IAEA - Correntes Parasitas - Capítulo 1 - CONCEITOS GERAIS
traduzido do livro: https://www.iaea.org/publications/8414/eddy-current-testing-at-level-2-manual-for-the-syllabi-contained-in-iaea-tecdoc-628rev-2-training-guidelines-for-non-destructive-testing-techniques
- Princípios Gerais dos Ensaios Não Destrutivos
(ENDs)
- Materiais e Descontinuidades
- Processos de Fabricação e Descontinuidades
- Materiais em Serviço e Mecanismos de Dano
- Qualidade e Normalização
- Exercícios do Capítulo 1
1. CONCEITOS GERAIS
1.1.
Princípios Básicos dos Ensaios Não Destrutivos (ENDs)
1.1.1 Definição e importância dos ENDs
Ensaio
não destrutivo é o uso de métodos físicos que testarão materiais,
componentes e peças quanto a falhas em sua estrutura sem prejudicar sua
utilidade futura. O END está preocupado em revelar falhas ou anomalias na estrutura de um produto. No entanto, não pode prever onde as falhas se desenvolverão devido ao próprio projeto. Todos os métodos de END têm as seguintes características comuns:
- (a) A aplicação de um meio de ensaio ao produto a ser testado.
- (b) Mudanças no meio empregado no ensaio que ocorrem devido a presença de descontinuidades na estrutura do produto.
- (c) Uma forma de detectar a mudança do meio de ensaio.
- (d) Forma de interpretação dessas mudanças para obter informações sobre as falhas na estrutura do produto.
Importância dos ENDs Os ENDs desempenham um papel importante no controle de qualidade de um produto. Podem ser utilizados durante todas as etapas de fabricação de um produto. São usados para monitorar a qualidade de:
- (a) Matérias-primas que são utilizadas na fabricação do produto.
- (b) Processos de fabricação que são usados para fabricar o produto.
- (c) Produto acabado antes de ser colocado em serviço.
O uso de END durante todas as etapas de fabricação resulta nos seguintes benefícios:
- (a) Aumenta a segurança e confiabilidade do produto durante a operação.
- (b)
Diminui o custo do produto final pela redução de descartes do produtos
finais e conservando materiais, mão de obra e energia.
- (c) Melhora a reputação do fabricante como produtor de bens de qualidade.
Todos os fatores acima tendem a
aumentar as vendas do produto (confiabilidade perante os
clientes) que trazem benefícios econômicos para o fabricante. Os ENDs
também são amplamente utilizados para determinação rotineira ou
periódica da integridade das plantas e estruturas durante o serviço.
Isso não apenas aumenta a segurança da operação, mas também elimina
paradas emergenciais das plantas.
1.1.2 Tipos de métodos de END
Os métodos de END variam do de execução mais simples aos de execução mais complexa. A inspeção visual é a mais simples de todas. As
imperfeições da superfície invisíveis ao olho podem ser reveladas pelos
métodos de líquidos penetrantes ou de partículas magnéticas. Se
forem encontrados defeitos superficiais realmente graves, muitas vezes
há pouco sentido em proceder a exames internos mais complexos por
ultrassom ou radiografia.
Os métods de END podem ser
divididos para os propositos desse curso como convencionais e não
convencionais. Os primeiros podem ser considerados aqueles de uso comum
e que incluem a inspeção visual ou ótica, líquidos penetrantes,
partículas magnéticas, correntes parasitas, ensaio radiográfico e
ensaio ultrassônico.
O segundo grupo dos métodos de ENDs são aqueles usados apenas em
aplicações específicas e consequentemente estão limitados quanto ao
uso. Alguns desses métodos que serão considerados aqui apenas por
curiosidade para os leitores incluem radiografia com neutrons, emissão
acústica, ensaio termográfico, ensaio por infravermelho, extensometria,
técnicas de microondas, teste de vazament, holografia, etc. Deve se
lembrar que nenhum desses métodos pode ser solução para a detecção de
todos as possíveis descontinuidades, ou seja, eles não são opções
alternativas, mas sim complementares entre si. Os princípios básicos,
aplicações típicas, vantagens e limitações dos métodos do grupo
um serão agora brevemente descritos.
1.1.3 Inspeção visual (VT- sigla da lingua inglesa)
Muitas
vezes esquecido em qualquer lista de métodos de END, a inspeção visual
é um dos meios mais comuns e mais poderosos dos ensaios não destrutivos. O ensaio visual requer iluminação adequada da superfície de teste e visão adequada do inspetor. No
entanto, para ser a inspeção visual mais eficaz, merece atenção
especial, pois requer treinamento (conhecimento do produto e processo,
condições de serviço previstas, critérios de aceitação, manutenção de
registros, por exemplo) e possui sua própria gama de equipamentos e
instrumentação. Também é um fato que todos os defeitos encontrados por outros métodos de END devem ser comprovados por inspeção visual. Os ensaios visuais podem ser classificados como ensaios visuais diretos, ensaios visuais remotos e ensaios visuais translúcidos. Os
métodos de END mais comuns partículas magnéticas (MT) e líquidos
penetrantes (PT) são, na verdade, simplesmente formas científicas de
melhorar a indicação para torná-la mais visível. Muitas vezes o equipamento necessário é simples (FIG. 1.1)
uma luz portátil, um espelho com haste, uma lente de mão com aumento de
2x ou 4x, uma lupa iluminada com ampliação de 5x ou 10x. Para inspeção interna, sistemas de lentes com luz, como boroscópios, permitem que superfícies remotas sejam examinadas. Dispositivos
óticos mais sofisticados usando fibra ótica permitem a introdução do
dispositivo em orifícios e canais de acesso muito pequenos. A maioria desses sistemas prevê a conexão de uma câmera para permitir a gravação permanente.
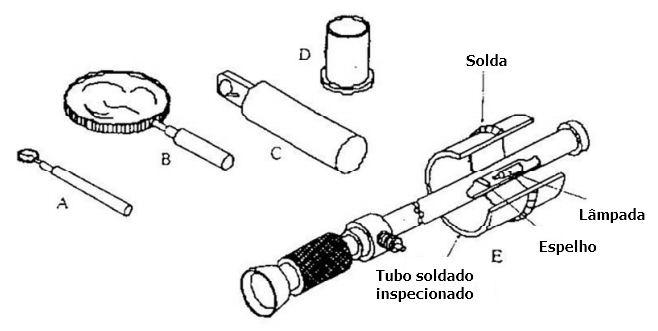
FIG. 1.1. Vários dispositivos óticos usados na inspeção visual.
(a) Espelho com haste
(b) Lupa de mão (amplificação geralmente entre 2 e 3X)
(c) Lupa com iluminação, campo de visão mais restrito que (d) (amplficação entre 5 e 10x)
(d) Lente de inspeção, normalmente possui uma escala para medição que
fica em contato com a superfície inspecionada (amplificação entre 5 e
10X)
(e) Boroscópio com iluminação interna (amplificação entre 2 e 3X)
As aplicações do ensaio visual incluem:
- (a) Verificação da condição da superfície do corpo de prova.
- (b) Verificação do alinhamento das superfícies em contato.
- (c) Verificação da forma do componente.
- (d) Verificação de evidência de vazamento.
- (e) Verificação de defeitos internos que chegam as laterais do componente.
1.1.4 Ensaios por Líquidos penetrantes (PT - sigla da lingua inglesa)
Este é um método que pode ser empregado para a detecção de
descontinuidades abertas à superfície em qualquer produto industrial
que seja feito de um material não poroso. Este método é amplamente
utilizado para ensaios de materiais não magnéticos. Neste método, um
líquido penetrante é aplicado na superfície do produto por um certo
tempo predeterminado, após o qual o excesso de penetrante é removido da
superfície. A superfície é então seca e um revelador é aplicado a ela.
O penetrante que permanece na descontinuidade é absorvido pelo
revelador para indicar a presença, bem como a localização, tamanho e
natureza da descontinuidade. O processo é ilustrado na FIG. 1.2.
Os penetrantes usados são penetrante com pigmentos de cor visível ou
penetrante com pigmentos de cor fluorescente. A inspeção para detectar
a presença de indicações de cor visível é feita sob luz branca,
enquanto a inspeção para detectar a presença de indicações por
penetrante de cor fluorescente é feita sob iluminação ultravioleta em
ambiente escurecidos (penumbra). Os processos de líquido penetrante são
ainda subdivididos de acordo com o método de remoção do excesso de
penetrante da amostra.
Os penetrantes podem ser:
- (i) lavável com água,
- (ii)
pós-emulsificável, ou seja, um emulsificante é adicionado ao excesso de
penetrante na superfície da amostra para torná-la lavável com água, e
- (iii)
removível por solvente, ou seja, o excesso de penetrante precisa ser
dissolvido em um solvente para removê-lo da superfície do corpo de
prova.
Em ordem de sensibilidade decrescente e custo também decrescente, os processos de líquido penetrante podem ser listados como:
- (a) Penetrante fluorescente pós-emulsificável.
- (b) Penetrante fluorescente removível por solvente.
- (c) Penetrante fluorescente lavável com água.
- (d) Penetrante visível pós-emulsificável.
- (e) Penetrante visível removível por solvente.
- (f) Penetrante visível lavável com água.
Algumas das vantagens do ensaio por líquidos penetrantes são as seguintes:
- (a) Custo relativamente baixo.
- (b) Método END altamente portátil.
- (c) Altamente sensível a descontinuidades finas e apertadas.
- (d) Método bastante simples.
- (e) Pode ser usado em uma variedade grande de materiais.
- (f)
Todas as descontinuidades da superfície são detectadas em uma única
aplicação, independentemente da orientação da descontinuidade.
Algumas das limitações do ensaio com líquidos penetrantes são as seguintes:
- (a) A superfície de ensaio deve estar livre de todos os contaminantes (sujeira, óleo, graxa, tinta, ferrugem, etc.).
- (b) Detecta apenas descontinuidades superficiais.
- (c) Não pode ser usado em amostras porosas e é difícil de usar em superfícies muito ásperas.
- (d) A remoção de todos os materiais penetrantes, após o ensaio, é frequentemente necessária.
- (e) Não existe um método fácil para produzir um registro permanente.
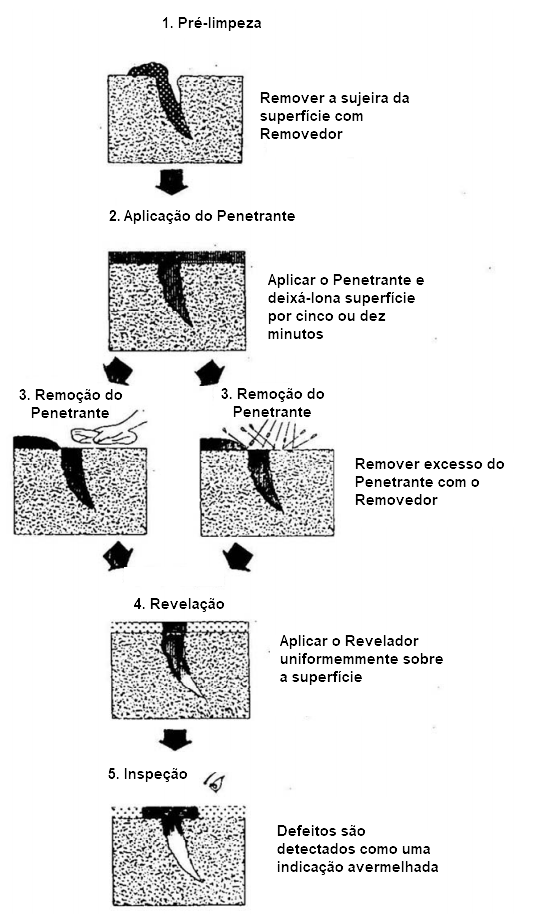
FIG. 1.2. Different stages of liquid penetrant process.
1.1.5 Ensaio de partículas magnéticas (MT = sigla da lingua inglesa) O ensaio de partículas magnéticas é usado para testar materiais que podem ser facilmente magnetizados. Este método é capaz de detectar falhas abertas à superfície e logo abaixo da superfície (subsuperficiais). Neste
método, a amostra de ensaio é primeiro magnetizada usando um imã
permanente ou um eletroímã ou passando corrente elétrica através dela
ou aproximado a amostra de um campo magnético gerado por um fio
enrolado ao redor da amostra (bobina). O campo magnético assim introduzido na amostra é composto por linhas de força magnéticas. Sempre
que houver uma falha que interrompa o fluxo das linhas de força
magnéticas, algumas dessas linhas devem sair e reentrar no corpo de
prova. Esses pontos de saída e reentrada formam pólos magnéticos opostos. Sempre
que partículas magnéticas diminutas são espalhadas na superfície de tal
amostra, essas partículas são atraídas por esses pólos magnéticos para
criar uma indicação visual aproximando o tamanho e a forma da falha. FIG. 1.3. ilustra os princípios básicos desse método.
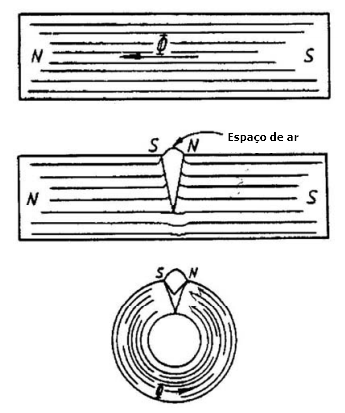
FIG. 1.3. Pricípio básico do ensaio de partículas magnéticas.
Dependendo da aplicação, existem diferentes técnicas de magnetização usadas no ensaio de partículas magnéticas. Essas técnicas podem ser agrupadas nas duas categorias a seguir:
- (a)
Técnicas de corrente contínua: São as técnicas em que a corrente flui
através do corpo de prova e o campo magnético produzido por este fluxo
de corrente é utilizado para a detecção de defeitos. Estas técnicas são mostradas na FIG. 1.4 (a, b & c).
- (b)
Técnicas de fluxo do campo magnético: Nestas técnicas, o fluxo
magnético é induzido no corpo de prova pelo uso de um ímã permanente ou
pela passagem de corrente através de uma bobina ou condutor. Estas técnicas são mostradas na FIG. 1,4 (d–g).
As vantagens do ensaio de partículas magnéticas incluem o seguinte:
- (a) Não necessita de uma operação de pré-limpeza muito rigorosa.
- (b) Melhor método para a detecção de trincas superficiais e finas em materiais ferromagnéticos.
- (c) Método de END rápido e relativamente simples.
- (d) Geralmente barato.
- (e) Trabalhará com revestimento fino.
- (f) Poucas limitações quanto ao tamanho/forma dos corpos de prova.
- (g) Método END altamente portátil.
- (h) É mais rápido.
Algumas das limitações do teste de partículas magnéticas incluem o seguinte:
- (a) O material deve ser ferromagnético.
- (b) A orientação e a força do campo magnético são críticas.
- (c) Detecta apenas descontinuidades superficiais e próximas à superfície.
- (d) Às vezes são necessárias grandes correntes.
- (e) 'Queima' de peças de ensaio é uma possibilidade.
- (f) As peças devem ser frequentemente desmagnetizadas, o que pode ser difícil.
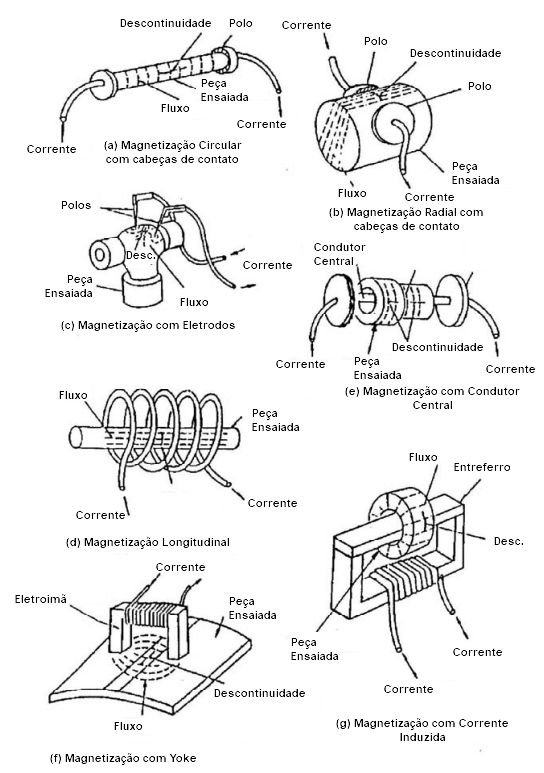
FIG. 1.4. Diferentes magnetizações empregadas no ensaio por partículas magnéticas.
1.1.6 Correntes parasitas (ET = sigla da lingua inglesa)
Este
método é amplamente utilizado para detectar falhas superficiais,
classificar materiais (composição química), medir espessura de paredes finas com acesso de apenas um dos lados,
medir revestimentos finos e, em algumas aplicações, medir a
profundidade da falha. Este método é aplicável apenas a materiais eletricamente condutores. No método, as correntes parasitas são produzidas no produto aproximando-o de uma bobina alimentada por corrente alternada. O campo magnético alternado da bobina é modificado pelos campos magnéticos das correntes parasitas. Essa
modificação, que depende da condição da peça próxima à bobina, é então
mostrada como uma leitura em medidor ou apresentação num tubo de raios
catódicos (antigamente), monitor informático, ou tela eletrônica. FIG. 1.5 fornece os princípios básicos do ensaio de correntes parasitas.
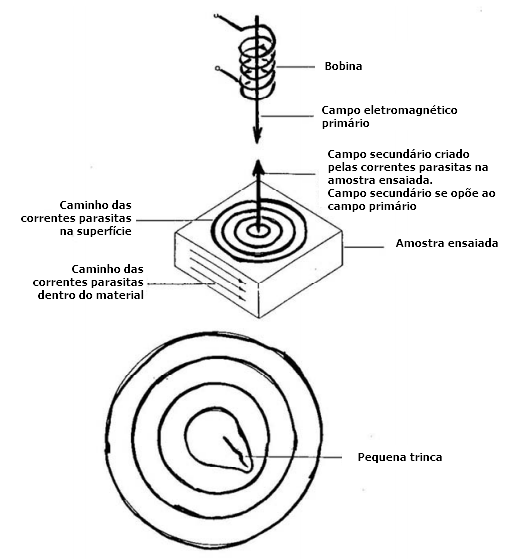
FIG. 1.5. (a) Geração de correntes parasitas na amostra.
(b) Distorção de correntes parasitas devido a presença de uma descontinuidade.
Quanto a forma, existem três tipos de sondas (FIG. 1.6) usadas no ensaio de correntes parasitas. As sondas internas são geralmente usadas para ensaios em serviço de tubos de trocadores de calor. As sondas envolventes são comumente usadas para o ensaio hastes, barras e tubos durante a fabricação. Os
usos das sondas superficiais incluem a localização de trincas,
classificação de materiais, medição da espessura da parede e do
revestimento e medição da profundidade da descontinuidade.
Este método pode ser usado para:
- (a) A detecção de defeitos em tubulações.
- (b) A seleção de materiais.
- (c) A medição de espessura de parede fina a partir do acesso a uma única superfície.
- (d) Medir revestimentos finos.
- (e) Medir a profundidade de trincas.
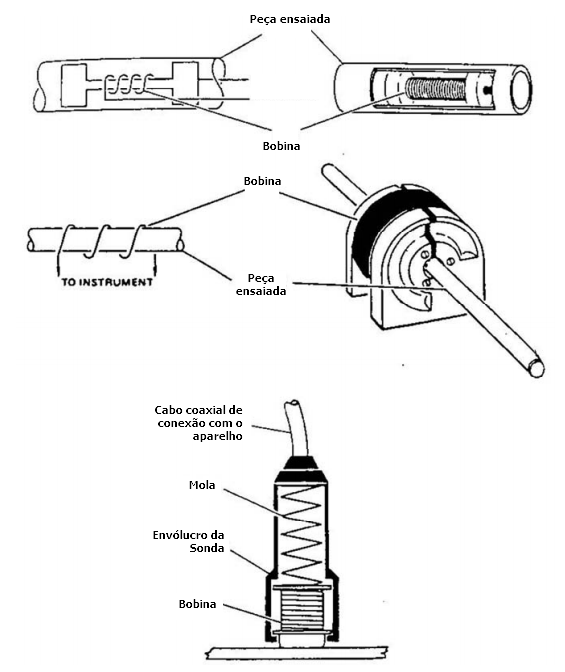
FIG. 1.6. Tipos de sondas usadas em ensaios de correntes parasitas.
(a) bobina interna)
(b) bobina envolvente
(c) sonda superficial.
Algumas das vantagens do ensaio de correntes parasitas são:
- (a) Não requer acoplante.
- (b) Dá resposta instantânea.
- (c) Tem etapas fáceis durante a calibração (ajustes de parâmetros para o ensaio).
- (d) É extremamente sensível a falhas.
- (e) É muito repetível.
- (f) Altas velocidades de varredura podem ser usadas.
- (g) É muito preciso para análise dimensional de falhas ou espessura de revestimento.
Algumas das limitações do ensaio de correntes parasitas são:
- (a) A teoria requer uma boa formação acadêmica em princípios elétricos e em matemática.
- (b) Extremamente sensível às variações da superfície e, portanto, requer um bom estado ou preparação da superfície.
- (c) É aplicável apenas a materiais condutores de eletricidade.
- (d)
Pode ser usado em materiais não magnéticos e magnéticos, mas não é
confiável em aço carbono para a detecção de falhas subsuperficiais.
- (e) Sua profundidade de penetração é limitada.
- (f) O grau de fechamento da fissura e a orientação das correntes
parasitas com relação a descontinuidade linear afetarão a
detectabilidade.
1.1.7 Ensaio radiográfico (radiografia, sigla em inglês = RT)
O método radiográfico é usado para a detecção de falhas internas em diversos materiais e configurações geométricas de peças. Um
filme radiográfico apropriado é colocado atrás da amostra de ensaio
(FIG. 1.7) e é exposto passando raios X ou raios gama (radiisótopos
Co-60 e Ir-192, principalmente) através dele. A
intensidade dos raios X ou raios gama ao passar pelo produto é
modificada de acordo com a estrutura interna da amostra e assim o filme
exposto, após o processamento, revela a imagem sombreada (tons de cinza), conhecida
como radiografia, do produto. Em seguida, é interpretado para obter dados sobre as falhas presentes no corpo de prova. Este método é usado em uma ampla variedade de produtos, como forjados, fundidos e soldados.
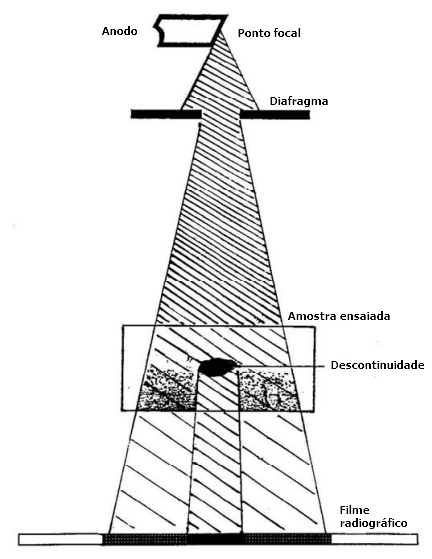
FIG. 1.7. Arranjo dos componentes para realização do ensaio radiográfico.
Algumas das vantagens do teste radiográfico são:
- (a) Pode ser usado para inspecionar grandes áreas de uma só vez.
- (b) É útil em uma ampla variedade de materiais.
- (c) Pode ser usado para verificar má estrutura interna, montagem incorreta ou desalinhamento.
- (d) Fornece registro permanente (o próprio filme radiográfico).
- (e) Nenhuma calibração necessária no local de trabalho.
- (f) Dispositivos para verificar a qualidade da radiografia estão disponíveis.
- (g) A interpretação de radiografias pode ser feita em condições confortáveis (laboratório com negatoscópio).
Algumas das limitações deste método são:
- (a) Os raios X e os raios gama são perigosos para a saúde humana. As Séries de Publicações Segurança contra Radiação da IAEA são indicadas para segurança pessoal e proteção contra radiação.
- (b) Não pode detectar defeitos planares em todas as condições (depende da orientação da fonte e da falha).
- (c) É necessário acesso a ambos os lados da amostra.
- (d) A faixa de espessura que pode ser inspecionada é limitada.
- (e)
Certas áreas em muitos itens não podem ser radiografadas devido à
consideração geométrica (geometria da peça gerando imagens em falsa
grandeza).
- (f) A sensibilidade da inspeção diminui com a espessura da peça radiografada.
- (g)
É mais caro normalmente que os demais ensaios convencionais,
principalmente PM (partículas magnéticas) e LP (líquidos penetrantes).
- (h) Não pode ser facilmente automatizado.
- (i) Requer habilidade considerável para a interpretação das radiografias.
- (j) Profundidade de descontinuidade não é indicada.
1.1.8 Ensaio ultrassônico (sigla em inglês = UT)
A
inspeção ultrassônica é um método
não destrutivo no qual ondas sonoras de alta frequência
são introduzidas no material que está sendo inspecionado.
A maioria das
inspeções ultrassônicas é feita em
frequências entre 0,5 e 20 MHz, bem acima da faixa de
audição humana que é cerca de 16 Hz a 20 kHz. As
ondas sonoras viajam através do material com alguma perda de
energia (atenuação) devido às
características do material. A
intensidade das ondas sonoras é medida, após
reflexão (pulso refletido) nas interfaces (ou falhas) ou é
medida na superfície oposta da amostra (pulso transmitido). O feixe sonoro refletido é detectado e analisado para definir a presença e a localização das falhas. O
grau de reflexão depende em grande parte do estado físico
(propriedade física impedância acústica) da matéria no lado oposto da interface e, em menor grau, das
propriedades físicas específicas da matéria no qual a feixe estava viajando até chegar a interface.
A reflexão parcial ocorre em interfaces metal-líquido ou metal-sólido. O ensaio ultrassônico tem um poder de penetração
superior ao da radiografia e pode detectar falhas profundas na amostra
ensaiada (digamos, até cerca de 6 a 7 metros de aço). É
bastante sensível a pequenas falhas e permite a
determinação precisa da localização e
tamanho das falhas. O princípio básico do ensaio ultrassônico é ilustrado na FIG. 1.8.
O ensaio ultrassónico é:
- (a) Usado principalmente para detecção de falhas em materiais.
- (b) Amplamente utilizado para medição de espessura.
- (c) Usado para a determinação de propriedades mecânicas e estrutura de grãos (metalúrgica) de materiais.
- (d) Usado para a avaliação de variáveis de processamento mecânico na fabricação de peças com os materiais.
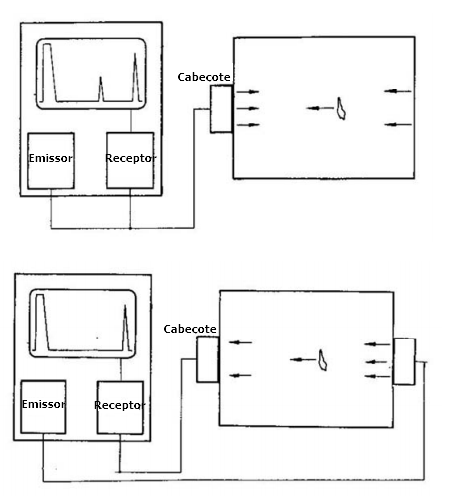
FIG. 1.8. Componentes básicos de um sistema ultrassônico de detecção de falhas.
(a) técnica pulso-eco
(b) técnica de transmissão
Algumas das vantagens dos ensaios ultrassônicos são:
- (a) Tem alta sensibilidade que permite a detecção de defeitos minúsculos.
- (b)
Possui alto poder de penetração (da ordem de 6 a 7 metros
em aço) o que permite o exame de seções
extremamente espessas.
- (c) Tem uma alta precisão de medição da posição e tamanho da falha.
- (d) Possui resposta rápida que permite inspeção rápida e automática.
- (e) Precisa de acesso a apenas uma superfície do corpo de prova.
Algumas das limitações deste método são:
- (a) A geometria desfavorável do corpo de prova causa problemas durante a inspeção.
- (b) A inspeção de materiais com estrutura interna indesejável (grosseira e/ou altamente atenuante) é difícil.
- (c) Requer o uso de um acoplante.
- (d) A sonda deve ser devidamente acoplada durante a varredura.
- (e) A orientação do defeito afeta a detectabilidade do defeito.
- (f) O equipamento é bastante caro.
- (g) É necessária mão de obra altamente qualificada.
- (h) Padrões de referência e calibração são necessários.
- (i)
Superfícies ásperas podem ser um problema e a
preparação da superfície é
necessária.
1.1.9 Comparação dos diferentes métodos de END
Frequentemente pode ser necessário usar um método de END para confirmar os resultados de outro. Portanto,
vários métodos devem ser considerados complementares e
não competitivos, ou como alternativas opcionais. Cada
método tem seus méritos e limitações
particulares e estes devem ser levados em consideração
quando qualquer programa de ensaio é planejado. A Tabela 1.1 apresenta um resumo dos métodos de END mais usados.
TABLE 1.1. COMPARAÇÃO DE VÁRIOS MÉTODOS DE END
(A: custo altíssimo, D: custo baixíssimo)
Técnica
|
Requisitos de Acesso
|
Custo do Sistema
|
Custo da Inspeção
|
Notas Importantes
|
Métodos Óticos
|
Pode ser empregada para visualizar o interior de equipamentos complexos.
Apenas um ponto de acesso pode ser suficiente.
|
B/D
|
D
|
Muito verátil; Pouca habilidade requerida; Deve ter considerções que permitam a execução no projeto
|
Radiografia
|
Necessita acesso aos dois lados da peça inspecionada
|
A
|
B/C
|
Apesar dos grandes
custos, grandes áreas pode ser inspecionadas de uma só vez. Habilidade
considerável requerida para interpletação dos resultados.
|
Ultrassom
|
Um lado ou ambos (ou extremos) devem estar acessíveis.
|
B
|
B/C
|
Requer inspeção ponto a ponto implicando em muito trabalho em grandes estruturas; Pessoal habilitado é requerido.
|
Partículas Magnéticas
|
Requer uma superfície relativamente suáve e limpa.
|
C
|
C/D
|
Apenas para
materiais magnéticos como os aços; Pouca habilidade requerida; Apenas
descontinuidades superficiais ou próximas a superfície
|
Líquidos Penetrates
|
Requer que a descontinuidade seja acessada pelo penetrante (isto é, na supefície que deve estar limpa
|
D
|
C/D
|
Para todos os materiais; Alguma habilidade requerida; Apenas
descontinuidades superficiais; Passível de má interpretação dos
resultados.
|
Correntes Parasitas
|
Superfície deve (usualmente) ser razoavelmente suáve e limpa
|
B/C
|
C/D
|
Para materiais
eletricamente condutores apenas; Para descontinuidades superficiais;
Para variações de espessura de revestimento, ou comparação de
materiaiPars; Para outras comparações mais complexas habilidades
especiais são requeridas.
|
1.2. Materiais e Descontinuidades
1.2.1 Estruturas dos metais (puros) e das ligas metálicas
As propriedades dos metais podem ser explicadas em termos da maneira
pela qual os átomos de um metal estão ligados. Nesta ligação, chamada de 'ligação metálica', que é formada entre átomos
metálicos semelhantes quando alguns elétrons na camada de
valência se separam de seu átomo e existem em uma nuvem ao
redor de todos os átomos carregados positivamente. Esses átomos carregados positivamente se organizam em um padrão muito ordenado. Os
átomos são mantidos juntos por causa de sua
atração mútua pela nuvem eletrônica negativa
FIG. 1.9.
Como os elétrons são livres para se mover em um campo elétrico, os metais conduzem eletricidade. Como
os elétrons livres absorvem e irradiam de volta a maior parte da
energia luminosa que incide sobre eles, os metais são opacos e
brilhantes. Como os elétrons livres podem transferir energia térmica, os metais conduzem o calor de forma eficaz. A
ligação metálica não é
específica, o que explica por que diferentes metais podem ser
ligados ou unidos um ao outro. Também é não direcional, puxando com a mesma força em todas as direções. Portanto,
ele liga os átomos de metal firmemente, de modo que seus
núcleos (núcleos e elétrons da camada interna) se
encaixam bem uns nos outros. O
empacotamento fechado favorecido pela ligação
metálica é melhor realizado em certas estruturas
cristalinas regulares. Essas
estruturas, embora resistentes à tração, oferecem
menor resistência às forças de cisalhamento e,
portanto, explicam a ductilidade dos metais.
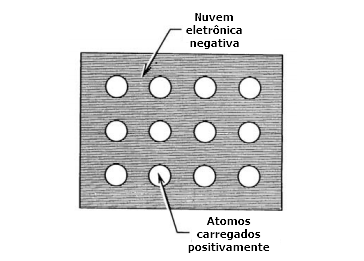
FIG. 1.9. Ilustração esquemática da interação metalúrgica.
Estrutura cristalina
Toda matéria é considerada composta de substâncias
unitárias conhecidas como elementos químicos. Estas são as menores unidades que são distinguíveis com base em sua atividade química e propriedades físicas. Os elementos são compostos de átomos que possuem uma estrutura distinta característica de cada elemento. Os átomos são pequenos demais para serem vistos com o auxílio de microscópios comuns,
mas o contorno das moléculas foi detectado com dispositivos como
o microscópio eletrônico de varredura e o de campo iônico. Os elementos químicos podem ser aproximadamente classificados em três grupos: metais, metalóides e não metais.
Algumas das propriedades que um elemento deve ter para ser considerado um metal são:
(1) estrutura cristalina;
(2) alta condutividade térmica e elétrica;
(3) capacidade de ser deformado plasticamente;
(4) brilho metálico ou alta refletividade da luz;
(5) capacidade de doar elétrons e formar um íon positivo.
Metalóides se assemelham a metais em alguns aspectos e a não metais em outros. Exemplos de metalóides são carbono, boro e silício. Os demais elementos são conhecidos como não-metais. Isso inclui os gases inertes, os elementos do Grupo VIIA (fluor (F), cloro (Cl), bromo (Br), iodo (I), astato (At)), N, O, P e S.
As propriedades mecânicas dos metais derivam então de sua estrutura cristalina. Isto
é, os átomos no estado sólido de um metal
estão dispostos em formas geométricas tridimensionais
definidas padrões para formar cristais ou grãos do metal. A
rede formada pela união do centro dos átomos em um
cristal é chamada de 'rede espacial' ou 'rede cristalina' do metal. O menor volume
em uma rede espacial que representa adequadamente a
posição dos átomos em relação uns
aos outros é conhecido como célula unitária. Existem quatorze tipos de células unitárias, mas as estruturas da maioria
dos metais comuns e comercialmente importantes no estado sólido
são construídas a partir dos seguintes três tipos
de células unitárias:
(a) Cubo de Corpo Centradac (CCC)
A célula cúbica de corpo centrado é composta por nove átomos. Oito estão localizados nos cantos do cubo com o nono posicionado centralmente entre eles, FIG. 1.10a. A cúbica de corpo centrado é uma estrutura forte e, em geral, os metais que são duros e fortes estão nessa forma em temperaturas normais. Esses metais incluem, por exemplo, cromo, molibdênio, bário, tungstênio, sódio e vanádio. O aço abaixo de 723 0C também possui essa estrutura e é chamado de ferro alfa ou ferrita.
(b) Cubo de Face Centrada (CFC)
As
células cúbicas de face centrada consistem em quatorze átomos com oito
nos vértices e os outros seis centrados nas faces do cubo, FIG. 1.10b.
Essa estrutura é característica dos metais dúcteis, que incluem
alumínio, cobre, ouro, chumbo, níquel, platina e prata. O ferro, que é
cúbico de corpo centrado à temperatura ambiente, também é da estrutura
de face centrada na faixa de temperatura de cerca de 910 o C a 1.400 o
C e é chamado de ferro gama ou austenita.
(c) Hexagonal Compacta (HC)
Dezessete átomos se combinam para formar a célula unitária hexagonal compacta. Sete átomos estão localizados em cada face hexagonal com um em cada canto e o sétimo no centro. Os três átomos restantes ocupam uma posição triangular no centro da célula equidistante das duas faces, FIG. 1,10c. Os metais com esta estrutura são bastante susceptíveis ao endurecimento. Alguns dos metais mais comumente usados que cristalizam com esta estrutura são cádmio, cobalto, magnésio, titânio e zinco.
