1.
OBJETIVO
Este
procedimento estabelece as condições mínimas para a execução do ensaio
eletromagnético 3MA (“Micromagnetic Multiparameter Microstructure and Stress
Analysis”), utilizando aparelho para detecção de pontos com dureza elevada
(também chamados de pontos duros, no inglês “hard spots”) em chapas grossas
fabricadas pela USIMINAS em Ipatinga – Minas Gerais.
2. NORMAS DE REFERÊNCIA E/OU OUTROS DOCUMENTOS
APLICÁVEIS
- Norma API 5L – “Specification for Line Pipe”
- Norma ISO 3183 – “Petroleum and natural gas
industries – Steel pipe for pipeline transportation systems”
- Especificação IOGP S-616 – “Supplementary
Specification to API Specification 5L and ISO 3183 Line Pipe”
- Norma ISO 11484 – “Steel products – Employer´s
qualification system for non-destructive testing (NDT) personnel”
- Manual ABENDI
NA-005 – “Qualificação e Certificação de Pessoal em END para Sistemas
Automatizados”
- Norma ISO 20807 – “Non-destructive testing –
Qualification of personnel or limited applications od non-destructive testing"
- Manual ROSEN 12636_IDA_0200090625 “HARD SPOT INSPECTION TROLLEY – Operating and Maintenance Instructions”
3. MATERIAIS
A SEREM ENSAIADOS / CAMPO DE APLICAÇÃO
Este procedimento se aplica ao ensaio
na etapa de fabricação de chapas grossas da qualidade API5L-X100 e
abaixo, principalmente destinadas a confecção de tubos para serem
empregados na construção de dutos de transporte de petróleo e seus
derivados.
O objetivo do ensaio é a detecção de pontos duros porventura existentes na superfície das chapas fabricadas.
A técnica 3MA está inserida nos métodos de ensaio eletromagnético não
destrutivo, no qual a obtenção de parâmetros é conseguida durante os
ciclos de histerese magnética. O 3MA avalia os parâmetros elétricos e
magnéticos que são influenciados, por exemplo, pela microestrutura
cristalina, dureza e profundidade de camada endurecida do material.
4. CERTIFICAÇÃO DE PESSOAL
O ensaio deve ser executado por um
inspetor qualificado e certificado na técnica SA-CP-N2, segundo os
requisitos do SNQC/END, que é um sistema de certificação reconhecido
internacionalmente, atendendo ao definido pela Norma ISO 11484.
5. APARELHO, SONDAS E CHAPA
DE CALIBRAÇÃO PARA O ENSAIO
5.1 Aparelho PLAMAT-M e Programa de Computador
3MA-X8 MMS
O aparelho de inspeção micro magnética
PLAMAT-M consiste em um carrinho (no inglês “trolley”) contendo toda a
parte mecânica, eletrônica e informatizada necessária para a varredura
e inspeção das chapas. A tabela I, a seguir, mostra os principais
componentes desse aparelho.
Tabela I – Desenho e
Componentes do Aparelho PLAMAT-M
Por ser uma das partes mais relevantes
para o resultado da inspeção descreveremos aqui em mais detalhes a
unidade de inspeção. A unidade de inspeção consiste em oito (8)
sensores eletromagnéticos, para detecção de pontos duros (“hard
spots”), e que estão posicionados em duas fileiras de forma escalonada
para permitir uma cobertura total da região sob esses sensores (figura
1).
Fig. 1 – Vista inferior da
unidade de inspeção.
Cada um dos oito (8) sensores
eletromagnéticos consiste além do detector das propriedades
eletromagnéticas pertinentes ao ensaio, também de um julgo magnético
excitado por uma corrente alternada, ver detalhe na figura 2.
Fig.
2 – Detalhe de um dos oito sensores eletromagnéticos da unidade de inspeção.
