correntes parasitas é a falta
de acoplamento ("lift-off", espaçamento sonda para espécime). Uma
pequena mudança no acoplamento cria uma grande sinal de saída.
Uma condição particular de perturbação, como o sinal oriundo da "oscilação"
da sonda, pode ser suprimido fazendo com que a amplitude do sinal
resposta com o uso de uma primeira frequência igual e sua fase
diferente (defasada) de 180 ° da
resposta desse mesmo sinal perturbador numa segunda frequência e, em
seguida, adicionando
os dois sinais junto (NT: Processo conhecido em correntes parasitas
como mixagem de sinais). A soma resultante implicará no cancelamento
das
respostas e, portanto, um sinal zero para essa condição particular.
(NT: Esse processo só é possível porque a defasagem entre o sinal de
interesse e o sinal ruído é diferente nas duas frequências de ensaio
empregadas)
4.3.1 Escolha do ensaio frequência
A frequência de ensaio é muitas vezes a única variável sobre a qual o inspetor tem controle apreciável.
As
propriedades e a geometria do material são normalmente fixas e a
escolha da sonda é muitas vezes ditada pela geometria do material
ensaiado e da disponibilidade da sonda. Escolha de uma frequência de
ensaio
adequada depende do tipo de inspeção. Ensaios para variações de
diâmetro
normalmente requer resposta máxima ao fator de enchimento que ocorre
em altas frequências. Ensaios para detecção de defeitos requerem
penetração em possíveis
locais com defeitos; defeitos na superfície podem ser detectados em
frequências mais elevadas do que os defeitos subsuperficiais. Máxima a
penetração requer uma baixa frequência que ainda permite a clara
discriminação entre sinais de variações inofensivas a propriedades do material
e defeitos graves. Os fatores acima mostram que a escolha da frequência
de ensaio é geralmente um compromisso entre vários fatores.
4.3.2 Desccriminação de fase
Na
maioria dos casos, nenhum conhecimento detalhado dos tipos, formas,
profundidades de descontinuidade e As orientações existem antes do
início dos exames de corrente parasita. Consequentemente, a maior parte
da análise dos dados depende da fase análise de ângulo para determinar
parâmetros de descontinuidade.
É
importante, no entanto, detectar e identificar a descontinuidade.
sinais e separá-los de sinais de fundo não relevantes antes que
qualquer análise de profundidade de rachadura possa ser realizada. O
ângulo de fase a técnica de discriminação é ideal para essa separação.
A
técnica de discriminação do ângulo de fase depende da escolha adequada
de frequências de teste para fornecer uma separação ótima do ângulo de
fase entre diferentes variáveis. Para um determinado material de
ensaio, ângulo de fase as orientações entre as variáveis mudam devido à
mudança da freqüência de ensaio empregada. Esta capacidade de obter informações
diferentes em diferentes frequências é uma importante característica do ensaio de correntes parasitas e deve ser utilizada.
A
prática mais comum envolvendo a discriminação do ângulo de fase é girar
os sinais relativos ao acoplamento eletromagnético sonda peça (lift-off
e fator de enchimento) para que estejam na horizontal e monitorar as
demais variáveis que apresentem sinais mais verticais. Com base neste
conceito de manter o o sinal de acoplamento como horizontal, um a
comparação detalhada das
separações de ângulo de fase dos sinais das demais variáveis pode ser
determinada.
Deve-se
enfatizar que a frequência selecionada pode não necessariamente ser a
frequência ideal para estimar profundidades da descontinuidade. O
conceito de detecção em primeiro lugar, seguido pela análise de
descontinuidade, é o método de avaliação normalmente empregado.
4.3.3 Filtragem
Para
acentuar as respostas na frequências desejadas e eliminar os sinais das
frequências indesejadas, a filtragem eletrônica é empregada. Três tipos de filtros
pode ser usado; o passa-alto, o passa-baixo e o de largura de banda.