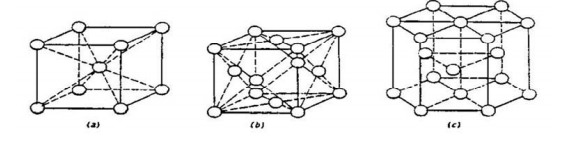
FIG. 1.10. Tipos de cristais.
(a) Cúbica de Corpo Centrado (CCC)
(b) Cúbica de Face Centrada (CFC) (c) Hexagonal Compacta (HC)
Grãos (cristais) e contornos de grão
Quando um metal é resfriado do estado líquido para o
estado sólido, porque o resfriamento não pode ser
exatamente o mesmo para todos os átomos, certos átomos
serão atraídos uns aos outros para formar uma célula unitária à frente de outros. Esta célula unitária torna-se o núcleo para a formação de cristais. À
medida que o resfriamento continua, outros átomos
assumirão suas posições ao lado desse
núcleo e os cristais, ou como geralmente é chamado no caso de metais, o grão, crescerá em tamanho. Esse
crescimento ordenado do grão continua em todas as
direções até encontrar interferência de
outros grãos que estão se
formando simultaneamente em torno de outros núcleos. A FIG. 1.11 ilustra o processo de formação de grãos e contornos de grão.
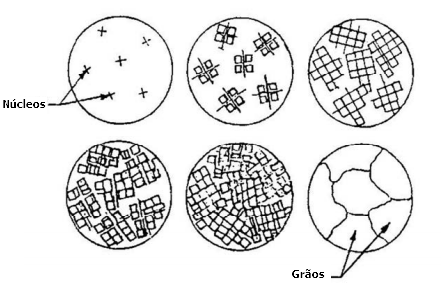
FIG. 1.11. Crescimento de cristais e grãos durante a solidificação.
Embora
com alguns metais com tratamento térmico especial seja possível crescer
cristais únicos com vários centímetros de
diâmetro, na maioria dos metais nas taxas de resfriamento usuais,
um grande número de cristais é nucleado e cresce ao mesmo tempo com diferentes orientações. Se
dois grãos com a mesma orientação se encontrarem,
eles se unirão para formar um grão maior, mas se
estiverem se formando em torno de eixos
diferentes, os últimos átomos a se solidificarem entre os
grãos em crescimento serão atraídos por cada um e
devem assumir posições de compromisso na tentativa para
satisfazer um desejo duplo de se unir a cada um. Esses átomos
mal posicionados estão em camadas ao redor dos grãos e
são conhecidos como contornos de grão. São interrupções no arranjo ordenado das estruturas cristalinas ordenadas de cada grão e oferecem resistência à deformação do metal. Um
metal de grão fino com um grande número de contornos de grão, portanto, será mais duro e mais
forte do que um metal de grãos grossos da mesma
composição e condição.
Estrutura das ligas metálicas
Uma liga é uma substância que possui propriedades
metálicas e é composta por dois ou mais elementos
químicos, dos quais pelo menos um é um metal. A maioria dos materiais metálicos usados comercialmente não são metais puros, mas ligas que consistem em mais de um elemento. Alguns deles podem ser elementos não metálicos. Fundamentalmente, existem três modos de arranjo de átomos ou fases em ligas. Esses três modos (fases) são; metal puro, solução sólida e composto intermetálico. Para
simplificar a ilustração, uma liga com dois elementos A e
B deve ser considerada na discussão a seguir.
(a) Metal puro
Não
existem átomos B nos grãos de cristal A nem átomos
A nos grãos B, ou seja, mistura de grãos de cristal A e B
puros. Os metais A e B são mutuamente insolúveis. Essa
completa falta de intersolubilidade é teoricamente quase
impossível (a solubilidade de um componente em outro pode ser
extremamente pequena, mas dificilmente nula).
(b) Solução sólida
Qualquer solução é composta de duas partes: um soluto e um solvente. O
soluto é a menor parte da solução ou do material
que é dissolvido, enquanto o solvente constitui a maior parte da solução. Existem átomos B (soluto) em grãos de cristal A (solvente). As
soluções sólidas são de dois tipos:
soluções sólidas substitucionais e
soluções sólidas intersticiais.
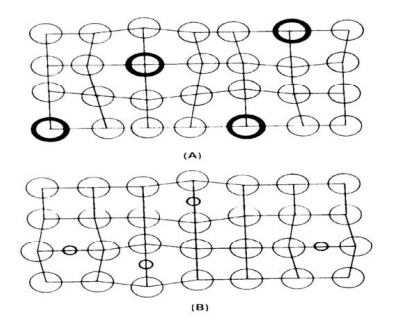
FIG. 1.12. Ilustração esquemática de soluções sólidas substitucionais (a) e intersticiais (b).
Solução sólida substitucional
Uma solução sólida substitucional
é uma solução de dois ou mais elementos com
átomos que são quase do mesmo tamanho. Este requisito é necessário porque os átomos de liga precisam substituir os átomos regulares na estrutura de rede como mostrado na FIG. 1.12 (a). Exemplos
de soluções sólidas substitucionais são
ouro dissolvido em prata e cobre dissolvido em níquel.
Solução sólida intersticial
As soluções sólidas intersticiais são compostas de elementos de liga ou átomos que diferem muito em tamanho.
Os átomos de liga devem ser pequenos o suficiente para caber dentro da estrutura de rede do material base. Este tipo de solução sólida é chamado intersticial e é ilustrado na FIG. 1.12 (b).
Pequenas quantidades de carbono, nitrogênio e hidrogênio podem se ligar intersticialmente ao ferro e outros metais.
Compostos intermetálicos
Geralmente são formados entre metais quimicamente diferentes e
são combinados seguindo as regras de valência
química. Como geralmente possuem forte ligação (iônica ou covalente), suas propriedades são essencialmente não metálicas. Os elementos A e B formam um composto intermetálico AB. Em
contraste com uma solução sólida, a
proporção do número de átomos A para
átomos B é fixa (m: n), e a estrutura cristalina é
bastante diferente dos cristais de metal A e B e geralmente muito
complexa. Quase todos
os compostos intermetálicos são muito duros e
quebradiços devido à sua estrutura cristalina complexa.
Transformação alotrópica
Muitos metais existem em mais de uma estrutura cristalina. A
transformação quando um metal muda de um arranjo de
cristal para outro é chamada de 'transformação
alotrópica' ou 'transformação de fase'. O ferro existe em três formas alotrópicas: CCC (abaixo de 704 oC), CFC (acima de 911 o C), e ferro delta (entre 1398 o C e 1538 o C). A temperatura exata é determinada pela quantidade de carbono e outros elementos de liga no metal. As propriedades do ferro e do aço são governadas pelas
transformações de fase que sofrem durante o processamento. Compreender essas transformações é essencial para o sucesso da soldagem desses metais.
O aço é uma liga de ferro que contém menos de 2% de carbono. A
presença de carbono altera as temperaturas nas quais o a mudança do
estado líquido para o estado sólido e as transformações de fase
ocorrem. A adição de outros elementos de liga também afeta as temperaturas de transformação. As
variações no teor de carbono têm um efeito profundo
tanto nas temperaturas de transformação quanto nas
proporções e distribuições das
várias fases (austenita, ferrita e cementita). O diagrama de fases ferro-carbono é mostrado na FIG. 1.13.
No resfriamento, a transformação da ferrita delta em austenita ocorre a 1390 oC
em ferro essencialmente puro, mas em aço, a temperatura de
transformação aumenta com o aumento do teor de carbono
até um máximo de 1492 oC.
Aços com mais de 0,5 por cento de carbono passam do estado líquido para
o sólido diretamente em austenita a uma temperatura abaixo de 1492 oC e, portanto, a ferrita delta não existe nesses aços. Em resfriamento adicional, a austenita se transforma em ferrita mais carboneto de ferro. Esta é uma das transformações mais importantes no aço. O seu controle é a base para a maioria dos tratamentos térmicos utilizados para o endurecimento do aço. Esta transformação ocorre em ferro essencialmente puro a 910 oC. No aço com teor de carbono crescente, no entanto, ocorre em uma faixa de temperaturas entre os limites A3 e A1, FIG. 1.13.
O limite superior desta faixa de temperatura (A3) varia de 910 oC até 723 oC. Por exemplo, o A3 de um aço carbono 0,10 por cento é 870 oC, enquanto para um aço carbono 0,50 por cento é 775 oC. Assim,
tanto em alta quanto em baixa temperatura a presença de carbono
promove a estabilidade da austenita em detrimento da ferrita delta e
alfa. A temperatura mais baixa da faixa (A1) permanece em 723 oC para todos os aços carbono simples, independentemente do nível de carbono. A
austenita pode dissolver até 2,0% de carbono em
solução sólida, mas a ferrita pode dissolver
apenas 0,025%. Na temperatura A1, a austenita se transforma em ferrita e um composto intermetálico de ferro e carbono (Fe3C), chamado cementita. A ferrita e a cementita nas plaquetas adjacentes formam uma estrutura lamelar, conhecida como perlita.
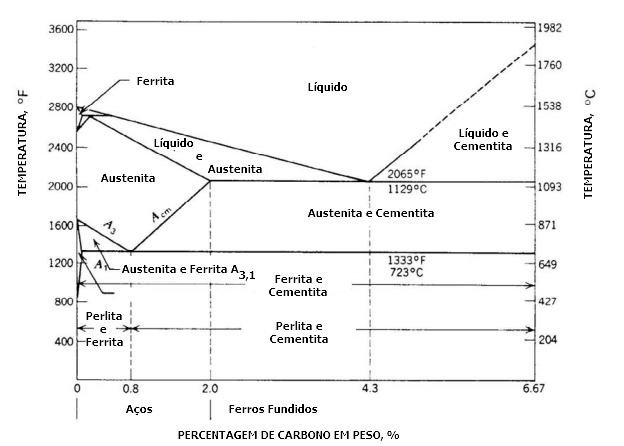
FIG. 1.13. O diagrama de fases ferro-carbono.
A maioria dos elementos de liga comuns adicionados ao aço
alteram ainda mais as temperaturas de transformação. As
microestruturas à temperatura ambiente de ligas de ferro-carbono
nas condições de equilíbrio cobertas por este
diagrama incluem um ou mais dos seguintes constituintes:
(a) Ferrita: Uma solução sólida de carbono em ferro alfa.
(b) Perlita: Uma mistura de cementita e ferrita que se forma em placas ou lamelas.
(c) Cementita: Carboneto de ferro, Fe3C, presente na perlita ou como carbonetos maciços em aços de alto carbono.
(d) Austenita: Uma mistura sólida de carbono em ferro gama.
(e) Leborita: Uma mistura eutética de austenita e cementita.
Quando
os aços carbono são resfriados lentamente a partir da
faixa de temperatura austenítica, as quantidades relativas
desses três constituintes à temperatura ambiente dependem
da composição química. No entanto, a decomposição da austenita é suprimida quando a taxa de resfriamento é acelerada. Quando
a transformação começa, ela progride mais
rapidamente e grandes volumes de perlita são formados. À
medida que a taxa de resfriamento é aumentada, as lamelas de
perlita tornam-se mais finas (plaquetas próximas). Em
taxas de resfriamento rápidas, temperaturas de
transformação ainda mais baixas são encontradas e
uma distribuição de carbonetos em ferrita é
formada em vez de perlita. Com
arranjo de aspecto de agulhas de cisalhamento com carbonetos finos em
uma matriz de ferrita se forma e é chamado de bainita. Tem resistência e dureza significativamente maiores e menor ductilidade do que as estruturas perlíticas finas. Com taxas de resfriamento muito rápidas (tratamento térmico de têmpera severa), a martensita é formada. A martensita é o produto mais duro da decomposição da austenita. Quando
a taxa de resfriamento é rápida o suficiente para formar
100 por cento de martensita, nenhum aumento adicional na dureza pode
ser alcançado por uma têmpera mais rápida. A
decomposição da austenita é uma
consideração importante na soldagem de ligas de
aço porque o metal de solda e partes da zona termicamente
afetada sofrem essa transformação.
1.2.2 Propriedades dos materiais (metálicos e não metálicos)
As propriedades mecânicas dos materiais metálicos são definidas
como as propriedades de um material que revelam seu comportamento
elástico e inelástico (plástico) quando a
força é aplicada, indicando assim sua
adequação para aplicações mecânicas,
por exemplo, módulo de elasticidade, resistência à
tração, alongamento, dureza e limite de fadiga. Outras
propriedades mecânicas, não mencionadas especificamente
acima, são resistência ao escoamento, ponto de escoamento,
resistência ao impacto e redução de área,
para mencionar alguns dos termos mais comuns. Em
geral, qualquer propriedade relativa às características
de resistência dos metais é considerada uma propriedade
mecânica. As
propriedades físicas referem-se à física de um
metal, como densidade, propriedades elétricas, propriedades
térmicas, propriedades magnéticas e semelhantes. Essas e outras propriedades serão descritas aqui com um pouco mais de detalhes.
Elasticidade e plasticidade
Quando uma tensão ou força é aplicada a um metal, ele muda de forma. Por
exemplo, um metal sob tensão de compressão irá
encurtar e o metal sob tensão irá alongar. Essa mudança na forma é chamada de deformação. A
capacidade do metal de deformar sob carga e depois retornar ao seu
tamanho e forma originais quando descarregado é chamada de
elasticidade. O limite
elástico (limite proporcional) é a maior carga que um
material pode suportar e ainda retornar à sua forma original
quando a carga é removida. Dentro
da faixa elástica, a tensão é proporcional
à deformação e isso é conhecido como lei de
Hooke. A
relação entre a tensão ou carga aplicada e a
conseqüente deformação ou mudança no
comprimento é mostrada na FIG. 1.14. A extremidade da parte em linha reta, no gráfico, é conhecida como limite elástico.
Um
ponto na curva ligeiramente superior ao limite elástico é conhecido
como ponto de escoamento ou tensão de escoamento. A carga permitida ou
segura para um metal em serviço deve estar bem abaixo do limite
elástico. Se forem aplicadas cargas mais altas, no entanto, a faixa de
elasticidade ou deformação elástica é excedida e o metal agora fica
permanentemente deformado. Agora ele não retornará às suas dimensões
originais mesmo quando a carga for removida. Por esta razão, a área da
curva tensão-deformação além do limite elástico é chamada de faixa
plástica. É esta propriedade que torna os metais tão úteis. Quando
força suficiente é aplicada por laminação, prensagem ou golpes de
martelo, os metais podem ser moldados, quando quentes ou frios, em
formas úteis. Se a aplicação de carga é aumentada na região plástica
chega-se a um estágio em que o material fratura.
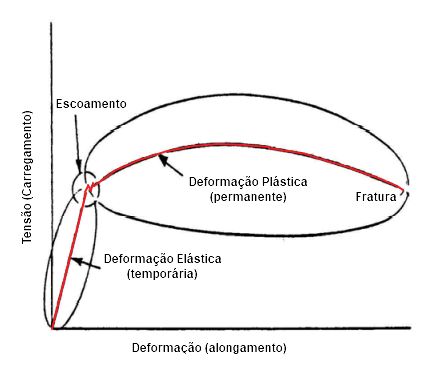
FIG. 1.14. Curva
tensão-deformação mostrando porções
elásticas e plásticas de uma curva típica.
Uma característica muito importante da curva tensão-deformação deve ser apontada. A
parte reta ou elástica da curva
tensão-deformação de um determinado metal tem uma
inclinação constante. Ou seja, não pode ser alterado, alterando a microestrutura ou tratamento térmico. Essa inclinação, chamada de módulo de elasticidade, mede a rigidez do metal na faixa elástica. Alterar a dureza ou resistência não altera a rigidez do metal. Existe apenas uma condição que altera a rigidez de qualquer metal, que é a temperatura. A rigidez de qualquer metal varia inversamente com sua temperatura; isto é, à medida que a temperatura aumenta, a rigidez diminui e vice-versa.
Resistência Metálica
A
resistênia de um metal é sua capacidade de resistir à
mudança de forma ou tamanho quando forças externas
são aplicadas. Existem três tipos básicos de tensões: tração, compressão e cisalhamento. Quando consideramos a resistência, deve-se conhecer o tipo de tensão a que o material será submetido. O
aço tem a mesma resistência à compressão e
à tração, mas o ferro fundido tem baixa
resistência à tração e alta
resistência à compressão. A
resistência ao cisalhamento é menor que a
resistência à tração em praticamente todos
os metais.
A
resistência à tração de um material pode ser
determinada dividindo a carga máxima pela área da
seção transversal original antes do teste. Assim:
Resistência
à tração = (Carga máxima)/(Área da
seção transversal original)
(1.1)
Os metais são 'puxados' (tracionados) em uma máquina chamada máquina de tração. Um
corpo de prova de dimensões conhecidas é colocado na
máquina de ensaio de tração e carregado lentamente
até quebrar (fraturar). Os
instrumentos às vezes são usados para fazer um registro
contínuo da carga e da quantidade de tensão
(mudança proporcional no comprimento). Esta informação é colocada em um gráfico chamado diagrama tensão-deformação. Um diagrama tensão-deformação pode ser feito para qualquer metal.
Dureza
A dureza de um metal é sua capacidade de resistir à deformação permanente. Existem três maneiras de medir a dureza; resistência à penetração, dureza elástica e resistência à abrasão (risco). A dureza varia consideravelmente de material para material. Essa
variação pode ser ilustrada fazendo uma
indentação em um metal macio, como o alumínio, e
depois em um metal duro, como uma liga de aço para ferramentas. A
indentação pode ser feita com um punção
central comum e um martelo, dando um leve golpe de igual força
em cada um dos dois espécimes. Neste caso, apenas por observação visual, pode-se dizer qual espécime é mais difícil de penetrar. É
claro que este não é um método confiável de
teste de dureza, mas mostra um dos princípios dos métodos de medição de
dureza; medir a
penetração da amostra por um penetrador,
como uma esfera de aço ou ponta de diamante.
As máquinas de medição de dureza Rockwell, Vicker e Brinell são os tipos de
durômetros mais usados para fins industriais e
metalúrgicos. Os operadores de tratamentos térmicos, inspetores e muitos outros na indústria costumam usar essas máquinas. O
teste de dureza Rockwell é feito aplicando duas cargas a uma
amostra e medindo a diferença na profundidade de
penetração na amostra entre a carga menor e a maior.
O ensaio de dureza Brinell é feito forçando uma esfera de
aço, geralmente de 10 milímetros (mm) de diâmetro,
no corpo de prova usando um peso de carga conhecido e medindo o
diâmetro da impressão resultante. Um pequeno microscópio é usado para medir o diâmetro das impressões. Várias
cargas são usadas para testar diferentes materiais, por exemplo,
500 kg (kg) para materiais macios como cobre e alumínio e 3.000
kg para aços e ferros fundidos. Geralmente
quanto mais duro o material, maior será sua resistência
à tração, ou seja, sua capacidade de resistir
à deformação e ruptura, quando uma carga é
aplicada.
Ductilidade
A
propriedade que permite que um metal se deforme permanentemente quando
carregado em tração é chamada de ductilidade. Qualquer metal que pode ser transformado em um fio é dúctil. Aço, alumínio, ouro, prata e níquel são exemplos de metais dúcteis. O ensaio de tração é usado para medir a ductilidade. As
amostras de tração são medidas quanto à
área e comprimento entre as marcas de calibração
(marcas feitas nos corpos de prova ensaiados) antes e depois de serem tracionados. A
porcentagem de alongamento (aumento no comprimento) e a porcentagem de
redução na área (diminuição da
área no ponto mais estreito) são medidas de ductilidade. Uma
alta porcentagem de alongamento (cerca de 40%) e redução
na área (cerca de 70%) indica uma alta ductilidade. Um metal com menos de 20% de alongamento teria baixa ductilidade.
Maleabilidade
A
capacidade de um metal de se deformar permanentemente quando carregado
em compressão é chamada de maleabilidade. Os metais que podem ser martelados ou enrolados em folhas são maleáveis. A
maioria dos metais dúcteis também são
maleáveis, mas alguns metais muito maleáveis, como o
chumbo, não são muito dúcteis e não podem
ser transformados em fios facilmente. Metais
com baixa ductilidade, como chumbo, podem ser extrudados ou
empurrados para fora de uma matriz (processo de extrusão) para formar fios e outras formas. Alguns metais muito maleáveis são chumbo, estanho, ouro, prata, ferro e cobre.
Fragilidade
Um material que não se deforma plasticamente sob carga é considerado frágil. O trabalho a frio excessivo causa fragilidade e perda de ductilidade. O ferro fundido não se deforma plasticamente sob uma carga de ruptura e, portanto, é quebradiço.
Um 'entalhe' muito afiado que concentra a carga em uma pequena área também pode reduzir a plasticidade. Os entalhes são causas comuns de falha prematura em peças. Mordedura de solda, ressaltos agudos (abruptos) em eixos usinados e ângulos agudos
em forjados e fundidos são exemplos de entalhes indesejados
(potenciais elevadores de tensão).
Tenacidade ao entalhe
A
tenacidade ao entalhe (resistência ao impacto) é a
capacidade de um metal de resistir à ruptura da carga de impacto
quando há um entalhe ou aumento de tensão presente. Um
metal pode mostrar alta ductilidade ou resistência quando testado
à tração ou ser duro ou macio quando testado em
dureza, mas muitas vezes o comportamento dos metais sob cargas de
choque aparentemente não está relacionado a essas
propriedades. É
claro que, como regra, um metal frágil, como ferro fundido
cinzento, falhará sob baixas cargas de choque; ou
seja, sua resistência ao choque é baixa e o ferro forjado
macio ou aço macio tem uma alta resistência ao choque. Mas
os metais macios e de granulação grossa terão
menor resistência ao choque do que os metais de
granulação fina. Um
entalhe ou ranhura em uma peça diminuirá a
resistência ao choque de um metal, de modo que uma forma e
dimensão de entalhe específicas são usinadas no
corpo de prova para fornecer resultados uniformes.
Em geral, a resistência à tração de um metal muda em proporção à dureza. No
entanto, essa relação nem sempre é verdadeira em
altos níveis de dureza ou com materiais frágeis porque
esses materiais são mais sensíveis às
concentrações de tensões, ou entalhes, e podem
fraturar prematuramente quando tensionados.
Condutividade
A condutividade é uma medida da capacidade de um material de conduzir corrente elétrica. É o recíproco da resistividade.
A condutividade é comumente expressa em mhos por metro, já que a unidade de resistividade é o ohm. A
condutividade dos elementos metálicos varia inversamente com a
temperatura absoluta na faixa normal de temperaturas, mas em
temperaturas próximas do zero absoluto as
imperfeições e impurezas na estrutura de rede de um
material tornam a relação mais complicada. Metais e materiais exibem uma ampla faixa de condutividade. Entre
as substâncias mais condutoras (prata e cobre) e as mais
resistivas (poliestireno, por exemplo) a diferença é de
23 ordens de grandeza.
Materiais não metálicos
Cerâmica
A
cerâmica oferece propriedades únicas como materiais de
engenharia, notavelmente dureza excepcionalmente alta e
resistência à abrasão e corrosão, bem como
propriedades de alta temperatura consideravelmente superiores às
de qualquer metal. No
entanto, são menos dúcteis, intrinsecamente
frágeis e suscetíveis a choques térmicos que podem
limitar sua temperatura máxima de serviço em
aplicações que envolvam ciclagem térmica. A
resistência ao choque térmico depende diretamente de um
baixo coeficiente de expansão térmica e alta
condutividade térmica, cujas propriedades diferem sensivelmente
entre os diferentes materiais cerâmicos.
A
fabricação de cerâmicas não apresenta
problemas particulares, uma vez que podem ser formadas por
técnicas tradicionais, como prensagem úmida e
extrusão de moldagem por deslizamento; e
por métodos modernos como moldagem por injeção,
prensagem isostática, fundição de fita e prensagem
a seco.
As
cerâmicas que podem ser classificadas (ou são
utilizáveis ou potencialmente utilizáveis) como
materiais de engenharia abrangem atualmente:
- (i) alumina,
- (ii) berílio (óxido de berílio) e nitreto de boro,
- (iii) porcelana (silicatos de alumínio),
- (iv) esteatita e forsterita (silicatos de magnésio),
- (v) nitreto de silício e carbeto de silício, (vi) diboreto de titânio e
- (vii) carbono vítreo.
A
cerâmica está encontrando um uso crescente na
fabricação de componentes eletrônicos, componentes
de engenharia, medicina e odontologia e joalheria.
Ceramics are finding an increasing use in the fabrication of electronic components,
engineering components, medicine and dentistry and jewellery.
Cermets
(composto cerâmico-metalico)
O
uso de metais revestidos de cerâmica e combinações
cerâmica-metal assumiu agora proporções
significativas, particularmente nas áreas de física
nuclear prática (por exemplo, peças para reatores
nucleares) e fabricação de motores a jato. As
combinações metalocerâmicas são de dois
tipos: um revestimento cerâmico sobre o metal ou uma
combinação química e mecânica de metais e
cerâmicas em um material cermet. Ambos
são essencialmente tentativas de produzir materiais de alta
temperatura satisfatórios, seja com custos reduzidos e melhor
disponibilidade ou com um desempenho geral superior aos materiais
metálicos ou cerâmicos existentes isoladamente. De um modo geral, as propriedades mecânicas desses dois tipos de materiais representam extremos. Os
metais têm alta resistência à tração e
resistência ao choque, mas perdem essas propriedades rapidamente
com o aumento da temperatura. As
cerâmicas do tipo refratário têm pontos de
fusão extremamente altos e excelente estabilidade geral, mas
são de baixa resistência à tração e
resistência a choques mecânicos e térmicos. A
demanda por materiais que combinem as características
favoráveis dos metais e da cerâmica está
aumentando; daí o desenvolvimento de combinações de cerâmicas com metais ao longo dos últimos anos.
Normalmente os cermets são formados por técnicas semelhantes às empregadas na metalurgia do pó. O
conteúdo cerâmico geralmente compreende óxidos
refratários, carbonetos ou nitretos, enquanto o componente de
pó metálico é geralmente cromo, níquel,
molibdênio ou titânio. As propriedades resultantes são diferentes das de qualquer um dos constituintes separados. Vários cermets têm pontos de fusão particularmente altos, melhor alcançados em chama aberta.
Materiais Compósitos
Um
compósito é um material no qual um material mais forte,
às vezes fibroso, é geralmente combinado com outro para
reforçar ou fortalecer a massa resultante. As
necessidades da indústria aeroespacial levaram ao
desenvolvimento e aceitação de materiais
compósitos. Baixo peso, alta resistência e grande rigidez eram de interesse primordial da aviação militar. Essas mesmas qualidades também estão em demanda em muitas aplicações não militares. As formas mais comuns de compósitos são baseadas em uma matriz plástica. O material de reforço fibroso pode estar em forma de folha, como em laminados plásticos termofixos; forma de filamento, tecido ou aleatório, como em plásticos reforçados com vidro ou carbono; ou forma de fibra curta como em termoplásticos preenchidos ou reforçados. Esses materiais estão bem estabelecidos e amplamente disponíveis.
No
caso de compósitos laminados termofixos, fenólico,
melamina e epóxido são os principais sistemas de resinas utilizados, tendo papel, tecido de algodão, tecido de
vidro e amianto como principais materiais de reforço
alternativos.
Os
compósitos cerâmicos e metálicos permaneceram
relativamente pouco desenvolvidos como materiais gerais de engenharia e
construção, em grande parte devido ao alto custo. Existem,
no entanto, inúmeras aplicações de formas
metálicas 'preenchidas' e 'laminadas' que se qualificam como
compósitos sob a descrição geral.
Concreto
O
concreto é uma mistura de pedra e areia mantidas juntas por uma
pasta endurecida de cimento hidráulico e água. Quando
os ingredientes são bem misturados, eles formam uma massa
plástica que pode ser moldada em um tamanho e forma
predeterminados. Quando a pasta de cimento endurece, o concreto fica muito duro como uma rocha. Possui grande durabilidade e tem capacidade de suportar altas cargas principalmente em compressão.
A
resistência e as propriedades exigidas do concreto podem ser
obtidas pela seleção cuidadosa de seus ingredientes,
classificação correta dos ingredientes,
adições precisas de água e adoção de
um bom acabamento na mistura, transporte, colocação,
compactação, acabamento e cura do concreto na obra. .
Os
principais ingredientes do concreto são cimento, agregado
graúdo (ou seja, pedriscos, cascalho, etc.), agregado fino (ou
seja, areia), aditivos químicos (se necessário) e
materiais fibrosos (se necessário). Os agregados no concreto constituem de longe a maior parte da massa.
1.2.3 Descontinuidades e defeitos em materiais metálicos
(NT: Nesse assunto existe uma apresentação que pode ser acessada em https://1drv.ms/b/s!AvbIqQJ5umbcs0TTpuoXQERrNJpa)
Sempre
que há uma mudança na homogeneidade e uniformidade das
propriedades dentro de um material, isso pode invariavelmente ser
atribuído à presença de descontinuidades ou
imperfeições (falta de material) dentro do material. A
partir dos deslocamentos e irregularidades da estrutura atômica,
as descontinuidades podem assumir vários formatos e formas como
inclusões gasosas (microporosidade, porosidade,
bolhas, vazios alinhados, vazios concentrados), trincas, inclusões
metálicas, falta de penetração, falta de
fusão, retração, voltas e costuras, etc.
As descontinuidades podem ser divididas em três categorias gerais inerentes, processamento e serviço.
- (a) Descontinuidades inerentes são geralmente formadas quando o metal é fundido. Existem mais duas subclassificações. As
descontinuidades inerentes ao forjado referem-se à fusão e
solidificação do lingote original antes de ser formado em placas,
blocos e tarugos. As
descontinuidades inerentes a fusão-solidificação dos metais
referem-se à fusão, vazamento em moldes e solidificação de um artigo do
processo de fundição.
- (b)
As descontinuidades de processamento geralmente estão relacionadas aos
vários processos de fabricação, como usinagem, conformação, extrusão,
laminação, soldagem, tratamento térmico e galvanização. Durante
o processo de fabricação, muitas descontinuidades que estavam no
subsolo serão abertas para a superfície por usinagem, retificação, etc.
- (c) As descontinuidades de serviço estão relacionadas às diversas condições de serviço, como tensão, corrosão, fadiga e erosão. As
descontinuidades podem alterar a distribuição de tensões locais e, além
disso, podem afetar as propriedades mecânicas ou químicas (resistência
à corrosão).
As descontinuidades devem ser caracterizadas não apenas por sua natureza, mas também por sua forma. Descontinuidades
do tipo planar, como trincas, laminações, fusão
incompleta e penetração inadequada da junta, criam
sérios efeitos de intensificação (aumento) da tensão aplicada. Descontinuidades
tridimensionais quase não criam efeito de intensificação, mas
amplificam as tensões pela redução a área na qual a força está aplicada. Portanto,
as características das descontinuidades que devem sempre ser
consideradas incluem o tamanho, forma (volumétrica, lineares ou planares),
orientação em relação à
tensão de trabalho principal e tensão residual,
localização em relação às
superfícies externas e às seções
críticas da estrutura.
Todas as descontinuidades acima são descritas nos processos individuais nas Seções 1.3 e 1.4.
1.3. Processos de Fabricação e Descontinuidades
1.3.1 Processos primários e descontinuidades relacionadas
Lingote fundido e descontinuidades relacionadas
Um fundido adequado para trabalhar de fabricação posterior ou re-fundir é chamado de lingote. Os
moldes nos quais o metal fundido é derramado para formar
lingotes são feitos de ferro fundido cinzento, ferro fundido com
grandes veios de grafite ("meehanita") e ligas de alumínio anodizadas. A
superfície interna do molde é frequentemente revestida
com materiais adequados para ajudar a formar uma superfície lisa
do lingote. Um lingote ou tarugo é normalmente o ponto de partida para a formação real de artigos ou materiais. Descontinuidades típicas encontradas no lingote FIG. 1.15 são inclusões não metálicas, porosidade e vazios de contração. A
maioria dessas descontinuidades no lingote está na parte
superior e pode ser facilmente eliminada cortando o topo do lingote. O lingote depois que o topo quente é cortado é chamado de bloco fundido. Os blocos podem então ser processados para formar placas, chapas e perfis como mostrado na FIG. 1.16.
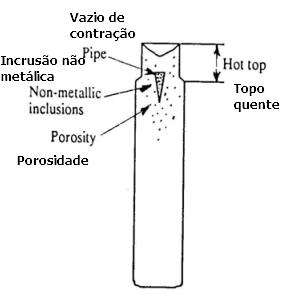
FIG. 1.15. Typical defects in an ingot.
Defeitos típicos em um lingote.
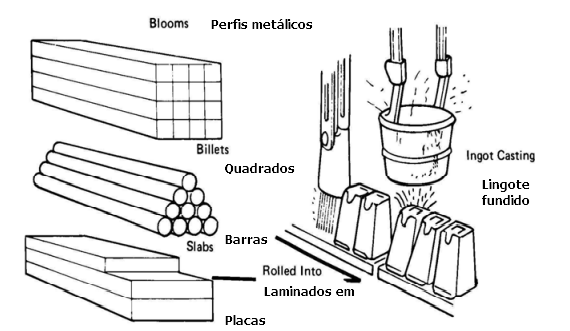
FIG. 1.16. Processos típicos de materiais primários.
Processos de fundição
Um
método comumente usado para formar objetos de metal de formas
complexas é vazar metal fundido em um molde no qual ele se
ajusta à forma necessária. O
molde é então quebrado para expor a peça fundida,
ou o projeto do molde é tal que pode ser separado (aberto) sem danos e
reutilizado. Os moldes
são geralmente formados a partir de formatos padrões que podem ser
usados várias vezes, se necessário, e seu projeto
é crítico, pois os orifícios de
'alimentação' e 'ventilação' devem ser
cuidadosamente posicionados no molde para permitir que o metal flua
livremente em todas as peças e que o ar previamente existente saia sem ficar aprisionado,FIG. 1.17. Os problemas que podem ocorrer são o aprisionamento no molde no resfriamento. Também
é improvável que a estrutura cristalina de uma
peça fundida seja ótima em todas as peças, de modo
que sua resistência pode ser menor do que com outros
métodos de fabricação. Vários
processos de fundição incluem fundição em
areia, fundição em molde permanente,
fundição sob pressão,
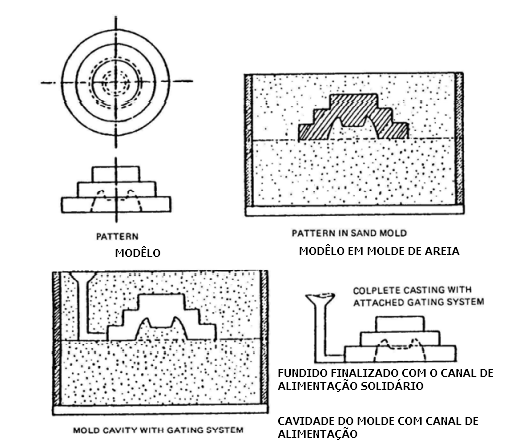
FIG. 1.17. Etapas típicas de fundição
Fundição em areia
Neste caso, um molde de areia é usado para moldar a forma desejada da liga necessária. Um
molde de areia pode ser definido como um recipiente de areia
pré-formado no qual o metal fundido é derramado e deixado
solidificar. Em geral, os moldes de areia são destruídos à medida que a peça fundida é removida deles. Moldes
de areia possibilitam moldar formas complexas que poderiam não ser
possíveis com outros processos convencionais de fabricação.
Diferentes tipos de moldes de areia podem ser existir para fazer diferentes peças fundidas. Os
moldes de areia natural são feitos de areia úmida e
são usados para praticamente todos os fundidos ferrosos e
não ferrosos. Eles
têm a desvantagem de não serem muito fortes, além
de exigirem umidade durante a fabricação, o que pode
causar certos defeitos na fundição. Os moldes de areia natural podem ser fornecidos com uma areia seca na superfície para formar superficies fundidas mais lisas. Moldes puramente de areia seca também podem ser feitos adicionando à areia um aglutinante em vez de umidade.
Os
métodos de preparação de moldes de areia incluem
moldagem de bancada, moldagem por máquina, moldagem de piso e
moldagem por poço. A moldagem de bancada é usada para pequenas peças fundidas. Este
é geralmente um processo lento e trabalhoso, uma vez que
geralmente é usado o amassamento manual com modelo solto.