Uma placa cerâmica com espessura de 0,5
mm está inserida entre o sistema yoke/bobina e a chapa. A placa
cerâmica está diretamente em contato com as sapatas do yoke, de forma
que nenhum lift-off adicional ocorra. O lift-off é função apenas da
espessura da cerâmica. Os sensores não estão fixos nos respectivos
suportes sendo possível a sua movimentação na direção vertical. A
movimentação do sensor é restrita pela presença de molas e de um
barramento superior. Cada sensor possui movimentação independente
permitindo adaptação a condições locais da superfície da chapa
(curvatura, sujeira, ...). Apesar da liberdade de movimentação vertical
dos sensores, os mesmos são pressionados contra a superfície da chapa
tanto pela força da mola como pela força magnética propiciada pelo yoke.
O aparelho de inspeção micro magnética PLAMAT-M é totalmente controlado
por um programa de computador (“software”) chamado 3MA-X8 MMS que
descreveremos resumidamente a seguir.
O programa 3MA-X8 MMS possui três (3) níveis de acesso controlados por senha:
- Usuário: acesso apenas à parte de inspeção e pode ser utilizado para conhecimento inicial do processo;
- Supervisor: acesso as janelas de inspeção, medição, calibração e
sinal bruto pelo pessoal qualificado e certificado pelo SNQC/END na
modalidade SA-CP-N2
- Serviço: acesso a todas as janelas anteriores, mais a janela de
configurações avançadas pelos Técnicos e Engenheiros das Gerências de