A filtragem passa-alto utiliza circuitos resistivos-capacitivos,
que remove os componentes de baixa frequência do sinal de corrente
parasita da ponte elétrica do aparelho. Este tipo de filtragem pode eliminar o efeito de
variações graduais na condutividade ou nas dimensões da peça na resposta da inspeção por
correntes parasitas. A filtragem passa-baixo emprega
circuitos de média de sinal para remover a resposta rápida (alta
frequência) do ruído eletrônico e das frequências harmônicas
relacionadas a variações na permeabilidade magnética. Os filtros
passa-banda usam combinações de ambos os tipos de circuitos para
promover a resposta em uma faixa específica de frequências e suprimir
frequências acima e abaixo deste intervalo. Os efeitos ou cada tipo de
filtro sobre a aparência gravada de sinais de corrente parasita é
ilustrado na FIG. 4.3.
Escolha de frequências
Para
um tipo de descontinuidade conhecido, por exemplo: trincas finas,
filtros apropriados podem ser calculados selecionando filtros de ambos os
lados da Resposta Frequência (Fr) calculada com a fórmula 4.7.
Para
componentes com várias descontinuidades, por exemplo: inspeção de
tubos, a seleção de frequências de filtro pode ser otimizada usando um
amostra de referência adequada.
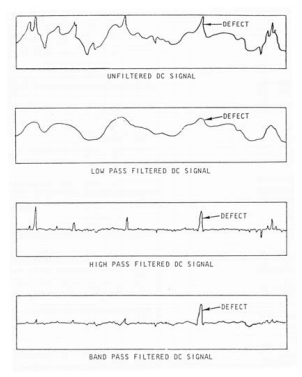
FIG. 4.3. Efeitos de Filtragem.
4.3.4
Saturação magnética
A
inspeção por correntes parasitas de materiais magnéticos em busca de
defeitos é difícil ou impossível devido à variação aleatória da
permeabilidade. Além disso existem limitações da profundidade de penetração.
Sem saturação, a permeabilidade relativainicial dos produtos siderúrgicos
pode variar de 50 a mais de 500. Desde a profundidade de penetração é
inversamente proporcional à raiz quadrada de permeabilidade e
frequência de teste, para obter igual penetração, requer uma redução da
frequência pelo mesmo fator de 50 a mais de 500. Infelizmente, a
redução da frequência moverá o ponto de operação para onde há má
separação de sinal entre lift-off, permeabilidade e resistividade, bem
como sensibilidade reduzida a defeitos. Portanto a saturação magnética
é necessária para suprimir efeitos de geralmente inofensivas variações
de permeabilidade, que podem ser confundidas ou obscurecer os sinais dos defeitos.
4.4. Influência no Acoplamento Eletromagnético
4.4.1 Vibrações
As
vibrações que ocorrem durante o movimento da sonda podem produzir
sinais indesejáveis, de agora por diante chamadas 'oscilação da sonda'
(no inglês, "probe wobble").
A
técnica de multifreqüência pode suprimir este efeito, fazendo a
amplitude de sua resposta na primeira frequência igual e sua fase 180
graus de defasagem da resposta na segunda frequência e em seguida,
adicionando os dois sinais juntos. A soma resultante resultará em
cancelamento das respostas e, portanto, um sinal zero para essa condição
particular.
4.4.2 Lift off
Quando
uma bobina superficial é energizada e mantida no ar acima de um
material condutor, o impedância da bobina tem um certo valor. À medida que a
bobina é movida para mais perto do condutor o valor inicial será
alterado quando o campo do bobina começa a interceptar o condutor.
Porque o campo da bobina é mais forte perto da bobina, o valor de
impedância continuará a mudar até a bobina tocar diretamente no condutor.
Por outro lado, uma vez que a bobina está em contato com o condutor qualquer pequena
variação na separação de bobina e condutor irão alterar a impedância da
bobina. O efeito de acoplamento eletromagnético (lift-off) é tão pronunciado que pequenas variações no
espaçamento podem mascarar muitos indicações.
O
efeito de acoplamento eletromagnético (lift-off) é usado regularmente
para medir a espessura de revestimentos em materiais condutores.
O
ângulo de orientação (inclinação) da sonda também terá um impacto
significativo da eficiência do acoplamento. O uso de guias/suportes mecânicos e sondas impulsionadas contra a superfície por mola podem ajudar a reduzir o lift-off.