Moldes
pequenos e médios podem ser feitos mesmo com o auxílio de
uma variedade de máquinas que geralmente são mais
rápidas e uniformes do que a moldagem de bancada. Os moldes de médio a grande porte são feitos diretamente no piso da fundição. Moldes muito grandes feitos em um poço construído para esse fim são chamados de moldes de poço.
As
areias mais comumente usadas em fundição de areia
contêm areia de sílica que geralmente é de 50 a 95%
do material total em qualquer areia de moldagem, zirconato e olivina,
etc. As propriedades e características mais importantes de tais
areias são permeabilidade, coesividade e refratariedade . A
permeabilidade é uma condição de porosidade e
está relacionada com a passagem de material gasoso
através da areia, bem como com a densidade dos grãos de
areia. A coesão
pode ser definida como a união dos grãos de areia ou a
resistência da areia de moldagem e depende do tamanho e da forma
dos grãos de areia.
A
propriedade de coesividade pode ser melhorada adicionando à
areia alguns ligantes como argila, resinas e gomas e óleo de
secagem. A
terceira característica importante da areia de moldagem é
a refratariedade, que é sua capacidade de resistir a altas
temperaturas sem se fundir. Areia
de sílica pura pode suportar uma temperatura tão alta
quanto 2000 oC. A propriedade de refratariedade pode ser afetada por
impurezas como óxidos metálicos.
As cavidades do molde podem ser produzidas envolvendo o material de moldagem em torno dos chamados moldes. Os moldes podem ser feitos de madeira, metal ou outros materiais adequados. Há uma variedade desses moldes usados na fabricação de peças fundidas. Outra
parte importante do processo de fundição é a caixa
do macho (que vai permitir a criação de espaços vazios no interior da
peça fundida pela não alimentação de metal liquido nesse espaço) que é
uma estrutura feita de madeira, metal ou outro
material adequado, contendo uma cavidade com a forma de um macho
desejado. Fazer um molde de areia envolve o empacotamento adequado de areia de moldagem em torno de um modelo. Depois
que o modelo é removido da areia e o arranjo de canal
é concluído, a cavidade do molde é preenchida com
metal fundido para formar a peça fundida.
Fundição de molde permanente
Uma
fundição feita por vazamento de metal fundido em um molde
feito de alguma liga metálica ou outro material de
permanência é conhecida como fundição de
molde permanente.
Ferro
fundido cinzento e erro fundido com
grandes veios de grafite ("meehanita") são
os materiais mais utilizados na construção de moldes
permanentes. Esse uso comum se deve em parte à facilidade com que podem ser usinados. Certos
aços, particularmente aços de liga especial que
são tratados termicamente, geralmente têm uma
resistência especialmente boa à erosão. Eles têm excelentes propriedades refratárias. Algumas
ligas de alumínio nas quais a superfície foi anodizada
também são usadas como materiais de moldagem. A anodização produz Al2O3 que é muito refratário e resistente à abrasão. Estas ligas são muito fáceis de usinar e possuem uma boa capacidade de resfriamento. O
molde não é destruído na remoção do
fundido e, portanto, pode ser reutilizado muitas vezes.
Fundição sob pressão
A
fundição pressurizada pode ser definida como o uso
de um molde permanente (matriz) no qual o metal fundido é
introduzido por meio de pressão. O termo fundição sob pressão é outro nome para este método de fundição. Esta
pressão é obtida pela aplicação de ar
comprimido ou por pistões operados pneumaticamente ou
hidraulicamente. Este
processo de fundição pode ser subdividido em dois tipos,
por exemplo (a) fundição sob pressão em
câmara quente e (b) fundição sob pressão em
câmara fria.
(a) Fundição em câmara quente.
A
unidade de fusão é parte integrante da máquina de
câmara quente, e o metal fundido é introduzido diretamente
desta unidade de fusão, por meio de mecanismo de êmbolo na
cavidade da matriz. O
processo é ainda caracterizado por uma quantidade normal de
superaquecimento no metal e a necessidade de uma pressão de
fundição proporcionalmente menor. A
pressão sobre o metal fundido em máquinas de
fundição sob pressão de câmara quente pode
variar de aproximadamente 500 a 6000 psi (3,5 a 41 MPa). Uma média de aproximadamente 2.000 a 2.500 psi (14 a 17 MPa) é comum. As pressões de injeção de ar são normalmente limitadas a cerca de 600 psi (4 MPa). A FIG. 1.18.
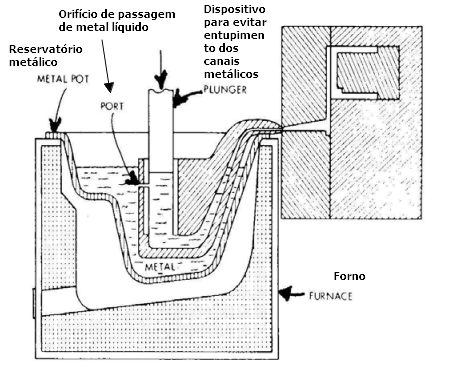
FIG. 1.18: Fundição de câmara quente.
(b) Fundição em câmara fria
A
unidade de fusão é geralmente separada neste caso, e o
metal fundido deve ser transferido para o mecanismo de
injeção por panela FIG. 1.19. Outras
características distintivas do processo são
pressões de metal muito altas e o fato de que a liga de
fundição pode estar a uma temperatura um pouco menor que
o superaquecimento normal; o fundido pode até estar em uma condição semifundida. A
pressão sobre o metal de fundição em
máquinas de fundição sob pressão de
câmara fria pode variar de 3.000 psi (20,5 MPa) até 25.000
psi (172 MPa) e, em alguns casos, pode chegar a 100.000 psi (690 MPa). As
ligas metálicas fundidas em estado semifundido requerem maior
pressão para compensar a fluidez reduzida resultante das baixas
temperaturas de vazamento. Temperaturas
de trabalho mais baixas e altas pressões produzem peças
fundidas de estrutura densa, livres de furos e porosidades relacionadas
a gases dissolvidos.

FIG. 1.19: Fundição em câmara fria.
Fundição centrífuga
Qualquer
processo no qual o metal fundido é vazado e solidificado
enquanto o molde está girando, é um processo de
fundição centrífuga. Os fundidos produzidos sob esta força centrífuga são chamados de fundidos centrífugados. Existem
três processos centrífugos reconhecidos, nomeadamente
fundição centrífuga verdadeira,
fundição semicentrífuga ou centrífuga
perfilada e fundição centrifugada ou sob pressão e
são mostradas na FIG. 1.20. A
verdadeira fundição centrífuga é aquela em
que as fundições são feitas em um molde
cilíndrico oco girado em torno de um eixo comum tanto à
fundição quanto ao molde. Tubo de ferro fundido é comumente feito por este método. Neste processo, o eixo de rotação pode ser horizontal, inclinado ou vertical. No verdadeiro processo de fundição centrífuga, a circunferência interna é sempre circular. Quando o molde é girado em um eixo horizontal, uma verdadeira superfície interna cilíndrica é produzida. A verdadeira fundição centrífuga é usada apenas em objetos de formato simétrico. A
fundição semicentrífuga ou centrífuga
perfilada é semelhante ao método centrífugo
verdadeiro, exceto que um núcleo central é usado para
formar a superfície ou superfícies internas. A fundição não depende da força centrífuga para sua forma. Um bom exemplo de trabalho semi-centrífugo é uma fundição em forma de roda. O eixo de rotação no processo semicentrífugo é sempre vertical. Embora
o rendimento seja melhor do que com a fundição
estática, não é tão alto quanto na
verdadeira fundição centrífuga. Com este processo também apenas objetos de forma simétrica podem ser moldados. exceto que um núcleo central é usado para formar a superfície ou superfícies internas. A fundição não depende da força centrífuga para sua forma. Um bom exemplo de trabalho semi-centrífugo é uma fundição em forma de roda. O eixo de rotação no processo semicentrífugo é sempre vertical. Embora
o rendimento seja melhor do que com a fundição
estática, não é tão alto quanto na
verdadeira fundição centrífuga. Com este processo também apenas objetos de forma simétrica podem ser moldados. exceto que um núcleo central é usado para formar a superfície ou superfícies internas. A fundição não depende da força centrífuga para sua forma. Um bom exemplo de trabalho semi-centrífugo é uma fundição em forma de roda. O eixo de rotação no processo semicentrífugo é sempre vertical. Embora
o rendimento seja melhor do que com a fundição
estática, não é tão alto quanto na
verdadeira fundição centrífuga. Com este processo também apenas objetos de forma simétrica podem ser moldados.
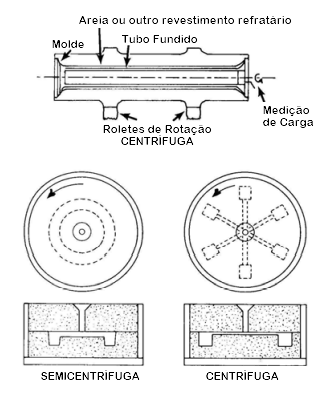
FIG. 1.20. Fundição centrífuga.
A
fundição centrifugada ou sob pressão é
aplicada para fundições não simétricas. A
cavidade do molde não é girada em torno de seu
próprio eixo, mas em torno do eixo de um canal central
descendente comum ao eixo de rotação, que alimenta o
metal na cavidade do molde sob força centrífuga. Este processo de centrifugação pode ser feito apenas em torno de um eixo vertical. A
força centrífuga fornece uma alta pressão para
forçar a liga metálica na cavidade do molde. Os
processos de fundição centrífuga podem ser usados
para produzir peças feitas de grupos de ligas ferrosas e
não ferrosas. Tubos
de ferro fundido, canos de armas, paredes de cilindros automotivos,
anéis de motores a jato, anéis de pistão e
tambores de freio são peças comuns fundidas por
centrifugação. As
vantagens incluem a eliminação de inclusões
estranhas (contaminantes) e a produção de peças fundidas mais
sólidas. As principais desvantagens são as limitações de forma e tamanho.
Fundição por microfusão
Este processo envolve a fabricação de um molde de
peça única a partir do qual o modelo é
removido por um procedimento que derrete o modelo. Os moldes utilizados neste processo são moldes de uso único. A eliminação de todos os planos de partição fornece tolerâncias dimensionais aprimoradas. Como
o modelo é removido por fusão ou queima, a
precisão da fundição é aumentada
através da eliminação de balaço, batidas
e deslocamentos para remoção de machos. Vários outros nomes são dados a este processo. Também
é chamado de fundição de precisão,
fundição de precisão ou processo de cera perdida e
é mostrado na FIG. 1.21.
Vários
tipos e graus de cera são os materiais comuns para a
fabricação de moldes para fundição por
microfusão. Certos plásticos que queimam sem resíduos também são usados como materiais de modelo. Algumas ligas metálicas de baixo ponto de fusão também podem ser usadas como materiais de modelo. Neste
processo de fundição, os padrões são
formados de novo, fundindo ou forjando o material do padrão em
matrizes feitas de metal, plástico, borracha ou madeira.
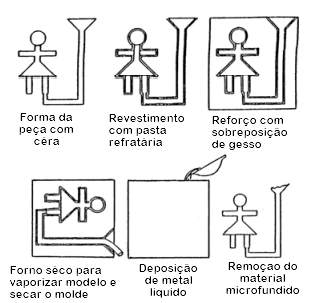
FIG. 1.21. Etapas para fundição por microfusão.
Os modelos são feitos primeiro de cera ou outros materiais
de modelo por fusão e depois injetados em uma matriz
metálica ou não metálica. Em
seguida, os moldes são soldados ou unidos aos canais de alimentação, que também são do mesmo material do
molde. Por esta união do modelo aos canais de alimentação, é preparado um modelo que se assemelha a uma
árvore. Esta "árvore" é agora mergulhada em areia refratária, colocada em um reservatório de metal e lacrada. Em
seguida, o revestimento ou material de moldagem, na forma de pasta
viscosa, é derramado ao redor do modelo e canais. Quando o revestimento endurece, o molde é aquecido colocando-o em um forno a 370 ºF. Por
este aquecimento o molde é seco e cozido e o molde é
derretido e o material fundido do molde é retirado do molde. Agora como um toque final no molde antes da fundição, o molde é colocado em um forno e é aquecido a uma temperatura de 980-1300 ºC. Isso remove todos os resíduos de cera, se houver, grudados no molde de revestimento. O molde é então aquecido até a temperatura de fundição.
Fundição de molde em casca
Este processo envolve a fabricação de um molde que tem
duas ou mais peças finas, semelhantes a conchas, consistindo de
areia termoendurecível ligada à resina. Essas
conchas são de uso único na aplicação e
são duras e facilmente manuseadas e armazenadas. As
cascas são feitas de modo que as peças correspondentes
se encaixem facilmente, presas com grampos ou adesivos e vazadas na
posição vertical ou horizontal. Esses
moldes podem ser apoiados em grelhas metálicas ou em uma massa de material volumoso
e permeável como areia, granalha de aço ou cascalho.
Modelos
metálicos são usados para a produção de
cascas, pois são submetidas a temperaturas de aquecimento
próximas a 810 ºC. O
modelo deve ter alguma provisão, na forma de pinos
ejetores, para a remoção de cascas da superfície
do padrão. Areia de sílica limpa e seca é o material a granel usado na fabricação de moldes de casca. O tamanho e a distribuição do grão podem variar com o uso. As resinas sintéticas termofixas são usadas como ligantes para areia. As resinas incluem os fenolformaldeídos, ureia formaldeídos e outros.
A
mistura de areia e resina ou areia revestida cai ou é soprada
contra um padrão de metal aquecido ou caixa. A temperatura do modelo varia de 350 a 590 ºC. O
contato da resina termofixa com o modelo quente causa uma pega
inicial e, assim, uma camada aderente de areia ligada é formada
em 5 a 20 segundos. O
padrão com esta camada aderente de areia colada é
colocado no forno e curado por aquecimento à temperatura
adequada por um a três minutos. O tempo de cura depende da espessura da casca e do tipo de resina. O
conjunto é então removido do forno e o invólucro
é retirado do modelo por dispositivos ejetores. Essa
decapagem às vezes é um problema e pode ser superada
usando um agente de separação de silício.
As
principais vantagens deste processo são que as peças
fundidas (casca) geralmente têm uma superfície lisa e,
portanto, reduzem os custos de usinagem. Essas
técnicas são facilmente adaptáveis à
produção em massa usando equipamentos automáticos.
As
desvantagens podem ser o custo inicial dos modelos de metal, o
custo mais alto dos aglutinantes de resina e uma
limitação geral de tamanho.
Fundição contínua
Embora
apenas uma pequena tonelagem de peças fundidas seja produzida
por fundição contínua, é possível
produzir formas bidimensionais em uma barra alongada por
extração de metal solidificado de um molde resfriado a
água. Como mostrado esquematicamente na FIG. 1.22. Metal fundido entra em uma extremidade do molde e o metal sólido é extraído da outra. O
controle da temperatura do molde e da velocidade de
trefilação é essencial para resultados
satisfatórios. A
exclusão do contato com o oxigênio, enquanto fundido e
durante a solidificação, produz metal de alta qualidade. Engrenagens
e outras formas em tamanhos pequenos podem ser moldadas em forma de
barra e depois cortadas em várias partes.
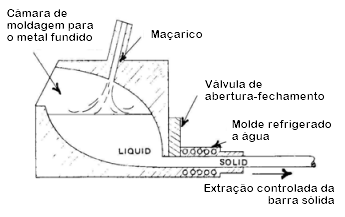
FIG. 1.22. Diagrama esquemático do processo de lingotamento contínuo.
TABELA 1.2. COMPARAÇÃO DE MÉTODOS DE FUNDIÇÃO (APROXIMADO)
|
Fundição em areia
|
Fundição de molde permanente
|
Fundição
|
Fundição centrífuga
|
Fundição de investimento
|
Fundição de molde de concha
|
Custo relativo em grande quantidade
|
Médio
|
Baixo
|
Mais baixo
|
Alto
|
Altíssima
|
Médio
|
Custo relativo para número pequeno
|
Mais baixo
|
Alto
|
Altíssima
|
Médio
|
Baixo
|
Baixo
|
Peso admissível de fundição
|
Ilimitado
|
45 kg
|
136 kg
|
Várias toneladas
|
2,3 kg
|
Limitado
|
Calcinável de seção mais fina (mm)
|
3,25
|
3,25
|
1
|
12,5
|
0,25
|
3,25
|
Tolerância dimensional típica (mm)
|
1,6
|
0,75
|
0,25
|
1,6
|
0,25
|
0,25
|
Acabamento da superfície relativa
|
Pobre
|
Bom
|
Melhor
|
Razoável
|
Muito bom
|
Bom
|
Propriedades mecânicas relativas
|
Razoável
|
Bom
|
Muito bom
|
Melhor
|
Razoável
|
Bom
|
Relativa facilidade de fundição de projetos complexos
|
Razoável
|
Razoável
|
Bom
|
Pobre
|
Melhor
|
Razoável
|
Relativa facilidade de mudança de design na produção
|
Melhor
|
Pobre
|
O mais pobre
|
Bom
|
Bom
|
Bom
|
Gama de ligas que podem ser fundidas
|
Ilimitado
|
Base de cobre e menor ponto de fusão preferível
|
Base de alumínio e menor ponto de fusão preferível
|
Ilimitado
|
Ilimitado
|
Ilimitado
|
Defeitos de fundição
Existem, em geral, três grandes categorias de defeitos de fundição. Primeiro
são os defeitos maiores ou mais graves que resultam em raspagem
ou rejeição da peça fundida. A
segunda categoria é a de defeitos intermediários que
permitem a recuperação da peça fundida
através de reparos necessários. Os defeitos da terceira categoria são os menores que podem ser facilmente reparados. A
eliminação e controle de defeitos de
fundição é um problema que o engenheiro de
fundição pode abordar de várias maneiras.
O procedimento comum é confiar em técnicas de salvamento que parecem proporcionar economias imediatas. Procedimentos
corretivos nas áreas de moldagem, fabricação de
núcleos, fusão ou vazamento da fundição
são frequentemente negligenciados, mas são altamente
desejáveis serem controlados para evitar defeitos. Alguns dos defeitos que normalmente ocorrem nas peças fundidas são apresentados a seguir:
Porosidade ("pinholes")
Os
orifícios de gás são orifícios
esféricos de tamanhos variados, com paredes brilhantes,
geralmente distribuídos de maneira bastante uniforme e formados
por gás no metal. Os furos maiores tendem a ser encontrados na seção mais pesada (ou seja, a última a solidificar). Se
o metal estiver correto antes da fundição, o tipo de
porosidade do tipo "pinhole" (pequenos poros agrupados) é provavelmente devido à
absorção de hidrogênio do vapor no molde. O
gás no metal fundido é removido por uma técnica de
remoção de gás e mantendo as cascas e moldes de
fundição secos.
Bolhas
("blowholes")
As
bolhas são encontradas principalmente em três formas:
- i)
Cavidades alongadas com paredes lisas, encontradas sobre ou logo abaixo
da superfície da parte superior de uma peça fundida. Estes
são causados pelo ar aprisionado e a repetição
pode ser evitada ventilando o molde e aumentando sua permeabilidade.
- ii)
Cavidades de forma arredondada com paredes lisas e brilhantes
são causadas por gases do molde ou do núcleo, juntamente
com permeabilidade insuficiente ou ventilação. Eles
podem ser evitados usando menos aglutinante de óleo no molde e
garantindo que os núcleos estejam secos e devidamente cozidos e
que a areia seja misturada adequadamente.
- iii)
Pequenas cavidades imediatamente abaixo da 'pele' da superfície
de fundição são formadas pela reação
do metal fundido com a umidade da areia de moldagem. Isso
pode ser evitado reduzindo o teor de voláteis nos núcleos
do molde e no revestimento do molde, garantindo que o metal seja
desoxidado,
Vazios Alongados ("piping")
Quando este termo é usado na fundição, refere-se
aos defeitos de inclusão de gás encontrados em canais de subida de metais ou
dentro da própria fundição.
Inclusões
("inclusions")
São
descontinuidades do material formadas pela inclusão de
óxidos, escórias e escórias em uma peça
fundida. Eles
são devidos ao descuido no vazamento, ou ao uso de uma concha
suja, e à turbulência devido a métodos
impróprios de passagem ao fundir ligas, como alumínio e
bronze, que estão sujeitas à formação de
película de óxido na superfície. O
fechamento defeituoso dos moldes pode causar esboroamento e
pedaços soltos de areia sendo incorporados na
fundição. A
ocorrência de inclusões pode ser evitada pelo uso adequado
dos equipamentos e prática de fundição.
Esponjosidade
("sponginess")
Defeito
que ocorre durante os primeiros estágios de
solidificação de uma peça fundida e tem a
aparência, como o nome indica, de uma esponja; pode ser local ou geral em extensão. A
principal causa é a falha em obter a solidificação
direcional do fundido em direção aos centros de calor
desejados, como canais de subida e entradas; temperatura
de vazamento insuficientemente alta e colocação de
entradas adjacentes a seções pesadas.
Contração ("shrinkage")
É
um defeito de fundição que ocorre durante os
estágios intermediários e posteriores da
solidificação do metal fundido. Tem
uma formação ramificada, é facilmente
distinguível da esponjosa e é uma forma de vazio. A FIG. 1.23. O
defeito pode ser evitado prestando atenção especial
à direção de solidificação e
garantindo canais de subida adequados, ou outros auxiliares de
alimentação, nas seções mais pesadas de uma
peça fundida. A
modificação do projeto de fundição, ou
seja, tornar as seções fundidas mais uniformes para o
fluxo e solidificação do metal é útil para
evitar a contração. Moldes
e machos são por vezes feitos demasiado fortes e resistem muito
à contração do metal fundido e, desta forma,
causarão uma quebra na homogeneidade do metal.
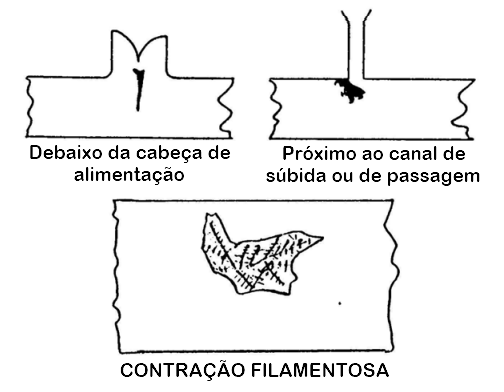
FIG. 1.23. Formação de defeitos de retração.
Trincas de fundição ("hot tears")
São
descontinuidades que resultam de tensões desenvolvidas
próximas à temperatura de solidificação
enquanto o metal ainda está fraco. Estes,
novamente, são atribuídos à resistência do
molde e do macho, que dificultam a contração do fundido,
causando estresse térmico. Trincas de fundição são trincas irregulares. Eles
podem ser evitados tornando os machos e moldes mais
desmontáveis (maleáveis), evitando mudanças bruscas de
seção e prevenindo a formação de pontos
quentes intensos, projetando com seções mais uniformes
FIG. 1,24.
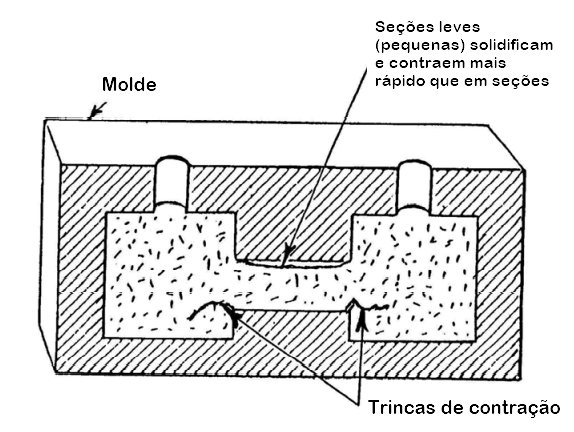
FIG. 1.24. Trincas de contração.
Trinca ("crack")
Bem definidos e normalmente retos, elas são formados após o metal se tornar completamente sólido. São
necessárias tensões bastante grandes para causar fratura,
e as paredes de tais trincas são descoloridas de acordo com a
temperatura da peça fundida quando as trincas se formaram. O
projeto de fundição ruim, juntamente com a
restrição de contração pelo molde,
núcleo ou barras de caixa, contribuem para a formação e trincas, e
evitá-las, juntamente com a flexibilização do
molde ou núcleos o mais rápido possível
após a solidificação, ajudará a evitar o
acúmulo de tensões .
Gota fria ("cold shuts")
Estas
são descontinuidades (uma forma de falta de fusão)
causadas pela falha de uma corrente de metal fundido em unir-se com
outra corrente de metal, ou com uma seção de metal
sólido, como um chapelim, Fig. 1,25. Eles são lineares na aparência, talvez com um efeito de ondulação nas extremidades. Uma gota a frio é causado pela fluidez do metal sendo muito
baixa (ou seja, superfícies muito frias) ou talvez por
métodos insatisfatórios de alimentação do
metal fundido. Os
fechamentos a frio geralmente podem ser evitados aumentando a
temperatura de vazamento ou a taxa de vazamento ou ambas e revisando a
posição, tamanho e número de entradas e os
arranjos para ventilação do molde.
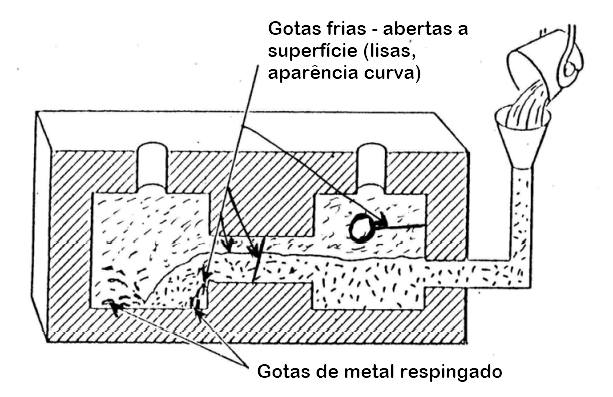
FIG. 1.25.Tipos de gotas fria.
Chapelim não fundido ("Unfused chaplet")
Um
chapelim é frequentemente usado para apoiar uma
seção de um molde ou um núcleo dentro de um molde
e quando o metal fundido é derramado, os chapelins devem se
fundir na fundição. Quando não fundido, o chapelim causará uma descontinuidade na fundição. O projeto do chapelim e o tipo de chapelim devem ser revistos para superar esse defeito.
Núcleo mal posicionado
("Misplaced core")
Uma irregularidade na espessura da parede, por exemplo, uma parede mais
espessa que a outra, pode ser detectada por uma radiografia na
técnica de parede dupla. Isso
é causado por desalinhamento do núcleo, retirada e
fechamento descuidados do molde ou manuseio brusco após o
fechamento do molde.
Segregação
A
segregação é uma condição resultante
da concentração local de qualquer um dos constituintes de
uma liga. A
segregação pode ser geral estendendo-se por uma parte
considerável de uma peça fundida, local quando apenas os
vazios de contração ou gotas quentes são total ou
parcialmente preenchidos com um constituinte de baixo ponto de
fusão ou 'segregado' que está principalmente associado a
fundições centrífugas, mas também pode
ocasionalmente ocorrem em fundidos estáticos.
Processos de metalurgia do pó
A
definição do termo metalurgia do pó é a
arte de produzir pós metálicos e objetos moldados a
partir de pós metálicos individuais, misturados ou
ligados, com ou sem a inclusão de componentes não
metálicos, por prensagem ou moldagem de objetos que podem ser
simultaneamente ou posteriormente aquecido para produzir uma massa
coerente, quer sem fusão, quer apenas com a fusão de um
constituinte de baixo ponto de fusão». FIG. 1.26
mostra as etapas normalmente requeridas na produção de
uma peça pelo processo de metalurgia do pó. O pó adequado deve primeiro ser produzido. Embora
teoricamente qualquer material cristalino possa ser fabricado por
metalurgia do pó, a produção de pó adequado
tem apresentado restrições em muitos casos, seja pela
dificuldade de obtenção de pureza adequada ou por
razões econômicas. Após
a seleção e mistura do pó e
fabricação de uma matriz para a forma a ser produzida, o
pó é prensado no tamanho e na forma. A aplicação de calor resulta no crescimento cristalino e na produção de um corpo homogêneo.
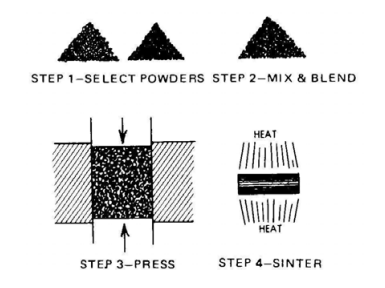
FIG. 1.26. Elementos de metalurgia do pó.
Mistura e combinação
A mistura é necessária mesmo para um único
pó metálico para promover a homogeneidade com uma
dispersão aleatória de tamanhos e formas de
partículas. A
mistura e combinação é ainda mais importante para
junções de materiais que dependem de uma liga
uniforme para desenvolver propriedades finais. Pequenas
quantidades de materiais orgânicos podem ser adicionadas para
reduzir a segregação, e outros materiais, tanto
orgânicos quanto inorgânicos, podem ser adicionados para
atuar como lubrificantes durante a prensagem ou algumas vezes no
produto final.
Compactação (Pressing)
A
compactação de pós metálicos idealmente
seria feita aplicando pressão em todas as direções
ao mesmo tempo. Isso
geralmente é impraticável para uso comercial, e a maior
parte da compactação é feita ao longo de um
único eixo. Às
vezes, a pressão é aplicada apenas em uma
direção, mas em outros casos são usados
movimentos opostos para reduzir o efeito do atrito da parede lateral.
A
eficácia da prensagem é mais frequentemente avaliada
medindo a densidade do material e expressando-a como uma porcentagem da
densidade teórica para o metal sólido do tipo que
está sendo tratado. As densidades dependem do tamanho e forma das partículas, do material, da pressão, do tempo e da temperatura. O
problema da variação de densidade é ainda mais
complicado por formas que não são cilindros simples.
Sinterização
O termo sinterização é usado para identificar o
mecanismo pelo qual as partículas sólidas são
unidas pela aplicação de pressão ou calor, ou
ambos. Em
seu sentido mais amplo, o processo inclui procedimentos como soldagem,
brasagem, solda fria, queima de cerâmica e união de lascas
ou grânulos plásticos. Cada
um dos procedimentos, exceto os que envolvem metal em forma de
pó, são suficientemente importantes e de uso tão
amplo que desenvolveram sua própria linguagem e tecnologia. A
sinterização pode ser realizada à temperatura
ambiente apenas com pressão, mas na maioria das vezes é
realizada em temperatura elevada, ao mesmo tempo ou após a
aplicação da pressão. Os dois procedimentos de sinterização mais comuns são:
- (1) aplicação conjunta de calor e pressão, denominada prensagem a quente; e
- (2) aplicação de calor após as partículas terem sido compactadas, por prensagem a frio. Na
prensagem a quente, a plasticidade das partículas é
maior, e elas recristalizam mais facilmente e, assim, permitem que
altas densidades sejam alcançadas com pressões mais
baixas do que seriam necessárias em temperaturas mais baixas. As
peças prensadas a frio que são posteriormente
sinterizadas podem ser aquecidas de maneira convencional, sendo
colocadas em fornos comuns ou banhos de sal.
Deformação
Devido às variações de densidade e outros fatores,
a contração dos produtos da metalurgia do pó
durante a sinterização é difícil de
controlar. Peças que exigem tolerâncias estreitas quase sempre devem ser finalizadas por algum tratamento dimensional. O
trabalho a frio pode ser usado para pequenas alterações
de dimensões, mas este procedimento é limitado pela falta
de ductilidade comum aos produtos de metalurgia do pó. A compressão, às vezes chamada de cunhagem, melhora a densidade, resistência e ductilidade do material. Mesmo
com esse processo, raramente essas propriedades são iguais
às de um material similar produzido por fusão. A
maior parte do trabalho de deformação comercial é
feito por trabalho a quente ou por trabalho a frio com
interrupções frequentes para
recristalização.
Tratamento térmico
Os
produtos da metalurgia do pó podem ser tratados termicamente da
mesma forma que outros materiais de composição
química semelhante, mas os tratamentos geralmente não
são tão eficazes quanto para os metais produzidos por
fusão, principalmente devido à estrutura porosa que
restringe a condutividade térmica. Muitos
dos vazios nos produtos de metalurgia do pó são pontos de
concentração de tensão que não apenas
limitam as cargas de serviço, mas também aumentam as
tensões decorrentes de gradientes térmicos durante o
tratamento térmico. Os
tratamentos incluem resinterização para
estabilização e homogeneidade, recozimento para maciez,
refinamento de grão para maior ductilidade e endurecimento para
maior resistência ao desgaste.
Usinagem
A
usinabilidade de materiais sinterizados geralmente é baixa, mas
a usinagem às vezes é necessária para fornecer
controle final de dimensões ou para estabelecer formas que
não são práticas para o processo de metalurgia do
pó. Em
alguns tipos de produtos, como os carbonetos cementados, a
retificação é o processo de acabamento comum tanto
para controlar tamanho e forma quanto, em muitos casos, para eliminar a
superfície produzida no processo de sinterização. Impregnação, uma importante etapa de acabamento é a impregnação. Materiais
inorgânicos, como óleos ou ceras, podem ser impregnados em
produtos metálicos porosos para fins de
lubrificação. Um
tipo de produto totalmente diferente pode ser produzido pela
impregnação de metais de alta temperatura de fusão
com metais de baixa temperatura de fusão. O principal uso desta técnica é na produção de aços cementados.
Aplicações de produtos de metalurgia do pó
A metalurgia do pó ocupa duas áreas bastante distintas. É
um método básico de produção de forma para
praticamente todos os metais, em competição direta com
outros métodos. Além
disso, para muitos materiais refratários, tanto metálicos
quanto não metálicos, a metalurgia do pó é
o único meio prático de produção de formas.
O tungstênio é típico dos metais refratários; tem
um ponto de fusão de 3400 oC, e não existem moldes ou
materiais de cadinho satisfatórios para o uso de técnicas
convencionais de fundição a esta temperatura. Tântalo e molibdênio são semelhantes.
Os
carbonetos cementados formam um dos grupos mais importantes de
materiais que podem ser fabricados em formas sólidas apenas pela
metalurgia do pó. O
maior uso é para ferramentas de corte e pontas ou pastilhas de
ferramentas de corte, mas os carbonetos cementados também
são usados para pequenas matrizes e algumas
aplicações onde a resistência ao desgaste é
importante. O principal
material usado é o carboneto de tungstênio, embora o
carboneto de titânio e o carboneto de tântalo também
sejam usados. Algumas
ferramentas de corte de produção muito úteis
são fabricadas usando materiais fortes e resistentes como
núcleo e impregnando a superfície com carboneto de
titânio ou outro material duro e resistente ao desgaste.
Uma
outra área em que a metalurgia do pó produz produtos
não práticos por outros meios é a
fabricação de materiais com baixa densidade controlada. Um dos primeiros produtos de metalurgia do pó produzidos em massa foram os rolamentos de bronze poroso sinterizado. Após
prensagem a frio, sinterização e calibragem, os mancais
são impregnados com óleo, que em serviço é
disponibilizado para lubrificação. Embora
não sejam verdadeiros rolamentos de filme fluido, eles
proporcionam um longo serviço com baixa
manutenção. Materiais porosos também são úteis como filtros.
Os materiais elétricos compostos formam um grupo semelhante aos carbonetos cementados. Tungstênio
e outros metais refratários em combinação com
prata, níquel, grafite ou cobre encontram amplas
aplicações como contatos elétricos e escovas de
comutadores; a
metalurgia do pó não apenas fornece um meio para produzir
a combinação, mas também fornece a forma acabada
das peças. Muitos
dos materiais magnéticos permanentes atualmente usados
também são produzidos pela metalurgia do pó.
1.3.2 Processos de fabricação e defeitos relacionados
Processos de soldagem
A
soldagem pode ser definida como o método metalúrgico de
união, aplicado ao problema geral de construção e
fabricação. Consiste
em unir duas peças de metal estabelecendo uma
ligação metalúrgica átomo a átomo,
diferente de uma junta mantida por atrito ou intertravamento
mecânico. Esta
ligação metalúrgica átomo a átomo
é alcançada pela aplicação de calor e,
às vezes, pressão.