Chapas Grossas, Gerência Técnica da Laminação a Quente, Manutenção e
Instrumentação. Ao início e ao fim de cada jornada de trabalho, ou
quando a chapa inspecionada for de grau diferente da que foi
anteriormente inspecionada é necessária uma nova calibração do
aparelho, portanto de acesso com nível de supervisão. As duas tabelas a
seguir descrevem a principal, e mais utilizada, janela (“window”) do
software que é a janela de inspeção. Durante a calibração, caso seja
identificada alguma anormalidade no aparelho, sensores ou outro
componente que venha afetar a sensibilidade e consequentemente o
resultado do ensaio, todas as chapas processadas após a última
calibração deverão ser relacionadas e devolvidas ao processo para serem
reensaiadas após a resolução do problema, esse levantamento poderá ser
feito no sistema LQCG (processo 25).
Tabela II – Visão
geral da janela de inspeção e seus principais elementos
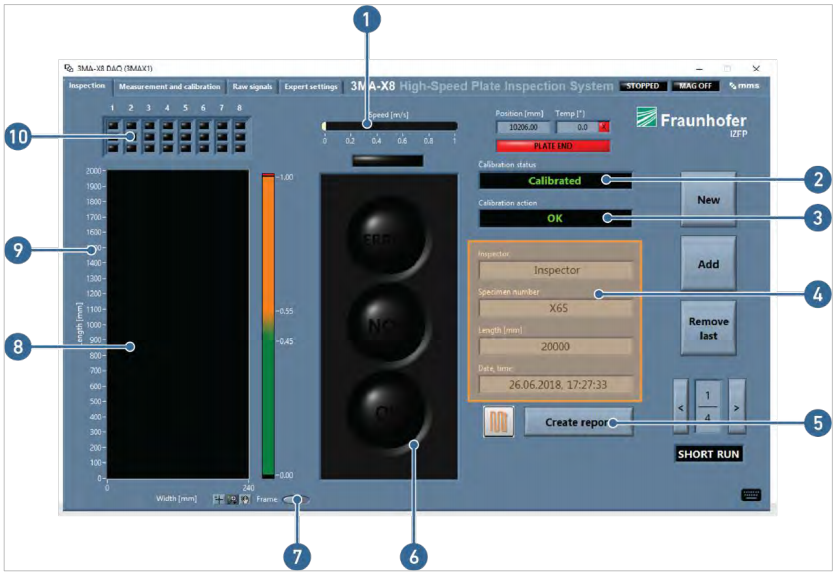
|
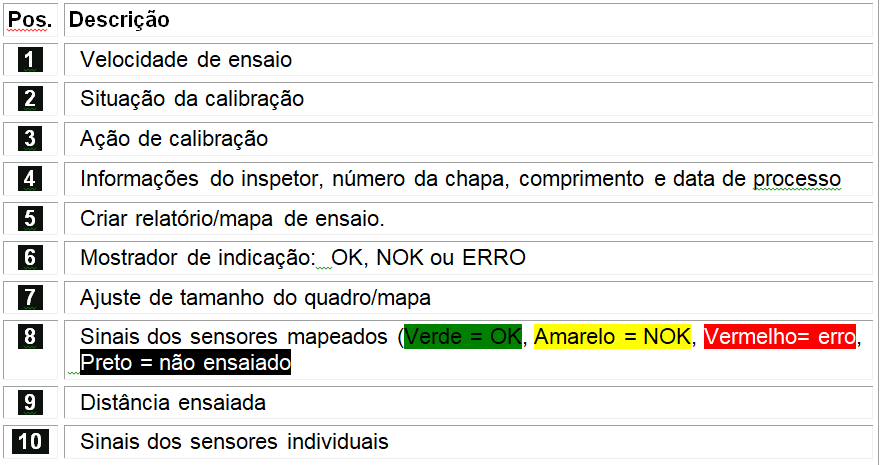
|
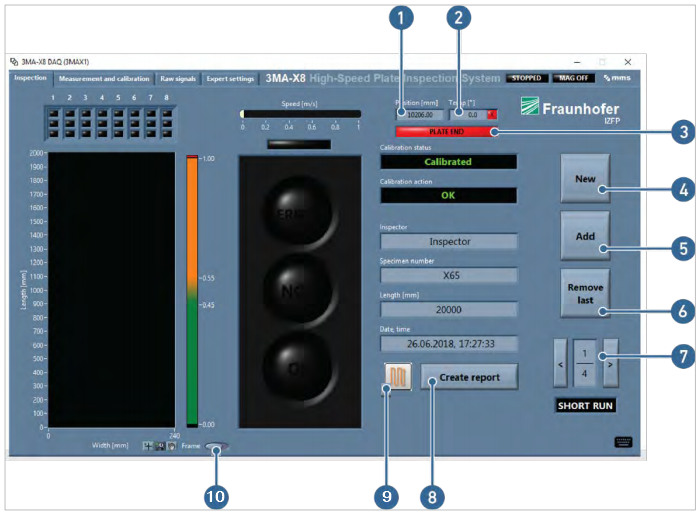 |
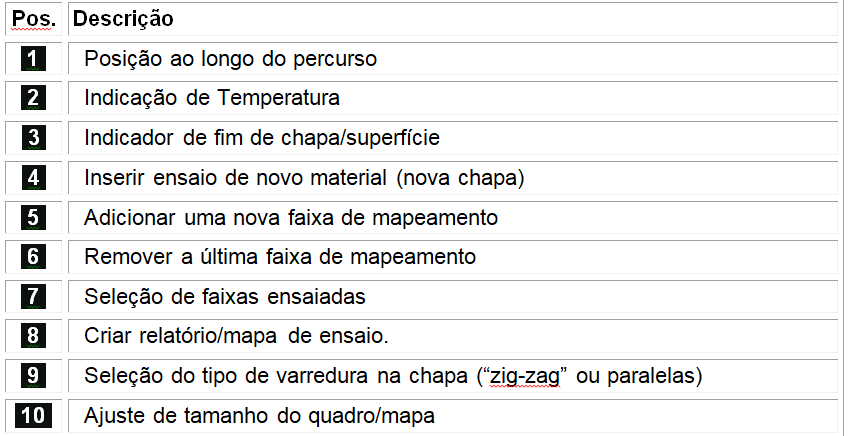
|
5.2 Chapa de Calibração para o Ensaio
Para
calibração (ajuste dos parâmetros de ensaio) do aparelho de inspeção
micro magnética PLAMAT-M no programa de computador (“software”) 3MA
deve ser utilizada uma chapa padrão, ou de referência, de mesmo grau
das chapas grossas fabricadas a serem inspecionadas. As figuras a
seguir mostram detalhes construtivos dessa chapa.