4.4.3 Centralização, fator de enchimento
Numa bobina envolvente ou numa
bobina interna, o fator de enchimento é uma medida do acoplamento eletromagnético ou quão
bem o condutor (amostra ensaiada) se encaixa na bobina. É necessário
para manter uma relação constante entre o diâmetro da bobina/sonda e o
diâmetro do condutor. Mais uma vez, pequenas mudanças no diâmetro do
condutor pode causar alterações na impedância da bobina. Este pode ser
útil na detecção de alterações no diâmetro do condutor, mas também pode
mascarar outras indicações.
Para uma bobina externa:

Para uma bobina interna:

onde: η = fator de enchimento (%)
D1 = diâmetro da peça
D2 = diâmetro da sonda
Assim, o fator de enchimento deve ser menor que 1 uma vez que se η =
1 a bobina é exatamente do mesmo tamanho que o material. No entanto,
quanto mais próximo o fator de enchimento estiver de 1, mais preciso
será o ensaio. (NT: na prática deve haver uma folga que permita o deslocamento da sonda na barra ou tubo)
O fator de enchimento também pode ser expresso como %. Para o máximo
sensibilidade, o fator de enchimento deve ser o mais alto possível
compatível com fácil movimento da sonda no tubo. Observe que o fator de
preenchimento nunca pode exceder 1 (100%).
4.4.4 Sensibilidade
A
distribuição das correntes parasitas em uma barra redonda usando uma
bobina envolvente é tal que o campo é máximo na superfície e é zero no
centro da barra.
A
distribuição de correntes parasitas em uma placa plana usando uma
superfície a sonda é tal que o campo é máximo na superfície diretamente
abaixo dos enrolamentos da bobina e é mínimo no centro da bobina.
4.4.5 Compensação
Para otimizar o acoplamento da sonda, inúmeras técnicas podem ser empregadas, incluindo;
- (a) A utilização de guias/suportes mecânicos e de sondas com molas pode contribuir para reduzir o efeito de lift-off.
- (b) Diâmetro da sonda apropriado para maximizar o fator de enchimento.
4.5. Influência da velocidade relativa da peça/sonda
4.5.1 Frequência do instrumento de acordo com a velocidade
Os instrumentos de corrente parasita e a instrumentação de gravação de sinais têm uma resposta de frequência limitada.
Isso
significa que eles exigem tempo finito para responder a um sinal de
entrada. A resposta de frequência, às vezes chamada de velocidade de
resposta, é definida como a frequência com que o sinal de saída cai
para 0,707 (-3 dB) do sinal de entrada máximo.This means they require finite time to respond to an input signal.
Frequency response, sometimes called speed of response, is defined as
the frequency at which the output signal falls to 0.707 (-3 dB) of the
maximum input signal.
Uma bobina de teste com uma largura de detecção efetiva W, passando sobre um defeito localizado de largura w a uma velocidade s, detectará o defeito de ponto por uma duração de w / s segundos. Este sinal é aproximadamente igual a um comprimento de onda com uma frequência.
A Frequência de Resposta (Fr) é o valor inverso do tempo necessário para a sonda atravessar a falha e pode ser mostrado pela fórmula:

onde:
S = velocidade de movimento da sonda (mm/s)
W = largura da sonda (mm)
w = abertura da trinca (mm)
NOTA: Em aplicações práticas a abertura da trinca pode ser considerada zero.
Por exemplo, a uma velocidade de sonda de 0,5 m/s e largura de detecção de sonda de 2 mm, Fr =
250 hertz. Se a instrumentação tiver uma resposta de frequência de 250
hertz, o sinal de saída é reduzido para 0,707 o sinal de entrada e o O
sinal X-Y está distorcido. Se a resposta de frequência de
instrumentação for 500 hertz, o sinal de saída diminui apenas
ligeiramente. Para este exemplo, o instrumento de corrente parasita
deve ter uma resposta de frequência igual a ou superior a 500 hertz
para obter sinais não distorcidos. Ou inversamente, se a resposta de
frequência do instrumento for de apenas 350 hertz, o máximo a
velocidade de inspecção deve ser reduzida para 0,25 m/s. 4.5.2
4.5.2 Resposta de frequência do aparelho de acordo com a velocidade de ensaio
Alguns
os padrões especificam a velocidade máxima de digitalização permitida.