Muitos
processos de soldagem requerem a aplicação de calor ou
pressão, ou ambos, para produzir uma ligação
adequada entre as peças que estão sendo unidas. A
física da soldagem lida com os complexos fenômenos
físicos associados à soldagem, incluindo calor,
eletricidade, magnetismo, luz e som. Ao
fazer uma junta, duas partes da mesma composição
química podem ser soldadas juntas sem adição de
metal para realizar a junta. Isso pode ser denominado como soldagem autógena. Pode
ser adicionado um metal com a mesma composição das partes
a serem unidas, caso em que o processo seria classificado sob a
designação geral de soldagem
«autógena». Finalmente,
uma liga bastante diferente daquela de que as peças são
feitas pode ser usada ou, alternativamente, as próprias
peças podem diferir significativamente em
composição. Então esse processo é chamado de soldagem dissimilar. Quase todas as fontes de calor de alta densidade de energia imagináveis foram usadas uma vez ou outra na soldagem. Fontes
de calor aplicadas externamente de importância incluem arcos elétricos,
feixes de elétrons, feixes de luz (lasers),
reações exotérmicas (gás
oxicombustível e termite) e resistência elétrica. Os
processos de soldagem que adquirem calor de fontes externas geralmente
são identificados com o tipo de fonte de calor empregada. Os
processos de soldagem que são comumente usados para soldagem
de metais são descritos e suas características são
discutidas nas seções a seguir.
Tipos e posições de soldagem
As cargas em uma estrutura soldada são transferidas de um membro
para outro através de soldas colocadas nas juntas. Os tipos de juntas usadas na construção soldada e as soldas aplicáveis são mostradas na FIG. 1,27.
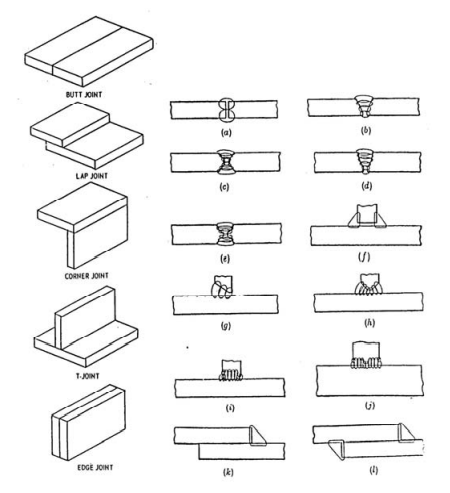
FIG. 1.27. Tipos
de juntas soldadas:
(a) junta plana com chanfro reto;
(b) junta plana com chanfro v
simples;
(c) junta plana com chanfro duplo v;
(d) junta plana com chanfro simples u;
(e)
junta plana com chanfro duplo u;
(f) junta em ângulo reto ou t com chanfro reto (solda de filete, sem penetração);
(g) junta em ângulo reto ou t com chanfro ou bisel
simples (solda com penetração);
(h) junta em ângulo reto ou t com chanfro ou bisel duplo (solda com penetração);
(i) junta em ângulo reto ou t com chanfro reto (solda com penetração realizada por apenas um dos lados); (j) junta em ângulo reto ou t com chanfro reto (solda com penetração realizada pelos dois lados);
(k)
junta sobreposta com cordão simples;
(l)
junta sobreposta com cordão duplo.
Todas
as soldas encontradas na construção real, exceto as
soldas com chanfros em tubos, são classificadas como planas,
horizontais, verticais ou sobrecabeças.. As
soldas com chanfros em tubos são classificadas como horizontais com
rotação do tubo, fixas horizontais, verticais, ou fixas inclinadas. Essas posições são ilustradas nas FIGs 1.28 e 1.29 e explicadas abaixo:
- Posição plana (1G). As
placas de a serem soldadas são colocadas em um plano aproximadamente
horizontal e o metal de solda depositado do lado superior FIG. 1,28 (A).
- Posição horizontal (2G). As
placas a serem soldadas são colocadas em um plano aproximadamente
vertical com o chanfro de soda aproximadamente horizontal. FIG. 1,28 (B).
- Posição vertical (3G). As
placas a serem soldadas são colocadas em um plano aproximadamente
vertical com o chanfro de solda aproximadamente vertical. FIG. 1,28 (C).
- Posição sobrecabeça (4G). As
placas a serem soldadas são colocadas em um plano aproximadamente
horizontal e o metal de solda depositado pela parte inferior da FIG. 1,28 (D).
- Horizontal com rotação (1G). O
tubo é colocado com o seu eixo num plano aproximadamente
horizontal com o chanfro de solda num plano aproximadamente
vertical e o tubo é "rolado" durante a soldagem A FIG. 1,28 (A).
- Vertical (2G). O
tubo é colocado com o seu eixo numa posição
aproximadamente vertical com o chanfro de solda num plano
aproximadamente horizontal FIG. 1,28 (B).
- Fixo horizontal (5G). O
tubo é colocado com seu eixo em um plano aproximadamente
horizontal com o chanfro de solda em um plano aproximadamente
vertical e o tubo não deve ser "rolado" ou girado durante a
soldagem. A FIG. 1,28 (E)
- Inclinado fixo (6G). O tubo é fixo inclinado (45o ±5o) e não gira durante a soldagem FIG. 1,28 (F).
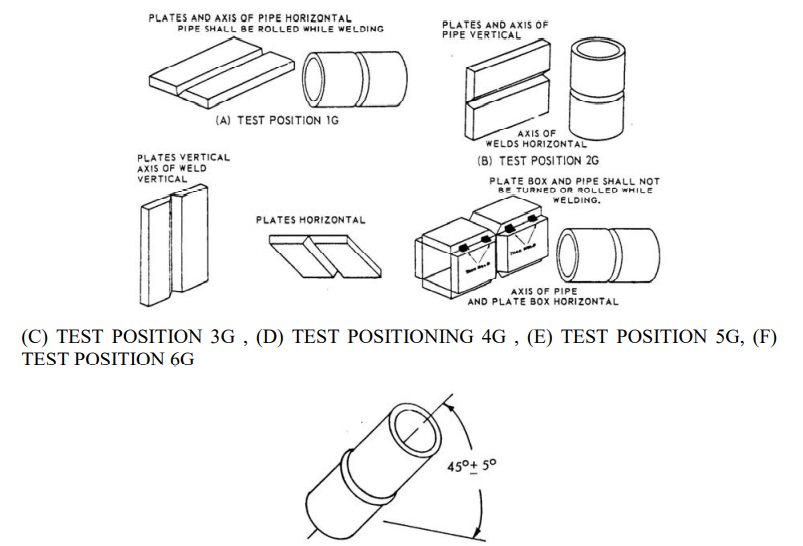
FIG. 1.28. Positions of plates and pipes for groove weld.
Posições de placas e tubos para solda de ranhura.
Para soldas de filete em chapas, as diferentes posições são definidas conforme abaixo:
- Posição plana (1F). As
placas a serem soldadas são colocadas de modo que cada filete de solda
seja depositado com seu eixo aproximadamente horizontal e sua garganta
aproximadamente vertical. 1,29 (A).
- Posição horizontal (2F). As
placas a serem soldadas são colocadas de modo que cada cordão de
solda seja depositado no lado superior da superfície horizontal
e contra a superfície vertical FIG. 1,29 (B).
- Posição vertical (3F). Cada solda de filete é feita verticalmente FIG. 1,29 (C).
- Posição
sobrecabeça (4F). As placas a serem soldadas são posicionadas de forma
que cada filete de solda seja depositado na parte inferior da
superfície horizondal e contra a superfície vertical FIG. 1.29 (D).
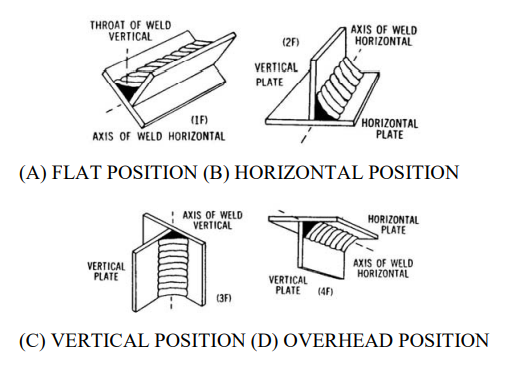
FIG. 1.29. Posições de placas para soldas de filete.
Soldagem por eletrodo revestido (Shielded metal arc welding = SMAW)
A soldagem por eletrodo revestido é o primeiro processo de soldagem por arco elétrico. É
um dos processos simples e versáteis para soldagem de metais
ferrosos e para diversos metais não ferrosos. Basicamente,
é um processo de soldagem manual no qual o calor para soldagem
é gerado por um arco estabelecido entre um eletrodo
consumível revestido com fluxo de soldagem e a peça. A
ponta do eletrodo, poça soldada, arco e áreas adjacentes
da peça no ponto de soldagem são protegidas da
contaminação atmosférica por um isolamento (proteção) gasoso(a)
obtida da combustão e decomposição do revestimento
de fluxo. O processo é ilustrado na FIG. 1,30.
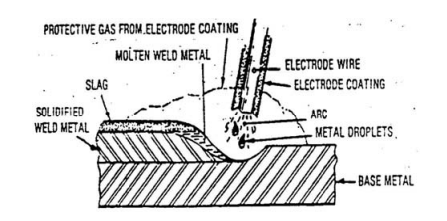
FIG. 1.30. Processo de soldagem a arco com eletrodo revestido.
Os
eletrodos revestidos são produzidos em uma variedade de
diâmetros normalmente variando de 1/16 a 5/16 pol. (2 a 8 mm). Os
diâmetros menores são usados com baixas correntes para
unir seções finas e para soldagem em todas as
posições. Os
grandes diâmetros são projetados para conduzir altas
correntes para obter maiores taxas de deposição nas
posições plana e horizontal. Composições
de ligas especiais de metal de adição podem ser
formuladas com relativa facilidade pelo uso de pós
metálicos no revestimento do eletrodo.
O processo SMAW (abreviação em inglês) tem várias vantagens. Usando
o processo, as oficinas podem lidar com muitas aplicações
de soldagem com uma variedade relativamente pequena de eletrodos. Outras vantagens são a simplicidade e leveza do equipamento, e seu custo relativamente baixo. Além disso, as soldas podem ser feitas em locais confinados ou distantes de fontes de alimentação de altas voltagens.
Soldagem por arco submerso (SAW=Submerged Arc Welding)
Na
soldagem a arco submerso o arco e o metal fundido são protegidos
por um envelope de fluxo fundido e uma camada de partículas de
fluxo granular não fundidas como mostrado na FIG. 1.31. Quando
o arco é aberto, a ponta do eletrodo alimentado continuamente
é submersa no fluxo e, portanto, o arco não é
visível. A solda é feita sem a radiação luminosa intensa que caracteriza um processo de arco aberto, e com poucos fumos. O
processo SAW, sigla em inglês, é usado em operações automáticas e
semiautomáticas, embora o primeiro seja muito mais comum. Altas
correntes de soldagem podem ser empregadas para produzir altas taxas de
deposição de metal com economias de custo substanciais. As soldas só podem ser feitas nas posições plana e horizontal.
O processo é mais amplamente empregado para soldagem de todos os tipos de aços carbono, baixa liga e ligas. O
aço inoxidável e algumas ligas de níquel
também são efetivamente soldados ou usados como metais
de adição para criação de revestimentos superfíciais. Várias
combinações de metal de adição-fluxo podem
ser selecionadas para fornecer propriedades específicas do metal
de solda para o serviço pretendido. O
fluxo pode conter ingredientes que, quando fundidos, reagem para
contribuir com adições de liga ao metal de solda.
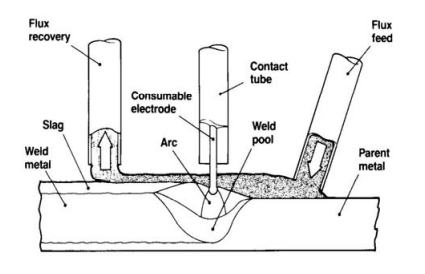
FIG. 1.31. Processo de soldagem a arco submerso.
Solda
a Arco com Gas Ativo/Inerte (MAG/MIG) e Solda a Arco com Fluxo Interno
(em inglês Gas Metal Arc Welding=GMAW & Flux Cored Arc
Welding=FCAW)
A
soldagem a arco com gás ativo/inerte (MAG/MIG = GMAW) e a soldagem a
arco com fluxo interno (FCAW) são dois processos distintos, mas possuem
muitas semelhanças na aplicação e no equipamento. Ambos
os processos usam um arame sólido contínuo ou eletrodo
tubular para fornecer metal de adição, e ambos usam
gás para proteger o arco e o metal de solda. No
MIG/MAG (GMAW), o eletrodo é sólido, e todo o gás de
proteção é argônio, hélio, CO2 ou
misturas desses gases, fornecido por uma fonte externa, conforme
mostrado na FIG. 1.32.
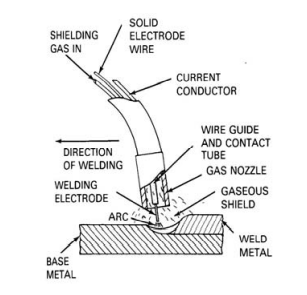
FIG. 1.32. Gas metal arc welding process.
Processo de soldagem a arco de metal a gás.
O
processo original de arco com proteção gasosa consiste em uma
operação contínua exigindo altas densidades de
corrente para obter uma transferência suave de metal fundido.
O
processo permite a soldagem com respingos mínimos,
penetração uniforme e boa capacidade fora de
posição. Com
arame tubular (FCAW), o eletrodo é tubular e contém ingredientes
essenciais que podem fornecer parte ou todo o gás de
proteção necessário. Este
processo também pode utilizar gás de
proteção auxiliar, dependendo do tipo de eletrodo
empregado, do material a ser soldado e da natureza da soldagem
envolvida. FCAW é ilustrado na FIG. 1,33.
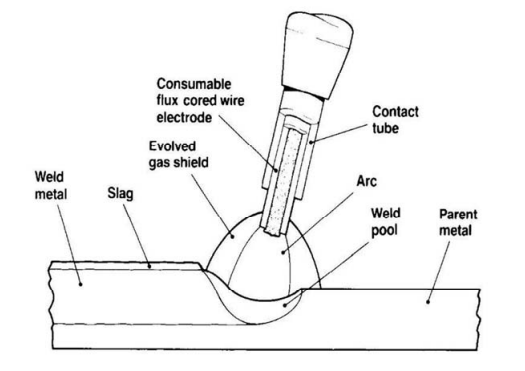
FIG. 1.33. Soldagem a arco com arame tubular (Flux cored arc welding).
A
soldagem a arco com arame tubular usa fluxo no espaço interno dos
eletrodos tubulares em vez de eletrodos sólidos, como o arco submerso,
para unir metais
ferrosos. O
núcleo de fluxo pode conter minerais, ferroligas e materiais que
fornecem gases de proteção, desoxidantes e materiais
formadores de escória. As
adições ao núcleo promovem a estabilidade do arco,
melhoram as propriedades mecânicas do metal de solda e melhoram o
contorno da solda. Muitos eletrodos com núcleo são projetados para serem usados com proteção externa adicional. Os gases ricos em dióxido de carbono são os mais comuns. O
metal de solda pode ser depositado em taxas mais altas, e as soldas
podem ser mais espessas e com melhor acabamento do que aquelas feitas com
eletrodos sólidos, independentemente do gás de
proteção.
Soldagem ao arco elétrico com eletrodo de tungstênio (TIG=Tungsten Inert Gas & GTAW=Gas Tungsten Arc Welding)
A
soldagem ao arco elétrico com eletrodo de tungstênio e atmosfera protetora gasosa, como o próprio nome diz emprega eletrodo de
tungstênio não consumível que deve ser isolado com
um gás inerte. O
arco é iniciado entre a ponta do eletrodo usado para fundir
o metal a ser soldado, assim como o metal de adição,
quando utilizado. Um
escudo de gás protege o eletrodo e a poça de fusão
derretida e fornece as características de arco
necessárias. Este processo é ilustrado na FIG. 1.34 e às vezes também é chamado de soldagem TIG.
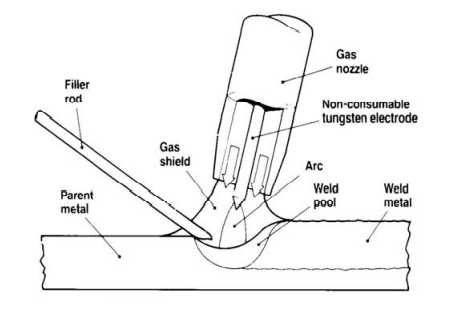
FIG. 1.34. Soldagem a arco com gás tungstênio.
Vários tipos de
eletrodos de tungstênio são usados com este
processo. Eletrodos
toriados e zircônios têm melhores
características de
emissão de elétrons do que o tungstênio
puro,
tornando-os mais adequados para operações em
corrente
contínua. O tório (Th)
é levemente radioativo com meia-vida longa e emite
principalmente partículas alfa (α).
O
óxido de tório (thoria) é, portanto,
um material
radioativo de baixo nível que pode dar origem a um pequeno
risco
de radiação externa e um risco interno por
ingestão ou inalação. Quase não
há liberação de material radioativo
durante o arco. No
entanto, para obter a máxima estabilidade do arco, a ponta
do
eletrodo é retificada em um formato cônico antes do
uso. Durante
o processo de soldagem, podem ser produzidas partículas de
tungstênio com tório na superfície. As partículas finas que podem ser produzidas propciam o perigo, pois podem ser inaladas, e o tório pode
liberar partículas alfa. No
entanto, o risco de câncer em soldadores TIG devido
à
exposição à torio é muito
baixo, uma vez
que os tempos de exposição aos
indivíduos
são invariavelmente pequenos. Recomenda-se
que os eletrodos toriados sejam armazenados em caixas de
aço,
claramente identificadas com o simbolo de radiação.
Quando
armazenado em caixas fechadas, não
há risco significativo no manuseio e armazenamento. Pequenos
números (fornecimento de 1 dia) de eletrodos podem ser
manuseados por soldadores com segurança sem quaisquer
precauções especiais. Geralmente
não há restrições
regulatórias sobre
o descarte de eletrodos toriados usados por meios convencionais. No
entanto, se grandes descartes forem previstos, valeria a pena ter
algumas discussões preliminares com o operador local do
aterro e
o órgão regulador em questão.
Soldagem eletroescória ("Electro-slag welding " - ESW)
A soldagem por
eletroescória é uma
adaptação especializada da soldagem a arco
submerso e
é usada para unir materiais espessos na
posição
vertical. Este
processo é ilustrado na FIG. 1,35. Estritamente
falando, não é um processo de soldagem a arco,
porque na
verdade depende da resistividade elétrica de um banho de
fluxo
fundido para produzir o calor necessário para derreter o
material de enchimento e o metal base.
O
processo é, no entanto, iniciado por um arco, que aquece uma
camada de fluxo de soldagem granular contido dentro de sapatas ou placas de moldagem refrigeradas a água e as bordas da
junta,
transformando-a em um banho de escória fundida. O
arco é então extinto e a escória
condutora mantida
em estado fundido por sua resistência à corrente
elétrica que passa de um eletrodo consumível para
a
peça. A
principal
aplicação da soldagem por
eletroescória é a
soldagem de chapas grossas de aço forjado e grandes
peças
fundidas de aço na fabricação de bases
de
máquinas e na indústria de aço
estrutural.
Suas principais
características são:
- (i) Taxas de
deposição de metal extremamente altas,
- (ii) Capacidade de soldar
materiais muito espessos em uma passagem,
- (iii)
Preparação mínima da junta e
requisitos de ajuste,
- (iv) Pouca ou nenhuma
distorção e
- (v) Baixo consumo de fluxo.
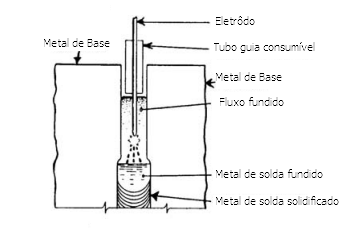
FIG. 1.35. Processo de soldagem por
eletroescória.
Soldagem por Pinos (SAW = Stud
Arc Welding)
Na
soldagem de pinos, basicamente um processo de soldagem a arco, o arco
de soldagem é gerado entre um pino de metal ou
peça
similar e a parte à qual ele é finalmente fundido
pelo
calor de soldagem assim gerado. FIG. 1.36. De
certa forma é também uma
variação do
processo ao arco elétrico com atmosfera protetora de metal , o pino representando o eletrodo. Mas apenas a extremidade do
eletrodo é derretida e se torna parte permanente da montagem
final. Em
operação, o pino é retido em uma
pistola manual ou
montada em bancada e é posicionado sobre o local onde deve
ser
fixado. Após
a
iniciação, a corrente flui através do
pino, que,
ao mesmo tempo, é levemente levantado, criando um arco. Após
um período de arco muito curto, o pino é
mergulhado na
poça fundida criada na placa de base e a pistola
é
retirada.
As
aplicações típicas de soldagem de
pinos incluem a
fixação de revestimentos especiais em tanques,
tubos de
caldeiras, montagem de painéis elétricos,
fixação de linhas hidráulicas,
hidráulicas
e elétricas em edifícios, veículos e
grandes
eletrodomésticos, e fixação de
pés e
alças em grandes eletrodomésticos.
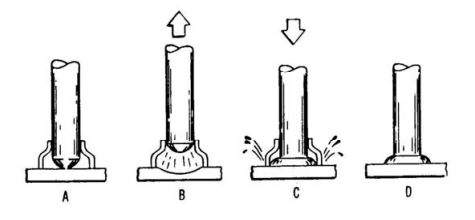
FIG. 1.36. Sequência de
soldagem de pinos.
Soldagem a arco de plasma
(PAW = Plasma arc welding )
O processo de soldagem a
arco de plasma fornece uma fonte de calor
muito estável para soldar a maioria dos metais de 0,02 a 6 mm. Este
processo tem vantagens sobre outros processos de soldagem a arco
aberto, como SMAW (eletrodo revestido), GMAW (MIG e MAG) e GTAW (TIG), porque possui maior
concentração de energia, melhor estabilidade do
arco,
maior teor de calor e maiores velocidades de soldagem. Como resultado, o PAW tem
maior capacidade de penetração do que SMAW, GMAW
e GTAW.
Os elementos
básicos da tocha de arco de plasma, ilustrados na FIG. 1.37, são o
eletrodo de tungstênio e o orifício de gás. Um pequeno fluxo de
argônio é fornecido através do
orifício para formar o plasma de arco. A proteção do arco e da zona de solda é fornecida pelo fluxo
de
gás através do bico externo
circundante da tocha. O
gás de proteção pode ser
argônio,
hélio ou misturas de argônio com
hidrogênio ou
hélio. O plasma é
iniciado por um arco piloto interno de baixa corrente entre o eletrodo
e o orifício. O arco piloto ioniza o
gás do orifício para acender o arco
primário entre o eletrodo e o metal base. O plasma de arco
é limitado em tamanho pelo orifício ao redor do
eletrodo e é chamado de arco transferido. Se for usado metal de
adição, ele é alimentado no arco como
no processo GTAW (TIG).
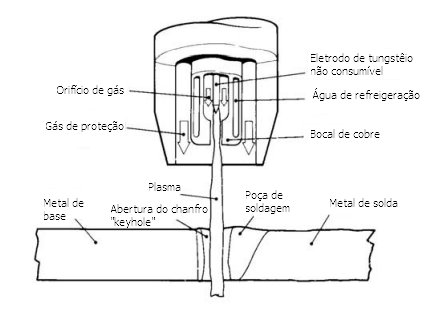
FIG. 1.37. Soldagem a plasma.
Soldagem por resistência elétrica (Resistance
welding = RW)
A
soldagem por resistência incorpora um grupo de processos em
que o
calor para soldagem é gerado pela resistência ao
fluxo de
corrente elétrica através das peças
que
estão sendo unidas. É mais comumente
usado para soldar duas chapas ou chapas sobrepostas que podem ter
espessuras diferentes. Um par de eletrodos conduz
corrente elétrica para a junta. A resistência a passagem de corrente aquece as superfícies das peças que serão unidas,
formando uma solda. Esses
eletrodos são presos as chapas sob pressão para fornecer um bom
contato elétrico e conter o metal fundido na junta. As
superfícies das juntas devem estar limpas para obter
resistência de contato elétrica consistente para
obter
tamanho e solidez uniformes da solda. As
principais variáveis do processo são a corrente
de
soldagem, o tempo de soldagem, a força do eletrodo e o
material
e o projeto do eletrodo. Altas
correntes de soldagem são necessárias para
produzir o
calor e derreter o metal base em um tempo muito curto. O
tempo para fazer uma única resistência aquecer e
derreter
o metal base é muito curto, geralmente menos de um segundo.
Existem
quatro processos principais de soldagem por resistência, a
saber,
soldagem por pontos (Resistence Spot Welding = RSW), soldagem por projeção
(Resistence Projection Welding = RPW),
soldagem por flash (Resistence Flash Welding = RFW) e soldagem por costura (Resistence Seam Electric Welding = RSEW). Esses processos
são ilustrados na FIG. 1,38. No RSW, a corrente de
soldagem é concentrada no ponto de união por meio
de eletrodos cilíndricos. As soldas a ponto
geralmente são feitas uma de cada vez. No RPW, uma
projeção ou reentrancia (sulco) é formada em uma
parte antes da soldagem. A
projeção concentra a corrente nas
superfícies opostas. Eletrodos
grandes e planos são usados em ambos os lados dos
componentes
para produzir várias soldas simultaneamente. Como
exemplo, um suporte estampado pode ter três ou quatro
projeções formadas nele para que possa ser
soldado a uma
chapa com um ciclo de soldagem. Na soldagem por costura, eletrodos
em forma de rolos são usados para transmitir
pressão e
enviar corrente através da folha sobreposta que
está
sendo movida entre eles. A soldagem por flash
geralmente é um processo automático. As
peças são fixadas por um operador de soldagem que
simplesmente pressiona um botão para iniciar a
sequência
de soldagem. A
solda flash usual une hastes ou barras de ponta a ponta ou de ponta a
ponta. A
ação de flash continua até que uma
camada fundida se forme em ambas as superfícies. Em seguida, os componentes
são forçados juntos rapidamente para espremer o
metal fundido. Isso
produz uma junta trabalhada a quente livre de metal de solda. As propriedades
mecânicas das soldas flash são muitas vezes
superiores a outros tipos de soldas. A solda flash usual une
hastes ou barras de ponta a ponta ou de ponta a ponta. A
ação de flash continua até que uma
camada fundida se forme em ambas as superfícies. Em seguida, os componentes
são forçados juntos rapidamente para espremer o
metal fundido. Isso
produz uma junta trabalhada a quente livre de metal de solda. As propriedades
mecânicas das soldas flash são muitas vezes
superiores a outros tipos de soldas. A solda flash usual une
hastes ou barras de extremidade a extremidade ou de aresta a aresta. A
ação de flash continua até que uma
camada fundida se forme em ambas as superfícies. Em seguida, os componentes
são forçados juntos rapidamente para espremer o
metal fundido. Isso
produz uma junta trabalhada a quente livre de metal de solda. As propriedades
mecânicas das soldas flash são muitas vezes
superiores a outros tipos de soldas.
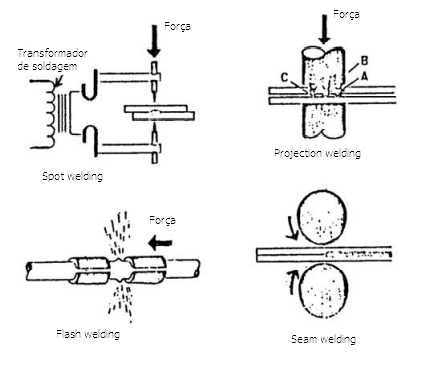
FIG. 1.38. Métodos
básicos de soldagem por resistência.
Soldagem a gás
oxiacetilênica (OFW = Oxyfuel gas welding)
A soldagem a gás
oxiacetilênica inclui um grupo de processos de
soldagem que usam o calor produzido por uma chama ou várias chamas de
gás para fundir o metal de base e, se usado, o metal de
adição. Soldagem
a gás oxiacetilênica é um termo inclusivo usado para
descrever
qualquer processo de soldagem que usa um gás
combustível
combinado com oxigênio para produzir uma chama com energia
suficiente para derreter o metal base. O
gás combustível e o oxigênio
são misturados
em proporções adequadas em uma câmara
que
geralmente faz parte do conjunto da tocha de soldagem. A
tocha é projetada para dar ao soldador controle completo da
chama de soldagem para derreter o metal base e o metal de
adição na junta. Este processo é
ilustrado na FIG. 1.39.
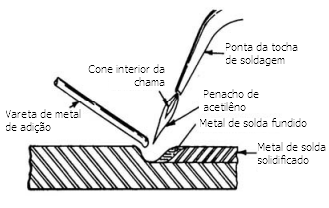
FIG. 1.39. Processo de soldagem a
gás oxiacetilênica.
A soldagem a gás
oxiacetilênica é normalmente feita com gás
combustível acetileno. Outros
gases combustíveis, como os provenientes de metil
acetileno e
hidrogênio, às vezes são usados para
soldagem a
gás oxiacetilênica de metais de baixo ponto de fusão. A chama de soldagem deve
fornecer alta energia localizada para produzir e sustentar uma
poça de fusão derretida. Com
o ajuste adequado, as chamas também podem fornecer uma
atmosfera
redutora protetora sobre a poça de fusão
derretida.
A
soldagem a gás oxiacetilênica pode ser usada para unir chapas
grossas,
mas a soldagem é lenta e é necessária
uma alta
entrada de calor. A
velocidade de soldagem é adequada para produzir soldas
econômicas em chapas metálicas e
tubulações
de paredes finas e de pequeno diâmetro. Assim, o OFW é
melhor aplicado em materiais com espessura máxima de
aproximadamente 6 mm.
Processo de brazagem
A brasagem
é um processo de união de metais
onde o metal base é aquecido a uma temperatura de cerca de
425oC. Metais
de adição não ferrosos, como
latão ou ligas
de prata, são fundidos pelo calor do metal base e fluem por
atração capilar entre as superfícies
bem ajustadas
da junta. O
calor para
brasagem é geralmente aplicado por maçaricos,
fornos,
indução elétrica,
resistência
elétrica ou colocando o trabalho em um banho de sais quentes. O
enchimento e o fluxo são aplicados manualmente ou
substituídos na forma de pó, anéis
metálicos ou tiras.
Processos de soldagem
diversos
Existem vários
outros processos de soldagem menos conhecidos e usados. Alguns dos mais importantes
desses processos são brevemente discutidos abaixo:
Solda por feixe de elétrons e a laser (Electron beam
and laser welding)
Esses métodos
são geralmente utilizados para montagens de
precisão que exigem soldas de alta qualidade. O
procedimento é realizado focando um feixe de
elétrons ou
feixe de laser na interface da junta e causando o derretimento e
a fusão do metal. As
soldas por feixe de elétrons exigem que o ajuste dos componentes a serem soldados
seja bem preciso, pois não há metal de
adição. A
junta de solda é criada pela fusão do material
penetrado
pela fonte de calor, portanto, a superfície de contato deve ser
preparada
geometricamente para que fiquem em contato íntimo em toda a
superfície da junta. As
soldas por feixe de elétrons geralmente são
feitas no
vácuo, enquanto a soldagem a laser é conduzida
usando um
gás inerte ao redor do feixe de laser. Atualmente,
o feixe de elétrons tem a capacidade de soldar corpos de
prova
mais espessos (até 200 mm em aço), mas
é limitado
pelo tamanho da câmara de vácuo.
Os
dispositivos utilizam um intenso feixe de elétrons para
aquecer
e derreter os metais básicos a serem soldados e qualquer
metal
de adição. O calor vem da
absorção dos elétrons no metal. Como
os elétrons podem ser interrompidos por qualquer
matéria,
incluindo o ar, o processo de soldagem é quase sempre
realizado
em uma câmara de vácuo. Os raios X são
gerados quando os elétrons acelerados atingem um material. A
energia máxima dos raios x produzidos será
determinada
pela voltagem utilizada para acelerar os elétrons e os
metais
envolvidos. Assumindo
paredes de câmara de aço de 1,5 ~ 2 cm de
espessura, a
taxa de exposição calculada fora do dispositivo
seria de
0,1 a 1 mR/h. As
medições reais feitas em torno dos equipamentos da soldagem por feixe de elétrons geralmente não excedem 0,05 a 0,1 mR/h
na
superfície da câmara.
Soldagem por
fricção ("Friction Welding", sigla do inglês = FW)
Na
soldagem por fricção, o calor para
coalescência
é produzido pela conversão direta de energia
mecânica em energia térmica na interface da junta.
A
energia mecânica é gerada pela
ação de
deslizamento entre superfícies rotativas ou por atrito. O
processo básico envolve manter uma peça de
trabalho
não rotativa em contato com uma peça de trabalho
rotativa
sob pressão constante ou gradualmente crescente
até que a
interface atinja a temperatura de soldagem. A
rotação é então
interrompida. É
um processo de estado sólido no qual a
coalescência ocorre
a uma temperatura abaixo do ponto de fusão dos metais que
estão sendo unidos. Muitas
ligas ferrosas e não ferrosas podem ser soldadas por
fricção, e o método pode ser usado
para unir
metais de propriedades térmicas e mecânicas
amplamente
diferentes.
Soldagem
ultrassônica (Ultrasonic welding [USW]
A
soldagem ultrassônica é uma forma de soldagem por
fricção que tem sido usada há muito
tempo para
unir plásticos. Recentemente,
essa vibração de alta frequência tem
sido aplicada
com sucesso na soldagem de metais, principalmente metais não
ferrosos. É
conhecido como um processo de ligação a frio,
porque a
combinação atômica e a
difusão ocorrem
enquanto os materiais estão em um estado
semi-sólido ou
sólido. Embora
ocorra algum aquecimento, a soldagem depende mais da
ação
de limpeza do processo do que do aquecimento do material.
Na
prática, as peças a serem soldadas são
presas sob
pressão entre uma bigorna e uma ponta conectada a um transdutor acústico
que vibra em alta frequência. A ponta de soldagem e a
bigorna podem ser confornadas de acordo com a geometria das
peças a serem soldadas. A parte em contato direto
com a ponta é esfregada em alta frequência contra
a parte estacionária. Esta
ação vibratória primeiro
corrói
óxidos e outros contaminantes nas superfícies de
interface. Uma
vez limpas, as superfícies entram em contato
íntimo e ocorre a ligação em estado
sólido. A soldagem
ultrassônica é mais adequada para unir
peças pequenas, chapas e folhas. O
processo é rápido, não requer
consumíveis
e, devido ao seu baixo calor, o resultado do processamento elimina a
necessidade de limpeza adicional. Em
alguns casos, mesmo superfícies revestidas, pintadas e muito
enferrujadas podem ser efetivamente unidas sem
preparação
da superfície.
Defeitos e descontinuidades de solda
Durante o
processo de soldagem podem ocorrer descontinuidades de
vários tipos. Estes podem ser
classificados pelo procedimento e processo de soldagem,
projeto do componente mecânico soldado e pelo comportamento metalúrgico dos materiais soldados. Os
grupos devem ser aplicados livremente porque as descontinuidades
listadas em cada grupo podem ter origens secundárias em
outros
grupos. As
descontinuidades relacionadas ao processo, procedimento e projeto
são, em sua maioria, aquelas que alteram as
tensões em
uma solda ou zona afetada pelo calor. As
descontinuidades metalúrgicas também podem
alterar a
distribuição de tensão local e,
além disso,
podem afetar as propriedades mecânicas ou químicas
(resistência à corrosão) da solda e da
zona afetada
pelo calor.
Porosidade (Porosity)
O
metal de solda fundido tem uma capacidade considerável de
dissolver os gases que entram em contato com ele, como
hidrogênio, oxigênio e nitrogênio. À medida que o
metal esfria, sua capacidade de reter os gases diminui. Por
exemplo, no aço, o oxigênio reage com o carbono
para
formar monóxido de carbono, que é liberado como
um
gás. Com
a
mudança do estado líquido para o
sólido, há
redução da solubilidade com a queda da
temperatura. Isso
faz com que um volume de gás não seja liberado no
momento
em que o metal está se tornando duro e, portanto, incapaz de
permitir que o gás escape livremente. O aprisionamento do
gás causa bolsões de gás e porosidade
na solda final. O
tipo de porosidade dentro de uma solda é geralmente
designado pela quantidade e distribuição dos
poros. Alguns
dos tipos são classificados da seguinte forma: FIG. 1.40.