A figura 3 apresenta um desenho completo da chapa padrão com suas
dimensões. Nessa chapa existem duas regiões com funções e
“descontinuidades” diferentes:
Uma região de
verificação da sensibilidade do sistema, na qual existe uma área
retangular com comprimento 250 mm, largura 300 mm e profundidade de 15
mm, aproximadamente, preenchida por processo de soldagem. Essa região
foi calculada para que todos os oito (8) sensores estejam contidos em
sua área, sem efeito de borda influindo nos sensores, e deve ter sua
superfície com dureza maior que limite superior permitido pela norma de
fabricação da chapa de grau objeto da inspeção para detecção de pontos
duros (“hard spots”);
Uma região de verificação de detectabilidade do
sistema, na qual existem oito (8) orifícios no qual são preenchidos por
processo de soldagem com arame tubular, essas regiões têm
diâmetro de 50 mm e profundidade de 15 mm. O
diâmetro dessas regiões foi estabelecido em função da mínima
detectabilidade exigida por norma para regiões com pontos duros. Os
posicionamentos dessas áreas foram estabelecidos para ficarem
perfeitamente centralizadas nos 8 (oito) sensores da unidade de
inspeção.
Fig. 3 – Desenho da chapa padrão para calibração/ajuste do aparelho PLAMAT-M e programa de computador 3MA-X8 MMS.
Fig. 4 – Desenho dos sulcos para
preenchimento por solda na regiões de verificação da sensibilidade
e da detectabilidade na chapa.
6. CALIBRAÇÃO
Ao início de cada jornada de trabalho,
ou quando a chapa inspecionada for de grau diferente da que foi
anteriormente inspecionada é necessária uma nova calibração do
aparelho, a fim de determinar a propriedade de dureza do material,
quantitativamente. Dependendo da composição química do aço e de seu
processo de fabricação, diferentes combinações de microestruturas e de
outras propriedades influentes nos resultados desse ensaio devem ser
distinguidas. Testes com consistências estatísticas (número de
amostras), considerando todas as variáveis independentes com influência
no ensaio, são necessários para separar a influência da microestrutura
(variável relevante) das outras influências (variáveis não relevantes)
na resposta obtida no ensaio.
Geralmente, a medição pode ser afetada por diferentes variáveis
perturbadoras (ruídos) do ensaio, como carepa, magnetização residual,
tensão residual além dos outros parâmetros essenciais. Como
consequência direta, uma calibração individual seria necessária para
cada tipo de aço e uma combinação dos demais parâmetros influentes.
Diferentes tipos de aço, implicam em diferentes microestruturas
(ferrita, perlita, bainita, ...), diferentes profundidades de
endurecimento, além da sua combinação com outros parâmetros influentes,
o que poderia implicar em uma grande variedade de chapas de referência
para calibração.
Como alternativa a essa dificuldade, um algoritmo de aprendizado de
máquina para classificação supervisionada é usado pelo programa de
computador que gere a inspeção. A figura 5 apresenta um fluxograma
desse algoritmo. Esse algoritmo emprega a distância euclidiana entre os
dados vizinhos mais próximos no espaço de parâmetros. O comportamento
estatístico do ensaio magnético de uma amostra desconhecida será
comparado com todos os comportamentos dos dados existentes na base de
dados de calibração. O dado vizinho com comportamento mais próximo do
da amostra desconhecida no espaço de parâmetro relevante será
investigado. O valor do parâmetro do vizinho mais próximo encontrado
será o valor alvo do parâmetro resultante para a amostra desconhecida.