Por exemplo de acordo com o artigo I-40.o do apêndice 8 do artigo 1.o
da ASME, o máximo a velocidade de varredura da sonda de corrente
parasita pode ser de 0,356 m/s para 100 Hz sistema de resposta de
frequência. Se um sistema de corrente parasita com uma frequência
resposta de 450 Hz é usada, permite e velocidade de varredura de 1,6
m/s.
4.6. Padrões de referência usados em testes de correntes parasitas
Análise
de sinais de correntes parasitas é, em sua maior parte, uma técnica
comparativa. Os padrões de referência são necessários para comparar a
amplitude do sinal e a fase (forma) de defeitos desconhecidos com
defeitos de referência conhecidos. Os sinais de referência também são
usados para padronizar as configurações do instrumento, ou seja,
sensibilidade e o ângulo de fase.
4.6.1 Função das amostras de referência
As
especificações e normas nacionais existentes apenas fornecem amplas
diretrizes na escolha dos parâmetros de ensaio. Eles não podem ser
usados para estabelecer procedimentos de ensaio de correntes parasitas
confiáveis para a maioria das inspeções. O efeito do seguinte pode ser
estabelecido:
- a) Resistividade eléctrica variável
- b) Espessura variável
- c) Geometria da superfície (curvatura)
- d) Comprimento do defeito para profundidade constante
- e) Profundidade do defeito para comprimento constante
- f) Aumento da descontinuidade sub superficial com profundidade da descontinuidade constante
- (g) Aumento da distância da descontinuidade sub superficial a partir da superfície com tamanho do defeito constante
- (h) Variação da espessura da camada não condutora (lift-off)
- (i) Variação da espessura da camada condutora
- (j) Inclusão ferromagnética
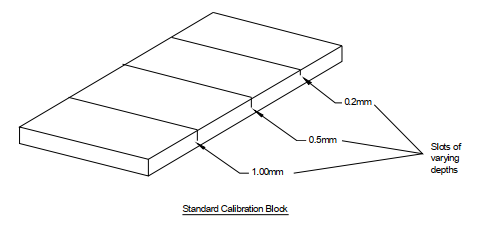
FIG. 4.4. High frequency reference block.
Bloco de referência de alta frequência.
Mais
de uma placa de referência seria necessário abranger uma gama completa
de materiais. A FIG. 4.5a ilustra os sinais de correntes parasitas
obtidos com uma sonda superfícial absoluta de alguns dos defeitos da
amostra de referência. A FIG. 4.5b ilustra sinais os mesmos defeitos
usando sonda superfícial diferencial.
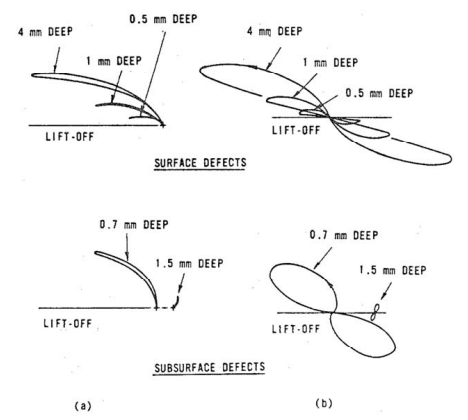
FIG. 4.5. Sinais de correntes parasitas com (a) sondas superficiais absolutas e (b) sondas superficiais diferenciais.
4.6.2 Escolha da amostra de referência
A amostra de referência deve ser uma amostra da parte
a ser inspecionada e deve ter o seu processo de fabricação e transformação semelhante ao do produto a ser examinado.
Deve ser das mesmas dimensões nominais e das mesmas composição nominal
como produto a examinar.
A
amostra de referência deve ser suficientemente longa para simular o
manuseamento do produto a ser examinado através do aparelho de
inspecção. A separação entre descontinuidades de referência colocadas
na mesma amostra não deve ser inferior ao comprimento
da unidade de detecção do aparelho de inspeção.
4.6.3 Fabricação e reprodutibilidade de vários tipos de amostra de referência
A maioria dos padrões de referência
consistem de furos usinados de vários diâmetros e/ou profundidades a
partir da superfície externa. Algumas amostras de referência têm
entalhes produzidos por eletroerosão ("EDM (electric discharge
machining) notches") nas direções axial e/ou circunferencial nas
superfícies interna e externa.