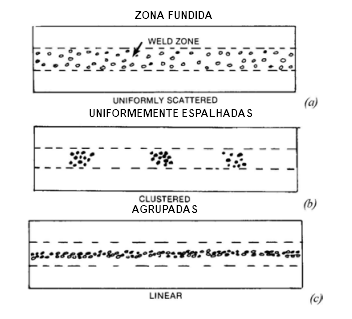
FIG. 1.40 Três tipos de porosidade de solda (a) Porosidade
uniformemente
espalhada (b) Porosidade agrupada (c) Porosidade linear.
Porosidade Linear ou Vermiforme (Pipe or wormholes inclusions)
Alguns aprisionamentos de gás têm uma forma alongada
conhecida como lineares ou vermiformes. Geralmente são
quase perpendiculares à superfície de solda. Eles podem resultar do uso
de fluxo em pó com umidade ou de corrente de soldagem
inadequada. Outra
forma típica de tubo tem a aparência de um galho
de uma árvore (ramificadas), FIG. 1,41. Estes podem ser causados
pelo uso de eletrodos de soldagem úmidos.
As causas comuns da
porosidade e os métodos sugeridos para preveni-la
estão resumidos na Tabela 1.3.
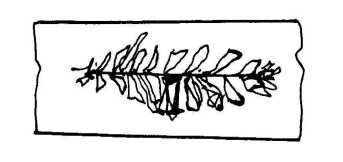
FIG. 1.41: Porosidade Linear ou Vermiforme em solda.
TABELA 1.3. CAUSAS COMUNS E
REMÉDIOS PARA POROSIDADE
Causas | Remédios | Excesso de hidrogênio, nitrogênio ou oxigênio na atmosfera de soldagem | Use processo de soldagem com baixo teor de hidrogênio, metais de adição com alto teor de desoxidantes; aumentar o fluxo de gás de proteção | Alta taxa de solidificação | Use pré-aquecimento ou aumente o calor de soldagem ("heat input") aplicado
| Metal de base sujo | Limpe as faces das juntas e superfícies adjacentes | Fio de enchimento sujo | Use arame de enchimento especialmente limpo e embalado e armazene-o em área limpa | Comprimento de arco inadequado, corrente de soldagem ou manipulação de eletrodos | Alterar as condições e técnicas de soldagem | Volatilização do zinco do latão | Use metal de enchimento de cobre-silício; reduzir o calor da soldagem | Aço galvanizado | Use eletrodos E6010 e manipule o calor do arco para volatilizar o zinco antes da poça de fusão derretida | Excesso de umidade na cobertura do eletrodo ou nas superfícies das juntas | Use os procedimentos recomendados para aquecer os eletrodos armazenados eletrodos. Pré-aqueça o metal base | Metal base com alto teor de enxofre | Use eletrodos com reações básicas de escória |
Inclusões não metálicas
As inclusões não metálicas podem ser resultado da contaminação do metal de
solda por
substâncias indesejadas na superfície da junta ou pela
atmosfera. Mas
a fonte usual é a escória formada pelo
revestimento do eletrodo ou fluxo utilizado no processo de soldagem. Alguma
escória pode ficar presa no metal depositado durante sua
solidificação, particularmente se o metal
não
permanecer fundido por um período suficiente para permitir
que a
escória suba até sua superfície. Na
soldagem multipasses, a limpeza insuficiente entre os passes de solda
pode deixar uma parte do revestimento de escória no local
para
ser coberta pelos passes subsequentes. Uma
característica particular das inclusões de
escória
é a linha de escória, intermitente ou
contínua. Tais
linhas de escória são frequentemente acompanhadas
por uma
pronunciada falta de fusão com o metal base. Em
geral, as inclusões podem ser devido a qualquer um dos
vários motivos que incluem falha na limpeza da
superfície
da junta, falha na remoção de escória
de um
depósito anterior, preparação
incorreta do chanfro,
manipulação incorreta do eletrodo e atmosfera de proteção
insuficiente do arco. As causas e
soluções comuns das descontinuidades do tipo
inclusão são mostradas na Tabela 1.4.
TABELA 1.4. CAUSAS COMUNS E REMÉDIOS PARA
INCLUSÃO DE ESCÓRIA
Causas |
Remédios |
Falha na
remoção de escória |
Limpe a
superfície e o cordão de solda anterior |
Aprisionamento de
óxidos refratários |
Escova elétrica no cordão de solda anterior |
Projeto de junta inadequado |
Aumente o ângulo
do sulco da junta |
Inclusões de
óxido |
Fornecer
proteção de gás adequada |
Acúmulo excessivo de escória antes da soldagem |
Reposicione o trabalho para
evitar a perda de controle de escória |
Técnica de
manipulação de eletrodos ruim |
Mude o eletrodo ou fluxo
para melhorar o controle de escória |
Pedaços presos
de revestimento de eletrodo |
Use eletrodos
não danificados |
Inclusões de
tungstênio
As inclusões de tungstênio
são partículas de tungstênio
metálico aprisionadas no metal de solda que se originam do
eletrodo
de tungstênio usado na soldagem a arco com eletrodo de
tungstênio. As
causas são corrente de soldagem excessiva permitindo a
fusão e deposição de
tungstênio na solda e
polaridade incorreta do eletrodo usando uma fonte CC. As
inclusões de tungstênio também podem
ser causadas
pela imersão do eletrodo no metal de solda fundido ou pelo
toque
do arame de metal de adição para o enchimento do chanfro no eletrodo durante a soldagem. Inclusões de
tungstênio ocorrem frequentemente no início das
soldas quando o eletrodo pode estar frio. Pequenas
inclusões globulares e amplamente espalhadas de
tungstênio
às vezes são permitidas, mas inclusões
de arestas
afiadas são perigosas.
Falta de fusão (Lack of fusion)
Ocorrem devido à falta de união em uma solda
entre o
metal de solda e o metal de base ou entre o metal de base e outro metal de
base ou entre o metal de solda e outro metal de solda. Consequentemente,
a falta de fusão pode ser de três tipos: falta de
fusão lateral, falta de fusão de raiz e falta de
fusão entre passes. O
defeito resulta principalmente da presença de
escórias,
óxidos, incrustações ou outras
substâncias
não metálicas, corrente de soldagem muito baixa
ou
preparação incorreta do chanfro. A
fusão incompleta também pode surgir de uma
corrente de
soldagem muito alta quando a alta taxa de fusão incentiva o
soldador a usar uma velocidade de soldagem excessiva. O
defeito reduz consideravelmente a resistência de uma junta
submetida a carga estática, e sob carga cíclica
ou de
choque é bastante grave. As causas e
soluções para a fusão incompleta
estão resumidas na Tabela 1.5.
TABELA 1.5. CAUSAS COMUNS E RECURSOS DE
FUSÃO INCOMPLETA
Causas |
Remédios |
Fonte de calor insuficiente, tipo ou tamanho incorreto de eletrodo, projeto
de junta inadequado ou proteção de gás
inadequada |
Siga a
especificação correta do procedimento de soldagem |
Posição
incorreta do eletrodo |
Mantenha a
posição correta do eletrodo |
Metal de solda posicionado
à frente do arco elétrico
|
Reposicione o trabalho,
reduza a corrente ou aumente a velocidade de deslocamento da solda |
Óxidos presos ou
escória no cordão de solda ou na face da solda |
Limpe a
superfície de solda antes de soldar |
Penetração incompleta na raiz (Incomplete root penetration
Na soldagem de topo, uma
abertura de raiz geralmente é deixada
na parte inferior da junta (na soldagem apenas por um lado) ou no centro da
solda (na soldagem pelos dois lados). Se
a abertura entre as duas placas soldadas for estreita, é
difícil
conseguir penetração e fusão completas
na raiz da
solda. Portanto,
pode
haver uma falta de fusão na raiz da solda ou uma lacuna
deixada
pela falha do metal de solda em preencher a raiz de uma solda de topo
FIG. 1.42.
É
causado pelo eletrodo posicionado em um ângulo incorreto, um
eletrodo muito grande em diâmetro, uma velocidade de
deslocamento
muito rápida, uma corrente de soldagem insuficiente ou uma
preparação inadequada da junta (por exemplo,
desalinhamento da junta).
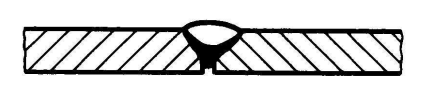
FIG. 1.42. Penetração
incompleta da raiz.
Trincas (Cracks)
As trincas são
rupturas lineares (2D) ou planas (3D) do metal sob tensão. Embora
às vezes largas, muitas vezes são
separações muito estreitas na solda ou no metal
base
adjacente. As
trincas
podem ocorrer em uma ampla variedade de formas e tipos e podem estar
localizadas em várias posições dentro
e ao redor
de uma junta soldada. Fig 1.43. As
trincas associadas à soldagem podem ser categorizadas de
acordo
com sua origem na própria solda ou no metal base. Quatro
tipos comumente ocorrem no metal de solda, ou seja, trincas
transversais, longitudinais, de cratera e de chapéu ("hat"). As
trincas de metais básicos podem ser divididas em sete
categorias, a saber, trincas transversais, fissuraçõe lamelares,
delaminações e trincas na linha de
fusão.
(a) Trincas transversais (Transverse cracks)
Aparecem no
metal de solda, e são formadas quando as
tensões de
contração predominantes estão na
direção do eixo de solda (Nº 2 na FIG.
1.43). Podem
ser trincas a quente, que se separam intergranularmente como resultado
de encurtamento a quente ou retração planar
localizada,
ou podem ser separações transgranulares
produzidas por
tensões que excedem a resistência do material. As
trincas transversais situam-se em um plano normal ao eixo da solda e
geralmente são abertas à superfície. Elas geralmente se estendem
por toda a face da solda e às vezes se propagam no metal
base.
Trincas transversais no
metal base (Nº 3 na FIG. 1.43) ocorrem
na superfície ou perto da zona afetada pelo calor. Eles são o
resultado das altas tensões residuais induzidas pelo
ciclo térmico durante a soldagem. Alta dureza,
restrição excessiva e a presença de
hidrogênio promovem sua formação. Tais trincas se propagam no
metal de solda ou além da zona afetada pelo calor no metal
de base.
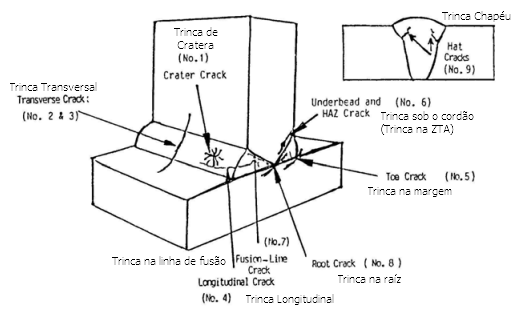
FIG. 1.43. Diferentes tipos de trincas
localizadas dentro e ao redor de uma junta soldada.
(b) Trincas sob o cordão (Underbead cracks)
São semelhantes às trincas transversais,
pois se formam na zona afetada pelo calor devido à alta
dureza,
restrição excessiva e presença de
hidrogênio. Sua
orientação segue o contorno da zona afetada pelo
calor (nº 6 na FIG. 1.43).
(c) Trincas longitudinais (Longitudinal cracks)
Estas fissuras podem
existir em três formas, dependendo de sua
posição na solda (Nº 4 na FIG. 1.43). As trincas
superficiais estão abertas na superfície e se estendem apenas
parcialmente através da solda. As trincas da raiz se
estendem da raiz até algum ponto dentro da solda. Trincas completas na linha
de centro podem se estender da raiz até a face do metal de
solda. As
fissuras de verificação são causadas
por altas
tensões de contração nos passes finais
aplicados a
uma junta de solda ou por um mecanismo de
fissuração a
quente.
As
trincas de raiz são a forma mais comum de trincas
longitudinais
de metal de solda devido à espessura e tamanho relativamente
pequenos do passe de raiz. Se
tais trincas não forem removidas, elas podem se propagar
através da solda à medida que os passes
subsequentes
são aplicados. Este é o
mecanismo usual pelo qual trincas completas na linha central
são formadas.
As trincas na linha
central podem ocorrer em temperaturas altas ou baixas. Em
baixas temperaturas, a fissuração geralmente
é o
resultado de um ajuste inadequado, ajuste excessivamente
rígido
ou uma pequena proporção de metal de solda para
metal
base.
Todos
os três tipos de trincas longitudinais geralmente
são
orientados perpendicularmente à face da solda e correm ao
longo
do plano que corta a junta soldada. Raramente se abrem na borda
da face da junta, pois isso requer uma solda de filete com um
cordão extremamente convexo.
(d) Trincas de cratera (Crater cracks
)
Como o nome indica, trincas
de cratera ocorrem na cratera de solda
formada no final de um passe de soldagem (Nº 1 na FIG. 1.43). Geralmente, esse tipo de trinca é causado pela falha em preencher a cratera antes
de interromper o arco. Quando
isso acontece, as bordas externas da cratera esfriam rapidamente,
produzindo tensões suficientes para rachar o interior da
cratera. Este
tipo de
fissura pode ser orientado longitudinalmente ou transversalmente, ou
pode ocorrer como um número de fissuras que se cruzam
formando
uma estrela (ou ramos de uma árvore). Trincas
longitudinais de cratera podem se propagar ao longo do eixo da solda
para formar uma trinca na linha central. Além
disso, essas trincas podem se propagar para cima através da
solda se não forem removidas antes da
aplicação
dos passes subsequentes.
(e) Trincas de chapéu (Hat cracks)
Essas
trincas derivam seu nome da forma da seção
transversal da
solda com a qual geralmente estão associadas. Este tipo de solda
alarga-se perto da face da solda, assemelhando-se a uma cartola
invertida (Nº 9 na FIG. 1.43). As fissuras de chapéu são o resultado do uso de
tensão excessiva ou de uma velocidade de soldagem muito
baixa. As
trincas estão localizadas na metade da espessura da solda e se estendem
até o metal de solda a partir da linha de fusão
da junta.
(f) Trincas na margem e na raíz (Toe and root cracks
)
Essas fissuras ocorrem na
área da raiz da solda ou perto do
limite entre o metal de solda e o metal de base (Nos 5 e 8 na FIG.
1.43).
These cracks occur in the root area of the weld or near the boundary between the weld metal
and the parent metal (Nos 5 and 8 in FIG. 1.43).
Mordedura (Undercut)
Durante
a passagem final ou de cobertura, as bordas superiores expostas da
preparação de solda chanfrada tendem a derreter e
escorrer para dentro do metal depositado na junta de solda. O
resultado é uma ranhura ou sulco que pode ser intermitente ou
contínua, com arestas mais ou menos afiadas ao longo do
reforço de solda, FIG. 1,44.
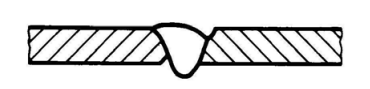
FIG. 1.44. Mordedura (Undercut).
Concavidade na raiz da solda (Concavity at the root of the weld)
Uma
superfície côncava na raiz da solda pode ocorrer
especialmente na soldagem de tubos (sem passe de cobertura no lado da
raiz). A
concavidade da raiz é comumente produzida pelo processo de
soldagem com arame tubular (FCAW). Na
soldagem sobre-cabeça, essa condição é
consequência da gravidade, que faz com que o metal fundido
ceda
da superfície superior inacessível da solda. Também
pode ocorrer na soldagem descendente com um cobre-junta de suporte na raiz da
ranhura de solda se a escória estiver presa entre o metal
fundido e o cobre-junta, FIG. 1,45.
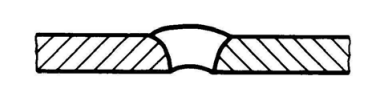
FIG. 1.45. Concavidade da raiz (Root concavity).
TABLE 1.7: CAUSAS COMUNS E RECOMENDAÇÕES PARA EVITAR TRINCAS
Juntas com alta restrição |
Pre
aquecimento, relaxar as tensões residuais mecanicamente, minimizar as
tensões de contração usando a técnica de soldagem com passo atrás
ou sequencia de soldagem em blocos |
Distorção excessivea |
Mudar
a corrente de soldagem e a velocidade, soldar com o eletrodo revestido
no negativo, amanteigar as faces do chanfro antes da soldagem |
Eletrodos defeituosos |
Mudar para eletrodos novos, aquecer eletrodos para remover a umidade |
Ajustagem indevida
|
Reduzir a abertura da raíz, corrigir as arestas com metal de solda |
Pequena cordão depositado |
Aumentar o diâmetro do eletrodo, aumentar a corrente de solda, reduzir a velocidade de soldagem |
Metal com alto teor de enxofre |
Usar metal de adição com baixo enxofre |
Distorção angular |
Executar soldagem balanceada em ambos os lados da junta |
Trincamento de cratera |
Encher a cratera antes de interromper o arco, use dispositivo de diminuição de corrente quando terminando o cordão de solda |
Presença de hidrogênio na atmosfera de soldagem |
Usar
processo de soldagem com baixo hidrogênio, prequecer e manter
aquecimento por 2 horas após a soldagem ou realizar tratamento térmico
pos soldagem imediatamente
|
Trincamento a quente |
Usar baixa energia de soldagem, depositar camadas finas, mudar o metal de base |
Baixa dutilidade
|
Usar preaquecimento, recozer o metal de base | Altas tensões residuais |
Reprojetar a solda, mudar a sequência de soldagem, aplicar tratamento térmico de de alívio de tensões |
Alta capacidade de endurecimento |
Preaquecimento, aumentar a energia de soldagem, tratar termicamente sem deixar a junta esfriar até a temperatura ambiente |
Fases metalúrgicas frágeis na microestrutura |
Tratamento térmico pré soldagem |
Penetração
excessiva (Excessive penetration
)
Em soldas, às
vezes, o metal fundido passa pela raiz do chanfro
da solda, produzindo um reforço excessivo na parte de
trás da solda. Em
geral, não é contínuo, mas tem uma
forma irregular
com gotas pendentes características de excesso de metal, FIG. .,46.
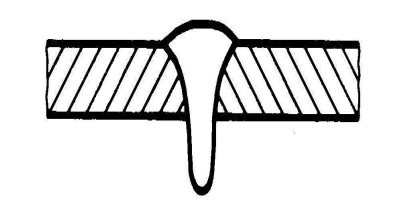
FIG. 1.46. Penetração
excessiva (Excessive penetration).
Sobreposição
(Overlap)
Sobreposição
é uma imperfeição no acabamento ou raiz de uma solda causada por um transbordamento do metal de
solda na superfície do metal de base, sem se fundir com este
último, FIG. 1.47. É
causado quando a vareta de solda foi usada em um ângulo
incorreto, o eletrodo viajou muito lentamente ou a corrente estava
muito baixa.
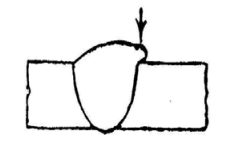
FIG. 1.47. Sobreposição (Overlap).
Fissuração Interlamelar (Lamellar tearing)
Este
é um fenômeno que ocorre em juntas em T onde a
placa da
alma é soldada em ambos os lados com soldas geralmente de
penetração total. As
tensões desenvolvidas por esta
configuração
resultam em uma separação que ocorre no metal
base entre
as raízes das duas soldas estendendo-se em um plano paralelo
à superfície do metal base. Tal descontinuidade
é frequentemente associada a
laminações ou outros planos de baixa resistência no metal.
Caracteriza-se
por uma fissura escalonada e causado pela retração
do
cordão de solda aplicando tensões no metal base através
de sua
espessura. Isso
resulta
inicialmente na descoesão das inclusões
não
metálicas e, em seguida, no rasgo dúctil a cerca
de 45o
entre as inclusões não metálicas
adjacentes para
produzir a fissuração em forma de degrau. A fissuração interlamenlar pode
ocorrer fora da zona afetada pelo calor 5–10 mm abaixo da
face de fusão, FIG. 1.48.
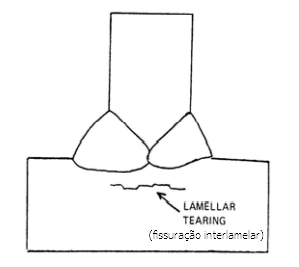
FIG. 1.48. Fissuração interlamenlar (Lamellar tearing).
Perfuração (Burn through)
Uma área com perfuração é aquela porção do
cordão de solda onde a penetração
excessiva fez
com que a poça de solda fosse soprada para dentro do tubo ou
vaso soldado pela parte externa. É
causada por fatores, como alta corrente, baixa velocidade da vareta de metal de solda,
manipulação incorreta da vareta, etc., que
produzem calor
excessivo em uma área. Muitas vezes é
acompanhado por queda excessiva do metal no interior do tubo. FIGO. 1.49.
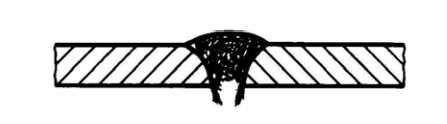
FIG. 1.49. Perfuração (Burn through).
Oxidação
do passe de raiz (Root pass oxidation)
A oxidação é o resultado
da proteção insuficiente da solda e da zona
afetada pelo calor da atmosfera. A
oxidação severa ocorrerá em
aços
inoxidáveis, por exemplo, reduzindo a resistência
à
corrosão, se a junta não for purgada com um
gás
inerte.
Processo de forjamento (Forging processes)
Forjamento
é o trabalho em um volume de metal para transformá-lo em uma forma
útil por martelagem ou prensagem e é o mais
antigo dos
processos de formação de metal. A maioria das
operações de forjamento são realizadas
a quente, embora alguns metais sejam forjados a frio. O trabalho a quente de
metais no processo de forjamento resulta em uma melhoria nas
propriedades mecânicas. Este
método de moldagem é, portanto, usado na
fabricação de peças que requerem boas
propriedades
mecânicas. A
melhoria nas propriedades mecânicas resulta de uma
consolidação geral do metal e fechamento de
cavidades de
gás e contração por meio de
pressão
mecânica, com um refinamento da estrutura cristalina e uma
remoção das
concentrações intergranulares de impurezas e
inclusões.
O forjamento é
feito em um martelo ou uma prensa. Uma prensa horizontal
(máquina de forjamento) é usada em certos casos
para forjar peças pequenas; caso
contrário, as máquinas de forjamento
são
verticais, cuja matriz inferior é fixa enquanto a matriz
superior é móvel, sendo transportada em um eixo
vertical. No
caso dos martelos, a matriz é levantada mecanicamente e o
golpe é dado pela queda livre da matriz,. FIG. 1.50.
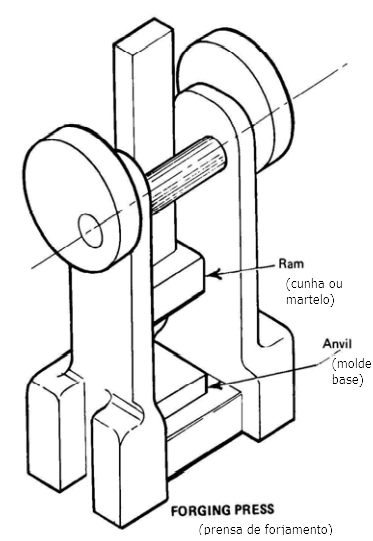
FIG. 1.50. Prensa de forjamento
vertical.
O forjamento pode ser
considerado em duas categorias. Primeiro
onde a superfície de trabalho das matrizes é
plana ou de
contorno curvo uniforme e a modelagem é feita por
manipulação usando ferramentas de forma simples. Isso é chamado
de forjamento em matriz aberta. A
segunda é onde os moldes de prensagem
são usados
e o metal é moldado ao ser forçado para dentro
dos
moldes. Isso
é chamado de forjamento em matriz fechada. Na
primeira categoria estão os forjados de
seção
transversal simples, redonda ou retangular e os forjados de formas mais
complicadas que são tão grandes que a moldagem em
matrizes fechadas seria impraticável ou muito caro. Pequenos
forjados de formato final complicado podem ser forjados grosseiramente
em matrizes simples e depois usinados até a forma final se o
número necessário for muito pequeno para
justificar o
custo de uma matriz de impressão. Nesta categoria
também estão as peças forjadas ocas. Para estes, o
metal central da peça bruta de tamanho adequado
é
usinado a frio (trepanado) ou é puncionado a quente usando
matrizes adequadas em uma prensa. A
peça é então forjada em um mandril que
passa pelo
furo central e é apoiada em ambas as extremidades para que o
mandril atue como a matriz inferior. No
forjamento de matriz fechada com prensa vertical, a matriz
inferior tem uma impressão correspondente a metade da
peça a ser feita, enquanto a matriz superior tem uma
impressão correspondente à outra metade. Para
formas relativamente simples, as matrizes podem ter apenas uma
impressão, mas mais comumente incorporam uma
série de
impressões nas quais a peça é moldada
sucessivamente até a forma final. O forjamento em matriz
fechada é comumente conhecido como 'forjamento em queda'. Ao redor das formas de impressão as matrizes são moldadas para fornecer
espaço para o excesso de metal usado, pois
não é prático ter exatamente a
quantidade de metal
necessária para preencher as formas de impressões. O excesso de metal que
é forçado para este espaço
é chamado em inglês de flash ou flashing. Após o
forjamento, este é cortado em outras matrizes adequadas. O negócio de
forjamento em matriz fechada FIG. 1.51
é tão competitivo que as perdas na sucata de
aparas
representam uma das áreas mais importantes para a economia.
O
processo de forjamento a quente pelo qual os parafusos, por exemplo,
são encabeçados é referido como
forjamento a
quente ou encabeçamento a quente. Neste
processo, uma barra de seção transversal uniforme
é presa entre matrizes ranhuradas e a pressão
é
aplicada na extremidade na direção do eixo da
barra por
meio de uma ferramenta com a forma da cabeça do parafuso. O metal flui sob a
pressão aplicada e preenche a cavidade entre as matrizes.
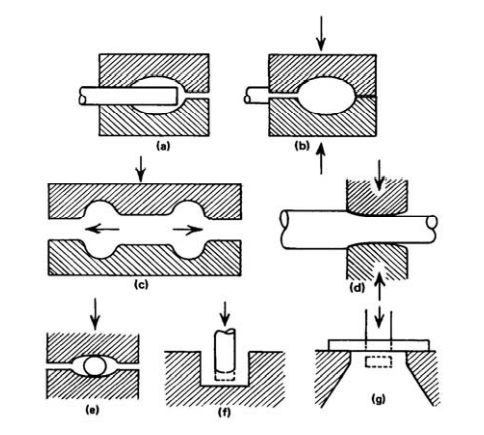
FIG. 1.51. Operações
de forjamento:
(a,
b) alimentação de material bruto (adding);
(c)
preenchimento da matriz (fuullering);
(d)
trefilação (drawing);
(e) estampagem (swaging);
(f)
retroextrusão (back extruding);
(g)
perfuração (punching).
Processo de Laminação
A laminação de metal
entre rolos laminadores é utilizada para a
produção de tiras, chapas, chapas, barras e
perfis. Uma
vez que o metal é formado por uma ação
de
compressão, a laminação pode ser
considerada como
um processo de forjamento contínuo com os rolos atuando como
martelos e o metal tendo afinada sua espessura.
A
laminação pode ser realizada acima da temperatura
de
recristalização (laminação
a quente) ou
abaixo da temperatura de recristalização
(laminação a frio). A
laminação a quente é sempre usada para
a laminação inicial do lingote fundido. Não
só é mais fácil deformar o lingote
rapidamente
quando ele está quente e plástico, mas o processo
de
laminação a quente fecha quaisquer
descontinuidades de
fundição e forja as superfícies
da descontinuidade juntas. Isso
evita que quaisquer falhas, que poderiam passar pela laminação a quente, sejam transportadas para
operações de laminação
subsequentes. Na
laminação a quente, os grãos
grosseiros são
primeiro alongados e distorcidos e depois formados em cristais
equiaxiais devido à recristalização. Os
cristais alongados e distorcidos pela laminação a
frio
não recristalizam e, portanto, o metal permanece endurecido.
Os laminadores
são descritos de acordo com a
disposição dos cilindros. O mais simples é
o rolete reversor de duas alturas FIG. 1,52 (b). Neste,
o metal é passado de um lado, os rolos são
então
abaixados e seu sentido de rotação é
invertido, e
o metal é passado de volta através deles. Este ciclo é
repetido até que o metal tenha a espessura desejada. No moinho de três
alturas FIG. 1.52
(c) os rolos giram continuamente em uma direção. As
camas de rolos sobem e descem para passar o metal entre os dois rolos
inferiores primeiro e depois de volta entre os dois rolos superiores. O ciclo é
repetido até que o metal tenha a espessura
desejadaa. No laminador de quatro alturas
FIG. 1.52
(d) e no laminador com multiplos roletes FIG. 1.52
(e) os rolos adicionais "apoiam" os rolos de trabalho e permitem que
eles apliquem maior pressão sobre o metal que
está sendo
laminado sem deflexão. Os
laminadores de quatro alturas e aglomerados operam da mesma maneira que
os laminadores reversores de duas alturas e são amplamente
utilizados para laminação a frio de tiras com
acabamento liso.
Do inglês "slabbing" ("slabs"=tarugos) é o
processo de sub dividir o lingote em tarugos menores prontos para serem relaminadas
em tiras, chapas e placas. O
processo é realizado a 1300°C e as descontinuidades
da
fundição no lingote são soldadas pelo
processo
tornando o tarugo homogêneo. O processo de fundição direto em perfis de barras ("cogging")
é semelhante ao "slabbing", exceto que o lingote é
nesse caso enrolado ('blooms") pronto para re-laminar em barras e
seções de perfis variados. Laminadores reversores de duas e
quatro alturas geralmente são usadas para
laminação de placas e blocos. A
relaminação de placas em tiras é
geralmente realizada em um laminador de tiras contínuo. A
placa é reaquecida a 1300°C e passa por um jatode
água e rolos de quebra de carepa
para remover
a oxidação deixada na superfície da
placa do
processamento anterior. Em seguida, é
desbastado e, finalmente, passado para o conjunto de rolos de acabamento. A tira é
finalmente enrolada pronta para processamento adicional. A
relaminagem de perfis e barras é normalmente realizada em
dois
laminadores reversores de alta altura equipados com cilindros
ranhurados. Algumas
plantas modernas que lidam com grandes quantidades de vigas e juntas de
seção padrão geralmente são
dispostas para
fornecer um processo contínuo FIG. 1.53. A
relaminagem de perfis e barras é normalmente realizada em
dois
laminadores reversores de alta altura equipados com cilindros
ranhurados. Algumas
plantas modernas que lidam com grandes quantidades de vigas e juntas de
seção padrão geralmente são
dispostas para
fornecer um processo contínuo FIG. 1.53.
Enquanto
os materiais que são forjados em arame e tubo requerem a
propriedade de maleabilidade, os materiais que são
trefilados em
arame e tubo requerem a propriedade de ductilidade, combinada com uma
resistência à tração
relativamente alta e
uma baixa capacidade de encruamento à medida que o processo
é realizado a frio. A
redução no tamanho da seção
trefilada
é fornecida pelo material sendo puxado através de
uma
matriz. As
hastes e barras são moldadas na seção final usando bancadas de
estiramento FIG. 1.54.
.
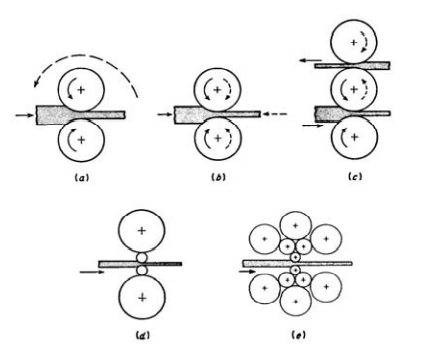
FIG. 1.52. Arranjos típicos
de rolos para laminadores:
(a, b) Laminação em uma direção (uma altura de roletes), Laminação com reversão (uma altura de roletes);
(c) Laminação com três
alturas de roletes;
(d) Laninação com quatro alturas de roletes;
(e) "cluster" (conjunto de roletes).
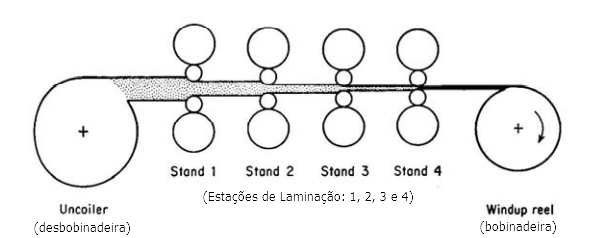
FIG. 1.53. Desenho
esquemático da laminação de tiras em
um laminador contínuo de quatro estágios.
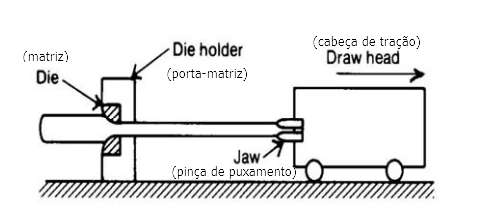
FIG. 1.54. Desenho
esquemático de um trefilador.
O
fio fino, especialmente o fio de cobre usado para condutores
elétricos, é trefilado em máquinas de
múltiplas matrizes. Um
bloco a jusante puxa o fio através de cada matriz (trefila) e o
passa
para o próximo estágio da máquina. À
medida que o fio se torna mais fino, seu comprimento aumenta e a
velocidade do último cabrestante deve ser muito maior do que
a
primeira FIG. 1.55.
A fabricação de tubo
é semelhante ao de fios usando uma bancada de
tração. No entanto, o tarugo
é perfurado para iniciar o espaço anular e o tubo é puxado
sobre um mandril. Onde forem
necessários comprimentos maiores de tubo, o tubos
fabricados devem ser enrolados. Isso proíbe o
uso de um mandril fixo e um mandril ou "plug" flutuante é
usado.
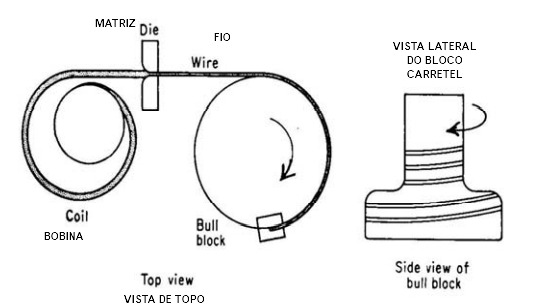
FIG. 1.55. Desenho esquemático de equipamento de
trefilação.
Processos de
extrusão
Outro processo semelhante
à laminação é a
extrusão. Em princípio, a
extrusão é semelhante a espremer pasta de dente
de um tubo de pasta de dente. A matéria-prima
é um tarugo fundido aquecido do metal necessário.
Normalmente,
esta é uma liga de cobre, uma liga de alumínio ou
chumbo. A
pressão necessária para forçar o metal
através da matriz é fornecida pelo
aríete
hidráulico. Como
o tarugo é reduzido ao tamanho da
seção acabada em
uma passagem pela matriz, a extrusão é um
processo
altamente produtivo. No entanto, a planta
é extremamente cara, assim como sua
operação e manutenção. Como
a maioria dos processos a quente, o acabamento e a precisão
dimensional da seção são menores do
que os
associados à trefilação a frio. Portanto,
onde é necessária maior precisão, a
seção extrudada recebe um leve tracionamento para
fortalecer a seção e o acabamento, e melhorar sua
precisão dimensional FIG. 1.56 (a, b).
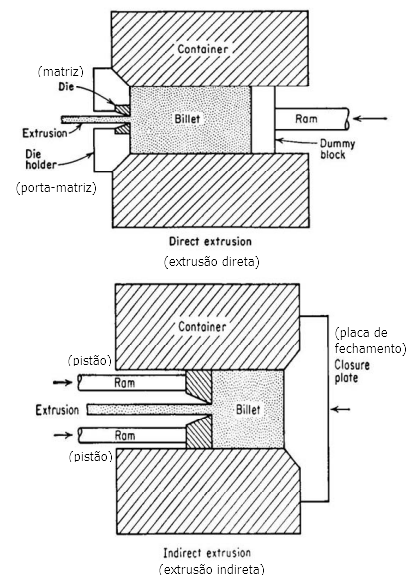
FIG. 1.56. Tipos de
extrusão.