O aparelho de inspeção não fornece a dureza absoluta da amostra
ensaiada. Portanto, quando da detecção de estados micro magnéticos
desconhecidos, a dureza real, deve ser confirmada via avaliação
mecânica com teste de dureza móvel (Leeb, UCI). Recomenda-se que a
medição da dureza deverá seguir a sistemática descrita no Procedimento
de Medição da Dureza com Equipamento Portátil. A base de calibração é
sucessivamente atualizada e ampliada com novos estados micro magnéticos
conhecidos após uma operação inicial, figura 5.
Fig. 5 – Visão geral do processo de aprendizagem de máquina.
Antes de iniciar o processo e
normalização, caso seja necessário, ajustes deverão ser feitos no
programa 3MA-X8 MMS para que não exista diferenças entre as respostas
dos oito sensores de mais que 20% para qualquer um dos 4 principais
parâmetros mais importantes de medição do aparelho PLAMAT-M (figura 6),
que são:
DZmax (Ohm) => Permeabilidade incremental máxima
DZmean (Ohm) => Permeabilidade incremental média
DZr (Ohm) => Permeabilidade incremental no ponto remanescente
Ucdz (Volts) => Tensão na permeabilidade incremental máxima
Fig. 6 Parâmetros a serem verificados.
Estando o aparelho sobre uma região da
chapa de calibração conhecida como OK (sem a presença de pontos duros),
para cada um dos 4 parâmetros, o inspetor deverá utilizar como
referência o valor para sonda de nº 1, comparando com as demais sondas.
A variação do valor obtido entre as oito sondas não poderá ser maior
que 20%, caso isso ocorra o inspetor primeiramente deverá fazer a
movimentação do aparelho para adequação desses valores em outra região
OK do material com melhor homogeneidade, persistindo a variação maior
que o permitido em qualquer uma das sondas, deverá ser feita a
verificação da condição dos cabos e posicionamento das sondas (figura
7) e se necessário acionar a equipe de manutenção.
Fig. 7 – Visão da unidade de inspeção e os cabos conectores.
Antes da etapa de calibração para a
inspeção de um novo grau de aço é preciso fazer a operação de
normalização. Para isso uma área da chapa padrão de referência que
possua dureza abaixo do limite de reprovação (chamada de material base)
deve ser inspecionada pelo aparelho e o resultado da inspeção
registrado no programa.
Após a operação de normalização é preciso estabelecer o limiar de
aprovação (OK)/reprovação(NOK) pela inserção de pontos de dados com
essas características (dureza abaixo do limiar/dureza acima do limiar)
no banco de dados de configuração para esse novo grau de material.
Devido a inexistência inicial de banco de dados para o novo material é
provável a indicação de erro (ERROR) em pontos de leitura, nesse caso o
inspetor deverá avaliar a necessidade de se repetir o processo de
calibração acrescentando esse ponto ao banco de dados como OK ou NOK
dependendo do valor de dureza medido nesse ponto. A definição de pontos
com condição OK/NOK é obtida através de referência por medidas de
dureza com técnica complementar (Leeb, UCI). Após a inserção de pontos
(OK/NOK) no banco de dados desse novo material é possível iniciar a
inspeção de chapas do novo grau de aço.
A seguir apresentam-se a sequência das etapas de calibração:
- Mova o aparelho PLAMAT-M para uma área OK da amostra de referência.
- Calibre pelo menos 10 pontos por canal como OK (nuvem de pontos
verde) em pelo menos 4 regiões diferentes da chapa de calibração.
- Mova o aparelho e verifique as variações do sinal com base nas mudanças normais do material.
- As regiões de coleta, preferencialmente serão onde a variação do
sinal com base no material for mais alta, o sistema mostrará o
inspetor. Caso o inspetor julgar necessário, atualizar a calibração
adquirindo mais pelo menos 10 pontos.
- Mova o aparelho para uma área NOK da amostra de referência.