4.7. Método de inspeção
4.7.1 Faixa de inspeção
A inspeção por correntes parasitas abrange uma grande variedade de técnicas de inspeção específicas, que incluem, mas não se limitam a:
- a)
Detecção de trincas superficiais em placas ou componentes de geometria
complexa utilizando bobinas superfíciais, geralmente usando sondas de alta frequência e pequeno diâmetro.
- b)
Detecção de trincas superficiais em orifícios de fixação utilizando
sondas manuais e rotativas. Usando sondas de alta frequência e pequeno
diâmetro.
- c)
Trincas subsuperfíciais e de segundo camada em componentes
semelhantes a placas utilizando sondas superfíciais de baixa frequência e maior diâmetro.
- d) Medição da condutividade.
- e) Medição da espessura do revestimento.
- f) Medição da espessura do material.
- g) Inspeção de tubos e barras utilizando arranjos de sonda de bobina envolventes, internos ou multi-bobinas.
4.7.2 Registo das indicações
O registo das indicações é
dependente dos aparelhos e procedimentos utilizados. Técnicas
anteriores discutido na Seção 3.7.3 pode ser usado para registrar os
resultados do inspeção.
Dependendo
dos procedimentos de inspeção utilizados e da qualificação nível do
inspetor, o grau de análise e interpretação dos dados será diferente.
Para a maioria das inspeções de detecção de trincas, um END
secundário método é comumente empregado para confirmar os resultados.
4.7.3 Análise dos dados e interpretação dos resultados
Como
em qualquer outro método de END, o método de corrente parasita
baseia-se na avaliação dos sinais de correntes parasitas recebidos
contendo informações sobre as características do material. É necessário
para utilizar amostras de referência aplicáveis para inspecionar
adequadamente e analisar sinais de interesse. As amostras de referência
utilizadas, portanto, deve ser feito de materiais semelhantes com
electricidade e propriedades mecânicas como os materiais a examinar.
Este interpretação de sinais de correntes parasitas para determinar a
integridade das partes ensaiadas, portanto, dependem em grande parte
da seleção e escolha de amostras de referência adequadas.
4.8. Preparação de instruções escritas para o nível 1
A norma ISO9712
(2005) define as responsabilidades do pessoal de inspeção da seguinte
forma:
Nível 1
Uma pessoa certificada para o nível 1 deve ter demonstrado competência para realizar END de acordo com as instruções de END e sob o supervisão do pessoal de nível 2 ou nível 3.
No
âmbito da competência definida no certificado, O pessoal de nível 1
pode ser autorizado pelo empregador a realizar o de acordo com as
instruções de END:
- a) Instalar e ajustar o aparelho de END;
- b) Efetuar os ensaios;
- c) Registar e classificar os resultados dos ensaios;
- d) Comunicar os resultados.
O
pessoal certificado de nível 1 não deve ser responsável pela escolha do
método ou técnica de ensaio a ser utilizado, nem para a avaliação dos
resultados dos ensaios.
Nível 2
Um indivíduo certificado para o nível 2 deve ter demonstrado competência para realizar ensaios não destrutivos de
acordo com os procedimentos estabelecidos. No âmbito da competência
definido no certificado, o pessoal de nível 2 pode ser autorizado pelo
empregador para:
- a) Seleccionar a técnica de END para o método de ensaio a utilizar;
- b) Definir as limitações de aplicação do método de ensaio;
- c)
Traduzir os códigos, normas, especificações e procedimentos de END em
instruções de END, adaptados às condições reais de trabalho;
- d) Definir e verificar as condições de trabalho do equipamento;
- e) Efetuar e supervisionar ensaios;
- f) Interpretar e avaliar os resultados de acordo com os códigos, normas, especificações aplicáveis ou procedimentos;
- g) Preparar instruções de END para auxiliares;
- h) Executar e supervisionar todas as tarefas de nível 2 ou inferior;
- i) fornecer orientações para o pessoal de nível 2 ou inferior, e
- j) Comunicar os resultados dos ensaios não destrutivos.
Portanto,
todos os técnicos de níveis 1 são obrigados a trabalhar de acordo com
instruções escritas e preparados\por técnico de nível 2, no mínimo, autorizadas por um nível 3.
Os pormenores típicos dos requisitos de inspecção por escrito são apresentados no item 6.3.
|