Os
roletes Mannesmann, laminadores de cilindros com "plug", três rolos de perfuração de cilindros e roletes de fabricação de tubos
também são usados para a
produção de
tubos sem costura FIG. 1,57. Os roletes Mannesmann FIG. 1.57 (a) é
amplamente utilizado para a perfuração rotativa
de tarugos de aço e cobre. O processo emprega dois
rolos acionados em forma de barril que são colocados em
ângulo entre si. Um impulso axial
é desenvolvido, bem como rotação para
o tarugo. Devido
ao baixo arco de contato com o tarugo, tensões de
tração se desenvolvem ao longo do eixo do tarugo.
Isso
ajuda a abrir o centro do tarugo à medida que ele flui ao
redor
do ponto de perfuração para criar a cavidade do
tubo. A
perfuração é a
operação de trabalho a quente mais severa
normalmente aplicada a metais. Os
rolos Mannesmann não fornece redução
e
alongamento de parede suficientemente grandes para produzir tubos
acabados trabalhados a quente. Vários tipos de
laminadores de cilindros que conduzem o tubo sobre um longo mandril
contendo um cilindro, FIG. 1.57 (b) foram amplamente
adotados. Isso
levou ao desenvolvimento de máquinas de
perfuração de três rolos FIG. 1.57
(c) que produz tubos mais concêntricos com
superfícies
internas e externas mais lisas do que o projeto Mannesmann mais antigo. Os roletes de fabricação de tubos FIG. 1.57
(d) que lustra as superfícies externas e internas e remove a
forma levemente oval é geralmente uma das últimas
etapas
na produção de tubos ou
tubulações.
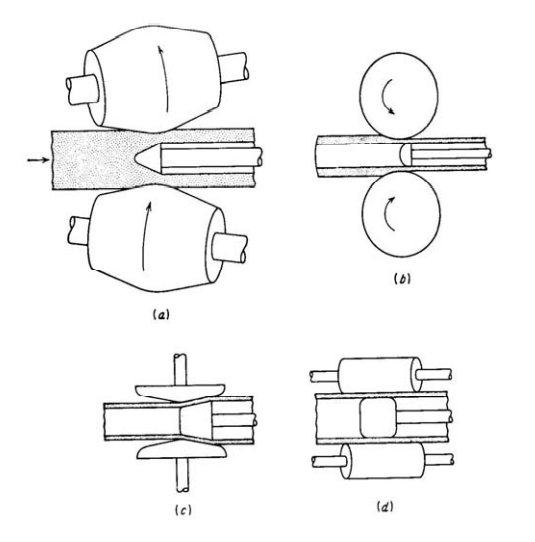
FIG. 1.57. Roletes
Mannesmann (a), laminadores de cilindros com "plug" (b), três rolos de
perfuração de cilindros (c) e roletes de fabricação de tubos (d).
Processo de Boleamento ("Spinning processes")
Um
método de fazer tampos de tanques e vasos e outras partes profundas de simetria circular
é chamado de boleamento (no inglês "spinning") FIG. 1.58 (a). A chapa base ("blank") de metal
é fixado contra um bloco, com a forma do boleado a produzir, que é girado em
alta velocidade. O
"blank" é formado progressivamente contra o bloco, seja com
ferramenta manual ou por meio de cilindros de trabalho pequenos. No processo de boleamento, a espessura do "blank" não muda,
mas seu diâmetro diminui. O processo de boleamento por cisalhamento FIG. 1.58 (b) é uma
variante do boleamento convencional. Neste
processo, o diâmetro da peça é igual ao
diâmetro do "blank", mas a espessura da peça boleada
é
reduzida de acordo com a equação t = to sen
α. Esse
processo também é conhecido como boleamento
mecânico, deformação com fluxo e boleamento
hidráulico. É
usado para grandes formas cônicas ou curvilíneas
axi-simétricas, como carcaças de dispositivo de propulsão de
foguetes e
cones de nariz de mísseis.
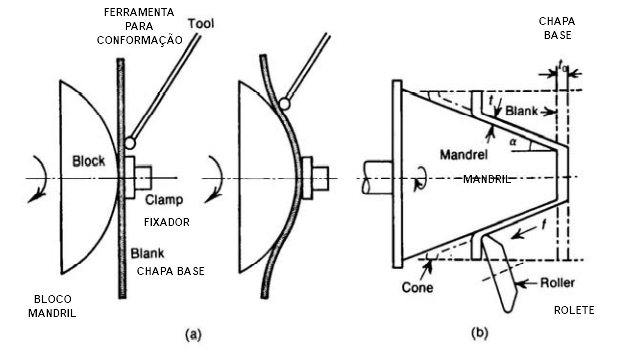
FIG. 1.58. Representação
esquemática de processos de boleamento:
(a) manual;
(b) por cisalhamento.
Cisalhamento e corte
O cisalhamento
é a separação do metal por duas
lâminas que se movem como mostrado na FIG. 1.59. No
cisalhamento, uma tira estreita de metal é severamente
deformada
plasticamente ao ponto de fraturar nas superfícies em
contato
com as lâminas. A fratura então
se propaga para dentro da espessura da chapa para fornecer separação
completa. A
profundidade em que o punção deve penetrar para
produzir
cisalhamento completo está diretamente relacionada
à
ductilidade do metal. A
penetração é apenas uma pequena
fração da espessura da chapa para materiais
frágeis, enquanto para materiais muito dúcteis
pode ser
ligeiramente maior que a espessura.
A folga entre as
lâminas é uma variável importante nas
operações de cisalhamento. Com
a folga adequada, as trincas que se iniciam nas bordas das
lâminas se propagarão através do metal
e se
encontrarão perto do centro da espessura para fornecer uma
superfície de fratura limpa. 1,59 (a), (b). Observe que, mesmo com a
folga adequada, ainda há distorção em
uma borda cortada. Folga
insuficiente produzirá uma fratura irregular e
também
exigirá mais energia para cisalhar o metal do que quando
há folga adequada. Com
folga excessiva, há maior distorção da
borda e
mais energia é necessária porque mais metal deve
se
deformar plasticamente antes de fraturar. Além disso, com
uma folga muito grande, rebarbas ou projeções
afiadas podem se formar na borda cortada. Uma aresta de corte cega
também aumenta a tendência à
formação de rebarbas. A altura da rebarba aumenta
com o aumento da folga e com o aumento da ductilidade do metal. Como a qualidade da borda
cortada influencia a conformabilidade da peça, o controle da
folga é importante. As folgas geralmente variam
entre 2 e 10 por cento da espessura da chapa; quanto mais espessa a
folha, maior a folga.
Todo um grupo de
operações de prensagem é baseado no
processo de cisalhamento. O
cisalhamento de contornos fechados, quando o metal dentro do contorno
é a parte desejada, é chamado de blanking, no inglês. Se
o material dentro do contorno for descartado, a
operação
é conhecida como puncionamento ou
perfuração. A
perfuração de entalhes na borda da folha
é chamada de entalhe.
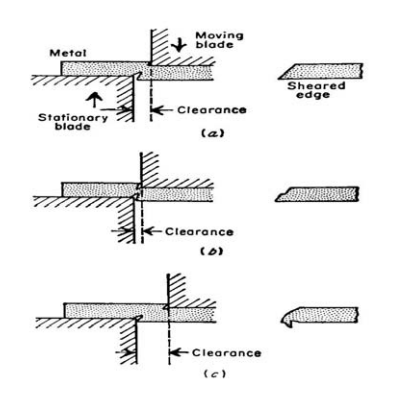
FIG. 1.59. Cisalhamento de metais:
(a) folga adequada,
(b)
folga insuficiente,
](c) folga excessiva.
Processos de dobramento
Dobramento
é o processo pelo qual um comprimento reto é
transformado em um comprimento curvo. É
um processo de conformação muito comum para
transformar
chapas planas e canais de chapas, tambores, tanques, etc. Além
disso, a
dobra faz parte da deformação em muitas outras
operações de conformação. A
definição dos termos usados nos processos de
dobra são ilustrados na FIG. 1.60. O raio da dobra R
é definido como o raio de curvatura na superfície
côncava ou interna da dobra. Para dobramento elástico abaixo do limite
elástico, a
deformação passa por zero na metade da espessura
da chapa
no eixo neutro. No dobramento plástico além do limite
elástico, o
eixo neutro se aproxima da superfície interna da curva
à
medida que a flexão prossegue.
Processos de estampagem
profunda
A
estampagem profunda é o processo de metalurgia usado para
moldar
chapas planas em artigos em forma de taça, como banheiras,
estojos e painéis de automóveis. Isto
é feito colocando uma chapa bruta de tamanho
apropriado
sobre uma matriz moldada e pressionando o metal na matriz com um
punção FIG. 1.61. Geralmente,
é necessária uma pressão de
fixação
ou retenção para pressionar a chapa bruta contra
a matriz para evitar enrugamento. Isso
é feito melhor por meio de um suporte liso ou anel de
retenção em uma prensa de dupla
ação.
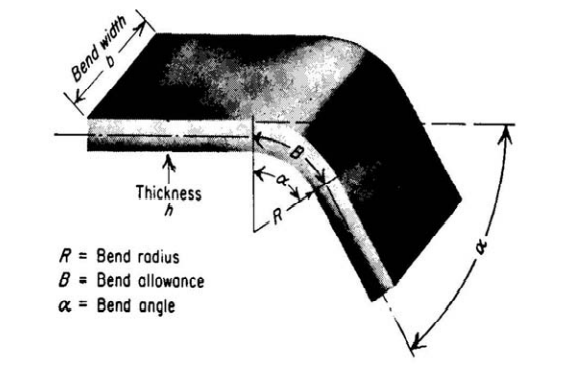
FIG. 1.60. Definição
dos termos utilizados no dobramento.
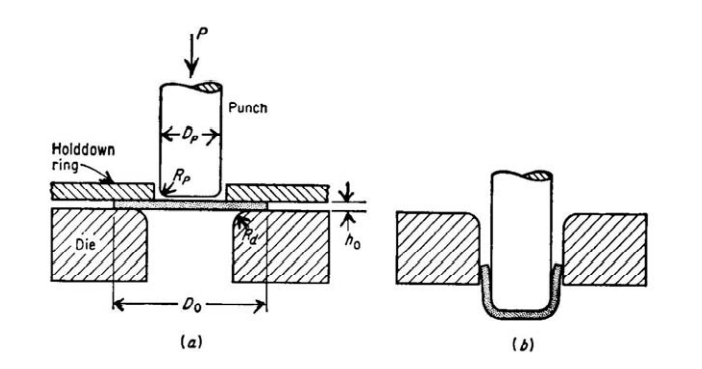
FIG. 1.61. Estampagem de um copo
cilíndrico:
(a) antes da
flexão,
(b) após a
trefilação.
Defeitos de forjamento e
laminação
As
descontinuidades em forjados podem ter origem na placa ou tarugo e ser
modificadas pela laminação e forjamento do
material, ou
podem resultar do próprio processo de forjamento. Alguns
dos defeitos que podem ocorrer nos forjados são semelhantes
aos
dos fundidos, pois a maioria dos forjados se origina de alguma forma de
lingote fundido. Dada
a seguir são alguns dos defeitos mais
específicos.
Laminações
(Fissurações lamelares)
Grandes porosidades,
tubulações e inclusões
não metálicas em placas ou tarugos são
achatadas e
espalhadas durante os processos de laminação e
forjamento. Estas
descontinuidades achatadas são conhecidas como
laminações, FIG. 1.62.
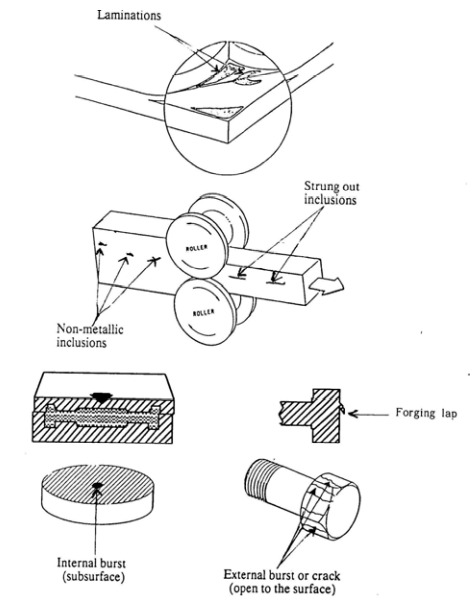
FIG. 1.62. Defeitos de forjamento e
laminação.
Costuras ("Seams")
As
irregularidades da superfície, como fissuras, na placa ou
no
tarugo, são esticadas e alongadas durante a
laminação e são então
chamadas de costuras. As costuras
também podem ser causadas pelo dobramento do metal devido a
laminação inadequada. As
costuras são descontinuidades na superfície e nas
barras
acabadas aparecerão como linhas retas contínuas
ou
interrompidas. Em
barras redondas, elas aparecerão como linhas retas ou
levemente espirais, contínuas ou interrompidas.
Dobras de forjamento
("Forging laps")
Dobras de forjamento são as descontinuidades causadas
pela dobra de metal em uma placa fina na superfície do
forjamento. Eles
são irregulares no contorno FIG. 1.62.
Descolamentos Internos ("Centre bursts")
Rupturas que ocorrem na
região central de um forjamento são chamadas de
descolamentos internos (no inglês, "centre bursts"). Eles
podem surgir devido a um procedimento de forjamento incorreto (por
exemplo, uma temperatura muito baixa ou uma
redução muito
drástica) ou pela presença de
segregação ou
fase frágil no metal que está sendo forjado, FIG. 1.62.
Trincas
térmicas ("Clinks")
Trincas térmicas são fissuras que ocorrem devido a tensões decorrentes de
gradientes de temperatura excessivamente altos dentro do material. As fissuras formadas durante o resfriamento muito rápido se
originam na superfície e se estendem para o corpo do
forjamento; aqueles
formados durante o aquecimento muito rápido ocorrem
internamente
e podem ser abertos para se tornarem cavidades em forma de diamante,
durante o forjamento subsequente.
Fissuras circulares ("Hairline cracks - flakes")
São trincas internas muito finas de formato circular
que
se desenvolvem e se estendem com o tempo e estão associadas
à presença de hidrogênio no
aço. Há
maior suscetibilidade em forjados maiores do que em menores e em certos
graus de liga de aço do que em aço carbono; eles podem ser evitados
pelo tratamento correto.
Gotas quentes (hot tears)
Defeitos superficiais
devido à ruptura e separação do metal
durante o forjamento. Eles podem estar associados
à presença de segregação
local, lascas/cordões ("seams") ou fases frágeis.
Inclusões alongadas ("Stringers")
Inclusões
não metálicas em placas ou tarugos, que
são afinadas e alongadas na direção da
laminação pelo processo de
laminação, FIG. 1,62.
Superaquecimento ("Overheating")
Normalmente
identificado pelas facetas vistas nas superfícies fraturadas
de
uma peça de teste, mas em casos extremos pode se manifestar
como
uma superfície severamente quebrada.
Tubo ("Pipe")
Se houver descarte
insuficiente dos gases aprisionados no lingote original, uma espécie de formação como um tubo
primário remanescente normalmente aparecerá
axialmente. O
tubo secundário que nunca foi exposto à atmosfera
será soldado se houver força de forjamento suficiente.
Processos de acabamento e
defeitos relacionados
Processo de usinagem
A
usinagem é um processo de produção de
forma no
qual um dispositivo acionado por energia faz com que o material seja
removido na forma de carepa. A
maior parte da usinagem é feita com equipamentos que
suportam
tanto a peça de trabalho quanto a ferramenta de corte. Embora
existam muitos tipos de máquinas utilizadas na
indústria
manufatureira, o termo máquinas-ferramenta foi
atribuído
ao grupo de equipamentos projetados para segurar uma ferramenta de
corte e uma peça de trabalho e estabelecer um conjunto
adequado
de movimentos entre eles para remover materiais do trabalho em forma de
carepas ou lascas. A
combinação comum de movimentos é
mostrada na FIG. 1.63.
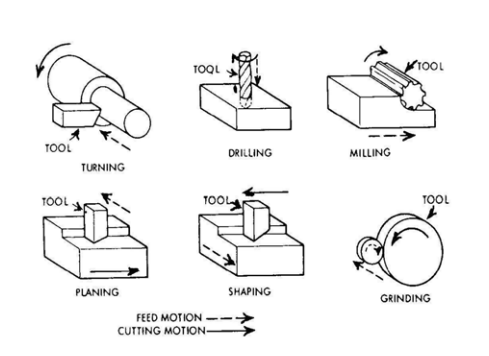
FIG. 1.63. Movimentos de
avanço e corte.
Girando e usinando
Essas
máquinas normalmente giram a peça de trabalho
para
produzir o movimento de corte e alimentam uma ferramenta de ponta
única paralela ao eixo de trabalho ou em algum
ângulo em
relação a ele. A
usinagem cilíndrica externa é chamada de
torneamento, a
usinagem cilíndrica interna é chamada de
mandrilamento e
a fabricação de uma superfície plana
alimentando a
ferramenta perpendicularmente ao eixo de
revolução
é chamada de faceamento.
Perfuração
com brocas
Uma ferramenta com uma ponta cônica
especial com dois ou mais arestas de
corte em sua extremidade exposta é chamada de broca e
é
girada e avançada axialmente na peça de trabalho
por meio
de uma furadeira. O trabalho principal
é a confecção ou
ampliação de furos cilíndricos.
Fresagem
Há uma grande
variedade de fresadoras que, como a furadeira, empregam fresas
multi-arestas especiais. Com
exceção de algumas fresadoras de
produção
especial, este equipamento permite alimentação
multidirecional e as fresas realizam seu corte principal em suas bordas
periféricas.
Máquinas de
linha reta
Um grupo de
máquinas-ferramentas fornece movimento de corte em linha
reta para sua ação de corte. Isso
inclui o modelador ("shaper", movimento em linha reta do cortador), a plaina
(movimento em linha reta da peça de trabalho e do bit) e a brocha
(movimento em linha reta de um cortador de vários dentes
especial). Devido
ao
alto custo da fresa especial, o brochamento é usado apenas
para
usinagem em quantidade de produção, mas o
modelador e a
plaina são mais comumente usados. Os rasgos da
máquina são causados por
máquinas-ferramentas cegas. Eles aparecerão
como linhas irregulares curtas em ângulo reto com a
direção da usinagem. Eles
são o resultado da ferramenta remover o metal mais
através de uma ação de rasgo do que
através
de uma ação de corte.
Processos de retificação
Os processos de retificação
empregam uma roda/disco abrasiva/o contendo muitos grãos de material
duro ligados em uma matriz. A
ação de um rebolo pode ser considerada como uma
ferramenta de corte de múltiplas arestas, exceto que as
arestas
de corte são de formato irregular e espaçadas
aleatoriamente ao redor da face do rebolo. Cada
grão remove um pequeno cavaco de espessura gradualmente
crescente, mas devido à forma irregular do grão
há
uma considerável ação de
aração
(como se a superfície da terra fosse uma área de terra que está sendo arada pelo rebolo) entre cada grão e a peça de trabalho.
A
profundidade de corte na retificação geralmente
é
muito pequena (alguns µm), e isso resulta em cavacos muito
pequenos que aderem prontamente ao rebolo ou à
peça de
trabalho. O
efeito líquido é que a energia de corte
específica
para retificação é cerca de 10 vezes
maior do que
para torneamento ou fresamento. Na
retificação, mais de 70% da energia vai para a
superfície acabada. Isso resulta em
considerável aumento de temperatura e
geração de tensões residuais.
As fissuras de retificação são uma
descontinuidade
do tipo de processamento causada por tensões que
são
geradas pelo excesso de calor criado entre o rebolo e o metal. As trincas de esmerilhamento são trincas finas e afiadas e
geralmente ocorrem em ângulos retos com a
rotação
do rebolo.
Tratamento
térmico do aço
Vários
ciclos de tratamento térmico foram desenvolvidos para
alterar a
microestrutura e, portanto, as propriedades do ferro e do aço. Alguns
dos tratamentos usuais e as propriedades específicas que
eles
desenvolvem em ferro e aço são discutidos na FIG.
1.64.
O
primeiro é o recozimento. O
aço é recozido para amolecê-lo para
facilitar a
usinagem e liberar tensões internas que podem ter sido
causadas
pelo trabalho do metal ou pela contração desigual
na
fundição. Para recozimento o
aço é aquecido lentamente a uma temperatura entre
800oC e 1000oC. É
então mantido a esta temperatura por tempo suficiente para
permitir que as mudanças internas ocorram. Em seguida, é
resfriado lentamente. Para
resfriamento lento, que é muito essencial, o aço
aquecido
é retirado do forno e embutido em areia, cinza, cal ou algum
outro material não condutor.
A
normalização é outro processo de
tratamento térmico. Este
tratamento é feito para refinar a estrutura e remover
tensões que possam ter sido causadas pelo trabalho a frio. Quando
o aço é trabalhado a frio, sua estrutura
cristalina pode
ficar perturbada e o metal pode se tornar quebradiço e
não confiável. Além disso,
quando o metal é aquecido a temperaturas muito altas para
forjamento, ele pode perder sua tenacidade. Para remediar esses
efeitos, o aço é aquecido lentamente
até cerca de 1000°C e resfriado ao ar.
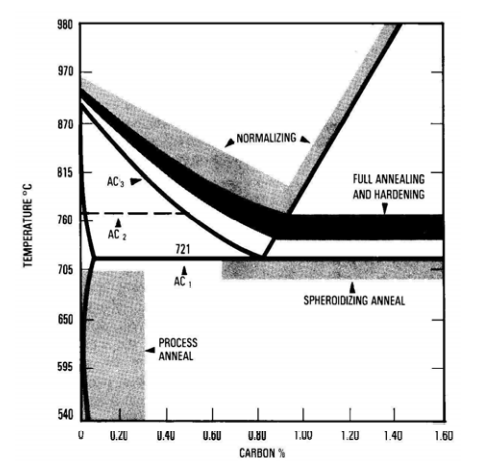
FIG. 1.64. Faixas de temperatura para
vários processos de tratamento térmico.
O
endurecimento ou têmpera do aço consiste em
aquecer o
aço acima da temperatura de
transformação e, em
seguida, resfriá-lo subitamente mergulhando-o em um banho de
água fria ou óleo. Esta forma de resfriamento
do aço quente é conhecida como têmpera
ou endurecimento. O aço
após a têmpera é conhecido como
aço temperado. Este tipo de aço
é duro e quebradiço devido à estrutura
cristalina martensítica. A dureza do aço
temperado depende do meio usado para têmpera e da taxa de
resfriamento.
Quando
o aço é aquecido até ou acima de sua
temperatura
crítica (faixa de temperatura de
transformação
cujo valor depende das porcentagens de liga) e mantido nessa
temperatura por algum período de tempo, o carbono se une em
solução sólida com o ferro na estrutura
cúbica
de face centrada. Nesta
fase, até 2% de carbono pode se dissolver na temperatura
eutética de 1148oC na qual existe a maior faixa de
composição gama. Isso é chamado
de processo de austentização.
O revenido envolve
o aquecimento do aço endurecido a uma temperatura adequada
entre 230oC e 600oC. Isso
causa uma transformação parcial da microestrutura martensítica de volta para perlita, tirando um
pouco
da dureza do aço para torná-lo mais resistente ao choque.
A
dureza mínima e a ductilidade máxima do
aço podem
ser produzidas por um processo chamado
esferoidização,
que faz com que o carboneto de ferro se forme em pequenas esferas ou
nódulos em uma matriz de ferrita. Para
começar com grãos pequenos que
esferóides mais
facilmente, o processo geralmente é realizado em
aço
normalizado. Algumas
variações de processamento são usadas,
mas todas
requerem a manutenção do aço
próximo
à temperatura A1 (geralmente um pouco abaixo) por um
número de horas para permitir que o carboneto de ferro se
forme
em seu estado mais estável e de menor energia de
glóbulos
pequenos e arredondados.
As
trincas de tratamento térmico são frequentemente
causadas
por tensões acumuladas durante o aquecimento e resfriamento.
O
resfriamento desigual entre seções leves e
pesadas pode causar fissuras no tratamento térmico. As
trincas de tratamento térmico não têm
direção específica e geralmente
começam em
cantos vivos que atuam como pontos de
concentração de
tensão (elevadores de tensão).
Acabamento da
superfície
Os
produtos acabados com a forma e o tamanho adequados requerem
frequentemente algum tipo de acabamento superficial para que possam
cumprir satisfatoriamente a sua função. Em
alguns casos, é necessário melhorar as
propriedades
físicas do material de superfície para
resistência
à penetração ou abrasão. Em
muitos processos de fabricação, a
superfície do
produto fica com sujeira, lascas de metal, graxa ou outros materiais
nocivos. Montagens
que
são feitas de materiais diferentes ou dos mesmos materiais
processados de maneiras diferentes podem exigir algum tratamento
especial de superfície para fornecer uniformidade de
aparência. Às vezes, o
acabamento da superfície pode se tornar uma etapa
intermediária no processamento. Por
exemplo, a limpeza e o polimento geralmente são essenciais
antes
de qualquer tipo de processo de galvanização. Alguns
dos procedimentos de limpeza também são usados
para
melhorar a suavidade da superfície nas peças
correspondentes e para remover rebarbas e cantos afiados, que podem ser
prejudiciais em uso posterior. Outra
necessidade importante para o acabamento superficial é a
proteção contra corrosão em diversos
ambientes. O
tipo de proteção fornecida dependerá
em grande
parte da exposição prevista, levando em
consideração o material protegido e os fatores
econômicos envolvidos.
A
obtenção dos objetivos acima exige o uso de
muitos
métodos de acabamento de superfície que envolvem
alteração química da
superfície, trabalho
mecânico que afeta as propriedades da superfície,
limpeza
por uma variedade de métodos e
aplicação de
revestimentos protetores, orgânicos e metálicos.
Endurecimento de
aços
O endurecimento do aço resulta em uma superfície dura, semelhante a uma casca. Algumas
aplicações do produto requerem propriedades de
superfície com dureza e resistência para resistir
à
penetração sob alta pressão e fornecer
propriedades de desgaste mínimas. Onde
a dureza total e a resistência máxima associada a
ela
não forem necessárias, pode ser mais
econômico
obter as propriedades de superfície necessárias
por um
processo de cementação. O
endurecimento da superfície envolve uma mudança nas propriedades
da
superfície para produzir uma casca dura e resistente ao
desgaste
com um núcleo resistente a choques. Isso geralmente
é realizado por uma mudança na química
do material da superfície. Com
alguns materiais, uma condição semelhante pode
ser
produzida por uma mudança da fase metalúrgica do material já
presente.
A
medição da profundidade de endurecimento às
vezes é
verificada por métodos destrutivos, cortando o objeto, atacando metalograficamente
a superfície de corte e verificando a profundidade de corte
com
um microscópio metalúrgico. Um
método mais rápido e fácil para o conhecimento
dessa profundidade diretamente para peças em serviço pode ser obtido pelo emprego do ensaio de correntes parasitas.
Cementação ("Carburizing")
O endurecimento do
aço pode ser realizado por vários
métodos. A escolha entre eles
depende do material a ser tratado, da aplicação e
das propriedades desejadas. Um
dos métodos mais comuns é a
cementação que
consiste em um aumento ou adição de carbono
à
superfície da peça. A
cementação geralmente é realizada em
aço de baixa liga ou aço (sem metais de adição) de baixo carbono. Se
uma liga de aço é usada, geralmente
contém
pequenas quantidades de níquel ou alguns outros elementos
que
atuam como retardadores de crescimento de grãos durante o
ciclo
de aquecimento. Aços
de baixo carbono são comumente usados para minimizar o
efeito
do tratamento térmico subsequente no material do
núcleo. É
possível cementar qualquer aço que contenha menos
de 0,7%
a 1,2% de carbono que é produzido no material da
superfície. O ciclo completo para
cementação por cementação
é ilustrado na FIG. 1.65.

FIG. 1.65. Ciclo de tratamento
térmico típico para
cementação.
Endurecimento por chama
Outro
processo de cementação que não requer
mudança de composição no material da
superfície é o endurecimento por chama. Este
método pode ser usado apenas em aços que
contêm
carbono suficiente para serem endurecidos por procedimentos
padrão de tratamento térmico. O endurecimento superficial é produzio aquecendo seletivamente parte ou toda a
superfície com queimadores a gás especiais de
alta
capacidade ou maçaricos de oxiacetileno a uma taxa
suficientemente alta para que apenas uma pequena profundidade da
superfície fique acima da temperatura crítica. Logo
atrás da tocha está uma cabeça de
têmpera de
água que inunda a superfície para reduzir a
temperatura
rápido o suficiente para produzir uma estrutura
martensítica. Como
no caso da cementação, a superfície
pode
então ser reaquecida para reveni-lo e melhorar a
tenacidade. A
profundidade de endurecimento é controlada pela temperatura
à qual o metal é elevado,
Limpeza
Poucos
processos de modelagem e dimensionamento produzem produtos adequados
sem algum tipo de limpeza, a menos que sejam tomadas
precauções especiais. Trabalho
a quente, tratamento térmico e soldagem causam
oxidação e formação de
incrustações na presença de
oxigênio. Pela
mesma razão, as peças fundidas são
geralmente
revestidas com incrustações de óxido. Se forem feitas em moldes
de areia podem apresentar grãos de areia fundidos ou
aderentes à superfície. Resíduos
de refrigerantes, lubrificantes e outros materiais de processamento
são comuns em muitas peças fabricadas. Além
dos filmes gordurosos do processamento, revestimentos protetores de
graxas, óleos ou ceras são frequentemente usados
intencionalmente para evitar oxidação ou corrosão em
peças que são armazenadas por algum
período de
tempo antes de serem colocadas em uso. Mesmo
que as peças estejam limpas na conclusão da
fabricação, raramente permanecem assim por muito
tempo.
Ao
usar métodos de END, como líquidos
penetrantes e
teste ultrassônico, uma boa pré-limpeza pode ser
necessária para obter resultados precisos e a
pós-limpeza
geralmente é necessária para deixar a
superfície
em condições adequadas. Em
algumas aplicações, como em aços
inoxidáveis e ligas à base de
níquel, os
acoplantes ultrassônicos e produtos dos líquidos penetrantes devem ser
feitos
apenas certos materiais para que não causem falhas por
corrosão sob tensão.
A limpeza às
vezes tem uma melhoria de acabamento associada a ela. Alguns
métodos de produção de formas produzem
características de superfície
insatisfatórias,
como cantos afiados, rebarbas e marcas de ferramentas que podem afetar
a função, facilidade de manuseio e
aparência do
produto. Alguns
processos de limpeza reduzem pelo menos parcialmente as
irregularidades da superfície para produzir uma
reflexão
de luz uniforme. A
melhoria das qualidades da superfície pode ser obtida pela
remoção de pontos altos por corte ou por revestimento com
plástico à medida que a limpeza é
realizada.
Muitos métodos
de limpeza diferentes estão disponíveis. Os
métodos de limpeza mais utilizados são aqui
brevemente
mencionados: os métodos de limpeza mais utilizados utilizam
um
meio de limpeza em forma líquida, que são
aplicados ao
objeto a ser limpo de diferentes maneiras, como
pulverização, escovação ou
imersão
do objeto em um banho de líquido de limpeza. A
limpeza pode ser realizada através do processo de jateamento
em
que o meio de limpeza que pode ser um líquido ou um
sólido (por exemplo, areia, granalhas de vidro ou
aço, etc.)
é acelerado a alta velocidade e colidido contra a
superfície a ser limpa. Várias
operações de limpeza podem ser realizadas de
forma
rápida e fácil usando escovas de arame
manualmente ou
girando-as em alta velocidade. A superfície
limpa pode receber um toque final de polimento usando um disco abrasiva
flexível. O polimento é um
tipo de processo de polimento.
Revestimentos
Muitos
produtos, principalmente os expostos à vista e os sujeitos a
alterações pelo ambiente com o qual
estão em
contato, necessitam de algum tipo de revestimento para melhorar a
aparência ou proteger contra ataques químicos. Todas
as superfícies recém-criadas estão
sujeitas
à corrosão, embora a taxa de ocorrência
varie muito
com o material, o ambiente e as condições. Para
todos os propósitos práticos, alguns materiais
são
altamente resistentes à corrosão porque os
produtos da
corrosão formados resistem à corrosão
adicional. Por
exemplo, uma superfície recém-usinada em uma liga
de
alumínio será imediatamente atacada pelo
oxigênio
do ar. O
revestimento
inicial de óxido de alumínio protege o metal
remanescente
e praticamente interrompe a corrosão, a menos que ocorra uma
mudança ambiental. As taxas de
corrosão são fortemente dependentes do
ambiente. As
taxas aumentam com o aumento da temperatura e maior
concentração do produto químico
atacante. A
necessidade de proteção contra
corrosão para
manutenção da aparência é
óbvia. A
menos que seja protegido, um objeto feito de aço brilhante
começará a mostrar oxidação em poucas horas de
exposição à atmosfera comum. Além
da mudança de aparência, perda de material real,
mudança de dimensões e
diminuição da
resistência, a corrosão pode ser a causa de
eventual perda
de serviço ou falha de um produto.
A
dureza e a resistência ao desgaste podem, no entanto, ser
fornecidas em uma superfície por revestimento com metais
duros. A
cromagem de contatos sujeitos à abrasão
é frequentemente usada para aumentar sua vida
útil. Revestimentos
de materiais plásticos e mistura asfáltica
são
às vezes colocados em superfícies para
proporcionar
amortecimento acústico. O benefício
adicional da proteção contra a
corrosão geralmente é adquirido ao mesmo tempo.
Metalização
A
pulverização de metal, ou
metalização,
é um processo no qual o fio metálico ou
pó
é alimentado em chama de aquecimento
anóxi-acetileno e o
mesmo após a fusão, é transportado
pelo ar de alta
velocidade para ser colidido contra a superfície de
trabalho. As
pequenas gotas aderem à superfície e se unem para
formar um revestimento. A natureza da
ligação depende em grande parte dos materiais. As
gotículas são relativamente frias quando entram
em
contato e, de fato, podem ser pulverizadas em madeira, couro e outros
materiais inflamáveis. Pouco ou nenhum fluxo
líquido auxilia na ação de
ligação. Se,
no entanto, existir afinidade suficiente entre os metais, pode-se
estabelecer um tipo de solda envolvendo ligações
atômicas. A
ligação é em grande parte
mecânica na
maioria dos casos e a pulverização de metal
geralmente
é feita em superfícies que foram intencionalmente
ásperas para auxiliar na fixação
mecânica. Zinco, alumínio
e cádmio, que
são anódicos ao aço e, portanto,
fornecem
proteção preferencial contra corrosão,
geralmente
são pulverizados em camadas finas, com espessura
média de
cerca de 0,25 milímetros (0,010 polegada), como
revestimentos
protetores. Como
os
revestimentos pulverizados tendem a ser porosos, revestimentos com duas
ou mais espessuras são usados para materiais
catódicos,
como estanho, chumbo e níquel. Os materiais
catódicos protegem apenas isolando o material base do
ambiente.
Vários
metais, principalmente zinco, estanho e chumbo, são
aplicados ao
aço para proteção contra
corrosão por um
processo de imersão a quente. O
aço em chapa, haste/vareta, tubo ou outra forma fabricada, devidamente
limpo
e fluxado (produto para facilitar a limpeza da superfície e a aderencia
do metal depositado), é imerso em metal de revestimento fundido. À medida que o
trabalho é retirado, o metal fundido que adere se solidifica
para formar uma camada protetora.
O
revestimento de muitos metais pode ser depositado em outros metais e em
não metais por galvanoplastia, quando adequadamente
preparado. Isto
é baseado no princípio de que quando uma
potência
de corrente contínua de alta voltagem é aplicada
a dois
eletrodos imersos em uma solução aquosa de sal
metálico, a corrente fluirá através do
circuito
causando mudanças nos eletrodos FIG. 1.66. No
eletrodo negativo, ou cátodo (peça que sofrerá a galvanoplastia), os
elétrons em
excesso fornecidos pela fonte de energia neutralizam os íons
metálicos carregados positivamente na
solução
salina para fazer com que o metal dissolvido seja depositado no estado
sólido. No
eletrodo positivo, ou ânodo (metal para recobrimento superficial, no inglês "plating metal"), o metal
entra
em solução para substituir o removido no outro
eletrodo. A
taxa de deposição e as propriedades do material revestido
dependem dos metais que estão sendo trabalhados, da
densidade de
corrente, da temperatura da solução, e de outros fatores.