- Calibre a área NOK (nuvem de pontos vermelho) e balanceie o banco
de dados (o número de dados NOK deve ser pelo menos 10% do número de
dados OK).
A figura 8, apresenta exemplo dos
gráficos inferiores da sub aba Medição e calibração (“Measurement and
calibration”) após uma calibração bem-sucedida. É possível observar a
nuvem de pontos verdes (região OK), a nuvem de pontos vermelhos (região
NOK), e o raio do círculo de classificação (falta de precisão do
contorno, “unsharpness”).
Fig. 8 – Gráficos da sub aba Medição e calibração com nuvens de pontos OK e NOK perfeitamente separados.
A chapa padrão de referência possui
duas regiões representativas de pontos duros. Uma região, chamada de
verificação da sensibilidade da técnica micro magnética, ampla (abarca
todos os oito sensores ao mesmo tempo), na forma de um retângulo, e
que; e uma região, chamada de verificação da detectabilidade da técnica
micro magnética, com oito círculos, com diâmetro no limite de detecção
exigido por norma. A figura 9 apresenta o sentido de varredura que o
aparelho deve fazer na chapa para verificar a sensibilidade. A figura
10 apresenta o sentido de varredura que o aparelho deve fazer na chapa
para verificar a detectabilidade.
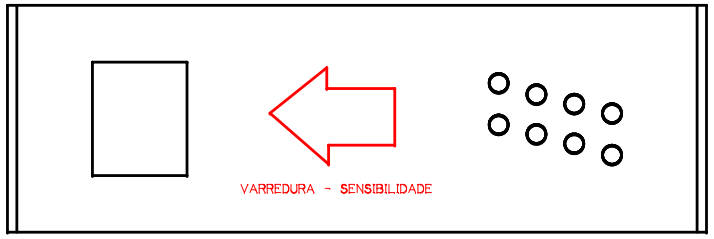
|
Fig. 9 – Sentido de varredura na chapa padrão de referência para verificação da sensibilidade.
|
Fig. 10 – Sentido de varredura na chapa padrão de referência para verificação da detectabilidade.
A cada 5 anos deverá ser feita uma
calibração do equipamento pelo fabricante ou órgão competente na
funcionalidade de sistemas eletromagnéticos.
7. CONDIÇÃO SUPERFICIAL E PREPARAÇÃO DA
SUPERFÍCIE
A chapa a ser inspecionada pelo sistema
de inspeção de pontos duros deve ter sua superfície na condição de como
fabricada. Recomenda-se escovar ou varrer a chapa para remover qualquer
objeto ou sujeita que esteja sob a superfície e venha a se interpor
entre a chapa e a unidade sensora prejudicando a inspeção.
8. PLANO DE VARREDURA
Toda superfície de um dos lados da
chapa é varrida completamente por um conjunto de faixas de inspeção
individuais consistindo na largura de varredura do aparelho. Cada faixa
varrida consiste em uma varredura curta mais uma varredura longa (ver
figura 11).
Figura 11 – Exemplo de varredura com aparelho PLAMAT-M iniciando sempre do ponto 0.
A fim de preparar a chapa para o
ensaio, recomenda-se a utilização de marcações (linhas) feitas com um
cordão esticado e embebido em giz para indicar as faixas com largura de
240 mm na chapa (varreduras individuais). Ver exemplo Figura 12.
Figura 12 – Demarcação de linhas na seção longitudinal na largura do modulo de inspeção com as sondas eletromagnéticas.
Se o modo escolhido para a varredura de toda a chapa for o “zig-zag”, proceda de acordo com as seguintes etapas:
1. Tendo como
referência o ponto 0 (zero), execute primeiro a varredura curta (figura 13,
faixa 1, da direita para esquerda).
2. Certifique-se
de que a distância varrida é maior do que o comprimento do carrinho.
- Ao atingir a
borda da placa (2), o programa indica
para fazer a mudança para varredura longa.