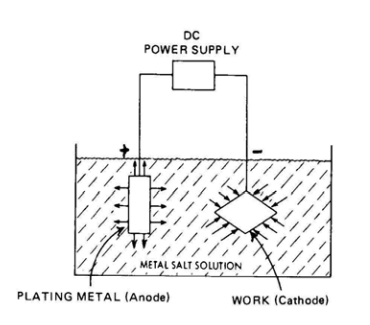
FIG. 1.66. Eletrodeposição ("Electroplating").
Tratamento
químico
Um método
relativamente simples e muitas vezes totalmente
satisfatório para proteção contra
corrosão
é a conversão de parte do material da
superfície
em uma composição química que resista
ao ataque do
meio ambiente. Essas
superfícies metálicas convertidas consistem em
filmes
inorgânicos relativamente finos (raramente mais de 0,025
milímetros ou 0,001 polegada de espessura) que
são
formados por reação química com o
material de
base. Uma
característica importante do processo de
conversão
é que os revestimentos têm pouco efeito sobre as
dimensões do produto. No
entanto, quando condições severas são
encontradas,
a superfície convertida pode fornecer apenas
proteção parcial, e revestimentos de tipos
totalmente
diferentes podem ser aplicados sobre elas.
Alumínio,
magnésio e zinco podem ser tratados eletricamente em um
eletrólito adequado para produzir um revestimento de
óxido resistente à corrosão. O
metal a ser tratado é conectado ao ânodo do
circuito, que
dá o nome de anodização ao processo.
Os
revestimentos de fosfato, usados principalmente em aço,
resultam de uma reação química do
ácido
fosfórico com o metal para formar um revestimento
não
metálico que é essencialmente sais de fosfato. O
revestimento é produzido por imersão de itens
pequenos ou
pulverização de itens grandes com a
solução
de fosfatização. Vários
processos proprietários de escurecimento, usados
principalmente em aço, produzem revestimentos de
óxido
preto atraentes. A
maioria dos processos envolve a imersão do aço em
uma
solução de soda cáustica aquecida a
cerca de 150oC
(300oF) e fortemente oxidante pela adição de
nitritos ou
nitratos. A
resistência à corrosão é
bastante fraca, a
menos que melhorada pela aplicação de
óleo, laca
ou cera. Como
no caso da
maioria dos outros procedimentos de conversão
química,
este procedimento também encontra uso como base para
acabamentos
de pintura.
1.4. Materiais em Serviço e Mecanismos de Dano
1.4.1 Comportamento dos
materiais em serviço
Os materiais devem operar
e funcionar em ambientes e situações muito
variados. Os
requisitos de segurança e confiabilidade exigem que os
materiais
e componentes tenham um bom desempenho em seus ambientes e
situações sem falhas prematuras. Há uma
série de fatores e processos que podem causar a falha de
materiais. Como
a falha prematura de componentes críticos pode ser
desastrosa em
muitas situações, além de ser causa de
perda de
produção e má
reputação, é
essencial entender e controlar essas causas de falha.
1.4.2
Condições que levam a defeitos e falhas
Devido
aos avanços na tecnologia e na compreensão dos
materiais
e seu design, e devido aos métodos sofisticados de
inspeção e ensaios, como os métodos de ensaios
não destrutivos, as falhas de metal ocorrem apenas em uma
porcentagem extremamente baixa dos milhões de toneladas de
metais fabricados a cada ano. Aqueles que ocorrem caem
principalmente em três categorias. As
falhas operacionais podem ser causadas por sobrecarga, desgaste,
corrosão e corrosão sob tensão,
fratura
frágil e fadiga do metal. Na segunda categoria
enquadram-se as falhas por projeto inadequado. Nesse
caso, é necessário considerar se existem cantos
vivos ou
áreas de alta tensão no projeto, se o fator de
tensão de segurança suficiente foi considerado e
se o
material selecionado é adequado para uma
aplicação
específica. O terceiro tipo de falha
é causado por tratamentos térmicos como
forjamento, endurecimento, têmpera e
soldagem, e por trincas superficiais causadas pelo calor da
retificação. Esses
aspectos e especialmente aqueles relacionados às
condições operacionais ou em serviço
serão
descritos aqui com mais detalhes.
Corrosão
Com
exceção de alguns metais nobres, todos os metais
estão sujeitos à
deterioração causada pela
corrosão comum. O ferro, por exemplo, tende
a voltar ao seu estado natural de óxido de ferro. Outros metais revertem a
sulfetos e óxidos ou carbonatos. Prédios, navios,
máquinas e automóveis estão todos
sujeitos a ataques do meio ambiente. A corrosão
resultante muitas vezes os torna inúteis e eles precisam ser
descartados. Bilhões
de dólares por ano são perdidos como resultado da
corrosão. A
corrosão também pode causar
condições
perigosas, como em pontes, onde as estruturas de suporte foram
corroídas, ou em aeronaves nas quais uma corrosão
insidiosa chamada corrosão intergranular pode enfraquecer os
membros estruturais da aeronave e causar uma falha repentina.
A
corrosão em metais é o resultado de seu desejo de
se unir
ao oxigênio na atmosfera ou em outros ambientes para retornar
a
um composto mais estável, geralmente chamado de
minério. O minério de
ferro, por exemplo, em alguns casos é simplesmente ferrugem
(óxido) do ferro. A
corrosão pode ser classificada pelos dois processos
diferentes pelos quais pode ocorrer; corrosão
por oxidação direta, que geralmente ocorre em
alta
temperatura, e corrosão galvânica, que ocorre em
temperaturas normais na presença de umidade ou de um
eletrólito. A
corrosão por oxidação direta
é
frequentemente vista na incrustação que ocorre
quando um
pedaço de metal é deixado em um forno por um
período de tempo. A escama (carepa) preta é
na verdade uma forma de óxido de ferro, chamada magnetita
(Fe3O4). A
corrosão galvânica é essencialmente um
processo
eletroquímico que causa a deterioração
dos metais
por uma ação muito lenta, mas persistente. Nesse
processo, parte ou todo o metal se transforma do estado
metálico
para o estado iônico e muitas vezes forma um composto
químico no eletrólito. Na
superfície de alguns metais, como cobre ou
alumínio, o
produto de corrosão às vezes existe como um filme
fino
que resiste à corrosão. Em
outros metais, como o ferro, o filme de óxido que se forma
é tão poroso que não resiste
à
ação corrosiva adicional, e a corrosão
continua
até que toda a peça seja convertida no
óxido.
A
corrosão requer a presença de um
eletrólito para
permitir que os íons metálicos entrem em
solução. O
eletrólito pode ser água doce ou salgada e
soluções ácidas ou alcalinas de
qualquer
concentração. Mesmo uma
impressão digital em metal pode formar um
eletrólito e produzir corrosão. Quando
ocorre a corrosão de um metal, átomos carregados
positivamente são liberados ou destacados da
superfície
sólida e entram em solução como
íons
metálicos, enquanto as cargas negativas correspondentes na
forma
de elétrons são deixadas para trás no
metal. Os
íons positivos destacados carregam uma ou mais cargas
positivas. Na
corrosão do ferro, cada átomo de ferro libera
dois
elétrons e então se torna um ferro ferroso
carregando
duas cargas positivas. Dois elétrons
devem então passar por um condutor para a área do
cátodo. Os
elétrons atingem a superfície do material do
cátodo e neutralizam os íons de
hidrogênio
carregados positivamente que se ligaram à
superfície do
cátodo. Dois
desses íons agora se tornarão átomos
neutros e
são liberados geralmente na forma de gás
hidrogênio. Essa
liberação dos íons de
hidrogênio carregados
positivamente deixa um acúmulo e uma
concentração
de íons negativos de OH que aumenta a alcalinidade no
cátodo. Quando
este processo está ocorrendo, pode-se observar que bolhas de
hidrogênio estão se formando apenas no
cátodo. Quando
cátodos e ânodos são formados em uma
única
peça de metal, suas localizações
particulares
são determinadas, por exemplo, pela falta de homogeneidade
no
metal, imperfeições da superfície,
tensões,
inclusões no metal ou qualquer coisa que possa formar uma
falha superficial que será como que lavada pelo processo corrosivo.
A
corrosão também pode assumir a forma de
erosão na
qual o filme protetor, geralmente um filme de óxido,
é
removido por uma atmosfera ou meio em movimento rápido. A
despolarização também pode ocorrer,
por exemplo,
nas hélices dos navios por causa do movimento
através da
água, que é o eletrólito. Isso causa um aumento da
taxa de corrosão do casco do navio de aço
anódico. Os
impulsores das bombas são frequentemente
corroídos por
esta forma de corrosão por erosão na qual os
íons
metálicos são rapidamente removidos na periferia
do
impulsor, mas são concentrados perto do centro, onde a
velocidade é menor. Outra forma de
corrosão é a corrosão intergranular. Isso ocorre internamente. Muitas
vezes, os contornos de grão formam ânodos e os
próprios grãos formam cátodos,
causando uma
deterioração completa do metal no qual ele
simplesmente
se desintegra quando falha. Isso
geralmente ocorre em aços inoxidáveis nos quais
carbonetos de cromo precipitam nos contornos de grão. Isso reduz o teor de cromo
adjacente aos contornos de grão, criando assim uma
célula galvânica. As diferenças no
ambiente podem causar uma alta concentração de
íons de oxigênio. Isso é chamado
de corrosão por concentração celular. A
corrosão por pites é localizada e resulta em
pequenos
orifícios na superfície de um metal causados
por uma
célula de concentração naquele ponto. Quando
altas tensões são aplicadas a metais em um
ambiente
corrosivo, a fissuração também pode
ser acelerada
na forma de falha por corrosão por tensão. É um
fenômeno muito localizado e resulta em uma falha do tipo
rachadura. A
proteção catódica é
frequentemente usada
para proteger cascos de navios de aço e
tubulações
de aço enterradas. Isso
é feito usando ânodos de sacrifício de
zinco e
magnésio que são aparafusados ao casco do navio
ou
enterrados no solo em intervalos e conectados eletricamente ao metal a
ser protegido. No
caso
do navio, a hélice de bronze atua como cátodo, o
casco de
aço como ânodo e a água do mar como
eletrólito. A corrosão
severa pode ocorrer no casco como resultado da
ação galvânica. Os
ânodos de sacrifício estão muito
próximos da
extremidade anódica da série galvânica
e têm
uma grande diferença de potencial entre o casco de
aço do
navio e a hélice de bronze. Tanto o casco quanto a
hélice tornam-se catódicos e consequentemente
não se deterioram. Os ânodos de
zinco ou magnésio são substituídos de
tempos em tempos. A
seleção dos materiais é de suma
importância. Mesmo que um material possa
ser normalmente resistente à corrosão, pode falhar em um ambiente
particular ou se acoplado a um metal mais catódico. Os revestimentos
são amplamente utilizados para evitar a corrosão.
Existem
diferentes tipos de tais revestimentos, por exemplo; revestimentos
anódicos, revestimentos catódicos, revestimentos
orgânicos e inorgânicos, revestimentos inibidores,
etc.
Fadiga
Quando
as peças metálicas são submetidas a
carregamentos
e descarregamentos repetidos por períodos prolongados, elas
podem falhar em tensões muito abaixo de seu limite de
escoamento
sem nenhum sinal de deformação
plástica. Isso é chamado
de falha por fadiga. Ao
projetar peças de máquinas que estão
sujeitas a
vibrações ou cargas cíclicas, a
resistência
à fadiga pode ser mais importante do que a
tração
final ou a resistência ao escoamento. A fadiga é um
fenômeno universal observado na maioria dos
sólidos. O
carregamento cíclico leva a um acúmulo
contínuo de
danos que, como no caso de fratura estática, eventualmente
resulta em ruptura. Limite
de fadiga, ou limite de resistência, é a carga
máxima que pode ser aplicada um número infinito
de vezes
sem causar falha. FIG. 1.67. Mas
10 milhões de ciclos de carregamento geralmente
são
considerados suficientes para estabelecer limites de fadiga. O
número de ciclos que levam à fratura em uma
determinada
tensão é muitas vezes referido como
resistência
à fadiga ou resistência. Este
fenômeno de falha de um material quando submetido a uma
série de ciclos de tensão variados é
conhecido
como fadiga, uma vez que se pensava que a fratura ocorria devido ao
enfraquecimento do metal ou ao cansaço.
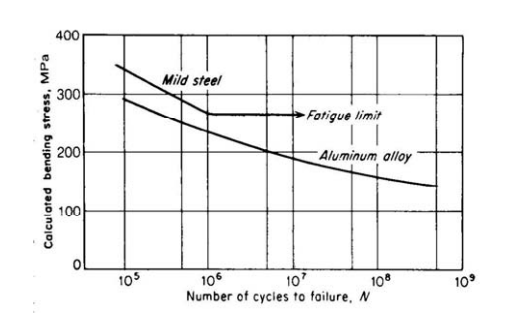
FIG. 1.67. Curvas de fadiga
típicas para metais ferrosos e não ferrosos.
Falhas causadas por fadiga
são encontradas em muitos dos materiais da
indústria. Alguns
plásticos e a maioria dos metais estão sujeitos
à
fadiga em vários graus, pois são amplamente
utilizados em
estruturas e máquinas carregadas dinamicamente. Estima-se que pelo menos
75% de todas as falhas de máquinas e estruturas foram
causadas por alguma forma de fadiga. A
falha por fadiga é causada por uma fissura iniciada por um
entalhe, dobra ou arranhão que continua a crescer
gradualmente
como resultado de reversões de tensão na
peça. O
crescimento da trinca continua até que a área da
seção transversal da peça seja
reduzida o
suficiente para enfraquecer a peça até o ponto de
fratura. Na
soldagem, mesmo respingos em uma superfície
sensível,
como uma mola de aço, podem iniciar a falha por fadiga. A fadiga é muito
influenciada pelo tipo de material, estrutura do grão e tipo
de carregamento.
Existem vários
tipos de falha por fadiga. No
caso de carga de flexão unidirecional, uma pequena trinca de
fadiga de formato elíptico geralmente começa em
uma falha
de superfície, como um arranhão ou marca de
ferramenta. A
fissura tende a se achatar (menor relação profundidade x altura) à medida que cresce. É
causada pela menor tensão na base da trinca devido à
diminuição da distância da borda da
trinca ao eixo
neutro. Se
um aumento de
tensão distinto, como um entalhe, estiver presente, a
tensão na base da trinca será alta, fazendo com
que a
trinca progrida rapidamente perto da superfície, e a trinca
tende a se achatar mais cedo. Em
uma carga de flexão bidirecional, as trincas
começam
quase simultaneamente em superfícies opostas quando as
superfícies são igualmente tensionadas. As
trincas prosseguem em direção ao centro em taxas
semelhantes e resultam em uma fratura bastante simétrica.
Nos estágios
iniciais do teste de fadiga, as amostras geralmente desenvolvem uma
quantidade apreciável de calor. Fissuras posteriores se
desenvolvem na superfície, eventualmente levando ao
falha. A
superfície da amostra é um local preferencial de
iniciação do dano. Os efeitos corrosivos
também podem auxiliar na degradação da
estrutura na superfície. A
corrosão é essencialmente um processo de
oxidação e, sob condições
estáticas,
forma-se uma película protetora de óxido que
tende a
retardar o ataque de corrosão. Na
presença de tensão cíclica a
situação
é bem diferente, uma vez que o filme de óxido
parcialmente protetor é rompido a cada ciclo permitindo um
novo
ataque. É
uma
explicação bastante simplificada que a
microestrutura na
superfície do metal é atacada pelo ambiente
corrosivo
causando uma iniciação mais fácil e
rápida
de trincas. Um dos aspectos mais importantes da corrosão-fadiga é que o
metal tendo um limite de fadiga no ar e normalmente não tem a definição
do limite de fadiga em um ambiente corrosivo que indicaria uma
possibilidade de fratura ocorrer em limites de tensão mais baixos.
Em
ligas comerciais, o limite de fadiga técnica geralmente fica
entre 0,3 e 0,5 da tensão de tração
final. A
resistência à fadiga dos metais muitas vezes pode
ser
aumentada por tratamentos que tornam a superfície mais
resistente à deformação. A
fratura então tende a começar na interface entre
a camada
de superfície dura e o núcleo mais macio. Elevadores
de tensão, como entalhes afiados, cantos, chavetas, furos de
rebites e arranhões podem levar a uma
redução
considerável da resistência à fadiga
dos
componentes metálicos. Bom
acabamento superficial e proteção contra
corrosão
são desejáveis para aumentar a
resistência
à fadiga. A
fadiga é basicamente um problema de baixa temperatura e em
temperaturas relativamente altas em relação ao
ponto de
fusão, a fratura e, portanto, a vida do corpo de prova
são governadas pela fluência.
Superfícies
fraturadas de metais fatigados geralmente apresentam uma
região
lisa e lustrosa devido aos efeitos de polimento decorrentes do atrito
nas fissuras. As
partes restantes da superfície de fratura, sobre as quais a
falha ocorreu por enfraquecimento do corpo de prova pela
redução de sua seção
transversal de carga
por trincas e fissuras superficiais, podem parecer mais irregular e
grosseiras, pois é causada essencialmente por fratura
estática.
As
trincas de fadiga são descontinuidades do tipo
serviço
que geralmente estão abertas para a superfície
onde
começam a partir de pontos de
concentração de
tensão (FIG. 1.68).
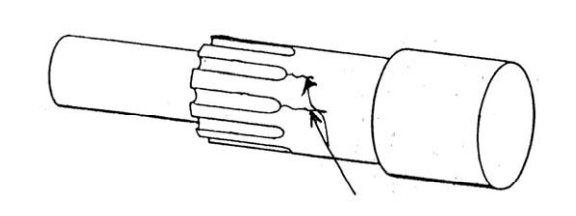
FIG. 1.68. Trincas de fadiga.
Fluência
A
deformação progressiva de um material sob
tensão constante é chamada de fluência.
Para
determinar a curva de fluência de engenharia de um metal, uma
carga constante é aplicada a um corpo de prova de
tração mantido a uma temperatura constante, e a
deformação (extensão) do corpo de
prova é
determinada em função do tempo. Embora
a medição da resistência à
fluência
seja bastante simples em princípio, na prática
requer um
equipamento de laboratório considerável. O
tempo decorrido de tais testes pode se estender por vários
meses, enquanto alguns testes foram executados por mais de 10 anos.
A curva da FIG. 1.69 ilustra a forma
idealizada de uma curva de fluência. A
inclinação desta curva (dε/dt)
é referida como a taxa de fluência. Após
um rápido alongamento inicial do corpo de prova,
εo, a
taxa de fluência, diminui com o tempo, então
atinge
essencialmente um estado estacionário no qual a taxa de
fluência muda pouco com o tempo e, finalmente, a taxa de
fluência aumenta rapidamente com o tempo até
ocorrer a
fratura. Assim,
é natural discutir a curva de fluência em termos
de seus três estágios. Deve-se
notar, no entanto, que o grau em que esses três
estágios
são facilmente distinguíveis depende fortemente
da
tensão aplicada e da temperatura.
Ao fazer um teste de
fluência, é prática comum
manter a carga constante durante todo o teste. Assim,
à medida que o corpo de prova se alonga e diminui em
área
de seção transversal, a tensão axial
aumenta. A
tensão inicial que foi aplicada ao corpo de prova
é geralmente o valor de tensão relatado. Foram
desenvolvidos métodos para compensar a mudança
nas
dimensões do corpo de prova para realizar o ensaio de
fluência sob condições de
tensão constante
do corpo de prova. Quando
são feitos testes de tensão constante, verifica-se que o
início do estágio III é muito
retardado. A
linha tracejada (curva B) mostra a forma de uma curva de
fluência de tensão constante. Em
situações de aplicação de engenharia, geralmente é
a carga e
não a tensão que é mantida constante,
portanto, um
teste de fluência com carga constante é mais
importante. No
entanto, estudos fundamentais do mecanismo de fluência devem ser feitos sob condições de tensão constante.
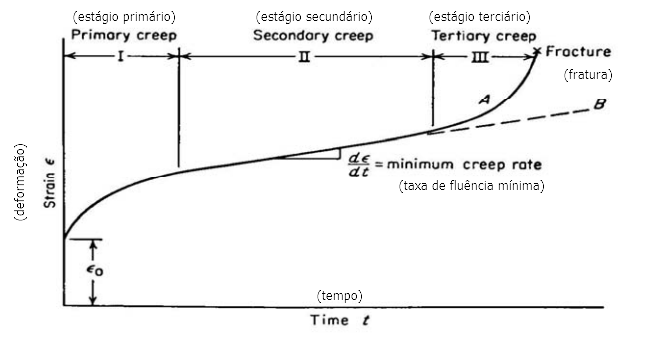
FIG. 1.69. Curva de fluência
típica mostrando as três etapas da curva de
fluência A, teste com carga constante; curva B, teste com tensão
constante.
O
primeiro estágio de fluência, conhecido como
fluência primária, representa uma
região de taxa de
fluência decrescente. A
fluência primária é um
período de
fluência predominantemente transitória em que a
resistência à fluência do material
aumenta em
virtude de sua própria deformação. Para
baixas temperaturas e tensões, como na fluência do
chumbo
à temperatura ambiente, a fluência
primária
é o processo de fluência predominante. O
segundo estágio de fluência, também
conhecido como
fluência secundária, é um
período de taxa de
fluência quase constante que resulta de um
equilíbrio
entre os processos concorrentes de encruamento e
recuperação. Por
esta razão, a fluência secundária
é
geralmente chamada de fluência em estado
estacionário. O
valor médio da taxa de fluência durante a
fluência
secundária é chamado de taxa de
fluência
mínima. A
fluência de terceiro estágio ou
terciária ocorre
principalmente em testes de fluência de carga constante em
altas
tensões e altas temperaturas. A
fluência terciária ocorre quando há uma
redução efetiva na área da
seção
transversal, seja por causa do estreitamento ou pela
formação de vazios internos. A
fluência de terceiro estágio é
frequentemente
associada a mudanças metalúrgicas, como
engrossamento de
partículas de precipitado,
recristalização ou
mudanças difusionais nas fases que estão
presentes.
Desgaste
O
desgaste metálico é um fenômeno de
superfície, que é causado pelo deslocamento e
desprendimento das partículas da superfície. Todas as
superfícies sujeitas a contato rolante ou deslizante
apresentam algum desgaste. Em alguns casos graves, a
superfície de desgaste pode ser soldada a frio na outra
superfície. De
fato, alguns metais são soldados por pressão em
máquinas, aproveitando sua tendência de serem
soldados a
frio. Isso
acontece
quando pequenas projeções de metal fazem contato
direto
na outra superfície e produzem atrito e calor, fazendo com
que
sejam soldadas na superfície oposta se o material for macio.
O
metal é arrancado se o material for quebradiço. A
lubrificação insuficiente geralmente é
a causa desse problema. Lubrificantes
de alta pressão são frequentemente usados ao
pressionar
duas peças para evitar esse tipo de soldagem. Duas
peças de aço, como um eixo de aço e um
furo de
aço em uma engrenagem ou roda dentada, se pressionadas
juntas a
seco, virtualmente sempre emperrarão ou soldarão
e
farão com que as duas peças sejam arruinadas para
uso
posterior. Em
geral, os
metais macios, quando forçados juntos, têm uma
tendência maior a 'soldar a frio' do que os metais mais
duros. Dois
metais extremamente duros, mesmo quando secos, terão muito
pouca tendência a soldar entre si. Por
esta razão, buchas de aço endurecido e pinos
endurecidos
são frequentemente usados em máquinas de
terraplenagem
para evitar desgaste. Alguns
metais macios quando usados juntos para superfícies de
rolamento (por exemplo, alumínio para alumínio)
têm
uma tendência muito grande de soldar ou emperrar. Entre esses metais
estão o alumínio, o cobre e o aço
inoxidável austenítico. virtualmente
sempre emperrará ou soldará e fará com
que as duas
partes sejam arruinadas para uso posterior. Em
geral, os metais macios, quando forçados juntos,
têm uma
tendência maior a 'soldar a frio' do que os metais mais
duros. Dois
metais extremamente duros, mesmo quando secos, terão muito
pouca tendência a soldar entre si. Por
esta razão, buchas de aço endurecido e pinos
endurecidos
são frequentemente usados em máquinas de
terraplenagem
para evitar desgaste. Alguns
metais macios quando usados juntos para superfícies de
rolamento (por exemplo, alumínio para alumínio)
têm
uma tendência muito grande de soldar ou emperrar. Entre esses metais
estão o alumínio, o cobre e o aço
inoxidável austenítico. virtualmente
sempre emperrará ou soldará e fará com
que as duas
partes sejam arruinadas para uso posterior. Em
geral, os metais macios, quando forçados juntos,
têm uma
tendência maior a 'soldar a frio' do que os metais mais
duros. Dois
metais extremamente duros, mesmo quando secos, terão muito
pouca tendência a soldar entre si. Por
esta razão, buchas de aço endurecido e pinos
endurecidos
são frequentemente usados em máquinas de
terraplenagem
para evitar desgaste. Alguns
metais macios quando usados juntos para superfícies de
rolamento (por exemplo, alumínio para alumínio)
têm
uma tendência muito grande de soldar ou emperrar. Entre esses metais
estão o alumínio, o cobre e o aço
inoxidável austenítico. Por
esta razão, buchas de aço endurecido e pinos
endurecidos
são frequentemente usados em máquinas de
terraplenagem
para evitar desgaste. Alguns
metais macios quando usados juntos para superfícies de
rolamento (por exemplo, alumínio para alumínio)
têm
uma tendência muito grande de soldar ou emperrar. Entre esses metais
estão o alumínio, o cobre e o aço
inoxidável austenítico. Por
esta razão, buchas de aço endurecido e pinos
endurecidos
são frequentemente usados em máquinas de
terraplenagem
para evitar desgaste. Alguns
metais macios quando usados juntos para superfícies de
rolamento (por exemplo, alumínio para alumínio)
têm
uma tendência muito grande de soldar ou emperrar. Entre esses metais
estão o alumínio, o cobre e o aço
inoxidável austenítico.
O
desgaste pode ser definido como a remoção
indesejada de
material das superfícies de contato por
ação
mecânica. Desgaste
excessivo pode ser causado por sobrecarga contínua, mas o
desgaste é normalmente um processo lento que está
relacionado ao atrito entre duas superfícies. O
desgaste rápido muitas vezes pode ser atribuído
à
falta de lubrificação ou à
seleção
inadequada de material para a superfície de desgaste. Algum desgaste é
esperado, no entanto, e pode ser chamado de desgaste normal. O desgaste é uma
das causas mais frequentes de falha. Encontramos
desgaste normal em máquinas-ferramentas como metal duro e
ferramentas de alta velocidade que se desgastam e precisam ser
substituídas ou reafiadas. As peças dos
automóveis se desgastam até que uma
revisão seja necessária. As
máquinas são inspecionadas regularmente quanto a
peças desgastadas, que quando encontradas são
substituídas; isso é chamado
de manutenção preventiva. Muitas vezes, o desgaste
normal não pode ser evitado; é simplesmente
aceito, mas pode ser reduzido ao mínimo pelo uso adequado de
lubrificantes. O
desgaste rápido pode ocorrer se a
distribuição de
carga estiver concentrada em uma área pequena devido ao
design
ou formato da peça. Isso pode ser alterado pelo
redesenho para oferecer mais superfície de desgaste. Velocidades muito altas
podem aumentar consideravelmente o atrito e causar desgaste
rápido.
Diferentes tipos de
desgaste incluem desgaste abrasivo, desgaste erosivo, desgaste
corrosivo e fadiga superficial. No desgaste abrasivo,
pequenas partículas são arrancadas das
superfícies do metal, criando atrito. O
atrito envolvendo desgaste abrasivo às vezes é
usado ou
mesmo necessário em um mecanismo como nos freios de um
automóvel. Os materiais são
projetados para minimizar o desgaste com a maior quantidade de atrito
neste caso. Onde
o atrito não é desejado, um lubrificante
é
normalmente usado para fornecer uma barreira entre as duas
superfícies. Isso
pode ser feito por filmes lubrificantes pesados ou
lubrificação de contorno mais leve em que
há um
filme residual. O
desgaste erosivo é frequentemente encontrado em
áreas
sujeitas a um fluxo de partículas ou gases que colidem com o
metal em altas velocidades. O jateamento de areia, que
às vezes é usado para limpar peças,
utiliza esse princípio. O
desgaste corrosivo ocorre como resultado de um meio ácido,
cáustico ou outro meio corrosivo em contato com
peças
metálicas. Quando
os lubrificantes são contaminados com materiais corrosivos,
a
corrosão pode ocorrer em áreas como rolamentos de
máquinas. A
fadiga da superfície é frequentemente encontrada
em
rolamentos de rolos ou esferas ou rolamentos de manga, onde um impulso
lateral excessivo foi aplicado ao rolamento. É visto como uma
rachadura fina ou como pequenos pedaços (lasca) despreendendo-se da
superfície.
Vários
métodos são usados para limitar a quantidade de
desgaste na peça. Um dos métodos
mais usados é simplesmente endurecer a peça. Além
disso, a peça pode ser endurecida superficialmente por
difusão de um material, como carbono ou cromo, na
superfície da peça. As peças
também podem ser metalizadas, revestidas ou tratadas
termicamente. Outros
métodos para limitar o desgaste são a
galvanoplastia
(especialmente o uso de cromo industrial duro) e a
anodização do alumínio. Algumas
placas de níquel são usadas, assim como
ródio, que
é muito duro e tem alta resistência ao calor. O
revestimento de óxido que é formado por
anodização em certos metais, como
magnésio, zinco,
alumínio e suas ligas, é muito duro e resistente
ao
desgaste. Esses
óxidos são porosos o suficiente para formar uma
base para
tintas ou manchas para dar maior resistência à
corrosão. Alguns
dos tipos de revestimento de difusão são
cementação,
carbonitretação, cianeto,
nitretação, cromação e
siliconização. A
cromização consiste na
introdução de cromo nas camadas superficiais do
metal base. Isso
às vezes é feito pelo uso de pó de
cromo e banhos
de chumbo nos quais a peça é imersa a uma
temperatura
relativamente alta. Isso,
é claro, produz um aço inoxidável na
superfície do aço de baixo carbono ou um metal
base de
ferro, mas também pode ser aplicado a materiais
não
ferrosos como tungstênio, molibdênio, cobalto ou
níquel para melhorar a resistência à
corrosão e ao desgaste. A
fusão do silício, que é chamada de
hirigização, consiste na
impregnação de um
material à base de ferro com silício. Isso também
aumenta muito a resistência ao desgaste. A
cromização consiste na
introdução de cromo nas camadas superficiais do
metal base. Isso
às vezes é feito pelo uso de pó de
cromo e banhos
de chumbo nos quais a peça é imersa a uma
temperatura
relativamente alta. Isso,
é claro, produz um aço inoxidável na
superfície do aço de baixo carbono ou um metal
base de
ferro, mas também pode ser aplicado a materiais
não
ferrosos como tungstênio, molibdênio, cobalto ou
níquel para melhorar a resistência à
corrosão e ao desgaste. A
fusão do silício, que é chamada de
hirigização, consiste na
impregnação de um
material à base de ferro com silício. Isso também
aumenta muito a resistência ao desgaste. A
cromização consiste na
introdução de cromo nas camadas superficiais do
metal base. Isso
às vezes é feito pelo uso de pó de
cromo e banhos
de chumbo nos quais a peça é imersa a uma
temperatura
relativamente alta. Isso,
é claro, produz um aço inoxidável na
superfície do aço de baixo carbono ou um metal
base de
ferro, mas também pode ser aplicado a materiais
não
ferrosos como tungstênio, molibdênio, cobalto ou
níquel para melhorar a resistência à
corrosão e ao desgaste. A
fusão do silício, que é chamada de
hirigização, consiste na
impregnação de um
material à base de ferro com silício. Isso também
aumenta muito a resistência ao desgaste. produz
um aço inoxidável na superfície de
aço de
baixo carbono ou um metal base de ferro, mas também pode ser
aplicado a materiais não ferrosos como tungstênio,
molibdênio, cobalto ou níquel para melhorar a
resistência à corrosão e ao desgaste. A
fusão do silício, que é chamada de
hirigização, consiste na
impregnação de um
material à base de ferro com silício. Isso também
aumenta muito a resistência ao desgaste. produz
um aço inoxidável na superfície de
aço de
baixo carbono ou um metal base de ferro, mas também pode ser
aplicado a materiais não ferrosos como tungstênio,
molibdênio, cobalto ou níquel para melhorar a
resistência à corrosão e ao desgaste. A
fusão do silício, que é chamada de
hirigização, consiste na
impregnação de um
material à base de ferro com silício. Isso também
aumenta muito a resistência ao desgaste.
O
revestimento duro é colocado em um metal pelo uso de
vários tipos de operações de soldagem,
e é
simplesmente um tipo duro de liga metálica, como liga de
cobalto
e tungstênio ou carboneto de tungstênio, que produz
uma
superfície extremamente dura que é muito
resistente ao
desgaste. A
pulverização de metal é usada com a
finalidade de
tornar superfícies resistentes ao desgaste e para reparar
superfícies desgastadas.
Sobrecarga
As
falhas de sobrecarga geralmente são atribuídas a
um
projeto defeituoso, cargas extras aplicadas ou um movimento imprevisto
da máquina. Cargas de choque ou cargas
aplicadas acima do limite de projeto são muitas vezes a
causa da quebra de máquinas. Embora
os engenheiros mecânicos sempre planejem um alto fator de
segurança em projetos (por exemplo, o fator de
segurança
de 10 para 1 acima do limite de escoamento que às vezes
é
usado em fixadores), os operadores de máquinas geralmente
tendem
a usar máquinas acima do limite de projeto. Obviamente, esse tipo de
estresse excessivo é devido ao erro do operador. O design inadequado
às vezes pode desempenhar um papel em falhas de sobrecarga. A
seleção inadequada do material no projeto da
peça
ou o tratamento térmico inadequado podem causar algumas
falhas
quando a sobrecarga é um fator. Muitas
vezes, um maquinista ou soldador selecionará uma barra ou
peça de metal para um trabalho com base em sua
resistência
à tração final, e não em
seu ponto de
escoamento. Na
verdade, este é um erro de projeto e pode, em
última análise, resultar em avaria.
Overload failures are usually attributed to faulty design, extra loads applied, or an unforeseen
machine movement. Shock loads or loads applied above the design limit are quite often the
cause of the breakdown of machinery. Although mechanical engineers always plan for a high
safety factor in designs (for instance the 10 to 1 safety factor above the yield strength that is
sometimes used in fasteners), the operators of machinery often tend to use machines above
their design limit. Of course, this kind of over-stress is due to operator error. Inadequate
design can sometimes play a part in overload failures. Improper material selection in the
design of the part or improper heat treatment can cause some failures when overload is a
factor. Often a machinist or welder will select a metal bar or piece for a job based upon its
ultimate tensile strength rather than upon its yield point. In effect this is a design error and can
ultimately result in breakdown.
Basicamente,
existem apenas dois modos ou maneiras em que os metais podem fraturar
sob cargas únicas ou monotônicas. Esses
dois modos são cisalhamento e clivagem e diferem
principalmente
na maneira como a estrutura cristalina do metal básico se
comporta sob carga. Quase todos os metais
sólidos comerciais são policristalinos. Cada
cristal ou grão individual é uma estrutura
composta por
um número muito grande de átomos dos elementos
constituintes. Esses
átomos estão dispostos em células
dentro de cada
cristal em um padrão tridimensional regular e repetitivo. As
células adjacentes compartilham os átomos dos
cantos e
suas posições são equilibradas por
forças
elétricas de atração e
repulsão. Forças aplicadas
podem causar distorção das células.