3. Ao mudar de
varredura curta para varredura longa, inverta o sentido de varredura do
aparelho (3).
- Em seguida, a
varredura longa é realizada (na figura 11, da esquerda para a direita) e, dessa
forma, a inspeção faixa 1 será concluída com sucesso.
4. Mova o carrinho
para trás em uma curta distância, inverta o sentido de varredura do aparelho,
para começar com a corrida curta da faixa 2.
5. Repita o
procedimento descrito nas etapas anteriores até cobrir/inspecionar toda a
superfície da chapa em um dos lados.
Para garantir que o equipamento faça a
varredura em toda superfície, caso o inspetor julgue necessário ele
poderá contar com o auxílio de uma pessoa que ficará de frente para a
unidade de inspeção observando se o alinhamento está dentro da faixa
necessária.
Depois de concluir o procedimento acima para uma face da chapa inteira,
vire a chapa e repita o mesmo procedimento para varredura na outra face
da chapa, caso haja programação para realizar o processo também na face
inferior.
Fig. 13 – Vista geral da varredura da chapa em um dos lados.
9. CARACTERIZAÇÃO DAS REGIÕES COM INDICAÇÕES DE
PONTOS DUROS
Todas as regiões da chapa inspecionada
onde houver indicação pelo aparelho da presença de pontos duros devem
ser verificadas quanto ao valor de dureza real existente, com durômetro
portátil de acordo com o procedimento operacional para “Medição de
Dureza com Aparelho Portátil”. Os critérios necessários estão
estabelecidos nesse mesmo documento operacional, caso confirmada a
reprovação da região, analisar a pertinência de incluir esse novo ponto
detectado no banco de dados para o grau de aço sendo inspecionado.
10. REGISTRO DE RESULTADOS
Devem ser registrados os seguintes dados no sistema LQCG:
- Número da chapa;
- Face inspecionada da chapa;
- Número sequencial dos pontos duros detectados na face da chapa;
- Coordenadas a partir de uma origem definida na
chapa (canto de referência, “datum”) de localização (na direção da
largura e do comprimento) do ponto duro detectado;
- Dimensão da região detectada nas direções da largura e do comprimento;
- Dureza máxima medida mecanicamente com durômetro na região indicada pelo aparelho.
11. CRITÉRIO DE ACEITAÇÃO
Todas as regiões com pontos duros com
dimensão maior que 50 mm em qualquer direção serão consideradas
defeitos, e, portanto, reprovadas, se sua dureza exceder 30 HRC.
Nota: No processo realizado na Gerência de Chapas Grossas adota-se a
unidade HRC para as medidas de dureza, se necessário o inspetor poderá
utilizar a tabela de conversão existente no procedimento operacional
para “Medição de Dureza com Aparelho Portátil”.
- Caberá ao inspetor definir pela recuperação da chapa pelo
processo de esmerilhamento, onde deverá ser removida a região indicada
no mapa concebido durante o ensaio com o equipamento PLAMAT-M e
devidamente registrado no sistema informatizado da Usiminas (LQCG), não
podendo de forma alguma ser a espessura menor que a mínima definida na
ordem de venda de acordo com a Norma de Dimensão, Forma e Aspecto de
Chapas Grossas (SQCICNT0001), em caso de não atendimento desta norma, a
chapa deverá ser recusada e não poderá ser utilizada para sua aplicação
original.
12. TRATAMENTO DE NÃO CONFORMIDADES
Chapas com defeitos que não atendam as
normas de referência e não possibilitam ação de retrabalho e
aproveitamento, devem ser recusadas no ato da inspeção e marcadas para
estoque, desde que as dimensões atendam os critérios mínimos e máximos
para estocagem de produtos, indicados na tabela III.