A
deformação por cisalhamento representa uma
ação de deslizamento nos planos dos
átomos nos
cristais. Em
um metal policristalino, uma leve deformação
não causa mudança permanente na forma, é chamado de
deformação elástica. Ou seja, o metal volta ao
seu tamanho e forma originais, como uma mola, após ser
descarregado. Se
uma carga maior for imposta, ocorre deformação
permanente
ou plástica devido ao deslizamento irreversível
entre
certos planos de átomos que compõem a estrutura
cristalina. Se
a carga
ou força aplicada for continuada, a
deformação por
cisalhamento faz com que pequenos microvazios se formem na
região de maior tensão. Esses pequenos vazios logo
se interconectam e formam superfícies de fratura.
O modo de clivagem de
separação da célula é
diferente. Neste
caso, a separação ocorre repentinamente entre uma
face da
célula e a face de acoplamento da célula
adjacente sem
que nenhuma deformação esteja presente. Se
uma carga maior for imposta, ocorre deformação
permanente
ou plástica devido ao deslizamento irreversível
entre
certos planos de átomos que compõem a estrutura
cristalina. Se
a carga
ou força aplicada for continuada, a
deformação por
cisalhamento faz com que pequenos microvazios se formem na
região de maior tensão. Esses pequenos vazios logo
se interconectam e formam superfícies de fratura. O modo de clivagem de
separação da célula é
diferente. Neste
caso, a separação ocorre repentinamente entre uma
face da
célula e a face de acoplamento da célula
adjacente sem
que nenhuma deformação esteja presente. Se
uma carga maior for imposta, ocorre deformação
permanente
ou plástica devido ao deslizamento irreversível
entre
certos planos de átomos que compõem a estrutura
cristalina. Se
a carga
ou força aplicada for continuada, a
deformação por
cisalhamento faz com que pequenos microvazios se formem na
região de maior tensão. Esses pequenos vazios logo
se interconectam e formam superfícies de fratura. O modo de clivagem de
separação da célula é
diferente. Neste
caso, a separação ocorre repentinamente entre uma
face da
célula e a face de acoplamento da célula
adjacente sem
que nenhuma deformação esteja presente. Esses pequenos vazios logo
se interconectam e formam superfícies de fratura. O modo de clivagem de
separação da célula é
diferente. Neste
caso, a separação ocorre repentinamente entre uma
face da
célula e a face de acoplamento da célula
adjacente sem
que nenhuma deformação esteja presente. Esses pequenos vazios logo
se interconectam e formam superfícies de fratura. O modo de clivagem de
separação da célula é
diferente. Neste
caso, a separação ocorre repentinamente entre uma
face da
célula e a face de acoplamento da célula
adjacente sem
que nenhuma deformação esteja presente.
A
fratura se originará sempre que a tensão local,
ou seja,
a carga por unidade de área da seção
transversal,
exceder primeiro a resistência local. Esta
localização irá variar dependendo da
resistência do metal e da tensão aplicada. Quando
um eixo ou forma semelhante é puxado pela força
de
tração, torna-se mais longo e mais estreito. Para
metais dúcteis a resistência ao cisalhamento
é o
elo fraco e esses metais falham através do modo de
cisalhamento. Esses
metais falham quando a tensão de cisalhamento excede a
resistência ao cisalhamento. No
caso de metais frágeis, estes falham porque a
tensão de
tração excede a resistência
à
tração. Os
metais frágeis sempre têm uma fratura
perpendicular
à tensão de tração e pouca
ou nenhuma
deformação porque a fratura ocorre antes que o
metal
possa se deformar plasticamente como os metais dúcteis.
Quando um cilindro
é carregado em compressão axial, um metal
dúctil torna-se mais curto e mais espesso. Em suma, ele se abaula
quando pressionado pela força compressiva e não
há fratura. Um metal frágil
em compressão pura irá fraturar paralelamente ao
comprimento do cilindro.
Fratura frágil e
fratura dúctil
A
fratura precedida por uma quantidade significativa de
deformação plástica é
conhecida como
fratura dúctil, caso contrário é
fratura
frágil. A
fratura frágil ocorre quando o fluxo plástico
é
inibido seja pelo bloqueio efetivo das discordâncias
atômicas por precipitados ou elementos ou pela
pré-existência ou formação
de trincas e
imperfeições atuando como geradores de
tensões
locais no material. Todos os materiais podem
ser fragilizados se a temperatura for reduzida o suficiente. Vidro,
cera de vedação, germânio,
silício e outros
materiais, embora dúcteis em temperaturas
próximas ao seu
ponto de fusão, são frágeis em
temperaturas
normais. Na
maioria dos
materiais, a resistência frágil, definida como a
tensão de tração máxima
suportada sem a
ocorrência de fratura frágil, é baixa
em
comparação com a resistência ideal que
o material
livre de falhas poderia exibir.
Como
já foi mencionado, os metais frágeis sempre
têm uma
fratura perpendicular à tensão de
tração e
têm pouca ou nenhuma deformação porque
a fratura
ocorre antes que o metal possa se deformar plasticamente. Assim, uma fratura por
tração de um metal frágil tem um plano
de fratura que é essencialmente reto. Também
geralmente tem uma aparência brilhante característica quando recém-fraturada (antes da oxidação com o tempo).
O padrão de uma
quebra muitas vezes pode revelar como a falha foi precipitada. Por
exemplo, se a ruptura foi causada por uma carga de choque repentina,
como uma explosão, geralmente há
formações
em forma de "chevron" (no inglês, na forma de "V" invertido) presentes que apontam para a origem da fratura. Quando
uma concentração de tensão
está presente,
como uma solda em uma estrutura que está sujeita a uma
sobrecarga repentina, a fratura geralmente é
frágil em
toda a ruptura, mostrando cristais, estrias e frentes de onda. As fraturas
frágeis são frequentemente intergranulares (ao
longo dos contornos de grão); isso dá
à superfície da fratura uma aparência
de rochosa (irregular) em alta ampliação. Quando
os contornos de grão são enfraquecidos por
corrosão, hidrogênio, danos causados pelo calor
ou
impurezas, a fratura frágil pode ser intergranular. As
falhas frágeis também podem ser transgranulares
(através dos grãos): isso é chamado de
clivagem.
A
fratura por clivagem está confinada a certos planos
cristalográficos que são encontrados em
estruturas
cristalinas compactas cúbicas de corpo centrado ou
hexagonais. Na
maioria das vezes, metais com outras estruturas de unidades cristalinas
não falham por clivagem, a menos que seja por trincas por
corrosão sob tensão ou por fadiga por
corrosão. A clivagem normalmente deve
ter uma superfície plana e lisa; no
entanto, como os metais são policristalinos com o caminho da
fratura orientado aleatoriamente através dos
grãos e
devido a certas imperfeições, certos
padrões, não lisos, são formados na superfície.
Pequenas quantidades de
hidrogênio têm um grande efeito na ductilidade de
alguns metais. O
hidrogênio pode entrar nos aços quando aquecidos
em uma
atmosfera ou em um material contendo hidrogênio, como durante
operações de decapagem ou limpeza,
galvanoplastia,
trabalho a frio, soldagem na presença de compostos contendo
hidrogênio ou o próprio processo de
fabricação de aço. Há um efeito
fragilizante perceptível em aços contendo
hidrogênio. Isso
pode ser detectado em testes de tração e visto na
região plástica do diagrama
tensão-deformação mostrando uma perda
de
ductilidade. A
galvanoplastia de muitas peças é
necessária devido
ao seu ambiente de serviço para evitar falhas por
corrosão. O
aço pode ser contaminado por materiais de galvanoplastia que
são comumente usados para operações
de limpeza
ou decapagem. Esses
materiais causam fragilização por
hidrogênio ao carregar o material com hidrogênio. O
hidrogênio monoatômico é produzido pela
maioria das
operações de decapagem ou de revestimento na
interface
metal-líquido, e parece que átomos de
hidrogênio
simples podem se difundir facilmente no metal. Medidas
preventivas podem ser tomadas para reduzir esse acúmulo de
gás hidrogênio na superfície do metal.
Uma fonte frequente de
fragilização por hidrogênio
é encontrada no processo de soldagem. As
operações de soldagem em que estão
presentes
compostos contendo hidrogênio, como óleo, graxa,
tinta ou
água, são capazes de infundir
hidrogênio no metal
fundido, fragilizando a zona de solda. Métodos
especiais de blindagem são frequentemente usados para
ajudar a
reduzir a quantidade de absorção de
hidrogênio. Um
método eficaz de remoção de
hidrogênio
é um tratamento de recozimento no qual a peça, ou
em alguns
casos a vareta de solda, é aquecida por longos
períodos
de tempo em temperaturas de 121 a 204°C. Este tratamento promove o
escape do hidrogênio do metal e restaura a ductilidade.
Elevadores
de tensão, como entalhes na superfície de um
material,
têm um efeito de enfraquecimento e causam
fragilização. Um exemplo
clássico é fornecido pelos entalhes internos (micro estruturais)
devido aos veios de grafite em ferros fundidos. Os veios fragilizam os
ferros fundidos quando solicitados em tensão. Portanto,
em aplicações estruturais, os ferros fundidos
são
mais úteis sob cargas de compressão. A
sua resistência à fragilidade e tenacidade podem,
no
entanto, ser aumentadas consideravelmente se a grafite for formada na
forma esferoidal em vez de em veios. Isso pode ser feito ligando
o fundido, por exemplo, com magnésio.
1.4.3 Conceitos de
desenvolvimento de ruptura em metais
A
maioria das ideias relacionadas ao desenvolvimento de descontinuidades em
materiais já foram discutidas na Seção
1.4.2. A fratura ocorre quando o tamanho desses defeitos, especialmente trincas,
atinge um determinado tamanho crítico.
1.5. Qualidade e
normalização
1.5.1 Qualidade
Qualidade de um produto
industrial não significa melhor ou excelente. Por outro lado,
é definida como a aptidão do produto para fazer o
trabalho exigido pelo usuário. Pode-se
dizer também que é a capacidade do produto de
atender
às especificações de projeto que
geralmente
são estabelecidas tendo em vista a finalidade e o uso para o
qual se espera ou se destina o produto. Como
afirmado anteriormente, seria melhor estabelecer ou definir um
nível
de qualidade ideal para um produto, em vez de tentar
torná-lo da
melhor qualidade possível, o que tornaria desnecessariamente
o
produto mais caro, o que pode não ser aceitável
para o
cliente.
De
forma generalizada, as características típicas
dos
produtos industriais que auxiliam na definição e
fixação de suas
especificações e qualidade
são composição química,
estrutura
metalúrgica, forma e projeto, propriedades físicas
de
resistência e tenacidade, aparência, propriedades
ambientais, ou seja, resposta às
condições de
serviço e presença ou não de descontinuidades
internas. Esses
requisitos devem ser atendidos dentro das tolerâncias
especificadas. O
custo, é claro, é um componente importante. A
capacidade de uma organização de atender aos
critérios de qualidade na produção de
bens ou
serviços influenciará, em última
análise, a
lucratividade e a sobrevivência dessa
organização. Se
não puder produzir mercadorias de acordo com os requisitos
do
cliente, não poderá competir, exceto em
circunstâncias muito anormais e de curto prazo. No entanto, se o cliente ' Como
os requisitos são impossíveis de atender, ou
difíceis de atender dentro das
restrições
financeiras impostas, a solução pode muito bem
ser
redefinir o requisito. A insistência em
um requisito desnecessariamente alto de desempenho pode ser
completamente impraticável. Em
todos os setores, em todos os cantos do mundo, a busca pela qualidade
tornou-se uma atividade popular, aplicada com maior ou menor sucesso,
dependendo da organização e seu nível
de
comprometimento. Deve-se
reconhecer que a qualidade não é um acidente, mas
deve ser planejada. A qualidade não
pode ser inspecionada em um produto depois que ele é feito. Em
vez disso, os critérios de inspeção
servem apenas
para verificar se os critérios de qualidade estão
sendo
alcançados. A
complexidade da gestão da qualidade dentro de uma
organização depende da complexidade do produto e
do
processo, bem como do critério de desempenho.
1.5.2 Controle de qualidade
O controle de
qualidade pode ser definido como os
controles aplicados em cada estágio de
fabricação
para produzir consistentemente um produto de qualidade ou, de outra
forma, diz-se que são as aplicações de
técnicas e atividades operacionais que sustentam a qualidade
de
um produto ou serviço que irá satisfazer
determinadas
necessidades, também o uso de tais técnicas e
atividades. O
conceito de controle de qualidade total é definido como um
sistema para definir, controlar e integrar todas as atividades da
empresa que permitem a produção
econômica de bens
ou serviços que proporcionarão a plena
satisfação do cliente. A
palavra 'controle' representa uma ferramenta de gestão com
quatro etapas básicas, a saber, estabelecer
padrões de
qualidade, verificar a conformidade com os padrões, agir
quando
os padrões não são atendidos e avaliar
a
necessidade de mudanças nos padrões.
1.5.3 Garantia de qualidade
Como o nome sugere,
garantia de qualidade é a tomada de todas as
ações planejadas e sistemáticas
necessárias
para assegurar que o item esteja sendo produzido com o nível
de
qualidade ideal e que, com confiança adequada, tenha um
desempenho satisfatório em serviço. A
garantia de qualidade visa fazer as coisas certas na primeira vez e
envolve uma avaliação contínua da
adequação e eficácia do programa geral
de controle
de qualidade com vistas a iniciar medidas corretivas quando
necessário. Para
um produto ou serviço específico, isso envolve
auditorias
de verificação e avaliação
de fatores de
qualidade que afetam a produção ou uso do produto
ou
serviço. A garantia de qualidade
é o controle de qualidade do sistema de controle de
qualidade.
1.5.4 Exame e ensaio
Exame
e ensaio são as funções de controle de
qualidade
que são realizadas, durante a
fabricação de um
produto industrial, por funcionários de qualidade que
são
funcionários do fabricante. O
ensaio também pode ser definido como o desempenho
físico
das operações (testes) para determinar medidas
quantitativas de certas propriedades. A maioria dos ensaios
não destrutivos é realizada sob este
título.
1.5.5
Inspeção
As
inspeções executam as
funções de controle
de qualidade que são realizadas durante a
fabricação de um produto industrial, realizadas por um
inspetor
autorizado. Eles
incluem medir, examinar, ensaiar, testar, medir ou comparar os resultados com os
requisitos aplicáveis. Um
inspetor autorizado é uma pessoa que não
é
funcionário do fabricante de um produto industrial, mas que
está devidamente qualificado e tem autoridade para verificar
a
sua satisfação se todos os exames especificados
no
código de construção do produto foram
feitos de
acordo com os requisitos do a seção de
referência
do código de construção.
1.5.6 Processo de normalização
O
objetivo da maioria dos métodos de ensaio não
destrutivos
é detectar descontinuidades existentes em
relação à
sua natureza, tamanho e localização. Isso
é feito por diferentes métodos, dependendo de sua
capacidade inerente ou sensibilidade à
detecção de
falhas. Diz-se
que um
método tem uma sensibilidade boa ou alta de
detecção de falhas quando pode detectar falhas
relativamente menores e vice-versa. A
sensibilidade da detecção de falhas para
diferentes
métodos de END depende de vários fatores
variáveis. Agora
imagine que alguém vai realizar, digamos, ensaioss
ultrassônicos de soldas circunferenciais em tubos de
aço
de 50 cm de diâmetro com 10 cm de espessura de parede. Ele
realizará extensas experiências para estabelecer
os
valores de diferentes fatores variáveis para desenvolver
um
método que dê resultados confiáveis e
reprodutíveis de sensibilidade desejada. Essa pessoa é
sábia o suficiente para anotar cuidadosamente seu
procedimento para ensaiar soldas de tubos. Se
alguém em qualquer lugar tivesse um problema de
inspeção ultrassônica de soldas de
tubos de
especificações semelhantes, haveria duas
opções abertas para ele. Primeiro
ele poderia realizar toda a extensa
experimentação
envolvendo muito tempo, esforço e dinheiro, e segundo ele
poderia solicitar a primeira pessoa e usar seu procedimento que era
conhecido por fornecer resultados confiáveis e
reprodutíveis de sensibilidade desejada. Muitas
pessoas em uma cidade, país ou países diferentes
podem
usar este método como um guia ou procedimento ou
prática
recomendada. Essas
muitas pessoas podem às vezes se reunir em uma
reunião,
conferência ou comitê para trocar suas
opiniões e
experiências relacionadas a este procedimento. Eles
podem concordar mutuamente sobre um procedimento padrão para ensaioss ultrassônicos de soldas circunferenciais em tubos de
aço de 50 cm de diâmetro e 10 cm de espessura de
parede e
recomendar à autoridade emissora de padrões de
seu
país que o emita como padrão nacional. Algumas
dessas normas emitidas pela autoridade emissora de normas do
país podem ser adotadas pela legislatura ou parlamento do
país e seu uso é obrigatório por lei. Isso
explica brevemente em termos muito simples o processo complexo e
demorado de formulação e emissão de
códigos
e normas. Algumas
dessas
normas emitidas pela autoridade emissora de normas do país
podem
ser adotadas pela legislatura ou parlamento do país e seu
uso
é obrigatório por lei. Isso
explica brevemente em termos muito simples o processo complexo e
demorado de formulação e emissão de
códigos
e normas.
1.5.7 Guias e
práticas recomendadas
Guias e
práticas recomendadas são padrões
oferecidos principalmente como auxílio ao
usuário. Eles usam verbos como
'deveria' e 'pode' porque seu uso geralmente é opcional. No
entanto, se esses documentos forem referenciados por códigos
ou
acordos contratuais, seu uso pode se tornar obrigatório. Se
os códigos ou acordos contiverem
seções ou
apêndices não obrigatórios, o uso dos
guias
referenciados e das práticas recomendadas por eles fica a
critério do usuário.
1.5.8 Normas
Normas
são documentos que regem e orientam as diversas atividades
que
ocorrem durante a produção de um produto
industrial. As
normas descrevem os requisitos técnicos para um material,
processo, produto, sistema ou serviço. Eles
também indicam, conforme apropriado, os procedimentos,
métodos, aparelhos ou ensaios para determinar que os
requisitos foram atendidos.
1.5.9 Códigos e
especificações
Códigos
e especificações são tipos semelhantes
de normas
que usam os verbos 'devem' ou 'vai' para indicar o uso
obrigatório de determinados materiais ou
ações ou
ambos. Os
códigos diferem das especificações,
pois seu uso
é obrigatório com força de lei pela
jurisdição governamental. A
utilização de
especificações torna-se
obrigatória apenas quando são referenciadas por
códigos ou documentos contratuais. Um
excelente exemplo de códigos é o
código ASME para
caldeiras e vasos de pressão, que é um conjunto
de
padrões que garantem o projeto,
construção e teste
seguros de caldeiras e vasos de pressão.
Codes and specifications are similar types of standards that use the verbs ‘shall’ or ‘will’ to
indicate the mandatory use of certain materials or actions or both. Codes differ from
specifications in that their use is mandated with the force of law by governmental jurisdiction.
The use of specifications becomes mandatory only when they are referenced by codes or
contractual documents. A prime example of codes is the ASME boiler and pressure vessel
code which is a set of standards that assure the safe design, construction and testing of boilers
and pressure vessels.
1.5.10 Procedimento
Em
ensaios não destrutivos, um procedimento é uma
sequência ordenada de regras ou
instruções que
descrevem em termos detalhados onde, como e em que sequência
um
método END deve ser aplicado a uma
produção.
1.5.11 Protocolos
As regras, formalidades,
etc., de qualquer procedimento, grupo, etc. (The Concise Oxford
Dictionary 8th Edition).
1.5.12 Relatório
Um relatório de
um exame não destrutivo ou de ensaio
é um documento que inclui todas as
informações
necessárias para poder:
- (a) Tomar
decisões sobre a aceitação dos
defeitos pelo ensaio.
- (b) Facilitar reparos de
descontinuidades inaceitáveis.
- (c) Permitir que o ensaio, exame ou
teste seja repetido.
1.5.13 Registros
Registros são
documentos que fornecerão, a qualquer
momento no futuro, as seguintes informações sobre
um
exame de ensaio não destrutivo:
- (i) o procedimento usado
para realizar o exame,
- (ii) as técnicas
de registro e análise de dados usadas, e
- (iii) os resultados do
exame.
1.5.14 Desenvolvimento de
um sistema de qualidade
O sistema de qualidade,
também chamado de sistema de garantia de qualidade,
já foi definido na Seção 1.5.3. É um
método eficaz de atingir e manter os padrões de
qualidade desejados. Baseia-se
no fato de que a qualidade é responsabilidade de toda a
organização e que a
inspeção por si
só não garante a qualidade ou, mais precisamente,
não garante a conformidade com os requisitos do controle ou
pedido do cliente. Isso
se aplica não apenas a produtos complexos, como
satélites
ou submarinos nucleares, mas também a produtos simples, como
pregos ou acessórios para tubos. Independentemente
do produto ou serviço envolvido, os elementos essenciais de
um
sistema de garantia de qualidade eficaz incluem:
- (a) Independência do departamento de garantia de qualidade dos departamentos de projeto e produção.
- (b) Padrões de qualidade que refletem tanto as necessidades do cliente quanto as características do processo de fabricação.
- (c)
Procedimentos escritos que abrangem todas as fases de projeto,
produção, inspeção, instalação e serviço, com um programa de revisão e
atualização contínua desses procedimentos.
- (d)
Controle do fluxo de documentos como entrada de pedidos, alterações de
pedidos, especificações, desenhos, guias de rota, relatórios de
inspeção e documentos de embarque.
- (e) Métodos para manutenção da identidade da peça que devem estabelecer a rastreabilidade ao longo do processo.
- (f) Métodos para detecção oportuna e segregação de material não conforme que também devem incluir programas de ação corretiva.
- (g) Cronogramas para calibração periódica de equipamentos de inspeção.
- (h) Cronogramas para retenção de registros importantes.
- (i) Programas de treinamento e qualificação de pessoal-chave de produção e inspeção.
- (j) Sistemas de controle de especificações incorporados ao pedido de compra; para controle da qualidade dos bens adquiridos e para inspeção apropriada dos bens adquiridos.
- (k)
Sistemas de controle dos processos de fabricação, montagem e embalagem,
incluindo inspeção em pontos-chave do fluxo do processo.
- (l)
Um sistema para auditoria periódica de qualquer um ou todos os itens
acima por pessoas que não tenham responsabilidade direta na área que
está sendo auditada.
O sistema de garantia de
qualidade é uma avaliação
ou auditoria de cada um desses subsistemas para determinar a
eficácia com que as funções
estão sendo
desempenhadas. As
avaliações geralmente são realizadas a
cada ano
para determinar quais elementos e subsistemas precisam ser melhorados. A
classificação geral fornece uma
comparação
com o desempenho passado ou com outras plantas de uma empresa
multiplantas. Esses
subsistemas são descritos brevemente nas
seções a seguir.
Independência do
departamento de garantia de qualidade
A
responsabilidade pelo desenvolvimento, operação e
monitoramento de um programa eficaz de garantia de qualidade em um
plano geralmente é do gerente de garantia de qualidade. As
empresas com várias fábricas podem ter um
departamento
corporativo de garantia de qualidade que revisa e coordena o sistema
para toda a organização. Para
ser eficaz, este deve ser um departamento com pessoal independente que
se reporte diretamente a um gerente de nível superior, como
gerente geral, vice-presidente ou presidente. O
departamento de garantia de qualidade deve ser livre para conceber e
recomendar sistemas e procedimentos específicos e exigir
ações corretivas a seu critério.
Estabelecimento de
padrões de qualidade
Nenhum nível de
qualidade único é necessário ou
economicamente desejável para uso universal; os requisitos de qualidade
de um clipe de papel são obviamente muito diferentes dos de
um reator nuclear. Muitos
grupos profissionais, associações comerciais e
agências governamentais estabeleceram códigos e
padrões nacionais. No
entanto, esses códigos e padrões geralmente
cobrem
requisitos amplos, enquanto um conjunto de regras detalhadas para cada
produto ou classe de produtos é necessário para o
controle de qualidade. Na
maioria das fábricas, é responsabilidade do
gerente de
garantia de qualidade interpretar os códigos e
padrões
nacionais em termos do pedido de compra e, a partir deles, elaborar
regras de processo exclusivamente adequadas aos produtos
específicos e métodos de
fabricação usados
naquela fábrica em particular. O conjunto de regras de
processo assim concebido pode ser conhecido por vários
nomes: nestas
notas de treinamento, será chamado de
'descrição da prática operacional'. Pode
haver milhares de descrições de plantas
operacionais em
arquivos de plantas, cada uma variando das outras conforme ditado pelo
código ou requisitos do cliente, limites de
composição química ou propriedades
mecânicas
ou outras características especiais. Grandes
plantas podem ter sistemas de armazenamento computadorizados que
permitem a recuperação imediata de parte ou de
todas as
descrições de práticas operacionais em
locais-chave em toda a planta.
Procedimento escrito
Os procedimentos escritos
são de primordial importância na garantia de
qualidade. As
instruções orais podem ser dadas de forma
inadequada ou
incorreta e, portanto, mal compreendidas e seguidas incorretamente. Instruções
escritas claras e concisas minimizam a probabilidade de má
interpretação. Generalizações
vagas que não atribuem responsabilidades
específicas nem
determinam a responsabilização em caso de erro
devem ser
evitadas. Por
exemplo,
os procedimentos devem ser específicos em
relação
ao tipo e forma dos registros de inspeção, a
identidade
do indivíduo que mantém os registros e onde os
registros
são mantidos. Da
mesma forma, um procedimento de calibração
não
deve exigir calibração em 'intervalos
periódicos',
mas deve especificar intervalos máximos entre as
calibrações. Dependendo
do tipo de equipamento, a calibração pode ser
realizada
em intervalos que variam de algumas horas a um ano ou mais.
Fluxo de contrôle de documentos
O
pedido de compra original, que geralmente tem menos de uma
página, pode gerar centenas de outros papéis de
trabalho
antes que o material ou peça encomendado seja enviado. Toda a documentação deve ser
precisa e deve chegar a cada seção de trabalho
a tempo. Em
algumas indústrias onde pode haver uma média de
duas ou
mais especificações ou
alterações de
desenho por pedido, é necessário um sistema
eficaz de
rastreamento de material que seja separado e distinto da
identificação de material. O
controle do fluxo de documentos coloca a responsabilidade direta em
departamentos normalmente não associados ao controle de
qualidade. O
escritório de vendas (responsável pela entrada do
pedido
do cliente), o grupo de planejamento de produção
(responsável pela programação de
trabalho e
acompanhamento do material) e o departamento de contabilidade
(responsável pelo faturamento e
expedição)
estão todos envolvidos. Muitas
fábricas de grande porte possuem sistemas de pedidos
computadorizados, cujo coração é um
'arquivo de
pedidos ativo'. Este
arquivo de computador recebe entradas periódicas para
atualizar
informações sobre
especificações, desenhos,
tamanhos de materiais, operações da loja,
expedição e roteirização. Por
sua vez, este arquivo pode ser acessível a partir de
vários terminais no escritório de vendas, escritórios da fábrica ou
seções de fabricação da fábrica, quando são necessárias
informações sobre a
localização do
material, situação do pedido e similares.
Mantenimento da identidade e da rastreabilidade dos materiais
Em
operações de fabricação de
alta velocidade,
principalmente aquelas que envolvem trabalho a quente, as marcas de
identidade na matéria-prima (como marca de tinta,
estêncil
ou carimbos) geralmente são destruídas durante o
processamento. Nesses
casos, devem ser elaborados procedimentos para manter a identidade
não apenas por marcação, mas
também por
localização e contagem. Esses
procedimentos às vezes devem fornecer a rastreabilidade de
unidades individuais de produtos por um método adequado para
o
produto e processo e devem incluir qualquer identidade adicional que o
cliente possa exigir. Em
última análise, tanto o produtor quanto o cliente
devem
ter certeza de que as mercadorias realmente entregues estão
descritas com precisão nos documentos de remessa,
relatórios de ensaio e certificados de conformidade. Essa
confiança é de grande importância em
certas
aplicações nas indústrias aeroespacial
e nuclear.
Material não
conforme e ação corretiva
Um sistema para
detecção e segregação de
material não conforme requer:
- (a)
Instruções de inspeção
escritas que possam ser claramente compreendidas.
- (b) Áreas de
retenção identificadas e segregadas para
peças que foram rejeitadas.
- (c)
Um grupo estruturado (às vezes chamado de conselho de
revisão de materiais) para avaliar o material rejeitado,
fazer o
julgamento final sobre sua adequação ao uso,
decidir o
que deve ser feito com o material não conforme e prescrever
ações para a causa da
rejeição.
Em
muitos casos, as peças rejeitadas estão apenas
ligeiramente fora da tolerância e sua utilidade
não
é prejudicada. Mesmo
assim, todas as decisões de um comitê de
revisão de
materiais para aceitar materiais não conformes devem ser
unânimes. Na
ausência de unanimidade, o problema pode ser encaminhado
à
alta administração para uma decisão
baseada no
julgamento geral do negócio. Em
algumas empresas, a autoridade do conselho de revisão de
materiais limita-se a meramente decidir se o material não
conforme é ou não adequado para uso. No entanto, em muitas
empresas o conselho também determina o que deve ser feito
com lotes não conformes; se
eles devem ser enviados 'como estão', classificados,
reparados
ou sucateados, e fixa a responsabilidade por perdas incorridas. Quando
uma ação corretiva é recomendada por
um
comitê de revisão de materiais, geralmente
é
orientada a sistemas, ou seja, destina-se a prevenir a
reincidência da não conformidade, evitando a sua
causa. Nos
casos em que um lote foi rejeitado porque o número de
aceitação de um plano de amostragem foi excedido,
as
decisões relativas à
disposição do lote
geralmente são feitas com base nos custos, a
solução que resulta no menor custo total para o
produtor
e o cliente é adotado. Às
vezes, o material que está ligeiramente fora da
tolerância
e, portanto, não é adequado para uso por um
cliente, pode
atender às especificações de outro
cliente.
Calibração
do equipamento (NT:
mesmo na lingua inglesa a calibração é muitas vezes confundida com o
ajuste de parâmetros para realização do ensaio. Aqui trata-se da
verificação eletrônica dos aparelhos de inspeção feita por entidades
autorizadas para tal.)
O sistema de garantia de
qualidade deve reconhecer que a
precisão e a repetibilidade do equipamento de
medição e teste podem ser afetadas pelo uso
contínuo; os
intervalos máximos entre as
calibrações devem ser
especificados nos procedimentos escritos de garantia de qualidade. Exceto,
talvez, para pequenos instrumentos manuais, como micrômetros,
cada máquina ou instrumento de ensaio deve ser claramente
rotulado com a última data de
calibração. Os
padrões de calibração devem ser
rastreáveis
a padrões de medição reconhecidos
pela
indústria ou nacionais. Também
é desejável manter um arquivo central de
registros de
calibração para cada planta ou departamento.
Retenção
de registros
Um
sistema de garantia de qualidade deve designar quais registros devem
ser retidos e deve estabelecer períodos de tempo
mínimos
para retenção de tais registros. É comum que
documentos importantes sejam retidos por 25 anos ou mais; a indústria
nuclear é obrigada a manter registros por 40 anos. O
tempo de retenção, no entanto, deve ser
consistente com
as necessidades reais, conforme ditado pela vida útil
projetada
dos produtos ou pelos requisitos legais. Além
de satisfazer certos requisitos contratuais ou outros requisitos
legais, os registros retidos podem proporcionar importantes
benefícios de custo tanto para o produtor quanto para o
cliente. Em
um caso, ensaios extensos e caros de uma estrutura de 50 anos antes do reparo
foram evitados quando o fabricante foi capaz de produzir desenhos
originais e relatórios de ensaio de material.
Treinamento e
qualificação de pessoal
Existem
códigos nacionais para a qualificação
de certos
trabalhadores especializados, por exemplo, soldadores e inspetores. Quando
aplicável, os códigos devem ser incorporados como
requisitos mínimos para treinamento e
qualificação
de pessoal-chave. Tudo
isso, no entanto, deve ser complementado por procedimentos escritos
locais para treinamento no local de trabalho e em sala de aula. A
gestão da garantia da qualidade deve reduzir os
procedimentos
complexos à forma mais simples que permita ao formando
compreender exactamente o que é o trabalho e como deve ser
executado.
Controle de material comprado
Todas
as especificações e pedidos para compras externas de
material cujo desempenho possa afetar a qualidade do produto devem
estar sujeitos à aprovação da gerência de
garantia de qualidade. A
inspeção do material recebido deve estar sujeita à
aprovação da gestão de garantia de qualidade. A inspeção do material recebido deve ser incorporada ao programa de garantia de qualidade. O
principal objetivo da inspeção de recebimento é
verificar falhas nos programas de qualidade do fornecedor, mas
não se espera que a inspeção de recebimento
compense o controle de qualidade deficiente por parte dos fornecedores.
O comprador
deve avaliar e auditar periodicamente o sistema de garantia de
qualidade de cada fornecedor principal para garantir que o material
adquirido tenha o nível de qualidade especificado.
Fabricação, montagem e embalagem
Todos
os processos de fabricação, montagem e embalagem devem
ser controlados para garantir a obtenção do produto
acabado com a qualidade certa no momento de sua chegada ao cliente. Desenhos
de projeto e os processos de fabricação e montagem devem
ser avaliados se os métodos apropriados de capacidade e
sensibilidade adequadas estão sendo aplicados e se os resultados
obtidos são confiáveis e reprodutíveis ou
não. Os ensaios
devem ser aplicados em etapas apropriadas durante a
fabricação e todos os relatórios de teste devem
ser devidamente assinados por pessoas autorizadas. Toda
a fabricação, ensaios, montagem e embalagem devem ser
feitos de acordo com procedimentos escritos verificáveis.
Auditoria de qualidade
A
auditoria da qualidade é uma avaliação
independente de vários aspectos do desempenho da qualidade para
fornecer informações sobre esse desempenho. As
auditorias de qualidade geralmente são feitas por empresas para
avaliar seu próprio desempenho de qualidade, por compradores
para avaliar o desempenho de seus fornecedores, por agências
reguladoras para avaliar o desempenho de organizações que
são designadas para regular.
O objetivo da auditoria é fornecer garantia de que:
- (a) Os procedimentos para atingir a qualidade são tais que, se seguidos, a qualidade pretendida será obtida.
- (b) Os produtos são adequados para uso e seguros para o usuário.
- (c) As leis e regulamentos estão sendo seguidos.
- (d) Existe conformidade com as especificações.
- (e) Os procedimentos escritos são adequados e estão sendo seguidos.
- (f) O sistema de dados é capaz de fornecer informações adequadas sobre a qualidade.
- (g) Ações corretivas estão sendo tomadas em relação às deficiências.
- (h) São identificadas oportunidades de melhorias.
Para
uma auditoria interna de qualidade, normalmente a
organização é dividida em suas partes componentes
e cada área é auditada. O tempo necessário depende do tamanho da organização. Para uma pequena organização de END, pode-se auditar o seguinte:
- (a) Documentação dos procedimentos de END.
- (b) Controle de departamentos.
- (c) Recebimento de instruções de trabalho.
- (d) Aquisição de equipamentos e acessórios.
- (e) Manutenção de equipamentos e acessórios.
- (f) Calibração do equipamento.
- (g) Administração do contrato.
- (h) Segurança.
- (i) Contabilidade.
- (j) Administração do escritório, por exemplo, salários, férias, aposentadoria.
- (k) Estrutura organizacional.
- (l) Pesquisa e desenvolvimento.
- (m) Relatórios e registros.
Uma
auditoria periódica da qualidade do desempenho do sistema em
relação ao padrão escrito é
necessária para detectar desvios, não conformidade e
violações intencionais dos procedimentos de qualidade
estabelecidos. Para
ser o mais imparcial possível, tais auditorias devem ser
realizadas por pessoas que não tenham responsabilidade na
área auditada. Em
empresas com várias fábricas, cada fábrica
individual pode realizar sua própria auditoria interna, mas,
além disso, deve estar sujeita a auditoria pelo pessoal da
equipe corporativa. As
atividades mais importantes da equipe corporativa, além da
auditoria, são a revisão do sistema de qualidade com o
mais alto nível de gerenciamento da fábrica e o
acompanhamento para aprovar ações corretivas para
quaisquer discrepâncias encontradas durante uma auditoria. A
revisão periódica do sistema de garantia da qualidade e a
reafirmação dos objetivos da qualidade pela alta
administração devem fazer parte da política da
empresa.
|