ESPESSURA (mm)
|
LARGURA REAL (mm)
|
COMPRIMENTO REAL (mm)
|
SUBDIVISÃO
|
MÍNIMA
|
MÁXIMA
|
MÍNIMA
|
MÁXIMA
|
MÍNIMA
|
MÁXIMA
|
5,00
|
185,00 |
900
|
3200
|
2400
|
13500
|
Não subdividir
|
3201
|
3900
|
13501
|
25000
|
Subdividir*
|
*se não atender o critério para dimensões mínimas deve ser sucateada
13. SISTEMÁTICA DE REGISTRO DE RESULTADOS
Os resultados dos ensaios devem ser
registrados no sistema LQCG de maneira que seja possível correlacionar
o relatório com a localização física do local ensaiado e das
descontinuidades detectadas e vice-versa. Os relatórios devem ser
acompanhados de um croqui indicando de forma precisa a localização das
descontinuidades detectadas.
14. RELATÓRIO
DE REGISTRO DE RESULTAD
O registro de resultado deverá ser
feito no LQCG pelo executor da inspeção, esse relatório deve conter, no
mínimo, as seguintes informações:
Um modelo de relatório de registro de resultados deve ser acordado
entre o solicitante e o executor da inspeção esse relatório deve
conter, no mínimo, as seguintes informações:
- Nome da gerência executora da inspeção;
- Número e revisão do procedimento de inspeção utilizado;
- Identificação do componente ensaiado (lote, corrida, grau, tratamento térmico e dimensões);
- Material do componente inspecionado, indicando o tipo e especificação;
- Identificação do inspetor e nível de qualificação e certificação;
- Aparelho utilizado indicando o número de série;
- Sondas empregadas no ensaio (tipo, número de série);
- Tipo e identificação do chapa de calibração utilizada;
- Parâmetros do exame (frequência, ganho, fase, escala);
- Registro das verificações de calibração executadas;
- Condição superficial e método de preparação da superfície caso necessário;
- Regiões onde o ensaio foi realizado (preferencialmente com desenhos);
- Resultados de calibração, incluindo o valor mínimo e máximo medido das propriedades avaliadas;
- Data de realização do ensaio;
- Resultados do ensaio e croqui com o mapa de indicações rejeitadas;
- Norma de referência incluindo edição e revisão aplicável;
- Nome e assinatura do inspetor que realizou o ensaio;
- Laudo indicando aceitação, rejeição ou recomendação de ensaio/estudo complementar.
15. SEGURANÇA
Retrata-se instruções de segurança indicadas no manual de operação e manutenção do aparelho PLAMAT-M.
O sistema de inspeção deve ser operado apenas por inspetor treinado, qualificado e autorizado.
Qualquer pessoa que realize trabalhos no e com o aparelho deve ter lido
e compreendido o capítulo sobre as instruções de segurança do manual e
ser informado pelo inspetor responsável pelo aparelho de qualquer
perigo que possa ocorrer. É responsabilidade do inspetor do aparelho
verificar se as instruções de operação foram compreendidas.
As instruções de segurança devem ser sempre mantidas em local definido para operação do sistema de inspeção.
O inspetor, nível II, responsável pela operação do aparelho devem possuir os seguintes conhecimentos:
- regulamentos de segurança e para a prevenção de acidentes
- regras de operação na planta
- regulamentos de proteção ambiental
- básico geral na operação e manutenção técnica
- operação de aplicativos do Windows
- inspeção por correntes parasitas
- procedimentos de ensaio
16. MODELO DE RELATÓRIO DE RESULTADOS DO ENSAIO
As figuras 14 e 15, a seguir,
apresentam reprodução das telas do sistema LQCG para o registro do
resultado da inspeção do ensaio eletromagnético para detecção de pontos
duros e a tela de registro do mapa de processo.
Fig. 14 – Vista da tela do sistema
LGCQ com registro do resultado da inspeção para detecção de pontos duros (tela
1, processo 25).
Fig.
15 – Vista da tela do sistema LGCQ com registro do resultado da
inspeção para detecção de pontos duros (tela 2, processo 25).